Mayfair: A Modular Case Study
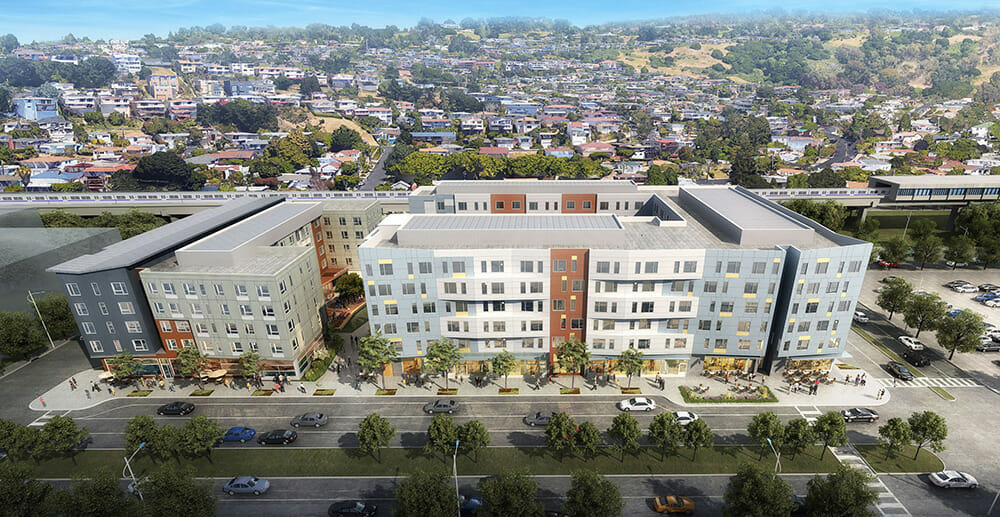
Previously used as a surface parking lot for commuters accessing public transit, the Mayfair development on a city-owned block in El Cerrito, Calif. brings 223 new housing units to a long-neglected stretch near the El Cerrito del Norte Bay Area Rapid Transit (BART) Station.
The affordable and market-rate units will be in their own U-shaped buildings that surround a pair of open courtyards. The central open space between buildings will be open to the public during daylight hours to encourage activity in the transit-oriented development. 67 of the units will be classified as affordable housing, ranging in affordability from 30% – 60% of area median income.
The program mix between the two buildings consist of 10,500 sf of ground floor retail, parking, bicycle parking, property management, community rooms, dog wash and tenant service offices as amenities available for tenants. Program open space will include play areas, vegetable gardens, BBQ area and an outdoor kitchen.
Named for the grocery chain that once occupied the block, The Mayfair project received its first stacked module unit October 2020 and reached its full building height of six stories after ten days of assembly.
The modules for the 156-market rate units of the project started production in June 2019. The modules were fabricated by Factory_OS, only 19 miles away from the site in Vallejo, Calif.
Design Intent
This project sits on a dynamic site in terms of passers-by. It is located on a major thoroughfare (San Pablo Ave.), next door to the El Cerrito del Norte BART stop and regional transit hub. The building façade was envisioned to push the boundaries of modular design while creating a dynamic expression that could hold up to the power of the site. Responding to the movement of the BART trains, the design has horizontal undulating angles that stagger between floors, not common in modular construction.
Normally, a site bounded by heavy traffic and a major public transit line would seek to turn itself inward to protect against these challenges to living; however, the design instead opens toward the BART parking lot with a two-story portal that offers glimpses into the inner courtyard and puts the building’s common space on display for the neighborhood to see.
The plan was arranged with building circulation in a single loaded corridor on the exterior, where the façade faces the BART track. This serves as a sound buffer to the interior units and creates a mostly solid area of the façade that will have a large-scale public artwork facing BART.
Rounding out the aesthetics, the design team is working with a local artist on an installation incorporating areas of mirrored building skin that will blur and change daily for commuters on BART. The idea is that as the time of day and colors of sky change, the rider approach and experience of passing by the building will be unique.
Related Reading:
Modular Design Through the Construction Perspective
Unlike traditional, site-built projects, modular projects require a significant amount of up-front coordination, not just on design, but with project scheduling and factory bidding. This article explores how development teams will benefit from a deeper understanding of some of the contractor’s considerations unique to the modular approach.
