Inside the Construction of 355 Sango Court
The 2024 Best of Show for Permanent Modular Construction
This year’s Awards of Distinction winner for Best of Show for Permanent Structures is 355 Sango Court, a 105,818 square foot affordable housing development manufactured by Nampa, Idaho based Autovol. The project team also included Prefab Logic for module design, Nibbi Brothers as the general contractor, Acc U Set Construction as the modular installer, and the overall project design was by David Baker Architects and DCI and Fard. The 102-unit development was constructed in Milpitas, California, and is comprised of 113 modules.
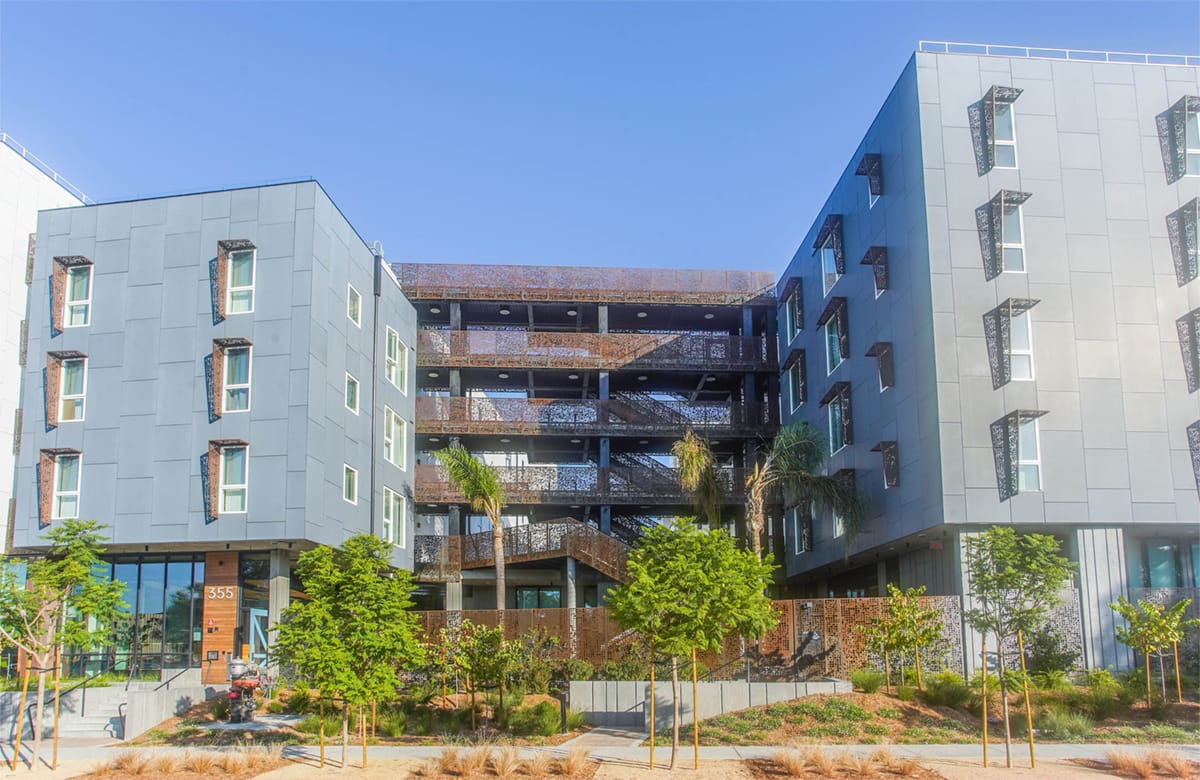
Rick Murdock, CEO and co-founder of Autovol, said it was one of the smoothest projects he’s experienced, which is surprising when you consider that this was the first modular project for the general contractor.
Nibbi Brothers approached Autovol after another manufacturer dropped out of the project. The two had an existing relationship, but no previous modular project experience. Murdock admits he was a bit nervous about taking on the project with a contractor who had no experience with modular construction. “All your alerts are out because there’s a lot of education that has to happen because it’s done differently.” But his nerves were unfounded.
“They worked with us all the way through the project. They were here at the plant really trying to understand how modular works, what are the issues with modular, what are the differences than with a traditionally built project. I was really pleased with the way they dove in and took ownership of their piece of it and did a tremendous job.” Nibbi even staffed a person at the factory to get a better understanding of Autovol’s quality assurance program.
Interestingly, Autovol also learned something from Nibbi Brothers during the project. Nibbi suggested a change in the material used to wrap the units and keep them dry while they are in transit and being installed. Murdock admits he was against it in the beginning because it was different than what they normally did and took more labor. But Nibbi was persistent, so they tried it, and now it has been implemented as the standard for all units going out of Autovol’s factory.
