Container Conversions Counts on Simplicity to Provide Critical Solutions
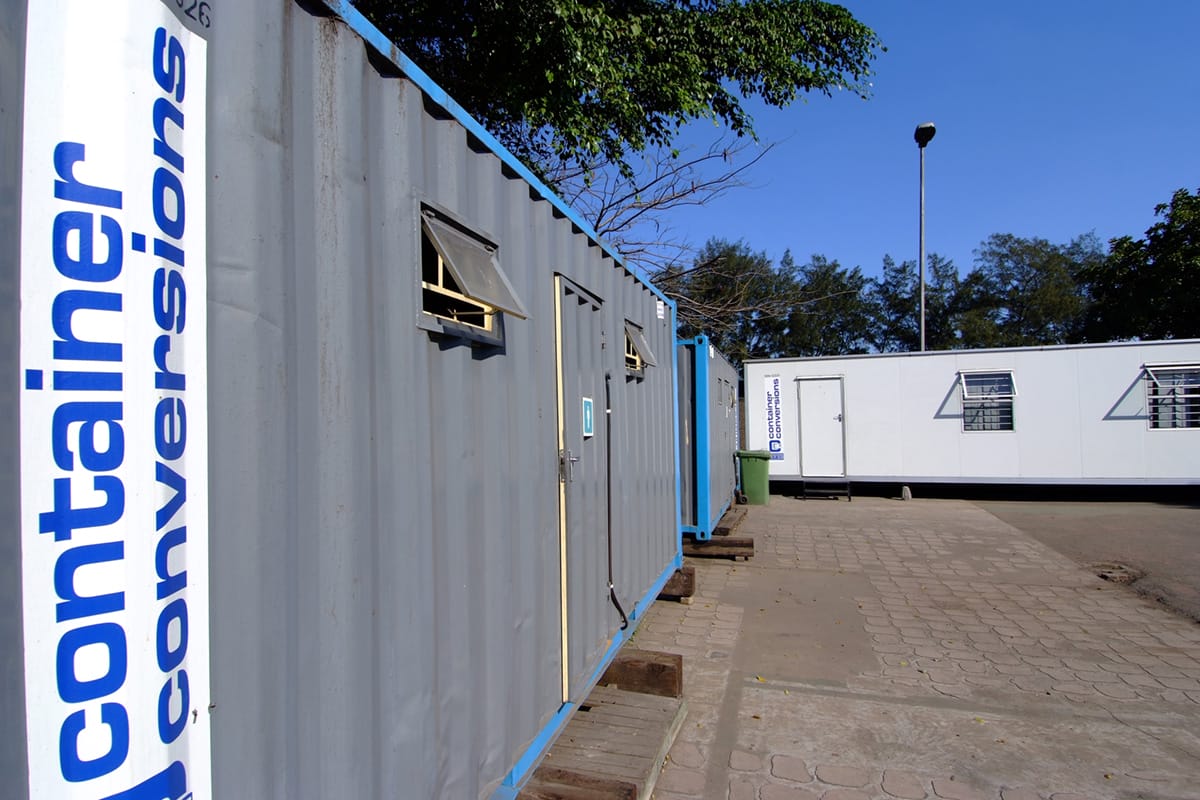
Container Conversions PTY Ltd. has always been in the container business. The South Africa-based company started out converting wooden railway carriages and shipping containers, expanding their business to include modular offerings in the mid-1990s.
Originally based out of Durban, KwaZulu-Natal, Container Conversions has since expanded to include branches in Pretoria, Johannesburg, and Cape Town. The company also owns five depots where they prefabricate modules off-site, servicing all of South Africa and a host of neighboring countries. But the company has the ability to export throughout Africa and beyond.
Container Conversions has fabricated and developed thousands of containers for varied projects, including rental refrigeration options, offices, kitchens, temporary workplace housing, and mobile health clinics.
Because of their location, Container Conversions has also developed highly insulated projects for use in Antarctica.
In 2014, the company created Modular Site Solutions as a separate export division to continue modular fabrication. Container Conversions also acquired Big Box Containers in 2023 to amplify their existing container business and expand geographically in South Africa.
Three Reasons to Go Container-First
CEO Guy Murray says there are three main advantages to using containers: durability, versatility, and speed. Container Conversions sources their containers from a few different places, such as international container retailers, shipping companies, and container factories in China.
“The structures are strong, built to withstand extreme conditions, and with care, their lifespan can be extended significantly,” he said.
