Modular Design Through the Construction Perspective
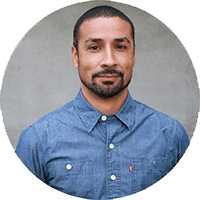
About the Author: Nick Gomez of Lowney Architecture has more than 15 years of experience working on multi-family housing and modular projects for nonprofit and for-profit clients. As the Oakland, Calif.-based firm’s Multi-family Studio Director, Nick has managed award-winning projects from design development through construction administration.
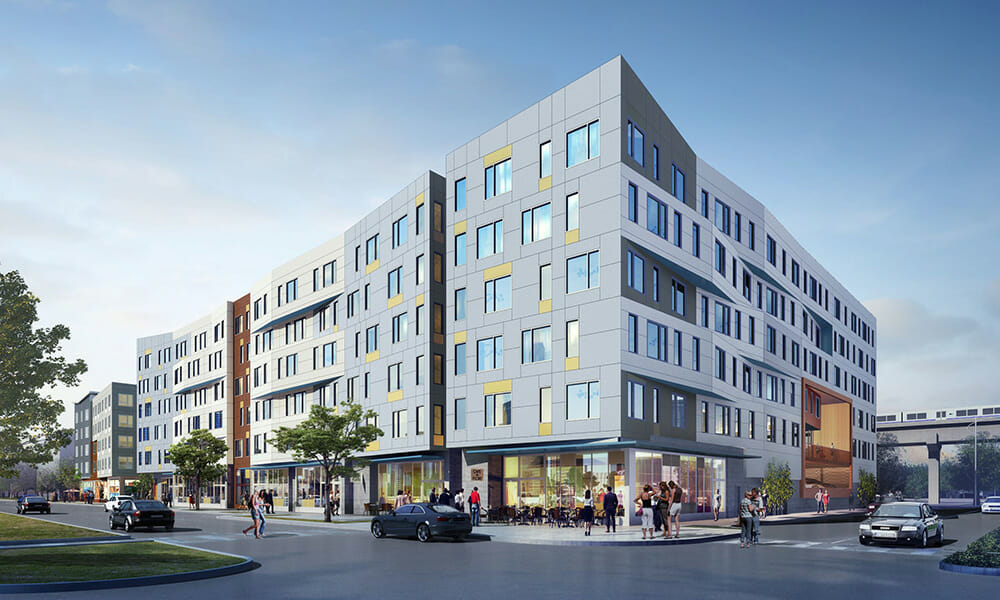
The Mayfair in El Cerito, CA.
Throughout this three-part series (Part 1, Part 2), we have looked at optimizing projects for modular construction. In the previous installments, we have explored modular from both the design and fabrication perspectives. Now, we turn our attention to the construction considerations that will help projects take full advantage of the value associated with this construction method. To bring you a contractor’s perspective, Lowney Architecture has collaborated with Mark Zaleski and Deanne Tipton from Cahill Contractors on the content of this article.
Unlike traditional, site-built projects, modular projects require a significant amount of up-front coordination, not just on design, but with project scheduling and factory bidding. We believe development teams will benefit from a deeper understanding of some of the contractor’s considerations unique to the modular approach.
Factory bidding and selection
Ideally, modular factory bidding should occur during the schematic design phase to optimize the benefits of the partnership, and a supplier must be in play no later than 50% into the design development phase. Among the key variables in factory selection are price, schedule, backlog, balance sheet, bonding ability, and owner requirements. Critically, the factory selected must have the capacity to not only produce the modules, but to do so when the project timeline requires them to be ready for site installation.
Owner requirements can also drive the selection of a modular supplier. Existing relationships, costs, bonding, contract agreements and payment schedules all come into play. The conversation around whether “Made in the USA” or not is of importance should be discussed upfront as there are strong Canadian and overseas factories in the market that can competitively supply regions of the U.S. market.
