UrbanBloc—From Passion to Industry Leader
After an extreme career change, the drive for continual improvement leads this shipping container building manufacturer to excellence.
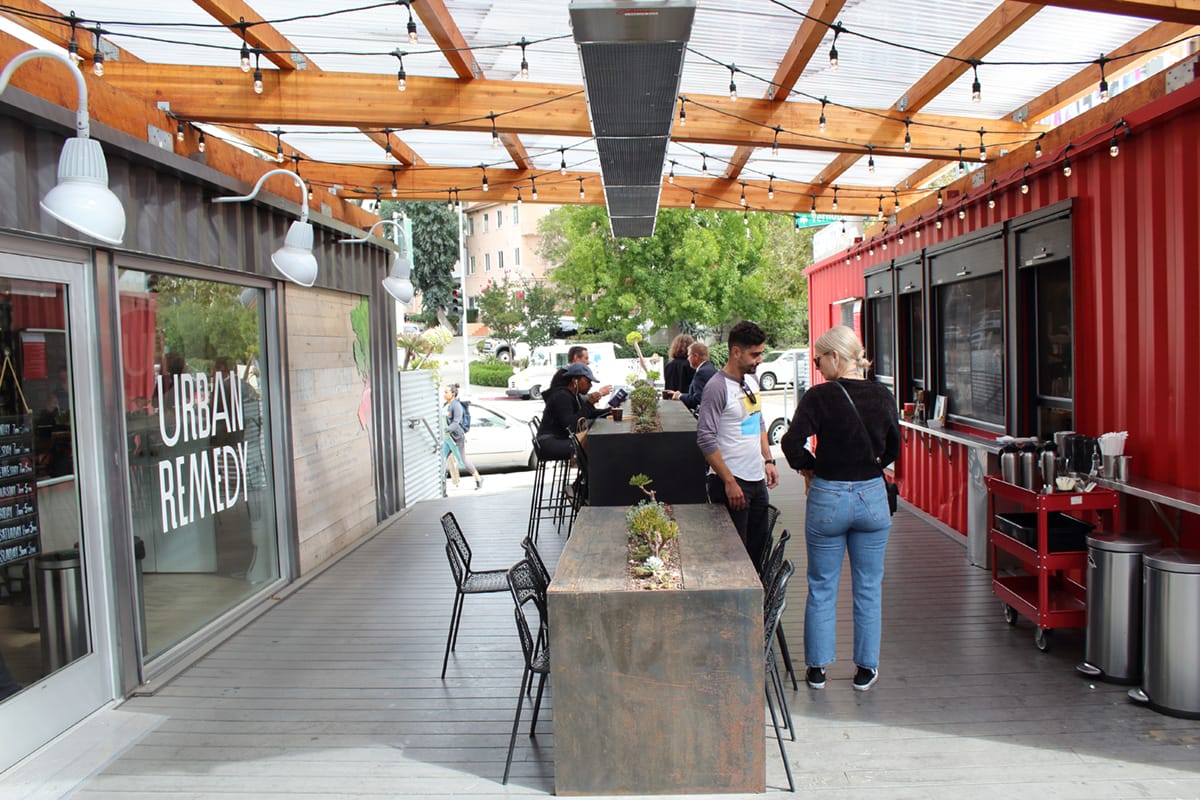
It was quite a career shift for Martha Trela, President and CEO of UrbanBloc – from DNA researcher to modular construction company owner. She partnered with Jerry Jameson, a California architect, to start the shipping container building company in 2014, and their first project had a high-profile client – the San Francisco Giants baseball team.
“It turned out to be a very large project for us,” Trela said, “and we had to really scramble to pull together every aspect of our business while working on a very high-profile project on a very tight timeline. We did it, but in the process, we really learned a lot.” Continual improvement has been Trela’s mantra over her ten years with UrbanBloc, almost a necessity considering her background.
After 25 years in the life sciences, she was ready for a change.
