Inside the Modular Building Process
In this article, each step of the modular construction process will be explored and reasons for these advantages will be detailed.
The Advantages of Modular Construction
Modular construction (also referred to as off-site and/or volumetric construction) is growing in popularity because it offers several advantages over traditional construction. Chiefly, these advantages include:
- Shorter construction times (leading to a quicker ROI for owners), and
- Cost certainty (obtained through fewer mid-project changes and weather delays, and, to a lesser degree, fewer on-site injuries)
These advantages are obtained through a carefully planned design and construction process. Unlike many traditional construction projects, modular construction leverages a precise timetable and a predictable, industrialized assembly process to realize its value.
Step 1: Design approval by the regulating authorities and end users
In the modular building process, the project begins at the design phase. Architects and engineers, using building information modeling (BIM) systems and other software, create exterior and interior plans. Once plans are approved by the owner, they are submitted to the locality or third-party service for approval and building permit applications are submitted. The manufacturing of components begins once the design is finalized.
Note: Modular buildings must follow the local building codes and zoning regulations. The modular building contractor should already know the regulations that apply to the project based on the address of the physical building site and the agencies that have jurisdiction over that area.
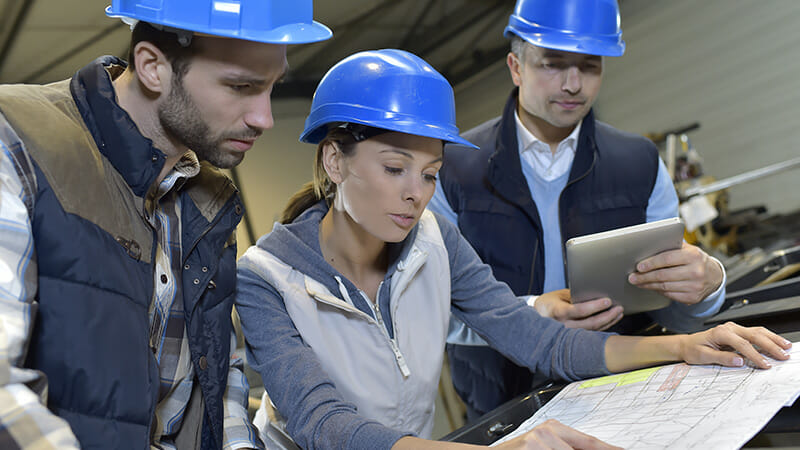
Modular buildings must have approved and finalized designs before construction begins.
Step 2: Construction of modular components in a controlled atmosphere
The module components are built in a controlled offsite factory environment while site excavation and grading is going on at the same time. The amount of work (60% - 90%) performed in the factory can vary based on owner requirements. For example, it can include assembling basic structural components (like exterior and interior walls, flooring, and windows), installing mechanical, plumbing, and electrical components, and completing interior finishes such as drywall and cabinets. Because so much can be accomplished off-site, the labor force in the factory can consist of any or all of the following:
- Carpenters
- Drywall finishers
- Plumbers
- Electricians
- HVAC workers
- Painters
- Floor finishers, and more
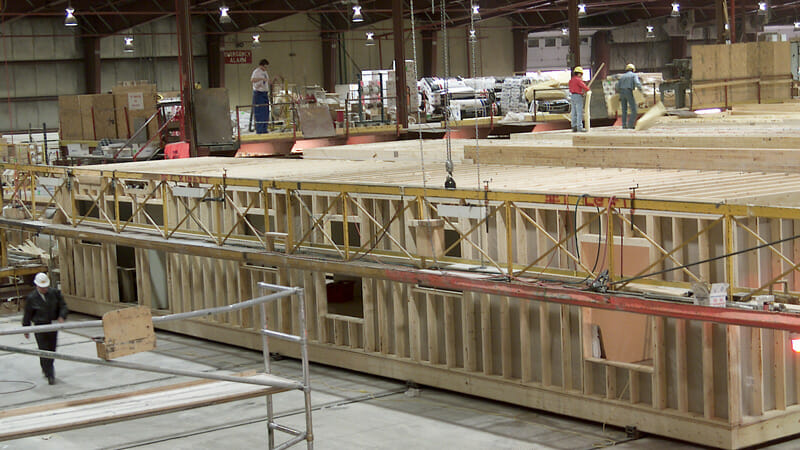
A controlled factory environment allows modules to be built quickly, precisely, and more safely.
