Sustainable and Energy-Efficient Solutions from DMDmodular
The real estate market needs a revolution – it is responsible for 38% of greenhouse gas emissions that enter the atmosphere. Therefore, it will play a
significant role in introducing solutions to meet the challenges of the future. Upcoming changes in regulations concerning the ecological aspects of buildings will soon compel real estate investors to seek urgent solutions enabling them to achieve the objectives outlined in the Net Zero strategy. DMDmodular has recently achieved a significant milestone by successfully completing a relevant energy-efficient housing project, fully financed by EU funds, that tackles the industry’s most pressing challenges.
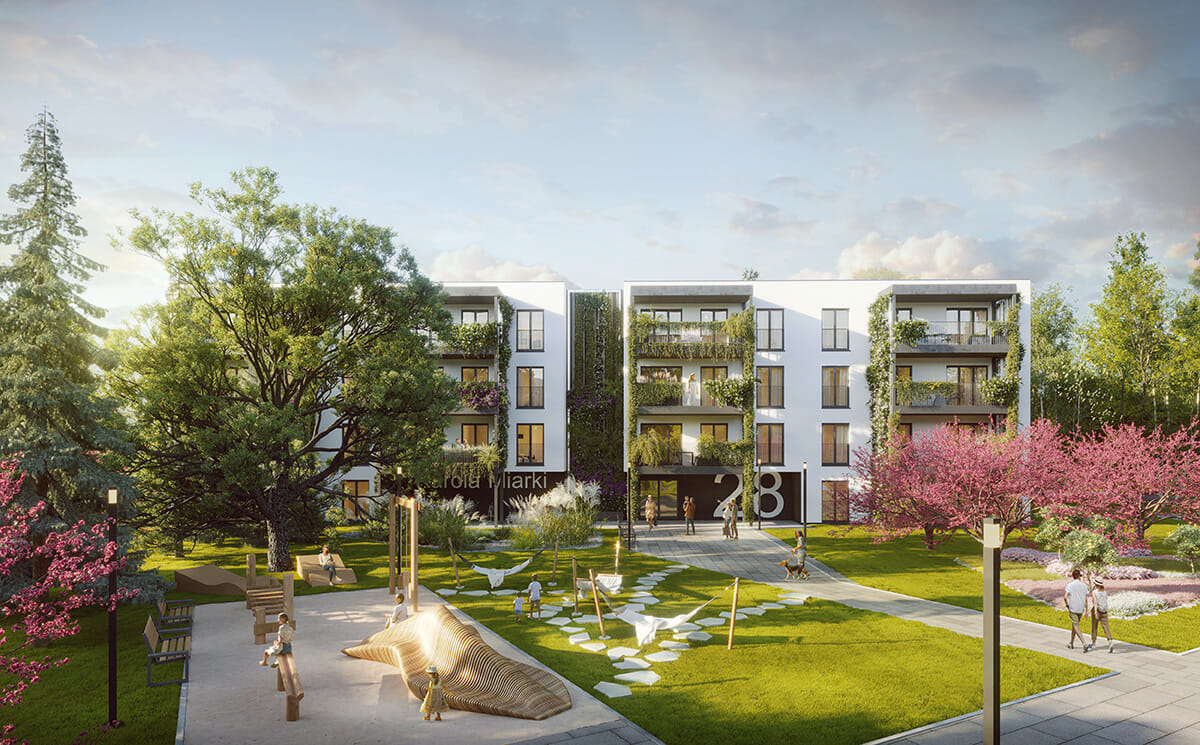
This energy-efficient multi-family building emerged as a response to an initiative led by the Polish National Center for Research and Development, titled “Energy and Process-Efficient Modular Construction” was designed and build using a volumetric modular system, and It was developed by DMDmodular in collaboration with researchers, architects, and technologists.
The project comprises 29 apartments ranging in size from 45 to 70 square meters, and it was materialized through 56 fully finished and furnished modules. These modules, manufactured at DMDmodular’s facility near Kraków, were transported and assembled in Mysłowice, Poland during July 2023.
This building stands as a technology demonstrator, offering an invaluable scalable and global solution for both local governments and private investors developing projects across the countries. Energy efficient modular technology can effectively address the housing shortage and energy crisis, as well as rising construction costs associated with traditional methods.
The project is defined by its superior quality finishing, energy efficiency, and remarkably rapid construction timeline of just 4 months. This high quality, energy efficient and quick delivery method not only can help alleviate housing shortages and the immediate need of building solutions to rebuild Ukraine (only 250 km from the Ukrainian border), but also significantly enhances returns on investment in the build-to-rent sector, encompassing hospitality, PRS ventures, co-living initiatives and student accommodations, compared to conventional construction techniques.
