ModCribs Are a Better Way
Modular building offers so many clear advantages over traditional stick-built structures, but it hasn’t come this far without challenges. Traditional cribs for short-term support are a prime example. They’re heavy, expensive, and have a short lifespan. Those things have been a pain for modular builders for decades, but now there’s a better way.
It’s actually surprising that it’s taken the modular industry this long to develop this product, but it’s true. Two veteran modular guys finally came up with something better and they call the idea ModCribs. These are strong, nestable, and lightweight replacements for traditional wooden cribs. As usual, necessity was the mother of invention.
They Were Builders First
Scott Bridger and Matt Mitchell connected and gained experience while building in North Dakota’s oil field region and became familiar with modular construction. Since the modules typically need to be staged near the construction site after they come off the trailer, they have to be supported somehow until they are placed by crane. Modular manufacturers also use them to store the units at their factory until they’re shipped. Wooden cribs have been the way until now, for the most part. They’re usually made from 2x4 lumber and nails. At around 120 pounds each, they’re not fun for the crew to handle and represent a true injury risk. And they’re not cheap when you consider the labor involved in building each one.
Developing the Product
“There’s got to be a better way” was a familiar refrain in the industry about wooden cribs but still, no one jumped in to solve the problem, Bridger and Mitchell noted. “This is just such an inefficient, cumbersome part of the industry and there’s got to be a better way,” Mitchell said of their thinking about four years ago. “So from our experience and process we have had an opportunity to spend a lot of time in a whole lot of different factories around the country. And so we’ve seen so many different versions of cribs,” he continued.
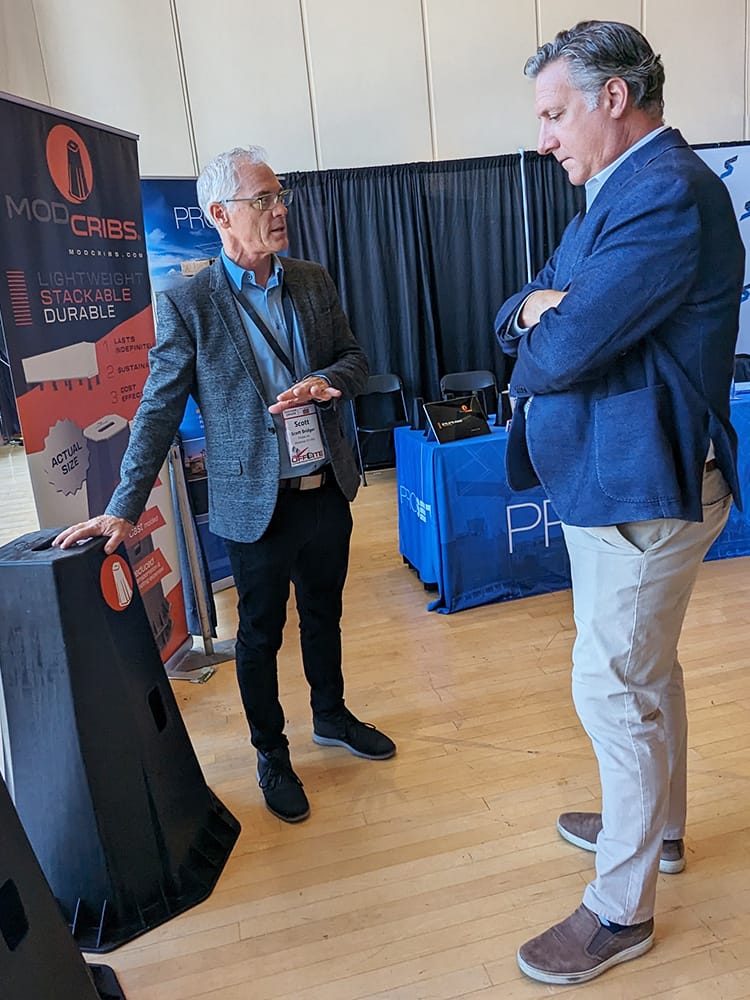
Scott Bridger displays ModCribs at the Offsite Construction Summit in Berkeley, CA.