With modular, transportation expenses are a key consideration. Shipping costs and trucking fees vary depending on geography, the modular factory location, and its proximity to the development site. Additionally, it’s important to note that delays or early deliveries requiring local staging of the completed modules will reflect an increase in costs.
Generally, each modular supplier varies on product details such as cabinet selections and windows. This is important because the factory will be more comfortable procuring and installing what they are familiar with, which will likely result in cost- and time-savings benefits to be realized from the special relationships between factories and their downstream material suppliers. Because of this, it is critical to work with the architecture and engineering teams on the initial design intent and project green building standards.
Given these interconnected elements, it is advantageous to get the modular supplier on board early to collaborate with the architect, owner and general contractor on design optimization, value engineering, details, and project schedule.
Related Reading:
Mayfair: A Modular Case Study
Previously used as a surface parking lot for commuters accessing public transit, the Mayfair development on a city-owned block in El Cerrito, Calif. brings 223 new housing units to a long-neglected stretch near the El Cerrito del Norte Bay Area Rapid Transit (BART) Station.
Named for the grocery chain that once occupied the block, The Mayfair project received its first stacked module unit October 2020 and reached its full building height of six stories after ten days of assembly.
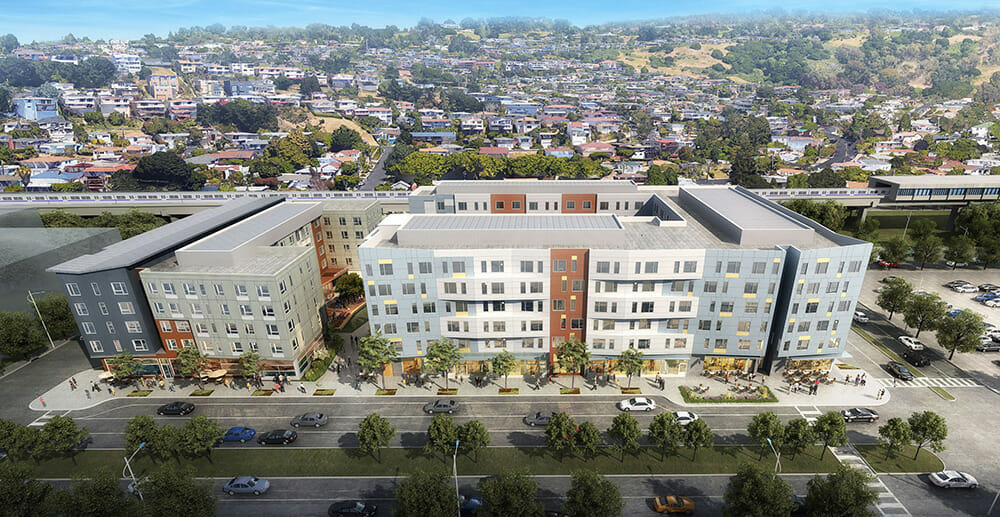
Scope of the factory build
Evaluating how much of the construction can be handled off-site is a central determination when leveraging modular construction. In general, the more that can be built by the modular supplier in its own factory, the greater the construction cost savings. This needs to be negotiated not only for monetary terms, but also the impact it has on the architect and engineering teams’ permit documents that are divided between site and factory scope of work.
It is important to ensure the modular supplier is within their comfort zone. Factories have the ability to provide parapets, corridor shaft plug walls and other factory furnished site installed items for the contractor. Avoid forcing the factory to provide items that may be less expensive for the contractor site sequence and installation.
In deriving the full benefit from a modular build, it is critical to limit onsite work inside factory-finished units. The common exceptions to this rule are window blinds, life safety devices and any stitching at the mate lines that occur at openings and doors between modules in multi-room units.
Site evaluation and logistics
For contractors, the site evaluation and development of a corresponding logistics plan is a critical early study needed to confirm if modular makes sense as a delivery method. One pivotal consideration – unique to modular builds – that derives many other logistical aspects is the maximum module dimensions: 72’ x 16’ wide x 12’-6” tall. These dimensions are mainly governed by highway trucking limits as anything larger requires special arrangements. For example, California requires oversized loads to be escorted by the highway patrol, which makes it cost prohibitive.