Inspections by a third party or other building code official takes place at various stages in the factory. Upon completion of the modules, they are prepared for transportation.
Step 3: Transportation of modules to a desired location
Modular buildings are shipped on chassis integrated into the structure or carriers towed by trucks. Due to the need to transport the modules to the final site, each module must be built to independently withstand travel and installation requirements (e.g., high winds, manipulation by cranes). Of note, the resiliency of the individual modules contributes to the greater structural strength of the final building, another advantage of modular construction.
Transportation of the modules depends upon some important factors such as the cost and method of transport, travel distance, and weight. It usually isn’t feasible to ship modules far due to road size and load restrictions. Generally, the maximum desirable distance for transportation of modules is 250 to 400 miles. The costs and transportation difficulties greatly increase for building sites farther than 400 miles.
The maximum width, height, and length of individual modules that can be transported is dependent on several criteria including local Department of Transportation restrictions; bridges, overpasses, utility lines that cross over roadways; and the actual route itself from the factory to the final destination. For ease of transportation, modules commonly have measurements of 15-feet wide, 12-feet high and 60-feet long, although these measurements can differ greatly in any direction based on a number of factors.
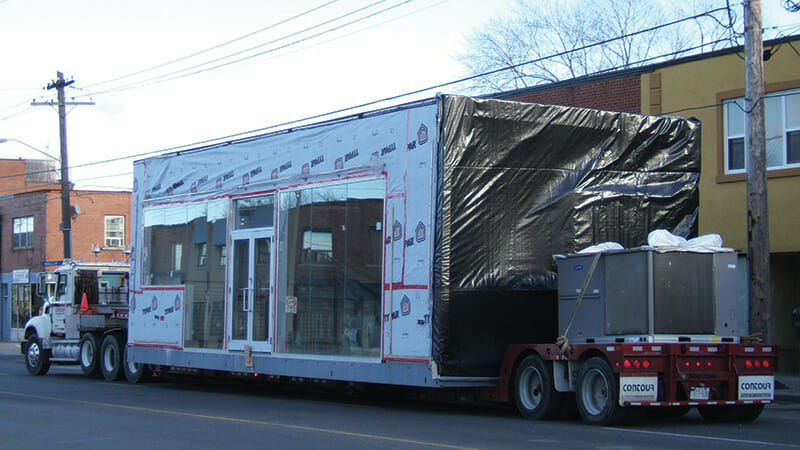
Transporting the finished modules to the jobsite can involve a single truck or many, depending on the size of the project.
Step 4: Erection of modules to form a finished building
Once at the jobsite, the modules are stacked by crane or rolled onto the foundation, bolted together and sealed for weather-proofing. The modules are then connected together, utilities are hooked-up, exterior siding and roofing components are completed, and site work is finished. The final construction stage includes completing exterior systems such as cladding, final caulking and sealing, adding stairs and elevators, and competing any interior elements such as painting, trim, cabinets, countertops, and installation of appliances that didn’t occur in the factory.
Modular construction offers an accelerated schedule for designers and builders and an accelerated ROI for owners. This is primarily accomplished by working on multiple fronts simultaneously. While modules are built and furnished in a controlled offsite location, site work can occur at the same time, eliminating the need for less efficient, strictly linear process.
This process—called parallel construction—is a key benefit of the modular construction process as it allows for reduced construction times of about 30% - 50% that of conventional construction.
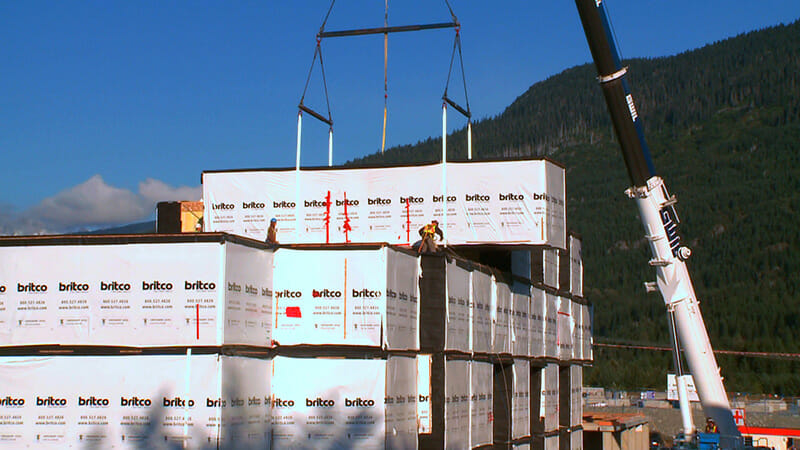
Installing the modules happens quickly. In some cases, large multi-story buildings can be stacked in less than two weeks.