Mitchell and Bridger took note of what other people were using. “We said, it doesn’t seem like anybody’s really working on a better solution to try to fix this,” Bridger said. At that point about four years ago, they decided to see what they could come up with. “That’s when we really in earnest decided to see if we can design and manufacture something that’s just better,” Mitchell said.
Related Listening:
28 Pounds of Innovation: How ModCribs is Changing the Game for Modular Set Crews w/ ModCribs
Scott Bridger, co-founder of ProSet Modular, introduces his newest venture: ModCribs. Nearly indestructible and only 28 pounds apiece, ModCribs modular cribbing units bring ease and efficiency to modular manufacturers and set crews. In this episode, Scott describes the evolution and benefits of product itself, shares how project stakeholders can bring them to their jobsites, and dives into the best practices of modular set-up and onsite logistics.
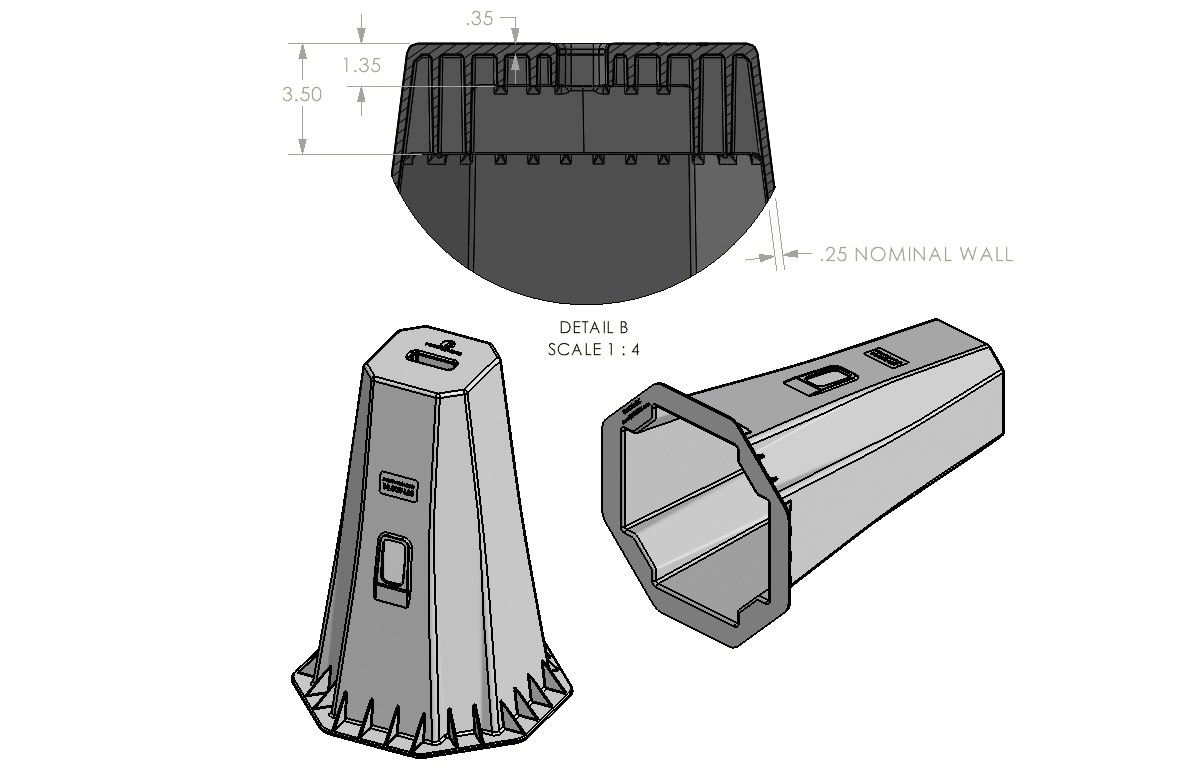
Wood is a versatile, accessible, and easy-to-work material, but its weight and propensity to rot are major drawbacks for outdoor tasks. Steel is cheap but heavy and harder to work with. Aluminum is light in weight but expensive.