Unlike traditional, site-built projects, modular projects require a significant amount of up-front coordination, not just on design, but with project scheduling and factory bidding. We believe development teams will benefit from a deeper understanding of some of the contractor’s considerations unique to the modular approach.
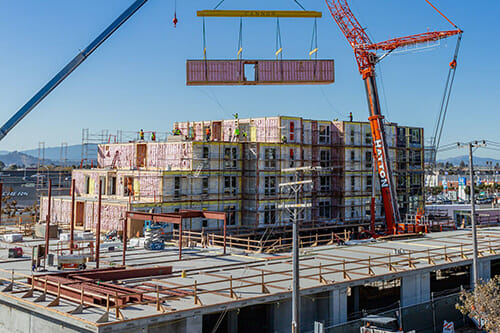
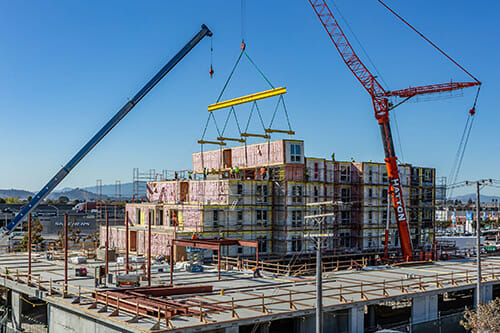
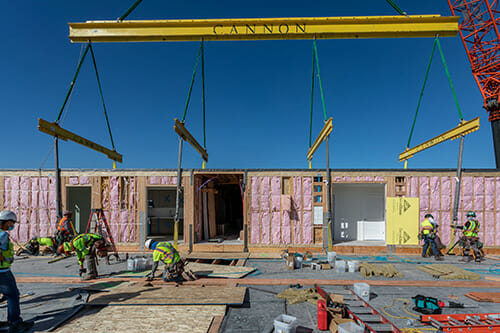
Site delivery and sequencing
When employing modular construction, submittals and RFIs need to be reviewed and approved, and owners are faced with selecting finishes much earlier than in typical onsite construction. The factory will need to complete shop drawings for review and approval by the owner, architect, and engineers, prior to production of the prototype modules. The factory will request a ‘design lock’ prior to procuring materials for the module prototype, a process that usually occurs at least six months prior to full production.
Factory construction process
Unless the owner directly hires the factory, building the modules offsite does not decrease the contractor’s responsibility. In fact, the need for contractor review and oversight is just as critical in the modular context. The modular factory will typically have its own, written QC/QA plan that must be approved by the state. The general contractor should oversee the factory’s QC efforts. It is also recommended that the architect and their consultants assist in QC efforts, but these parties are not responsible for QC—a factor that can vary depending on funds available and the factory’s locale.
The punchlist process can also vary depending on the factory’s location in relation to the owner, architect, contractor, and jobsite. Typically, there is a punchlist for the prototype that the owner, architect, design consultants, general contractor, owner’s rep, and any lender inspectors should be a part of to “set the expectations.” There is also the punchlist for the main production run of the modules, which is typically performed by the modular supplier in conjunction with the general contractor. The owner and architect may make periodic visits to the factory, too.
Of note, the general contractor’s fire sprinkler design-build subcontractor is the only subcontractor to work both inside the modular factory and onsite. The modular factory must accommodate the fire sprinkler subcontractor for installation of the fire sprinkler system within the modules and for system testing in the factory. For this reason, the contractor will usually pick a fire sprinkler subcontractor familiar with the factory and local to the site.
Fire sprinklers, fire alarms, any exterior building maintenance (EBM), and Emergency Responder Radio Communications Systems (ERRCS) need to be designed early to coordinate with modular production – and the fire safety measures must be submitted with the state for permitting. Fire Sprinkler and Fire Alarm consultants usually brought on board in construction will need to be advanced to coordinate with factory design and permitting.
