Inside the Modular Building Process
In this article, each step of the modular construction process will be explored and reasons for these advantages will be detailed.
The Advantages of Modular Construction
Modular construction (also referred to as off-site and/or volumetric construction) is growing in popularity because it offers several advantages over traditional construction. Chiefly, these advantages include:
- Shorter construction times (leading to a quicker ROI for owners), and
- Cost certainty (obtained through fewer mid-project changes and weather delays, and, to a lesser degree, fewer on-site injuries)
These advantages are obtained through a carefully planned design and construction process. Unlike many traditional construction projects, modular construction leverages a precise timetable and a predictable, industrialized assembly process to realize its value.
Step 1: Design approval by the regulating authorities and end users
In the modular building process, the project begins at the design phase. Architects and engineers, using building information modeling (BIM) systems and other software, create exterior and interior plans. Once plans are approved by the owner, they are submitted to the locality or third-party service for approval and building permit applications are submitted. The manufacturing of components begins once the design is finalized.
Note: Modular buildings must follow the local building codes and zoning regulations. The modular building contractor should already know the regulations that apply to the project based on the address of the physical building site and the agencies that have jurisdiction over that area.
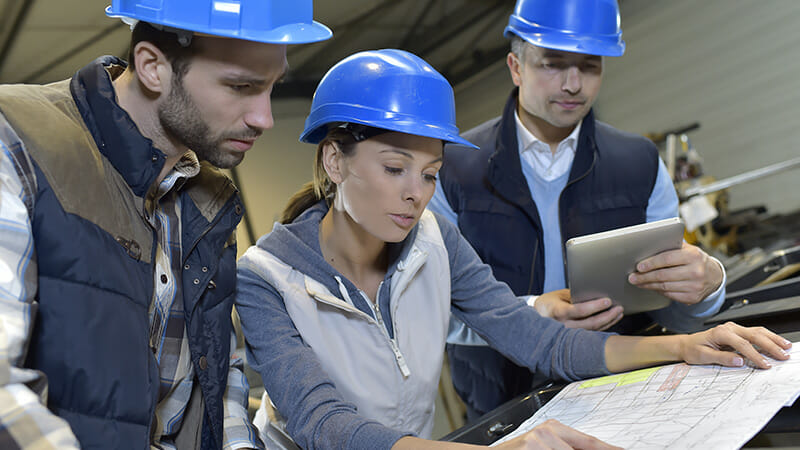
Modular buildings must have approved and finalized designs before construction begins.
Step 2: Construction of modular components in a controlled atmosphere
The module components are built in a controlled offsite factory environment while site excavation and grading is going on at the same time. The amount of work (60% - 90%) performed in the factory can vary based on owner requirements. For example, it can include assembling basic structural components (like exterior and interior walls, flooring, and windows), installing mechanical, plumbing, and electrical components, and completing interior finishes such as drywall and cabinets. Because so much can be accomplished off-site, the labor force in the factory can consist of any or all of the following:
- Carpenters
- Drywall finishers
- Plumbers
- Electricians
- HVAC workers
- Painters
- Floor finishers, and more
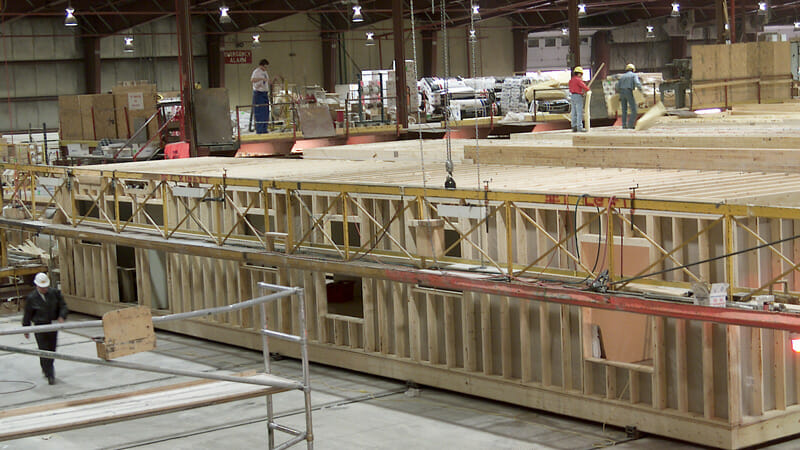
A controlled factory environment allows modules to be built quickly, precisely, and more safely.