“I ran across a project in San Francisco that really caught my attention. It was in Hayes Valley, which was a transforming neighborhood, and the city owned this piece of land and had a long-term development plan for it, but they wanted to activate the site in the short term to help transform the neighborhood from a kind of sketchy area into much more of a destination area. They put out an RFP for a five-year project bringing in buildings that could be moved in the future that could support new entrepreneurs, in particular underserved women owned businesses. And they were all made out of shipping containers. I was so fascinated by the concept of utilizing little scraps of land in certain areas to affect urban transformation, to support underserved populations, and provide a retail space for new businesses to get launched, and ultimately provide social activation. I just couldn’t shake it.”
The passion born by learning about this project and following up with more research led Trela to take a new path – starting a modular construction company that specialized in using shipping containers. And over 80 projects in, her experience has led her, and others on her team, to some interesting places.
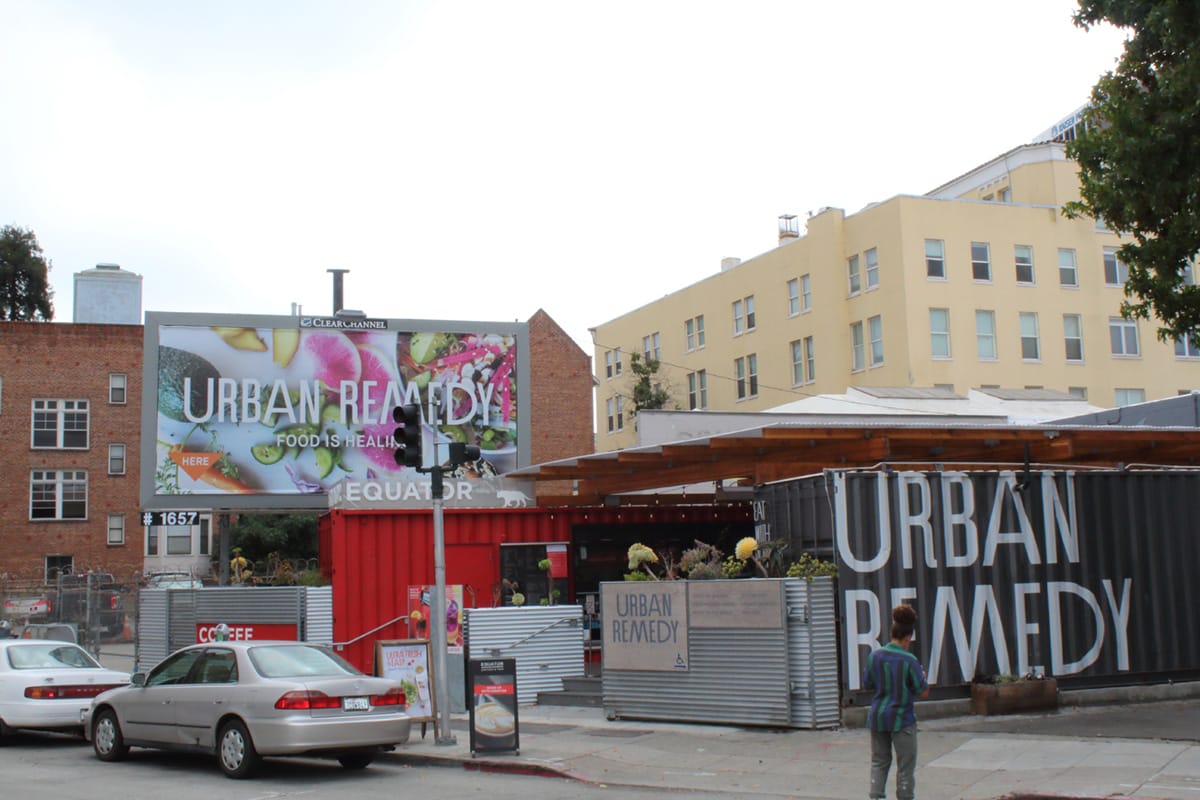