Sequence producing and delivery between the factory and site is also critical. It is ideal to synchronize timing of the factory’s module production and the start of setting the modules to minimize the storage time in between. In creating the project schedule, two schedules are needed: one for the online construction with its permits and another for the modular process with its permits. From there, these are combined and adjusted to get them in coordination with factory process and design team permitting.
A few fine points for the modular schedule: Allow time for submittals, materials procurement, and prototype production. Typically, obtaining the state (“modular”) permits takes less time than getting the building permits. Scheduling must consider weather conditions around setting the modules – including allowing enough time to get a roof on the structure before a rain season.
Related Listening:
Architectural Design for Modular w/ Lowney Architecture
In this episode of Inside Modular, Nick Gomez, studio director at Lowney Architecture, calls in to talk about designing for modular buildings and the advantages for architects.
Factory and site inspections
The state is responsible for inspections of the modules produced in the factory, and the factory handles hiring and compensating the state-approved third-party inspection firm, such as NTA. This is included in the suppliers’ bid scope. The inspection firm reviews the modules and the factory’s QC program. The inspector does not necessarily inspect each individual module at every step in the production process, but their intent is to inspect the structural and fire life safety systems. Once a module is inspected and approved, it’s physically stamped, and the inspection firm reports back to the state.
Local jurisdictions typically do not inspect pr review inside the modular units, except for life safety systems and any site-installed work, such as in the common corridors, structural connections, and fire continuity details at module connections.
Additional inspections completed at the factory are preformed by the owner, the owner’s lender(s), the architect, their consultants, and the general contractor. The number of inspections depends on the factory’s location and owner’s preference for oversight.
At least one prototype module should be built ahead of mass module production and be used as the “mockup” unit. Ultimately, this module will be permanently installed in the building, so it must be inspected and approved by the state’s inspection firm. The prototype module “sets the bar” and should be closely inspected by all parties to the project. Ideally, the prototypes should cover both standard and any fully accessible unit types in the project and any unique conditions the owner and or design team may want to review prior to production.
Setting the modules
The fun really starts when the modules start stacking – a job often handled by specialty contractors that focus exclusively on setting modules. Modules are set in a pre-planned sequence to minimize crane movements. Modular factories typically produce three to five modules per day, while onsite setting can accommodate 10-14 modules per day. For maximum efficiency, as discussed earlier, module production and storage need to be specifically coordinated with the erection schedule.
Cranes do the heavy lifting in a modular build, and the most used for the purpose are truck, “rubber tire” hydraulic cranes. For larger sites with space and long reaches, a crawler crane can be used, although there are a limited number of crawler cranes available in the country. Tower cranes are not generally used since the module weights are too heavy.
Finishing
Modular construction requires onsite finishing, including completion of structural connections and special inspections. The structural connections for exterior walls typically involve straps fastened to the exterior of the modules. Interior, structural connections are generally in the corridors and include straps, bolts and tie-down systems.
Corridors, stairs, and elevator shafts are finished onsite, and even when incorporated as part of the modular system, they are not completely finished. The interior structural and MEP connections are made in the corridor. Elevator and trash chute shafts are delivered open or supported by a temporary structure for shipping. The contractor will schedule and sequence the necessary site work and close-up for complete installation and inspections.
The MEP connections for vertical tie-ins are also completed onsite. Mechanical, electrical, plumbing and fire sprinkler connections are handled in the common corridor to avoid going into the finished units. The only exception will be fire alarm devices over factory installed j-boxes.
Rounding out the onsite construction elements are the exterior finishes and roofing. The factory will install a sacrificial EPDM membrane on the top of every module for protection from the elements during transport, and this is either removed during the setting process and/or abandoned in place. The factory includes the exterior sheathing, such as Densglass, and windows with window membrane flashing. Parapets, sunshades, and any exterior extrusions are not typically faculty built. Finally, any roof top equipment, including solar and exterior building maintenance is installed onsite, but will need to be coordinated with factory production for required blocking and or factory installed concealed structure.