An important part of Autovol’s process is the design and programming for their automated assembly line. In 2016, Murdock and Autovol co-founder Curtis Fletcher started a company to provide those services to Autovol and other modular manufacturers called Prefab Logic. According to Murdock, “There’s a disconnect between developers, general contractors, and modular manufacturers because modular is not as common as we’d like it to be and it’s a different type of building. So, we started the company to help everyone understand how it works.”
A year and a half ago they added a mechanical, electrical, and plumbing engineering group to their team. With in-house engineering they are able to be more efficient with their design process. “That’s one of the things we’re really focused on, trying to make the process better, faster, and more accurate from an engineering and architectural standpoint, so we have fewer coordination issues, improved accuracy, and better documentation for our teams,” said Fletcher.
Prefab Logic’s role in this project was to make the design viable for Autovol’s automated manufacturing, get the project through permitting, and then convert the design to programming language for the robots on the manufacturing floor. Their in-house MEP engineering team played a key part in this process.
Fletcher’s team created a digital twin of the completed structure. “We use it for our customers to preview what we’re doing and see if there’s anything that they would like to change or any comments they have,” said Murdock. All facets of the building are modeled, right down to framing, structural components, MEP locations, and every hole, screw, and nail. The model is also used by the internal manufacturing team to spot issues that might come up on the line.