Coming up with the design and material specifications took some time, Mitchell and Bridger said. The physical requirements were determined by the trailers that haul modules, as well as the weight-bearing requirement for supporting the modules. Finding a material, however, that would provide the strength needed at an acceptable cost was more challenging.
“The problem was to come up with a lightweight product 36 inches tall that could meet or exceed the load limits that they needed to carry,” Mitchell said. “Our original design was actually aluminum,” he added, “but that proved to be too expensive.”
What ended up working out, though, was injection molding with structural foam. At a weight of 28 pounds each, they are around 90 pounds lighter than a typical wooden crib, provide at least as much strength, and they don’t rot.
“Our cribs were designed to carry 20,000 pounds apiece,” Mitchell added. “We rate them at 10,000 pounds apiece, and we expect them to carry an average load of about 4000 pounds apiece.”
Design criteria included three crucial factors, Bridger noted. “This had to be lightweight, had to be stackable, and it had to be durable. And I guess if you wanted to add a fourth one in there, it’s probably cost effective because you can find other materials that would meet lightweight, stackable, and durable but not affordable,” he said.
The benefits of stackability can’t be overstated. Wood cribs at 18 inches square will fit just four per layer on a standard pallet. ModCribs will stack 48 units on a pallet. That’s a massive boost in efficiency. “So what’s happening today is you have these tractor trailer flatbed trailers that are transporting a couple hundred wood cribs per load. That’s an expensive transportation piece. And we can transport over 1100 ModCribs on that same trailer. So the transportation piece of it is much much more efficient,” Bridger noted.
Stackability also pays dividends for storage of the cribs. Cutting down on the square footage required by a factor of 10+ will be a benefit for almost any company, whether they’re a factory, set company, or general contractor.