Once the onsite construction is buttoned-up, utilities, including water, power, and low voltage, are connected and commissioned. Generally, warranties in the modular context are the same as site built, although the start of warranty period will need to be negotiated with the modular supplier. Suppliers push for the warranty period to start when the modules are accepted; owners want it to start at project completion/when they accept delivery of the project.
Summary
In this three-part series of articles, we have looked at optimizing projects for design, factory production and contractor installation. We hope this provides a roadmap for your future off-site construction projects and that more people will utilize this delivery method – especially for regions with tight housing markets and a need for speed in addressing the shortages.
This article was first published in the Modular Advantage - May/June 2021 Edition.
More from Modular Advantage
Oregon’s Prevailing Wage Proposal: A Wake-Up Call for Modular Construction
In early February, 2024, the Massachusetts Board of Building Regulations and Standards (BBRS) released its proposed 10th Edition building codes. This draft included several amendments targeting modular construction that would have created an extremely difficult environment for the entire modular industry and could have eliminated the industry entirely in the state.
Behind the Design of Bethany Senior Terraces, NYC’s First Modular Passive House Senior Housing Project
As more developers seek to meet new regulations for energy efficiency, the team at Murray Engineering has set a new record. With the Bethany Senior Terraces project, Murray Engineering has helped to develop NYC’s first modular structure that fully encompasses passive house principles — introducing a new era of energy efficiency in the energy-conscious city that never sleeps.
How LAMOD is Using Modular to Address Inefficiency, Sustainability, and the Future of Construction
As developers, designers, and contractors seek to understand the evolving needs of the modular industry, no one is as well-versed in the benefits of going modular as Mārcis Kreičmanis. As the co-founder and CBDO of LAMOD in Riga, Latvia, Mārcis has made it his ultimate goal to address the inefficiencies of traditional construction.
From Furniture Builder to ‘Activist Architect’: Stuart Emmons’ Unique Journey
Stuart Emmons was fascinated by buildings at a young age. He remembers building sand cities with his brother during trips to the Jersey shore. His father gave him his first drawing table at the age of ten. Today, he is an experienced architect who received his FAIA in June 2025. The road he took is unique, to say the least.
Forge Craft Architecture + Design: Codes, Contracts, and Intellectual Property
Founding Principal and Director of Modular Practice for Forge Craft Architecture + Design, Rommel Sulit, discusses the implications of codes, contracts, and intellectual property on
modular construction.
Eisa Lee, the “Bilingual” Architect
Now as the founder of XL
Architecture and Modular Design in Ontario, Canada, she applies not just her education as a traditional architect but an entire holistic view on modular design. It’s this expansive view that guides her work on being a true partner that bridges the gap between architects and modular factories as they collaborate on the design process.
Tamarack Grove Engineering: Designing for the Modular Sector
The role of a structural engineer is crucial to the success of a modular project, from initial analysis to construction administration. Tamarack Grove offers structural engineering services — project analysis, plan creation, design creation, and construction administration — for commercial, manufacturing, facilities, public services, and modular. Modular is only one market sector the company serves but it is an increasingly popular one.
Engineer Masters the Art of Listening to His Customers
Since founding Modular Structural Consultants, LLC. in 2014, Yurianto has established a steady following of modular and container-based construction clients, primarily manufacturers. His services often include providing engineering calculations, reviewing drawings, and engineering certification
Inside College Road: Engineering the Modules of One of the World’s Tallest Modular Buildings
College Road is a groundbreaking modular residential development in East Croydon, South London by offsite developer and contractor, Tide, its modular company Vision Volumetric (VV), and engineered by MJH Structural Engineers.
Design for Flow: The Overlooked Power of DfMA in Modular Construction
Unlocking higher throughput, lower costs, and fewer redesigns by aligning Lean production flow with design for manufacturing and assembly.