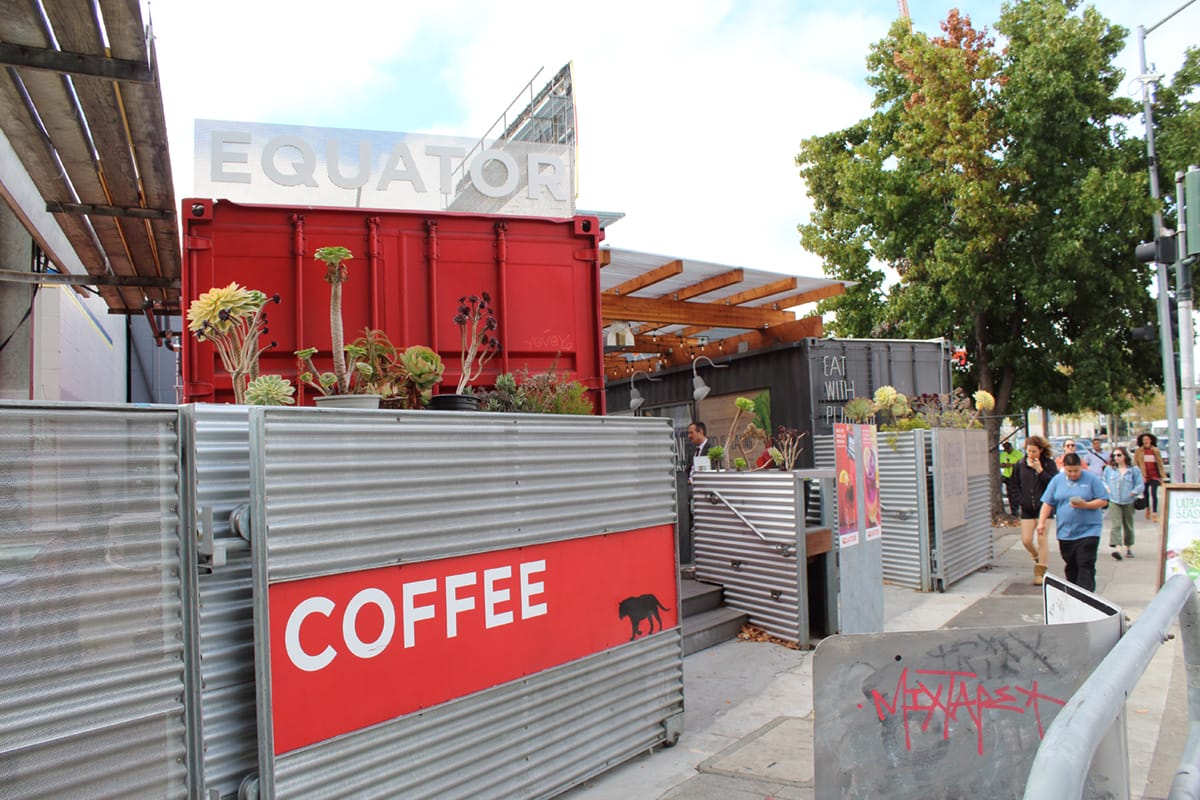
Driving Positive Social Change
UrbanBloc specializes in three main categories or markets – what they call “Phase 0” projects, amenities, and urban infill.
Phase 0 projects are precursors to a long-term development, like the revitalization project that first sparked Trela’s interest. Often temporary buildings are brought in for a defined period of time, 5, 7, or even 10 years, with the plan to remove them when the planned building or development begins construction. This is done for financial or strategic purposes.
UrbanBloc’s first project for the San Francisco Giants was a phase 0 project that was designed to support local businesses. The project included a space for community education, food, a beer garden, and a dog park. Everything was built using shipping containers, which were assembled off site and then delivered once the site work was completed. When construction of the larger project was set to start, the containers could be easily disconnected and moved or repurposed. “For these types of developments shipping containers are actually a great option because of their transportability and mobility. If someone wants to pick them up, move them to another location, or sell them to a second client, they can,” said Trela.
