Only the Future is at Stake
A new report from Anirban Basu, chairman & CEO of Sage Policy Group and Chief Economist of the Modular Building Institute
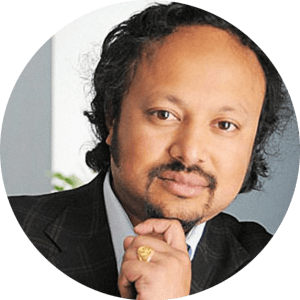
Anirban Basu is chairman & CEO of Sage Policy Group and Chief Economist of the Modular Building Institute
Climate Debates Get Heated
As of this writing, many of the world’s leaders are engaged in discussions at the 28th meeting of the Conference of the Parties to the United Nations Framework Convention on Climate Change, known simply as COP28. This year, the President of COP28 is none other than Sultan Al Jaber of the United Arab Emirates (UAE), who got the festivities started by suggesting that there is “no science” indicating that a phase-out of fossil fuels is required to restrict global temperate increase to 1.5 Celsius or 2.7 degrees Fahrenheit.
Many disagreed, loudly. As indicated by The Guardian, more than 100 nations already support phasing out fossil fuels. Whether the final COP28 agreement will call for a phase-out or will adopt diluted language is one of the most contentious issues at the summit.
As with many economic matters, there is underlying the tension between social goals and perceived economic well-being. For oil producing nations, the move away from fossil fuels represents something approaching an existential threat. According to the US Energy Information Administration’s International Energy Statistics database, the UAE was the world’s seventh-largest total liquid fuels producer in 2022 and third largest among OPEC members.
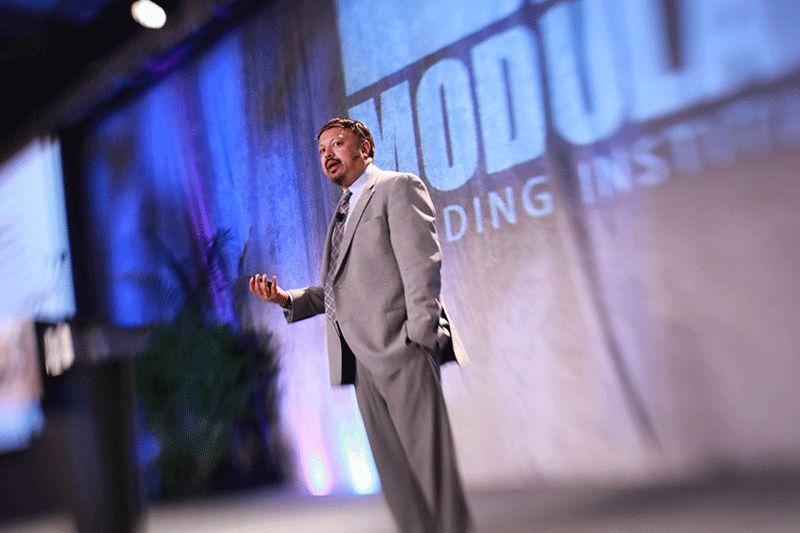
Anirban Basu speaks at MBI's annual World of Modular conference and tradeshow.
The movement away from fossil fuels also represents a source of inconvenience and cost among many American households. Many Americans like the flexibility and associated range of their gasoline-fired V-6s and V-8s. They like their gas stoves, propane-powered grills, and the rumble of a lawnmowers. Electrification would require abandoning many of the appliances and vehicles to which Americans have become accustomed. The transition to electric appliances and vehicles also stands to be expensive, as does electricity as utilities also shift away from fossil fuels.
For many onlookers, the world is engaged in a race. If the movement toward cleaner, greener economic activity takes too long, the world will suffer. While there are climate change skeptics, many leading scientists have concluded that the world will be fundamentally altered if the world warms by 1.5 degrees Celsius or more. Some conclude that at 1.5 degrees Celsius, 70 to 90 percent of coral reefs will die globally. At 2 degrees, the figure rises to approximately 99 percent. About 500 million people depend on those reefs for both food and livelihoods according to information acquired by NPR climate correspondent Lauren Summer.
Still others warn that at 1.5 degrees Celsius, the Greenland Ice Sheet would collapse, altering ocean currents. Degradation of the Amazon rainforest would further elevate emissions. Flooding would become rampant, destroying waterfront communities and tax bases in the process. Some scientists believe that the world is destined to surpass 1.5 degrees Celsius of warming, and the question is really what can be done to get the globe back to workable temperatures.
How Modular Building Can Help
Construction is infamous among the pantheon of industries in terms of its resistance to change. It is associated with slow productivity growth and modest evolutions in the mechanisms by which construction services are delivered. The reluctance to change is evident in the, which suggests that modular’s market share is edging higher as opposed to ramping higher aggressively.