With five depots across South Africa, Container Conversions can transport modules with a dedicated truck fleet in one to two days. They also ship projects from Durban, which hosts one of the busiest ports in Africa.
“We are pretty much a springboard for anybody that wants to do work in Africa,” says Group Marketing Executive Willie Ward.
For customers looking to expand or create different structures, stacking or joining is a viable option, which speaks directly to the versatility offered by containers. According to Guy, an average project can take about two to three months, “depending on scale and technicality, whilst more standard conversions can be mere weeks.”
They are also easily moved, which is a plus for customers that require temporary work housing or facilities.
Lastly, because of their predetermined dimensions, containers are already self-made structures that aid in the “rapid plug-and-play accommodation solution,” says Guy.
“We find them ideally suited to projects with short lead times where the solution is temporary or intermediate, and where space constraints necessitate stacking into two or three stories.”
Providing Infrastructure for Hard-to-Reach Areas
Part of what makes Container Conversions as a company so successful lies in their location. They can mobilize and provide turnkey solutions in rural areas where resources are scant. One such case was in 2020, at the start of the COVID pandemic.
The company was tasked with developing a 12-to-24 bed COVID isolation ward for a rural area in KwaZulu-Natal and to have it up and running as soon as possible. They developed a 360 square meter ICU facility with an ancillary building that is still in use to today as a primary healthcare facility.
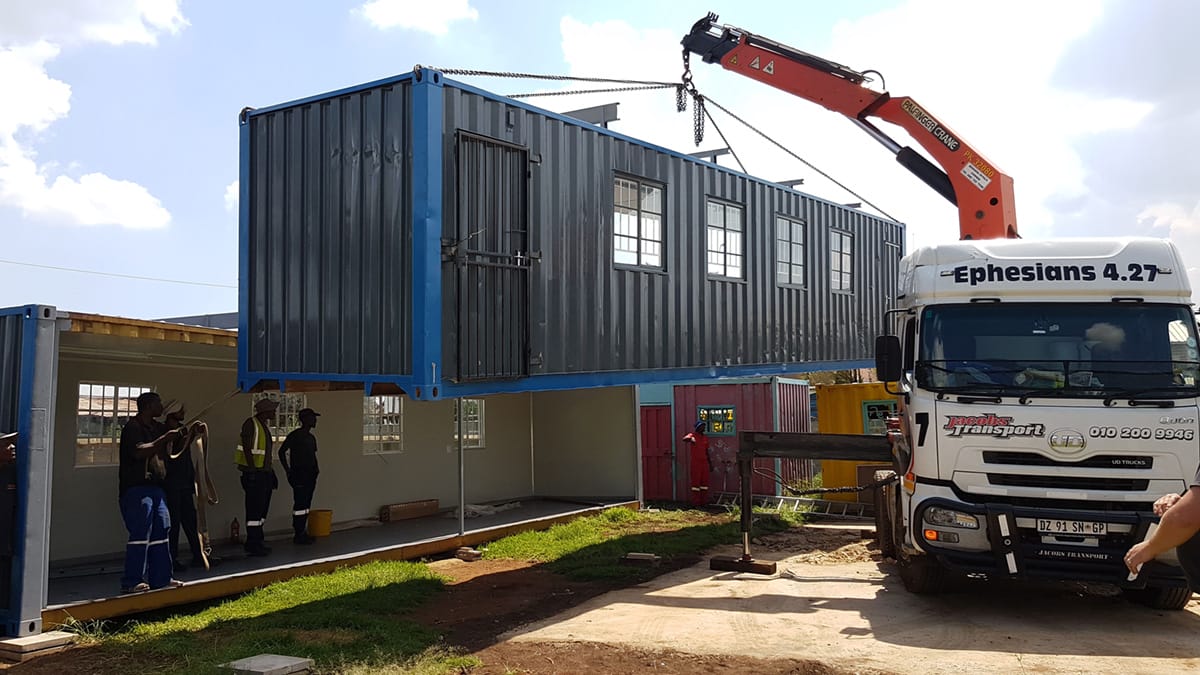
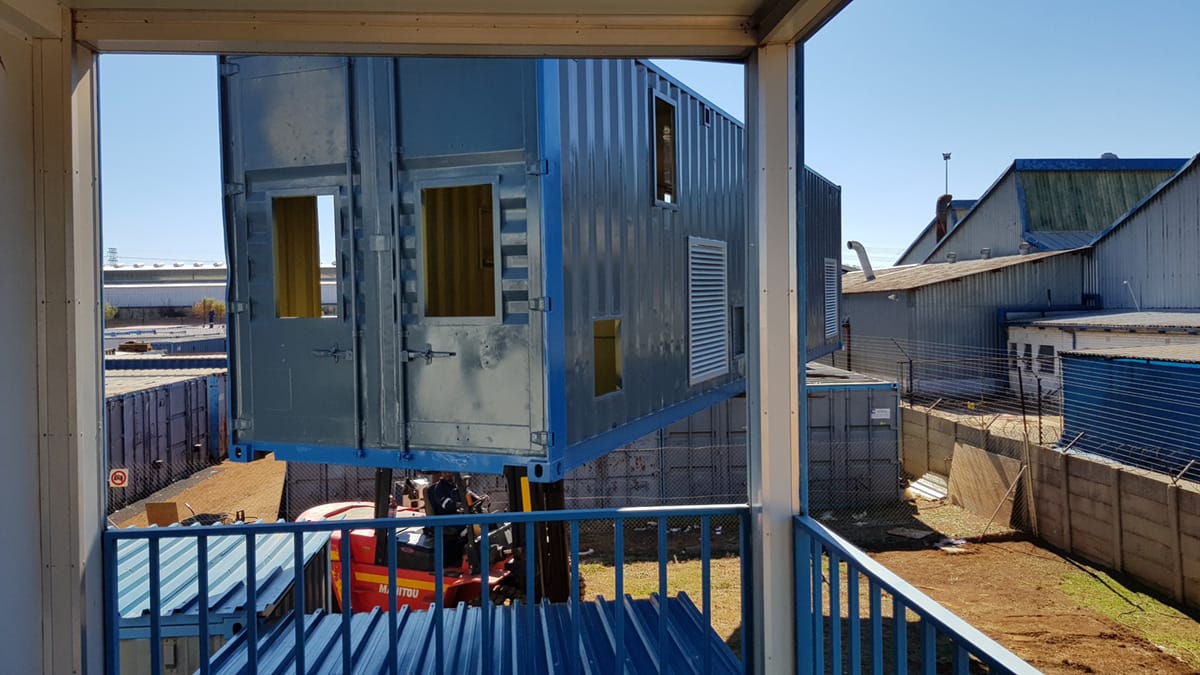
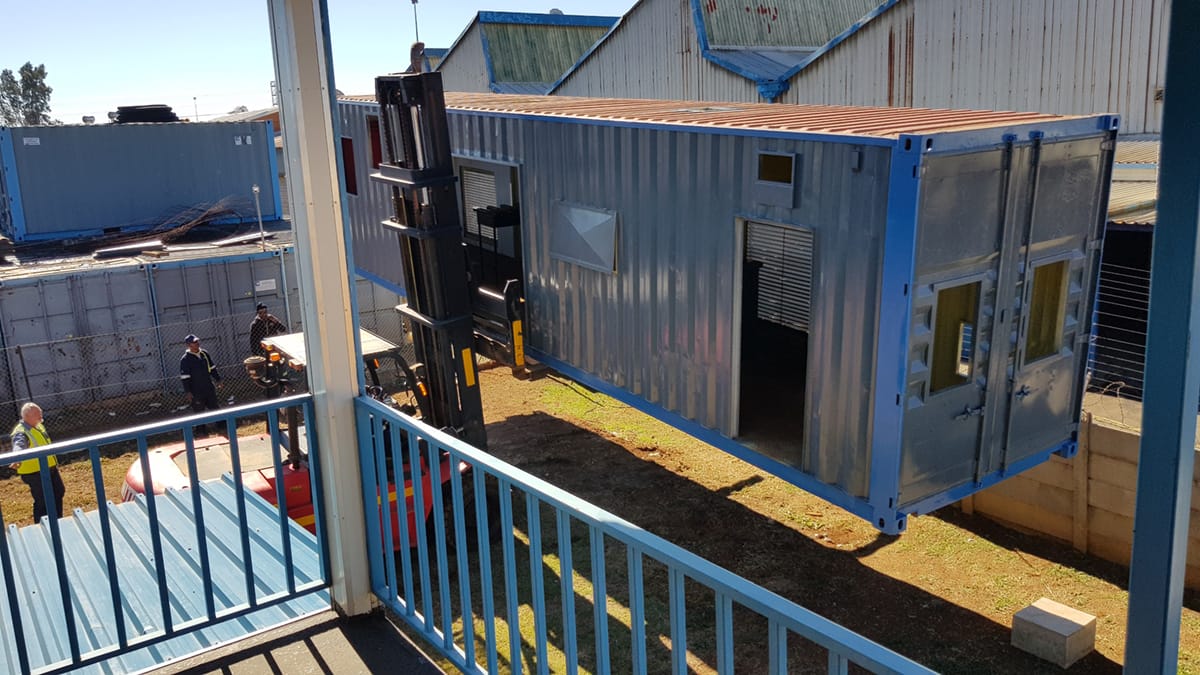
“Conventional building, especially in the remote rural area allocated, could not have met the imposed deadlines and consequently modular construction was identified as the preferred building method,” said Guy. “Modular Site Solutions was awarded the contract and essential supplier status to operate during lockdown in April 2020. The new hospital ward admitted their first COVID patient on March 7, 2020.”