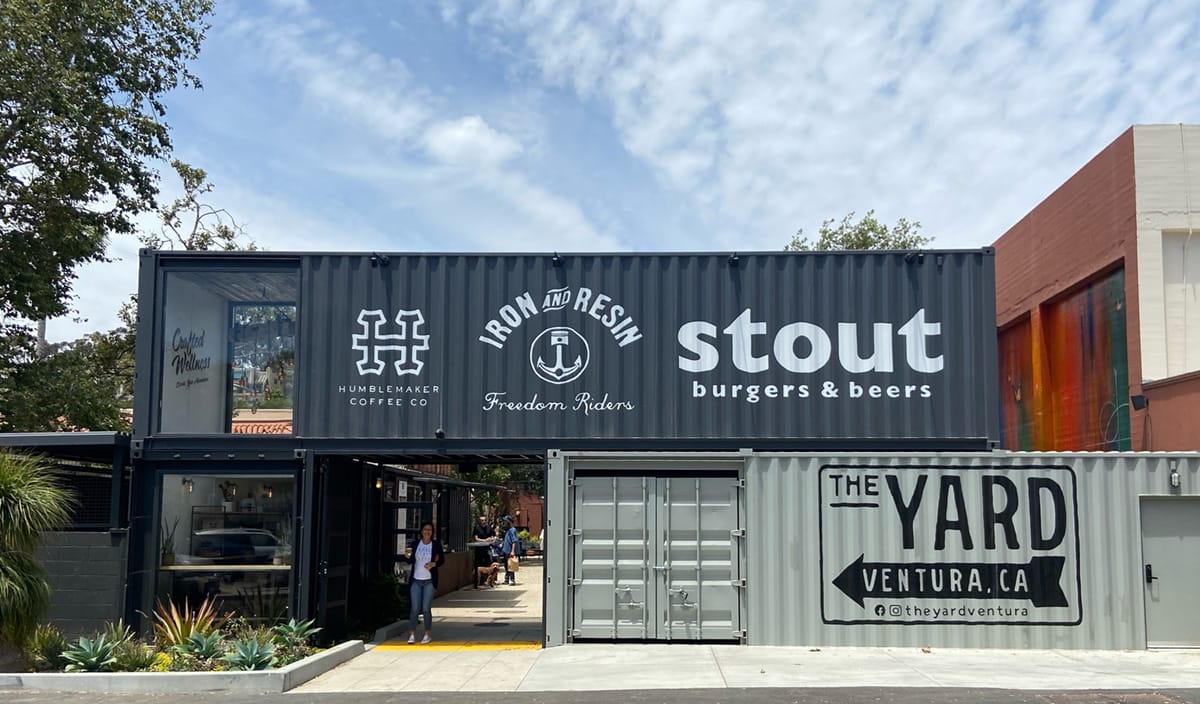
Amenities projects are added to another building or development to fill space, meet jurisdictional requirements, or as an added feature. A developer in southern California hired them to build a combination coffee shop, café, and bar that transitioned from one purpose to the next as the day progressed. The owner used it as an added draw when leasing out space in their office development.
Another high profile UrbanBloc amenity project sits outside the entrance to the BMO soccer stadium in Los Angeles. A shipping container in front of the ticket gates allows visitors to enjoy beer, wine, margaritas, or ice cream as they wait to be let into the stadium. This project was a bit of a challenge because all sides of the container had to be branded, so the team used wood and metal to create a unique look, including a 20-foot sliding wood barn door.
Urban infill projects are meant to help a neighborhood or area transition into a more positive space. In Oakland they built a coffee shop that offered healthy food with a deck and places for people to sit in a parking lot behind a fitness center that used to be a tire store. The area soon became a popular place for people to meet, have coffee, and eat. Many of these infill sites are almost too small for traditional construction methods. “But because we’re building off site, we can bring in an already built building with very little impact to the rest of the community, drop it in, finish up the site work, and voila, you’ve got this little community space.”