The process of modular construction is strict. Plans must be finalized early and stakeholders must have a complete understanding of the entire building process, but the advantages of modular construction are indisputable. To find a modular builder near you, click here.
More from Modular Advantage
Inside the Construction of 355 Sango Court
This year’s winner for Best of Show for Permanent Structures is 355 Sango Court, a 105,818 square foot affordable housing development manufactured by Nampa, Idaho based Autovol. The project team also included Prefab Logic for module design, Nibbi Brothers as the general contractor, Acc U Set Construction as the modular installer, and the overall project design was by David Baker Architects and DCI and Fard.
Aster Place by ROC Modular
Aster Place, a supportive housing building in Richmond, British Columbia, Canada, won the Best of Show Award and Honorable Mention for relocatable structures in the social and supportive housing category at this year’s World of Modular conference.
Looking Back at the 2024 World of Modular
On March 18-21, the Modular Building Institute presented its 41st annual
convention and tradeshow, hosted again at the luxurious the Rosen Shingle Creek in Orlando, FL. Nearly 1,500 attendees from around the world gathered to learn, network, and find ways to expand both their businesses and the industry at-large.
Touring Japan’s Offsite Construction Industry: An Interview with James Haas, Offsite Construction Sales Manager for Nichiha
Nichiha USA, a premier provider of building envelope solutions and member of the Modular Building Institute (MBI), recently partnered with MBI for a trip to Japan to visit the Nichiha home office in Nagoya as well as several other offsite manufacturers around the country. Besides learning about different offsite building methodologies and systems, the trip was an excellent chance for both MBI and Nichiha to create closer ties with potential industry partners in Japan.
Modular Multi-family Construction: A Field Study of Energy Code Compliance and Performance through Offsite Prefabrication
Prefabrication in a factory setting may improve the performance of modular buildings compared to traditional site-built buildings. To validate this premise, the U.S. Department of Energy (DOE) funded a 3-year study from 2020-2023 comparing the energy performance of more than 50 modular and site-built multifamily buildings under construction in Los Angeles, San Francisco, Philadelphia and Seattle.
Inflation Comes in Hot to Begin ’24
Last year was a shockingly good one for the U.S. economy, at least relative to expectations. Coming into 2023, the conventional wisdom was that near-term recession was inevitable in America. In the face of belligerent excess inflation (above the Federal Reserve’s 2 percent mandate), monetary policymakers began ratcheting interest rates higher in March 2022. That process continued throughout the balance of the year and into 2023.
A Huge Win for the Modular Construction Industry in Massachusetts
In early February, 2024, the Massachusetts Board of Building Regulations and Standards (BBRS) released its proposed 10th Edition building codes. This draft included several amendments targeting modular construction that would have created an extremely difficult environment for the entire modular industry and could have eliminated the industry entirely in the state.
FEMA Announces Hawaii Housing Plan Using Modular Construction
Utah becomes the second state in the country, following Virginia, to fully adopt ICC/MBI standards 1200 and 1205. MBI will continue to work with leadership in Utah to implement the new program.
Supply and Demand: Solving Canada’s Housing Crisis One Relocatable Housing Unit at a Time
Not only do Moda Modular’s repurposed employee housing solutions cut the emissions related to construction down to nearly zero, but they also keep building materials that are often not biodegradable from slowly decaying in storage facilities.
It’s the classic environmental mantra of reduce, reuse, and recycle, scaled up and applied to building after building.
ICC/MBI Standards 1200 & 1205 Provide Foundation for Utah’s First-Ever State Modular Program
Utah becomes the second state in the country, following Virginia, to fully adopt ICC/MBI standards 1200 and 1205. MBI will continue to work with leadership in Utah to implement the new program.