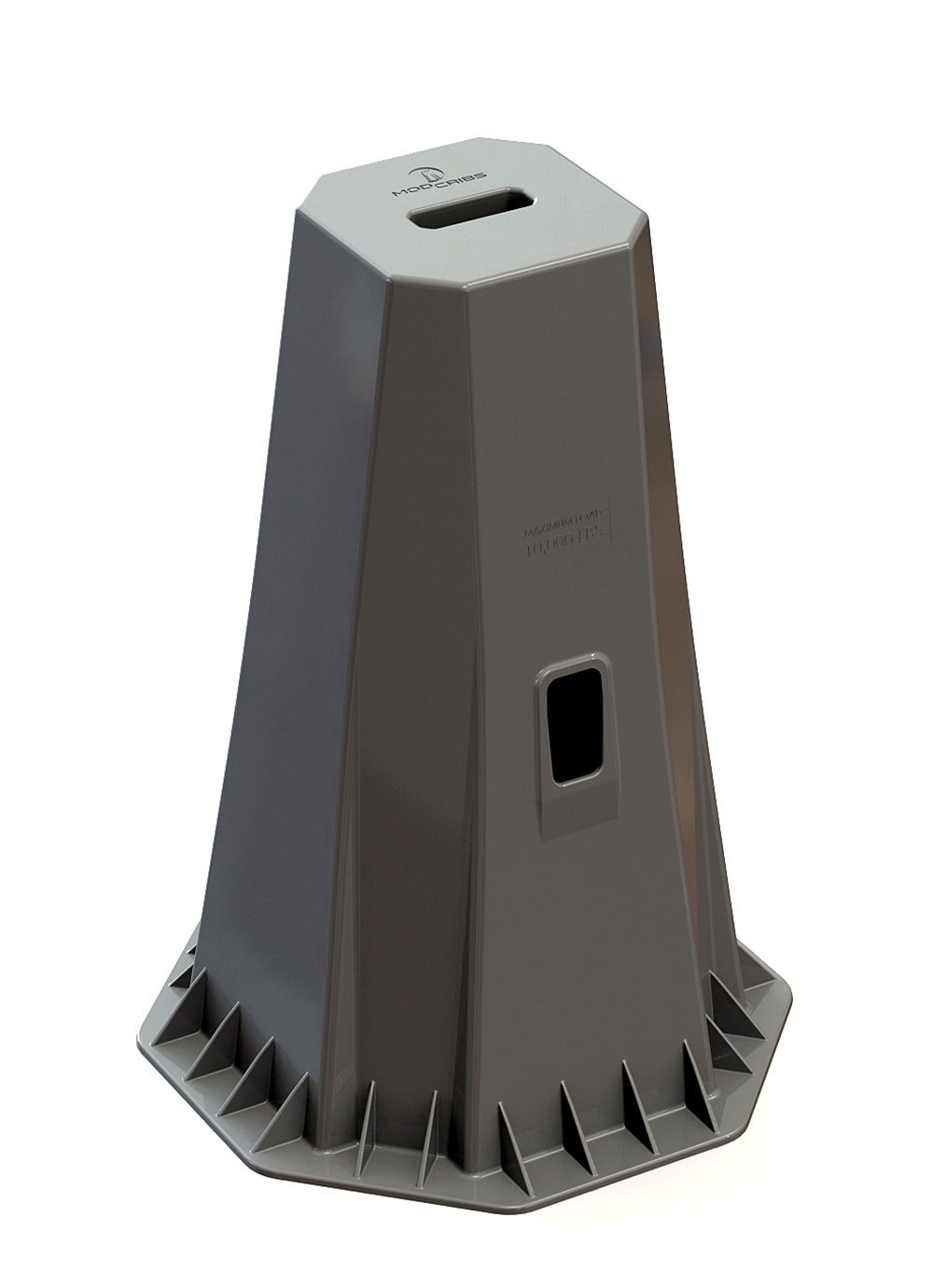
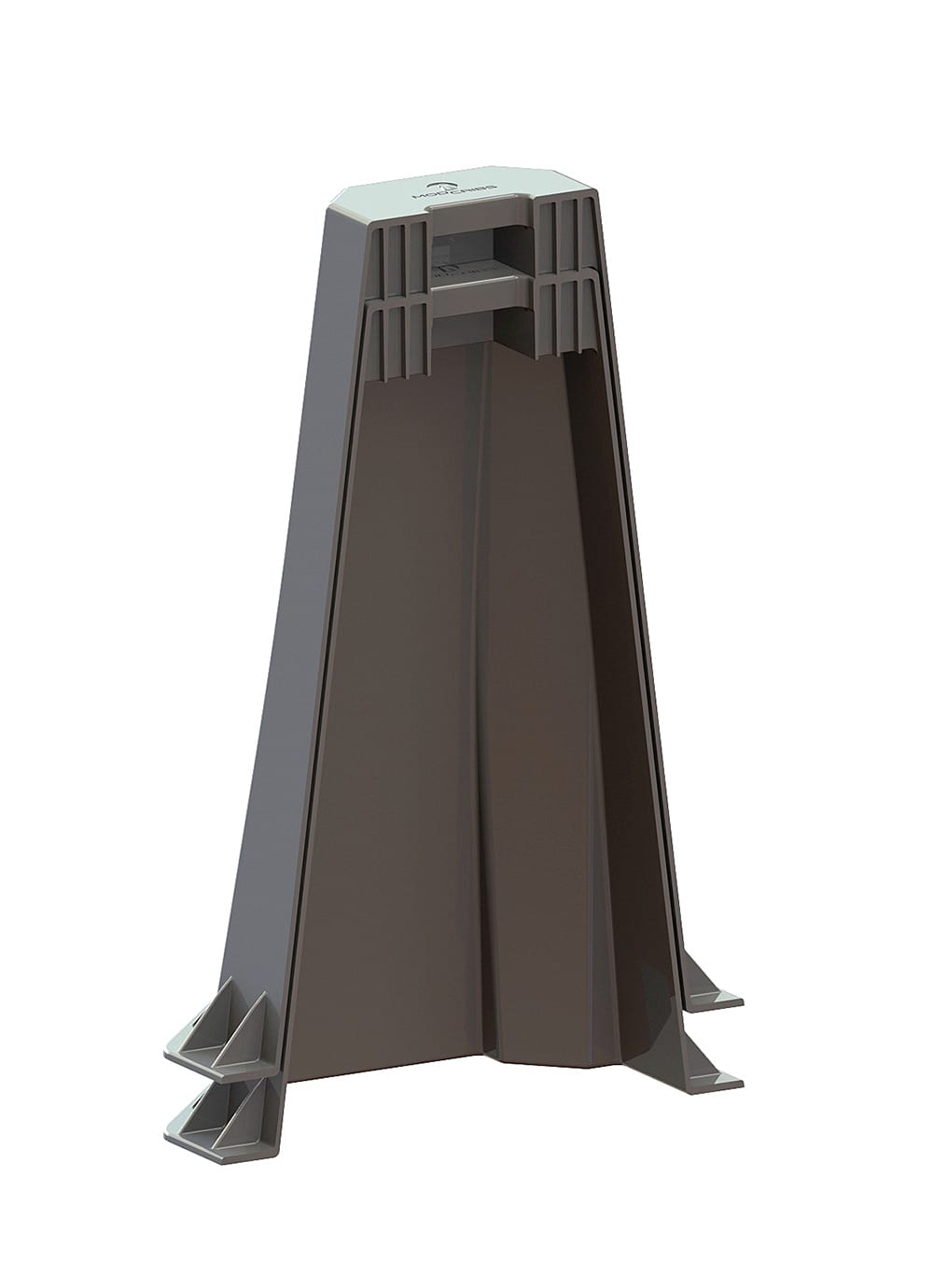
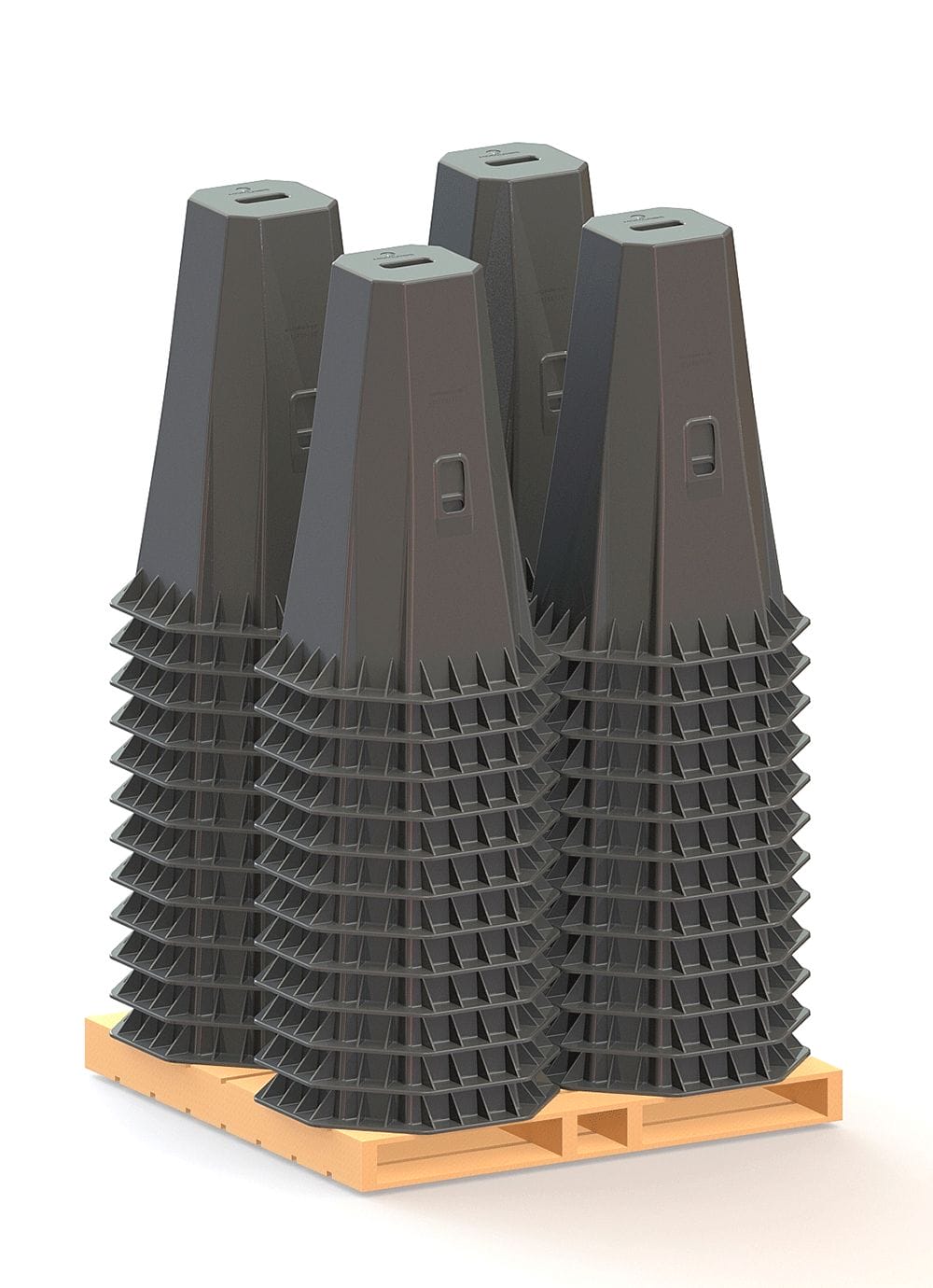
At 28 pounds apiece, ModCribs have been designed to easily stack for transport. Forty-eight ModCribs units will fit on a pallet.
For General Contractors, Rent—Don’t Buy
ModCribs are available to general contractors on a rental basis. For manufacturers, they are available for purchase as well. This approach makes a lot of sense. When you need something infrequently, but it must be totally dialed in for its use, renting the asset is a customer-friendly approach. For manufacturers, though, who may often have dozens of modules on site at any time, each needing multiple cribs, owning the asset makes more sense.
In comparison to wooden cribs, Bridger noted, “We just talked to a general contractor recently at the Denver Offsite Construction Summit. He was spending over $200 to build wooden cribs right now.” ModCribs will rent the cribs, deliver them to the site, and pick them up for quite a lot less than that. For buyers of ModCribs, the warranty is seven years.