The team has also done some work in the supportive housing space, mostly providing the more complicated facilities in these developments, like bathrooms, showers, and laundry and food facilities. “At some deep level, part of our reason for being is to help be a part of positive social change,” said Trela. “So, at our core, those projects are really important to who we are as a company.”
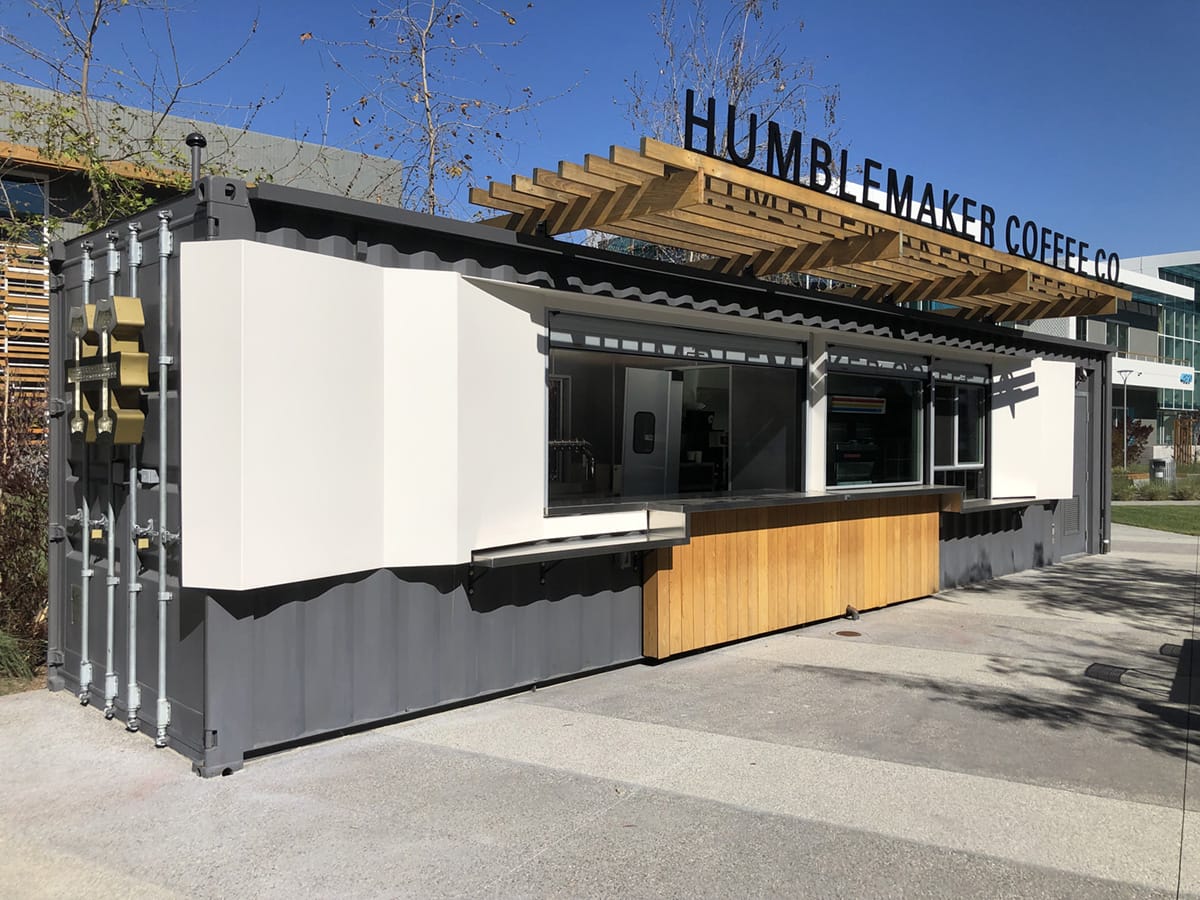
Why Shipping Containers?
While modular companies may dabble in working with shipping containers, not many rely on them solely for their projects. Containers offer quite a few advantages, according to Trela.