Once the project is completed, a Navisworks model is then passed on to the owner for use in operations and maintenance.
The project had a pretty aggressive timeline as it needed to fit into Autovol’s production schedule, so the team worked diligently to expedite the design and programming process, which was completed in only four and a half months. Autovol has one of the fastest production lines, so the project’s 102 units took just under two and a half months to manufacture, with the entire project taking 443 days to complete.
The four-story development consists of two concrete and steel buildings connected by a series of linked courtyards, providing access to nature for all residents. On the ground floor there’s a garden entry and open-air lobby, with 102 permanent supportive homes on the floors above. The units are a mix of studios, one-, two-, and three-bedroom apartments. An emphasis was placed on sustainability and energy efficiency, building to CalGreen standards, using WaterSense certified plumbing fixtures, and efficient windows. The facility is managed by Resources for Community Development, which provides rental homes for more than 5,450 people in 25 cities in the region, about one third of which are reserved for people with special needs.
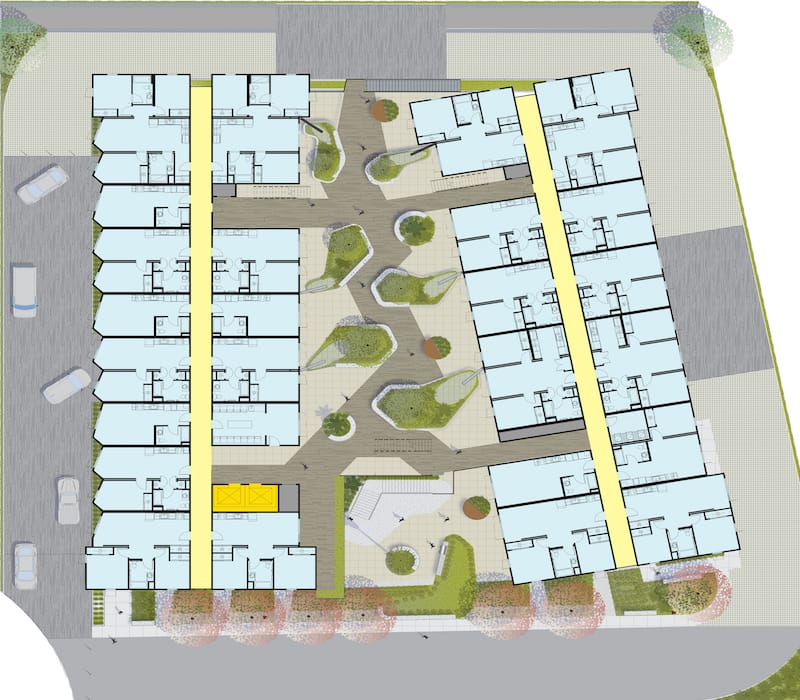
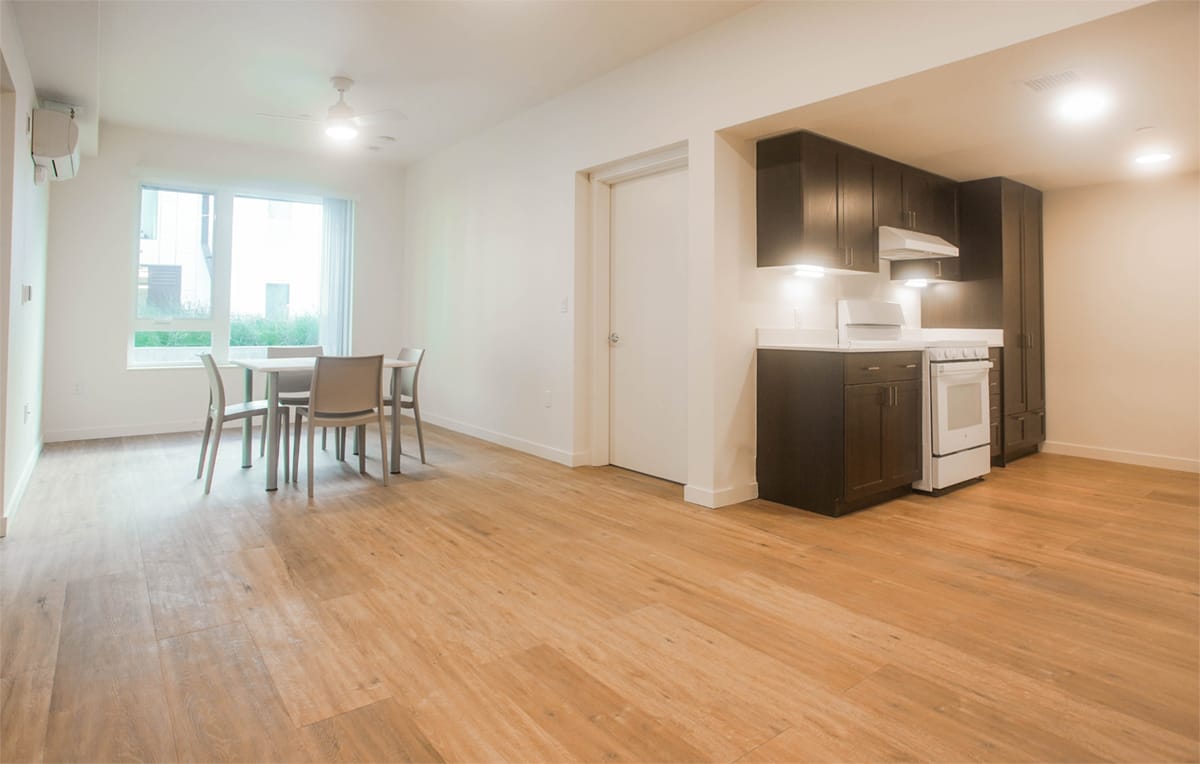
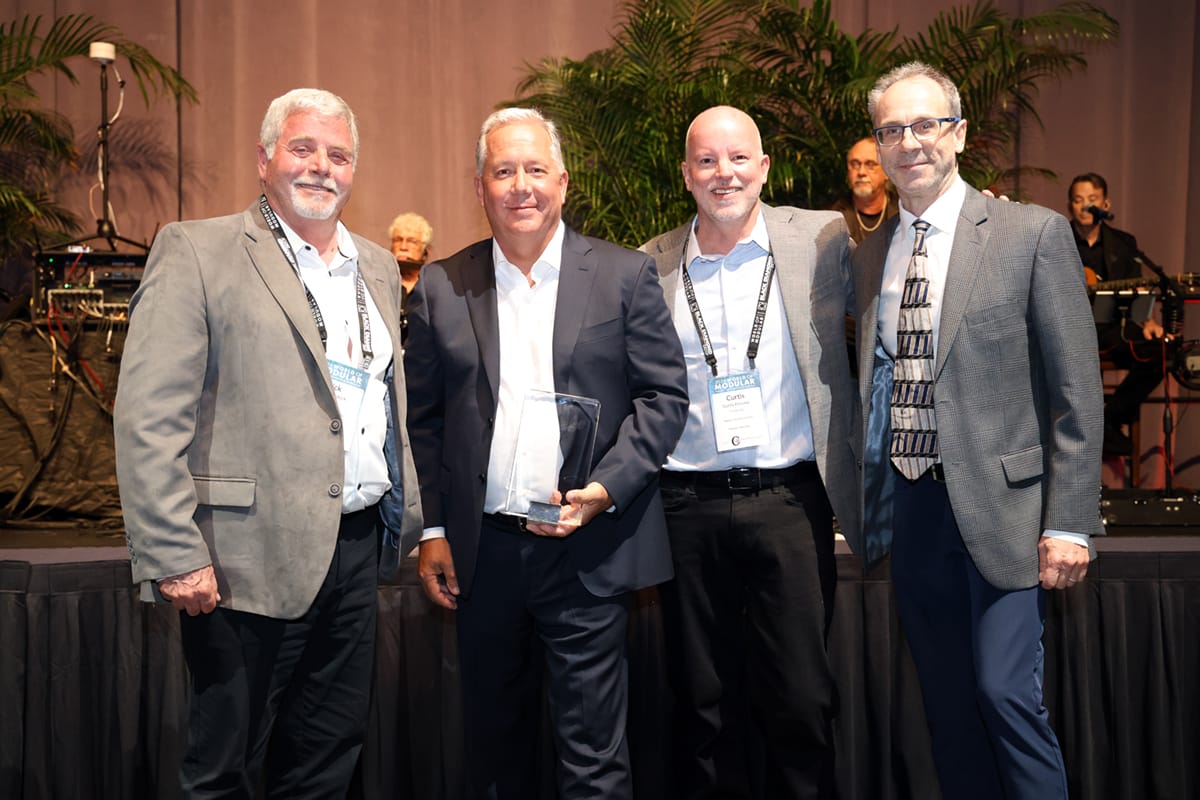
There are significant cost savings for using modular construction on a project like this. Murdock said that developers in the Bay Area could save between $80 to $100 a square foot. And of course, the real benefit is the time savings, as a modular building can be manufactured and assembled significantly quicker than a traditional building.