What’s the Response?
So far the reaction from the modular industry has supported Bridger’s and Mitchell’s approach. The industry has been in need of this solution for decades, and not just from a product standpoint. “The most enthusiastic response by far is from truck drivers that are hauling because they’re the ones that have to physically handle wood cribs,” Bridger said.
The OSHA standard recommends that no workers lift objects greater than 50 pounds, Bridger said, so at 28 pounds ModCribs are making life easier on workers.
What Does the Future Hold for ModCribs?
Will the “old timers” of modular construction be regaling the young folks with tales of the horrors of using wooden cribs soon?
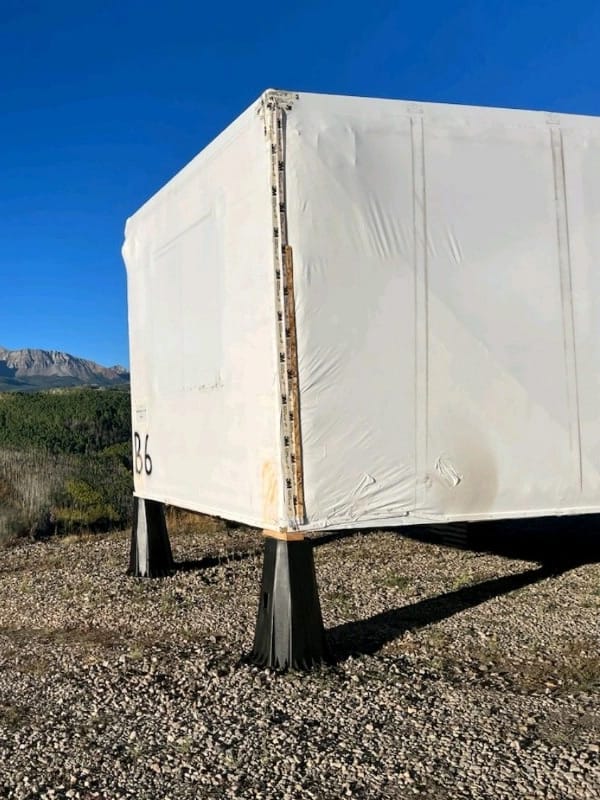
Lightweight, stackable, and exceptionally strong, ModCribs have been designed to replace the "headache in the industry that is the wood crib.”