That may be about to change, and environmental conditions have much to do with that. The bad news is that building operations and construction account for nearly 40 percent of global energy-related CO2 emissions. The good news is that changes in how construction services are delivered can supply major benefits in the war on climate change.
Environmental implications extend beyond waste produced. Noise pollution from construction sites disrupts local ecosystems, including impacting wildlife communication and behavior. Moreover, the industry stands as a major global consumer of resources, a fact highlighted by European Union data indicating that building construction consumes 40 percent of materials and primary energy while generating 40 percent of waste. Traditional construction techniques also impact water quality by injecting diesel, fossil fuels, paints, solvents, and other toxic chemicals into the environment.
Enter modular construction. By prefabricating components in a controlled factory setting, modular building minimizes waste, reduces onsite construction activities, and, as a result, significantly lowers overall environmental impacts. A noteworthy study by Professor Mohammed Al-Hussein at the University of Alberta reveals that modular construction could cut CO2 emissions by 43 percent on standard projects. This reduction is attributable to efficient use of resources and reduced construction time associated with modular methods.
There is more. A peer-reviewed study published in the Journal of Industrial Ecology and conducted by the University of Virginia indicates that modular homes typically use about 17 percent less material. If one extends that result to global housing requirements, the implications are mind-bending.
Looking Ahead
The Modular Building Institute along with other sources of leadership have been advocating for modular construction along several key dimensions, including cost containment, delivery speed, precision, appeal to emerging workforce members, and now the environment. As the race to reverse global warming intensifies, there is little doubt that modular techniques will be adopted with far greater frequency than has been the case to date. Meanwhile, modular building continues to offer its more traditional benefits to project owners, but the issues facing society are far more pressing these days than simply helping project owners make their pro-formas pencil out.
More from Modular Advantage
AI, Faster Sets, and Automation: The Future of Modular is at World of Modular
While the modular building industry has long known that it can be an effective solution to increase affordable housing, the word is slowly spreading to more mainstream audiences. Three presentations at this year’s World of Modular in Las Vegas hope to provide insight and direction for those seeking a real solution to the crisis.
An Insider’s Guide to the 2025 World of Modular
The Modular Building Institute is bringing its global World of Modular (WOM) event back to Las Vegas, and with it comes some of the industry’s best opportunities for networking, business development, and education. Over the course of the conference’s four days, there will be numerous opportunities for attendees to connect, learn, and leverage event resources to get the most out of the conference.
Affordable Housing Now: The Industry’s Best Bring New Solutions to World of Modular
While the modular building industry has long known that it can be an effective solution to increase affordable housing, the word is slowly spreading to more mainstream audiences. Three presentations at this year’s World of Modular in Las Vegas hope to provide insight and direction for those seeking a real solution to the crisis.
Opportunities for Innovation in Modular Offsite Construction
Modular Offsite Construction has already shattered the myth that it only produces uninspired, box-like designs. Architectural innovations in module geometry, configurations, materials, and products make it possible to create visually stunning buildings without sacrificing functionality or efficiency.
Safe Modular Construction with Aerofilm Air Caster Transport
In collaboration with Aerofilm Systems, Heijmans developed innovative skids using air caster technology for moving modules easily and safely. These pallets are equipped with an auto-flow system, making operation extremely simple.
Miles, Modules, and Memes: Building a Modular Network One Flight at a Time
At the end of the day, social media is just another tool for building connections, and like any other tool, needs to be used skillfully to work properly. Use social media thoughtfully, and it will open doors to real opportunities and relationships you didn’t even see coming.
Falcon Structures: Thinking Inside the Box
Some of Falcon’s latest projects include creating container solutions for New York’s Central Park and an East Coast professional baseball team. More and more, Falcon is shipping out container bathrooms and locker rooms to improve traditionally difficult work environments, like those in oil and gas or construction.
UrbanBloc—From Passion to Industry Leader
UrbanBloc specializes in three main categories or markets – what they call “Phase 0” projects, amenities, and urban infill. Clients are often attracted to shipping containers because from a real estate perspective they are considered an asset. Having the flexibility to move and transport these assets allows owners to respond to different circumstances in a fluid manner that they can’t get with standard construction.
The Hospitality Game-Changer
“Hospitality is about more than just providing a service – it’s about delivering an experience,” says Anthony Halsch, CEO of ROXBOX. “And that’s where containers thrive. They allow us to create spaces that are unique, efficient, and sustainable.”
Container Conversions Counts on Simplicity to Provide Critical Solutions
Container Conversions has fabricated and developed thousands of containers for varied projects, including rental refrigeration options, offices, kitchens, temporary workplace housing, and mobile health clinics.