Autovol boasts the world’s first fully automated volumetric modular factory. At 400,000 square feet the factory utilizes robots to do most of the heavy lifting and repetitive processes, including building the floors, walls, and ceilings, while skilled workers, called “solutioneers,” perform the interior finish work, fixture installation, and mechanical, electrical, and plumbing. Their production rate is an incredible five units a day, which translated into 629,772 square feet of living space in 2023.
Prefab Logic provides services to a variety of modular manufacturers and developers. They can help owners or contractors select a modular factory, work with design teams to design for modular construction, provide digital twin and BIM modeling, and walk projects through the permitting process.
About the Author: Dawn Killough is a freelance construction writer with over 25 years of experience working with construction companies, subcontractors and general contractors. Her published work can be found at dkilloughwriter.com.
More from Modular Advantage
Samantha Taylor: Leading the (Modular) Design of Tomorrow
“With modern technology and the way we’ve all embraced things like BIM, file sharing, and video conferencing since COVID, it’s easy to collaborate with companies in Austria, or Singapore, or anywhere else in the world.”
Greg DeLeon: Military Engineering to Modular Design
Greg DeLeon, a structural engineer at ISE Structural Engineers in Temecula, California, can tell you not only how large a beam needs to be to support a house, but also how much explosives you’ll need to take it down, thanks to his unique combination of professional and military experience.
To Remake North Minneapolis, Devean George Swaps Basketball for Buildings
He’s lived in Los Angeles, Dallas, and San Francisco (to name a few). He’s delivered championships with the Los Angeles Lakers and made career-defining moves with the Dallas Mavericks and the Golden State Warriors. No matter the wins, the championships, or even the seemingly impossible 3-pointers, Devean George has always returned to where it all started for him: Minneapolis.
Chelsi Tryon: Making the World a Better Place
For Chelsi Tryon, Director of Environmental, Social, and Governance (ESG) for WillScot Mobile Mini, nothing is more enjoyable than increasing the
company’s sustainability efforts while simultaneously doing her bit to save the environment.
Joshua Hart: Pushing Boundaries
Joshua Hart, P.E., vice president at Modular
Solutions, can sum up his job responsibilities in one sentence: “I do whatever needs to be done.” Hart thrives on the variety and the opportunity to be involved in every aspect of the company. And it shows! You might say Hart has come full circle.
Jamie Metzger: From Construction to Apparel and Back Again
Growing up in a blue-collar city like Edmonton, Alberta, Canada, it’s no surprise that Jamie Metzger spent some time working labor jobs on construction sites. It’s one of the most common summer jobs in the city. But that’s probably the last predictable thing about this particular story.
Victor Masso: Expanding Modular in Puerto Rico
Victor Masso joined 2 Go Storage, a company started by his grandfather and father, in 2018 to develop a modular building division in the wake of the devastation caused by Hurricane Maria in 2017. Prior to joining the company, he had worked in the industry for about four years focusing on pharmaceutical, commercial, and government projects.
Eliyah Ryals: Finding the Perfect Fit
It’s not common for people to find their perfect career fit straight out of college. It’s even less common to find it in the town you grew up in. But that’s exactly what happened when Eliyah Ryals was told about vacancies at Panel Built and made the decision to apply.
Through It All, It’s Still About the Workers
By February 2024, the number of available, unfilled construction job openings had reached an all-time high. At some point, interest rates will fall, creating another surge in demand for such workers. In short, solving the nation’s skilled worker shortage issue has never been more important.
Navigating Insurance Challenges in the Modular Construction Industry
Utilizing practical written minimum insurance and indemnity requirements, along with monitoring certificates of insurance by someone who has COI training will not yield a perfect risk transfer strategy, but the exposure will be managed much better than it likely is currently.