The showcased multi-family building integrates innovative solutions that enable a positive energy balance, resulting in surplus energy generation. It incorporates cutting-edge air handling units with 95% air recovery efficiency, moisture recovery systems, ceiling-based heating and cooling through capillary mats, thermal energy storage, and thermal energy recovery from sewage tanks. The building solely relies on renewable energy sources for its energy needs and integrates measures to minimize water consumption and the overall carbon footprint.
The demonstrator was also developed with numerous sustainable materials from Polish and foreign companies. One of them is the Norwegian waterproof wall systems in the form of easy-to-install panels. Manufactured from PEFC certified, layered plywood and high-pressure laminate, Fibo’s wall panels offer a sustainable - a 40% lower carbon footprint - alternative to tiles. The panels have been installed on surfaces where high strength, durability and quick assembly have been implemented in bathrooms and kitchens.
The garnered experience of DMDmodular has facilitated the establishment of a seamlessly coordinated supply chain comprising cooperating companies. For investors, this translates to project implementation stability and cost predictability, which, especially in light of the fluctuating prices of construction materials, stands as one of the advantages of DMDmodular technology compared to conventional methods.
Poland offers a sustainable and efficient supply chain which is a perfect environment for company Fibo, which supplies DMDmodular, focused on
turn-key modular units. The country has become one of the hottest manufacturing clusters in Europe as the economy continues to perform strongly being among the three fastest growing economies in the EU. Poland is a major producer and supplier to the automotive industry and a leading manufacturing position in the windows industry in the EU. And it holds the fourth position in the world as an exporter, and sixth place as a producer in the furniture industry. Thanks to the stable and credible local supply chain, DMD claims to be the attractive and reliable business partner for the UK construction market.
DMDmodular is an award-winning company focusing on the housing and hospitality industries, delivering unique volumetric modular solutions to international markets. Noteworthy recent developments are PBSA schemes in Scotland, Denmark, and Switzerland and numerous houses for recreational parks in the Benelux region. Furthermore, the company is presently engaged in several hotel projects, encompassing establishments in the UK and Belgium. DMD earned international recognition in 2022 by securing an award in the Green Building Category for its innovative co-living modular solution implemented in Paris.
More from Modular Advantage
AI, Faster Sets, and Automation: The Future of Modular is at World of Modular
While the modular building industry has long known that it can be an effective solution to increase affordable housing, the word is slowly spreading to more mainstream audiences. Three presentations at this year’s World of Modular in Las Vegas hope to provide insight and direction for those seeking a real solution to the crisis.
An Insider’s Guide to the 2025 World of Modular
The Modular Building Institute is bringing its global World of Modular (WOM) event back to Las Vegas, and with it comes some of the industry’s best opportunities for networking, business development, and education. Over the course of the conference’s four days, there will be numerous opportunities for attendees to connect, learn, and leverage event resources to get the most out of the conference.
Affordable Housing Now: The Industry’s Best Bring New Solutions to World of Modular
While the modular building industry has long known that it can be an effective solution to increase affordable housing, the word is slowly spreading to more mainstream audiences. Three presentations at this year’s World of Modular in Las Vegas hope to provide insight and direction for those seeking a real solution to the crisis.
Opportunities for Innovation in Modular Offsite Construction
Modular Offsite Construction has already shattered the myth that it only produces uninspired, box-like designs. Architectural innovations in module geometry, configurations, materials, and products make it possible to create visually stunning buildings without sacrificing functionality or efficiency.
Safe Modular Construction with Aerofilm Air Caster Transport
In collaboration with Aerofilm Systems, Heijmans developed innovative skids using air caster technology for moving modules easily and safely. These pallets are equipped with an auto-flow system, making operation extremely simple.
Miles, Modules, and Memes: Building a Modular Network One Flight at a Time
At the end of the day, social media is just another tool for building connections, and like any other tool, needs to be used skillfully to work properly. Use social media thoughtfully, and it will open doors to real opportunities and relationships you didn’t even see coming.
Falcon Structures: Thinking Inside the Box
Some of Falcon’s latest projects include creating container solutions for New York’s Central Park and an East Coast professional baseball team. More and more, Falcon is shipping out container bathrooms and locker rooms to improve traditionally difficult work environments, like those in oil and gas or construction.
UrbanBloc—From Passion to Industry Leader
UrbanBloc specializes in three main categories or markets – what they call “Phase 0” projects, amenities, and urban infill. Clients are often attracted to shipping containers because from a real estate perspective they are considered an asset. Having the flexibility to move and transport these assets allows owners to respond to different circumstances in a fluid manner that they can’t get with standard construction.
The Hospitality Game-Changer
“Hospitality is about more than just providing a service – it’s about delivering an experience,” says Anthony Halsch, CEO of ROXBOX. “And that’s where containers thrive. They allow us to create spaces that are unique, efficient, and sustainable.”
Container Conversions Counts on Simplicity to Provide Critical Solutions
Container Conversions has fabricated and developed thousands of containers for varied projects, including rental refrigeration options, offices, kitchens, temporary workplace housing, and mobile health clinics.