Inspections by a third party or other building code official takes place at various stages in the factory. Upon completion of the modules, they are prepared for transportation.
Step 3: Transportation of modules to a desired location
Modular buildings are shipped on chassis integrated into the structure or carriers towed by trucks. Due to the need to transport the modules to the final site, each module must be built to independently withstand travel and installation requirements (e.g., high winds, manipulation by cranes). Of note, the resiliency of the individual modules contributes to the greater structural strength of the final building, another advantage of modular construction.
Transportation of the modules depends upon some important factors such as the cost and method of transport, travel distance, and weight. It usually isn’t feasible to ship modules far due to road size and load restrictions. Generally, the maximum desirable distance for transportation of modules is 250 to 400 miles. The costs and transportation difficulties greatly increase for building sites farther than 400 miles.
The maximum width, height, and length of individual modules that can be transported is dependent on several criteria including local Department of Transportation restrictions; bridges, overpasses, utility lines that cross over roadways; and the actual route itself from the factory to the final destination. For ease of transportation, modules commonly have measurements of 15-feet wide, 12-feet high and 60-feet long, although these measurements can differ greatly in any direction based on a number of factors.
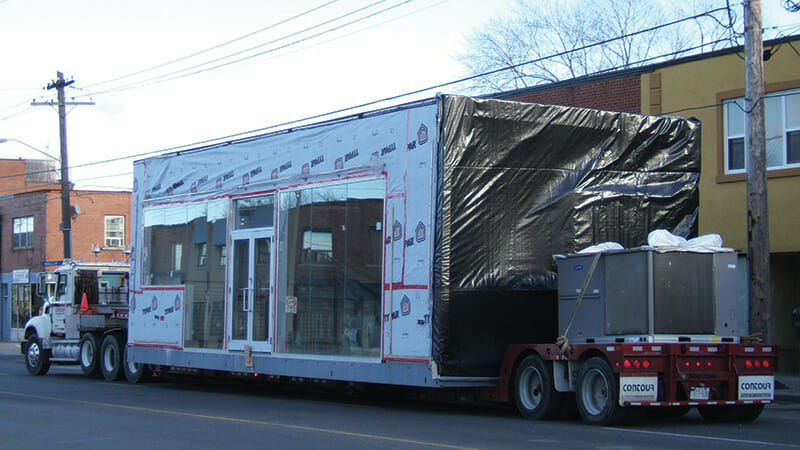
Transporting the finished modules to the jobsite can involve a single truck or many, depending on the size of the project.
Step 4: Erection of modules to form a finished building
Once at the jobsite, the modules are stacked by crane or rolled onto the foundation, bolted together and sealed for weather-proofing. The modules are then connected together, utilities are hooked-up, exterior siding and roofing components are completed, and site work is finished. The final construction stage includes completing exterior systems such as cladding, final caulking and sealing, adding stairs and elevators, and competing any interior elements such as painting, trim, cabinets, countertops, and installation of appliances that didn’t occur in the factory.
Modular construction offers an accelerated schedule for designers and builders and an accelerated ROI for owners. This is primarily accomplished by working on multiple fronts simultaneously. While modules are built and furnished in a controlled offsite location, site work can occur at the same time, eliminating the need for less efficient, strictly linear process.
This process—called parallel construction—is a key benefit of the modular construction process as it allows for reduced construction times of about 30% - 50% that of conventional construction.