“Our hope is that within a fairly short period of time, there’s just very few wooden cribs being built out there because it just doesn’t make sense anymore,” Mitchell said. “Additionally, I think there are going to be some other versions of a ModCrib that we might develop over time. Different sizes and for different uses. Different segments of the industry. But initially, I think our main goal was to get rid of this headache in the industry that is the wood crib.”
About the Author: Steve Hansen is a Colorado-based writer with a focus on the built environment—architecture, construction, renewable energy, and transportation. He can be reached on LinkedIn.
More from Modular Advantage
AI, Faster Sets, and Automation: The Future of Modular is at World of Modular
While the modular building industry has long known that it can be an effective solution to increase affordable housing, the word is slowly spreading to more mainstream audiences. Three presentations at this year’s World of Modular in Las Vegas hope to provide insight and direction for those seeking a real solution to the crisis.
An Insider’s Guide to the 2025 World of Modular
The Modular Building Institute is bringing its global World of Modular (WOM) event back to Las Vegas, and with it comes some of the industry’s best opportunities for networking, business development, and education. Over the course of the conference’s four days, there will be numerous opportunities for attendees to connect, learn, and leverage event resources to get the most out of the conference.
Affordable Housing Now: The Industry’s Best Bring New Solutions to World of Modular
While the modular building industry has long known that it can be an effective solution to increase affordable housing, the word is slowly spreading to more mainstream audiences. Three presentations at this year’s World of Modular in Las Vegas hope to provide insight and direction for those seeking a real solution to the crisis.
Opportunities for Innovation in Modular Offsite Construction
Modular Offsite Construction has already shattered the myth that it only produces uninspired, box-like designs. Architectural innovations in module geometry, configurations, materials, and products make it possible to create visually stunning buildings without sacrificing functionality or efficiency.
Safe Modular Construction with Aerofilm Air Caster Transport
In collaboration with Aerofilm Systems, Heijmans developed innovative skids using air caster technology for moving modules easily and safely. These pallets are equipped with an auto-flow system, making operation extremely simple.
Miles, Modules, and Memes: Building a Modular Network One Flight at a Time
At the end of the day, social media is just another tool for building connections, and like any other tool, needs to be used skillfully to work properly. Use social media thoughtfully, and it will open doors to real opportunities and relationships you didn’t even see coming.
Falcon Structures: Thinking Inside the Box
Some of Falcon’s latest projects include creating container solutions for New York’s Central Park and an East Coast professional baseball team. More and more, Falcon is shipping out container bathrooms and locker rooms to improve traditionally difficult work environments, like those in oil and gas or construction.
UrbanBloc—From Passion to Industry Leader
UrbanBloc specializes in three main categories or markets – what they call “Phase 0” projects, amenities, and urban infill. Clients are often attracted to shipping containers because from a real estate perspective they are considered an asset. Having the flexibility to move and transport these assets allows owners to respond to different circumstances in a fluid manner that they can’t get with standard construction.
The Hospitality Game-Changer
“Hospitality is about more than just providing a service – it’s about delivering an experience,” says Anthony Halsch, CEO of ROXBOX. “And that’s where containers thrive. They allow us to create spaces that are unique, efficient, and sustainable.”
Container Conversions Counts on Simplicity to Provide Critical Solutions
Container Conversions has fabricated and developed thousands of containers for varied projects, including rental refrigeration options, offices, kitchens, temporary workplace housing, and mobile health clinics.