Due to the stringent requirements set by the Department of Health in South Africa, this building had a variety of special furnishings and MEP designs, including “positive pressure ducted air-conditioning,” said Guy. Additionally, the ancillary building—another shipping container unit—protected the manifolds and vacuum suction required to keep the isolation ward sterile. All the initial modifications were done off-site so the buildings could truly be “plug and play.”
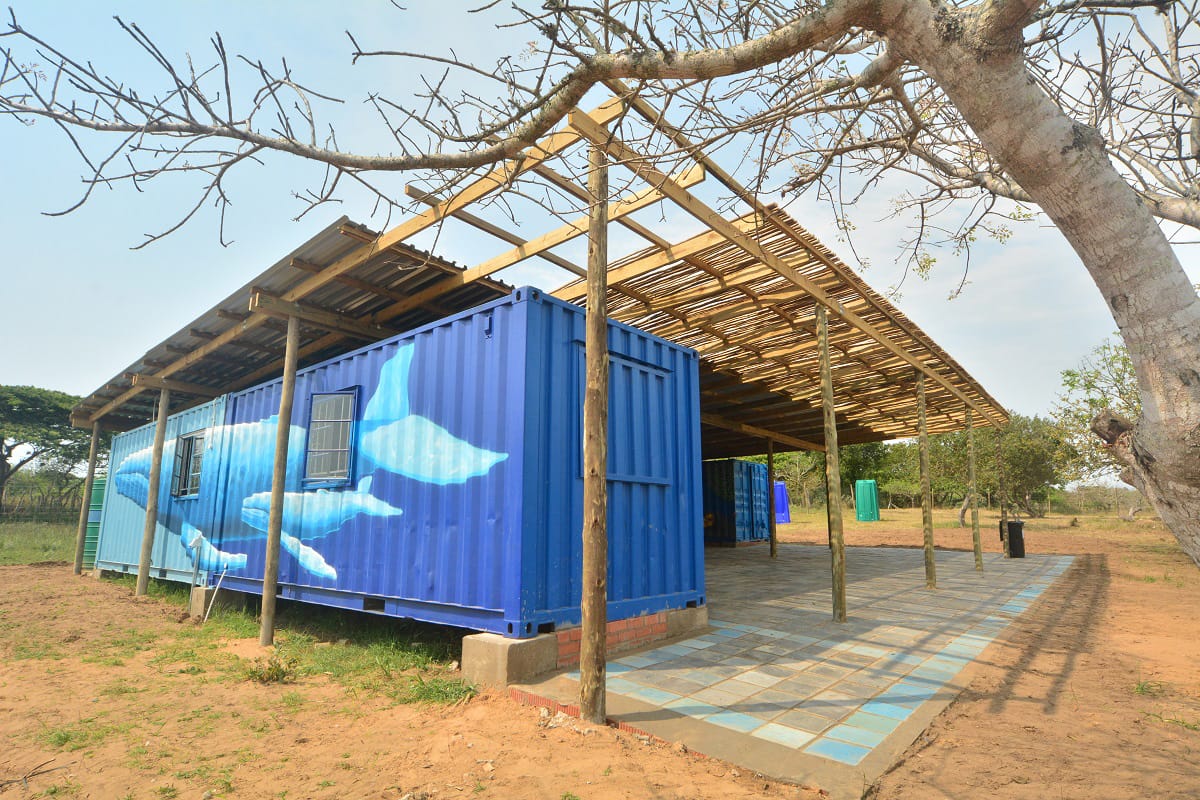
Mobility Leads to Accessibility with Containers
Container Conversions has also worked to produce one-of-a-kind sanitation solutions to address health and safety issues across South Africa. According to the Associated Press, the Department of Basic Education says that as of 2023, over 3,300 schools still use pit latrines—outhouses that feature 10-foot holes with a concrete or wooden slab covering used to collect human waste. These pit latrines pose a dangerous hazard to children, as they can fall in and drown.