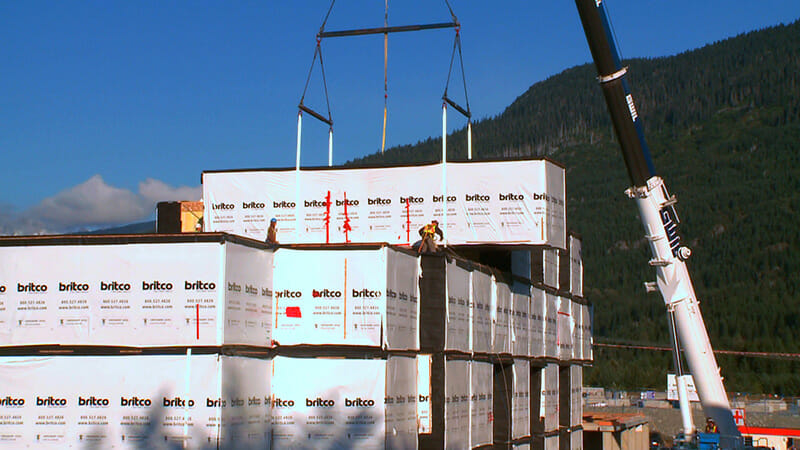
Installing the modules happens quickly. In some cases, large multi-story buildings can be stacked in less than two weeks.
The process of modular construction is strict. Plans must be finalized early and stakeholders must have a complete understanding of the entire building process, but the advantages of modular construction are indisputable. To find a modular builder near you, click here.
More from Modular Advantage
Behind the Design of Bethany Senior Terraces, NYC’s First Modular Passive House Senior Housing Project
As more developers seek to meet new regulations for energy efficiency, the team at Murray Engineering has set a new record. With the Bethany Senior Terraces project, Murray Engineering has helped to develop NYC’s first modular structure that fully encompasses passive house principles — introducing a new era of energy efficiency in the energy-conscious city that never sleeps.
How LAMOD is Using Modular to Address Inefficiency, Sustainability, and the Future of Construction
As developers, designers, and contractors seek to understand the evolving needs of the modular industry, no one is as well-versed in the benefits of going modular as Mārcis Kreičmanis. As the co-founder and CBDO of LAMOD in Riga, Latvia, Mārcis has made it his ultimate goal to address the inefficiencies of traditional construction.
From Furniture Builder to ‘Activist Architect’: Stuart Emmons’ Unique Journey
Stuart Emmons was fascinated by buildings at a young age. He remembers building sand cities with his brother during trips to the Jersey shore. His father gave him his first drawing table at the age of ten. Today, he is an experienced architect who received his FAIA in June 2025. The road he took is unique, to say the least.
Forge Craft Architecture + Design: Codes, Contracts, and Intellectual Property
Founding Principal and Director of Modular Practice for Forge Craft Architecture + Design, Rommel Sulit, discusses the implications of codes, contracts, and intellectual property on
modular construction.
Eisa Lee, the “Bilingual” Architect
Now as the founder of XL
Architecture and Modular Design in Ontario, Canada, she applies not just her education as a traditional architect but an entire holistic view on modular design. It’s this expansive view that guides her work on being a true partner that bridges the gap between architects and modular factories as they collaborate on the design process.
Tamarack Grove Engineering: Designing for the Modular Sector
The role of a structural engineer is crucial to the success of a modular project, from initial analysis to construction administration. Tamarack Grove offers structural engineering services — project analysis, plan creation, design creation, and construction administration — for commercial, manufacturing, facilities, public services, and modular. Modular is only one market sector the company serves but it is an increasingly popular one.
Engineer Masters the Art of Listening to His Customers
Since founding Modular Structural Consultants, LLC. in 2014, Yurianto has established a steady following of modular and container-based construction clients, primarily manufacturers. His services often include providing engineering calculations, reviewing drawings, and engineering certification
Inside College Road: Engineering the Modules of One of the World’s Tallest Modular Buildings
College Road is a groundbreaking modular residential development in East Croydon, South London by offsite developer and contractor, Tide, its modular company Vision Volumetric (VV), and engineered by MJH Structural Engineers.
Design for Flow: The Overlooked Power of DfMA in Modular Construction
Unlocking higher throughput, lower costs, and fewer redesigns by aligning Lean production flow with design for manufacturing and assembly.
Choosing the Right Ramp
Modular construction offers a compelling alternative to traditional methods for designing and building ADA and IBC-compliant entrances. By addressing the challenges of traditional construction, such as time-consuming processes, unavailable specialized labor, and variable field conditions, modular solutions provide a more efficient, cost-effective, and reliable approach.