“My business partner, Jerry, says that they’re human scale, so they’re approachable and they almost have their own little personalities. There’s something that is very compelling to people about containers and container developments. They tend to take on their own personality and become their own entities.” Secondly, the transportation industry is mostly organized around transporting these containers, so there are no special considerations when moving them from the factory to the site. Trela said, “The entire global transportation industry was organized around this 8'x40' or 8'x20' module to move and distribute goods and services. So, they’re very easy to transport.”
Clients are often attracted to them because from a real estate perspective they are considered an asset. Having the flexibility to move and transport these assets allows owners to respond to different circumstances in a fluid manner that they can’t get with standard construction.
Continual Improvement Drives Excellence
Trela’s team is small, with only ten employees, though they utilize subcontractors to complete most of the trade work in their factory. Many of their contracting partners have been with them since the beginning, learning alongside each other. “Our company has really embraced a constant thirst for evaluating how we can do better in the next project, where we can grow, and where we can learn. And it’s all with the intent of satisfying our customers and meeting their needs.”
Through that experience, they’ve assembled a network of suppliers and other strategic partners that allow them to complete projects under tight timelines. “Our business processes and relationships have really evolved, which gives us the ability to be very nimble and quick.”
“We’ve gained so much more expertise over these years that now we can be a much bigger participant in the larger process. Not just our containers. If we’re brought in early enough, we can be an advisor and a strategist as part of the larger team. We can say, how can we get this project to successful opening and beyond? That’s really rewarding for us because we can give back and help ensure fast, efficient, cost-effective projects throughout the process. I think as a company we’ve developed into a premiere, high-quality, well-respected brand in the industry, and we’re super proud of that.”
What’s Next?
UrbanBloc has several projects on the horizon, including a pizza restaurant in Hayward that will be using a refurbished BART car as the seating area.
“I feel like even though the ten years has gone by fast, we are veterans in the industry in some ways, but we don’t feel that way. Because we’re always learning and always looking at things through new perspectives, we still feel like we’re youngsters, but with a track record.”
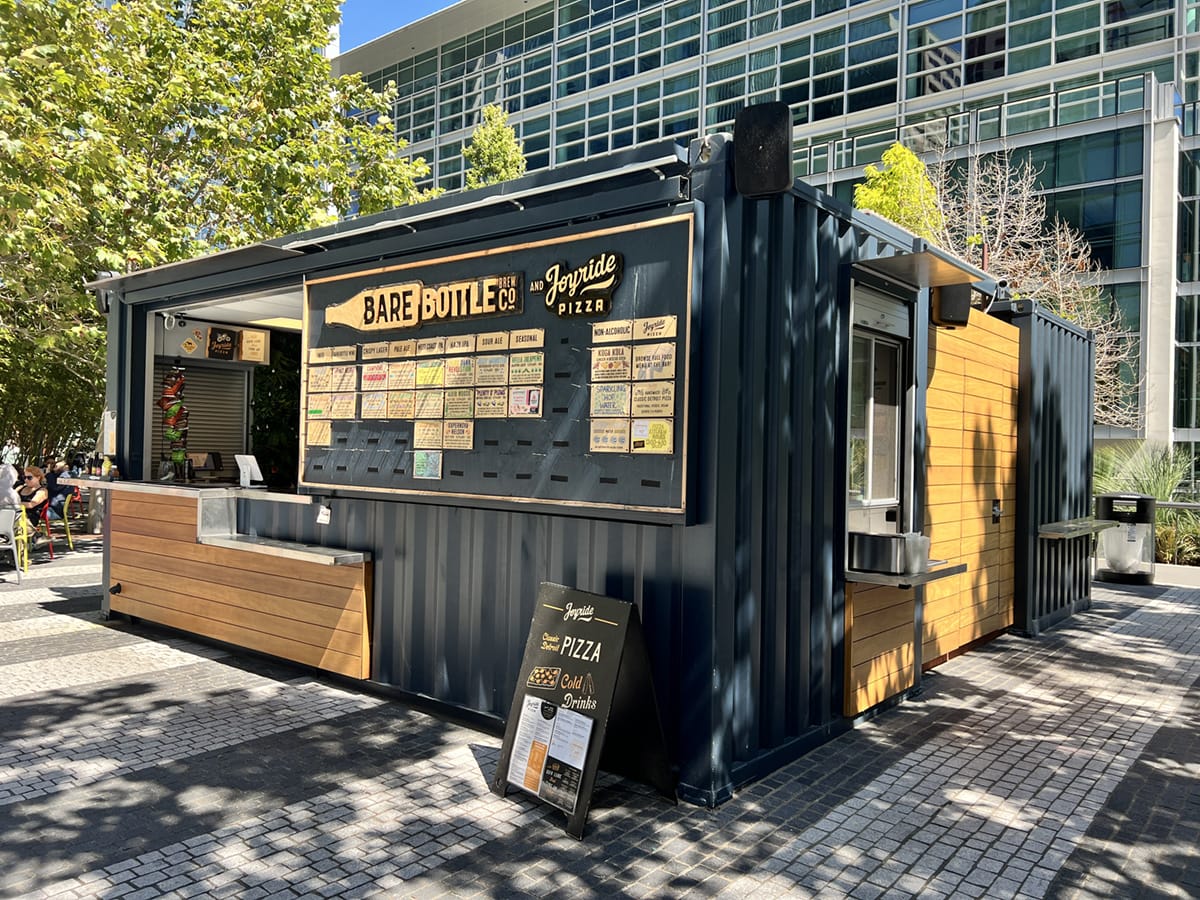
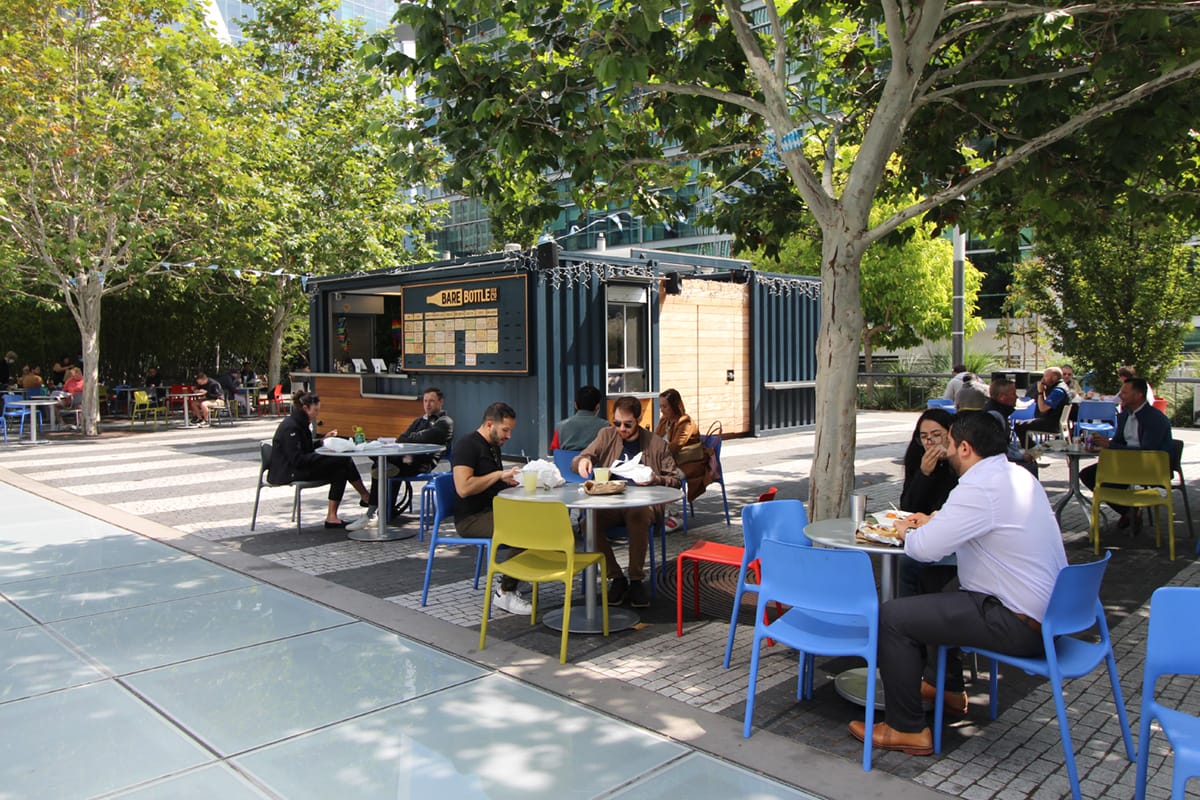
About the Author: Dawn Killough is a freelance construction writer with over 25 years of experience working with construction companies, subcontractors and general contractors. Her published work can be found at dkilloughwriter.com.