“There is a dire need to provide sanitation in rural schools and outlying areas where there is limited services and infrastructure,” said Guy. “Many of these areas use pit latrine toilets which are dangerous and unhealthy for the occupants.”
In 2023, they developed a container unit alongside the company Waterloo that reuses water within a closed circuit, requiring no hookups to sewer connections or fresh water. Over the course of a year, the two companies worked together to create a unique system that recycles and cleans water within a toileting system. The unit comes with a 6,500-liter capacity recycled water tank, alongside a bioreactor and disinfection tank.
According to Willie, the Waterloo solution features one container with a raised platform with eight toilets on top of the tank filtration system. For larger sites, an additional container can be provided to store materials.
One of these self-contained toilet units was tested at a secondary school in Newcastle, KwaZulu-Natal and proved to be a success. The two companies trialed eight additional toilets that were in use by up to 1600 students.
Waterloo is now working to market the container toilet solution system to the Department of Education in South Africa in addition to other global nonprofits and companies that have strong corporate social responsibility aims.
It’s this work that makes Container Conversions stand out as a company, while they also seek to furnish container units and modules for other more “traditional industries” and uses, like living spaces.
Making Living Quarters Available for Tough Jobs
Containers have also been used to provide temporary housing for those in remote work areas. Guy says that there are a host of companies that look for temporary housing for their workforce in a number of situations. The company is currently developing a large workforce housing project for a mining company out in Mozambique. The project includes about 100 container units that include “offices, boardrooms, sanitation blocks, and sleeping quarters,” says Guy.
In a nod back to its railway carriage days, the company has also developed four unique containers for a train transport company that requires a three-person staff for maintenance. The four containers feature several amenities that make it easy for the staff to rest, cook, wash, and live as they travel across remote train routes in Africa.
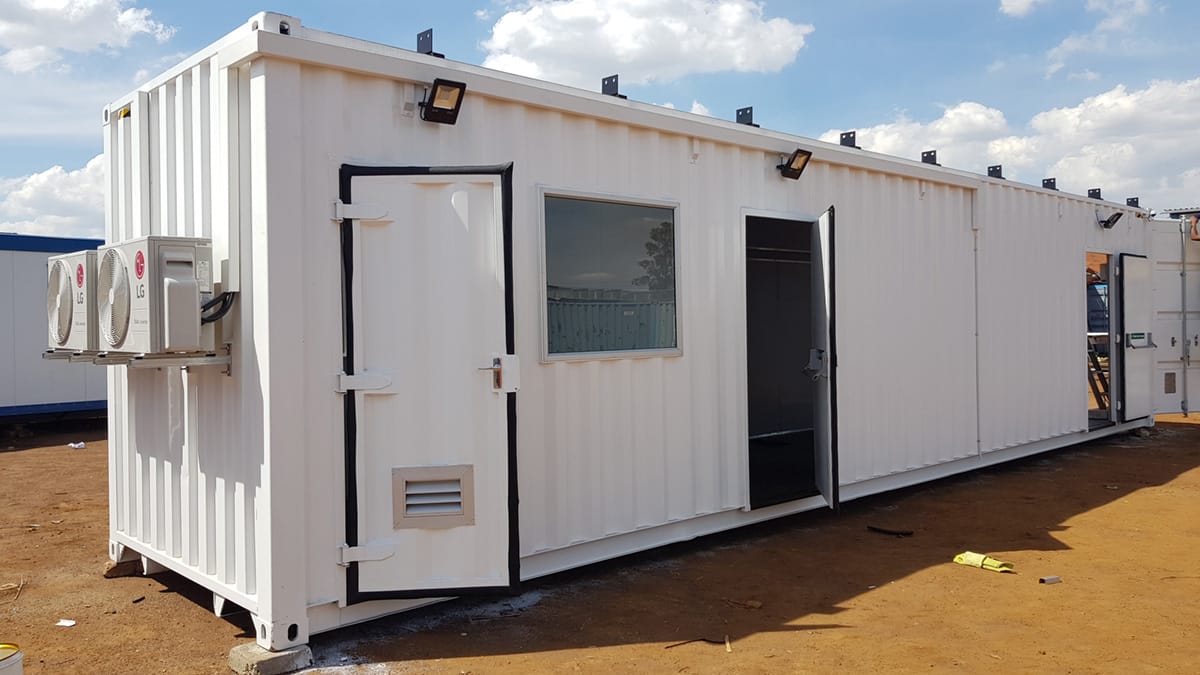
Container Design is About Simplicity
At the end of the day, Guy and his team at Container Conversions stay on top of their business by providing a mix of rental offerings and unique modular designs, as noted by the variety of their projects.