More from Modular Advantage
Oregon’s Prevailing Wage Proposal: A Wake-Up Call for Modular Construction
In early February, 2024, the Massachusetts Board of Building Regulations and Standards (BBRS) released its proposed 10th Edition building codes. This draft included several amendments targeting modular construction that would have created an extremely difficult environment for the entire modular industry and could have eliminated the industry entirely in the state.
Behind the Design of Bethany Senior Terraces, NYC’s First Modular Passive House Senior Housing Project
As more developers seek to meet new regulations for energy efficiency, the team at Murray Engineering has set a new record. With the Bethany Senior Terraces project, Murray Engineering has helped to develop NYC’s first modular structure that fully encompasses passive house principles — introducing a new era of energy efficiency in the energy-conscious city that never sleeps.
How LAMOD is Using Modular to Address Inefficiency, Sustainability, and the Future of Construction
As developers, designers, and contractors seek to understand the evolving needs of the modular industry, no one is as well-versed in the benefits of going modular as Mārcis Kreičmanis. As the co-founder and CBDO of LAMOD in Riga, Latvia, Mārcis has made it his ultimate goal to address the inefficiencies of traditional construction.
From Furniture Builder to ‘Activist Architect’: Stuart Emmons’ Unique Journey
Stuart Emmons was fascinated by buildings at a young age. He remembers building sand cities with his brother during trips to the Jersey shore. His father gave him his first drawing table at the age of ten. Today, he is an experienced architect who received his FAIA in June 2025. The road he took is unique, to say the least.
Forge Craft Architecture + Design: Codes, Contracts, and Intellectual Property
Founding Principal and Director of Modular Practice for Forge Craft Architecture + Design, Rommel Sulit, discusses the implications of codes, contracts, and intellectual property on
modular construction.
Eisa Lee, the “Bilingual” Architect
Now as the founder of XL
Architecture and Modular Design in Ontario, Canada, she applies not just her education as a traditional architect but an entire holistic view on modular design. It’s this expansive view that guides her work on being a true partner that bridges the gap between architects and modular factories as they collaborate on the design process.
Tamarack Grove Engineering: Designing for the Modular Sector
The role of a structural engineer is crucial to the success of a modular project, from initial analysis to construction administration. Tamarack Grove offers structural engineering services — project analysis, plan creation, design creation, and construction administration — for commercial, manufacturing, facilities, public services, and modular. Modular is only one market sector the company serves but it is an increasingly popular one.
Engineer Masters the Art of Listening to His Customers
Since founding Modular Structural Consultants, LLC. in 2014, Yurianto has established a steady following of modular and container-based construction clients, primarily manufacturers. His services often include providing engineering calculations, reviewing drawings, and engineering certification
Inside College Road: Engineering the Modules of One of the World’s Tallest Modular Buildings
College Road is a groundbreaking modular residential development in East Croydon, South London by offsite developer and contractor, Tide, its modular company Vision Volumetric (VV), and engineered by MJH Structural Engineers.
Design for Flow: The Overlooked Power of DfMA in Modular Construction
Unlocking higher throughput, lower costs, and fewer redesigns by aligning Lean production flow with design for manufacturing and assembly.