However, in order to keep the train chugging along, Guy says that it’s important to keep everything simple.
“Keep the design simple and functional,” he says. “This will allow for faster output times and reduced costs. Be very clear on what must be achieved by the project. Sometimes a container is not the best solution and that is where other modular products come in. But understanding your space, what you want to do inside the space—and the transport logistics involved—is key.”
About the Author: Karen P. Rivera is a freelance writer and editor with a passion for storytelling. She is a former United Nations-based reporter, with experience covering international breaking news, venture capital, emerging healthcare tech, and the video game industry.
More from Modular Advantage
Oregon’s Prevailing Wage Proposal: A Wake-Up Call for Modular Construction
In early February, 2024, the Massachusetts Board of Building Regulations and Standards (BBRS) released its proposed 10th Edition building codes. This draft included several amendments targeting modular construction that would have created an extremely difficult environment for the entire modular industry and could have eliminated the industry entirely in the state.
Behind the Design of Bethany Senior Terraces, NYC’s First Modular Passive House Senior Housing Project
As more developers seek to meet new regulations for energy efficiency, the team at Murray Engineering has set a new record. With the Bethany Senior Terraces project, Murray Engineering has helped to develop NYC’s first modular structure that fully encompasses passive house principles — introducing a new era of energy efficiency in the energy-conscious city that never sleeps.
How LAMOD is Using Modular to Address Inefficiency, Sustainability, and the Future of Construction
As developers, designers, and contractors seek to understand the evolving needs of the modular industry, no one is as well-versed in the benefits of going modular as Mārcis Kreičmanis. As the co-founder and CBDO of LAMOD in Riga, Latvia, Mārcis has made it his ultimate goal to address the inefficiencies of traditional construction.
From Furniture Builder to ‘Activist Architect’: Stuart Emmons’ Unique Journey
Stuart Emmons was fascinated by buildings at a young age. He remembers building sand cities with his brother during trips to the Jersey shore. His father gave him his first drawing table at the age of ten. Today, he is an experienced architect who received his FAIA in June 2025. The road he took is unique, to say the least.
Forge Craft Architecture + Design: Codes, Contracts, and Intellectual Property
Founding Principal and Director of Modular Practice for Forge Craft Architecture + Design, Rommel Sulit, discusses the implications of codes, contracts, and intellectual property on
modular construction.
Eisa Lee, the “Bilingual” Architect
Now as the founder of XL
Architecture and Modular Design in Ontario, Canada, she applies not just her education as a traditional architect but an entire holistic view on modular design. It’s this expansive view that guides her work on being a true partner that bridges the gap between architects and modular factories as they collaborate on the design process.
Tamarack Grove Engineering: Designing for the Modular Sector
The role of a structural engineer is crucial to the success of a modular project, from initial analysis to construction administration. Tamarack Grove offers structural engineering services — project analysis, plan creation, design creation, and construction administration — for commercial, manufacturing, facilities, public services, and modular. Modular is only one market sector the company serves but it is an increasingly popular one.
Engineer Masters the Art of Listening to His Customers
Since founding Modular Structural Consultants, LLC. in 2014, Yurianto has established a steady following of modular and container-based construction clients, primarily manufacturers. His services often include providing engineering calculations, reviewing drawings, and engineering certification
Inside College Road: Engineering the Modules of One of the World’s Tallest Modular Buildings
College Road is a groundbreaking modular residential development in East Croydon, South London by offsite developer and contractor, Tide, its modular company Vision Volumetric (VV), and engineered by MJH Structural Engineers.
Design for Flow: The Overlooked Power of DfMA in Modular Construction
Unlocking higher throughput, lower costs, and fewer redesigns by aligning Lean production flow with design for manufacturing and assembly.