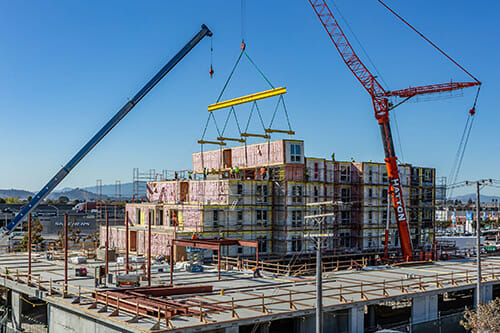
Modular Highlights
Initially, the Mayfair project was considered unbuildable as a modular project, given the complexity of exterior façade design. The architect and engineering team collaborated to figure out the best way to build the exterior envelope, which included the following challenges:
- Articulation – Façade articulation was very important to this project. To break up the façade plane, the design was broken horizontally – an aesthetic element that contextually related to the nearby BART tracks and station. In achieving this, the placement of shear walls needed to be strategically coordinated with the structural engineer. With no repeating, stacking façade elements, the modular manufacturer had to be onboard to fabricate the building. The two-story, site-built portal design required coordination with the structural engineers and the factory to get the final installation to work.
- Portal Design – The site-built portal is made up of both steel and wood framing construction. The design element is intended to activate the southern portion of building and support the modular units that sit above and adjacent to the opening. The coordination of steel placement was achieved with the help of a third-party clash detection agency, which was critical to overlay factory as-built conditions with site construction.
- Single Loaded Corridor – The eastern portion of the building consists of a single loaded corridor. Though saw box units are generally not efficient in modular design, here, they allow the eastern corridor to face the street while the units face the courtyard – a move necessary to achieve the desired density of units. The single loaded corridor also allows for an acoustic buffer and provides space for innovative art panel installation at the eastern exterior wall.
- Combination of Factory + Site Built for Common Rooms – Requested by planning to activate the façade, the common rooms were site built from structural steel, allowing for a greater span for programming including a lounge adjacent to the two-story portal and across from a fitness space.
Project Specifications
- Type 3A Construction
- Estimated completion: June 2021
- Team:
- Lowney Architects
- DCI Engineers
- FARD Engineers
- Cannon Cononstructors
- Factory_OS
- Holliday Development
More from Modular Advantage
Samantha Taylor: Leading the (Modular) Design of Tomorrow
“With modern technology and the way we’ve all embraced things like BIM, file sharing, and video conferencing since COVID, it’s easy to collaborate with companies in Austria, or Singapore, or anywhere else in the world.”
Greg DeLeon: Military Engineering to Modular Design
Greg DeLeon, a structural engineer at ISE Structural Engineers in Temecula, California, can tell you not only how large a beam needs to be to support a house, but also how much explosives you’ll need to take it down, thanks to his unique combination of professional and military experience.
To Remake North Minneapolis, Devean George Swaps Basketball for Buildings
He’s lived in Los Angeles, Dallas, and San Francisco (to name a few). He’s delivered championships with the Los Angeles Lakers and made career-defining moves with the Dallas Mavericks and the Golden State Warriors. No matter the wins, the championships, or even the seemingly impossible 3-pointers, Devean George has always returned to where it all started for him: Minneapolis.
Chelsi Tryon: Making the World a Better Place
For Chelsi Tryon, Director of Environmental, Social, and Governance (ESG) for WillScot Mobile Mini, nothing is more enjoyable than increasing the
company’s sustainability efforts while simultaneously doing her bit to save the environment.
Joshua Hart: Pushing Boundaries
Joshua Hart, P.E., vice president at Modular
Solutions, can sum up his job responsibilities in one sentence: “I do whatever needs to be done.” Hart thrives on the variety and the opportunity to be involved in every aspect of the company. And it shows! You might say Hart has come full circle.
Jamie Metzger: From Construction to Apparel and Back Again
Growing up in a blue-collar city like Edmonton, Alberta, Canada, it’s no surprise that Jamie Metzger spent some time working labor jobs on construction sites. It’s one of the most common summer jobs in the city. But that’s probably the last predictable thing about this particular story.
Victor Masso: Expanding Modular in Puerto Rico
Victor Masso joined 2 Go Storage, a company started by his grandfather and father, in 2018 to develop a modular building division in the wake of the devastation caused by Hurricane Maria in 2017. Prior to joining the company, he had worked in the industry for about four years focusing on pharmaceutical, commercial, and government projects.
Eliyah Ryals: Finding the Perfect Fit
It’s not common for people to find their perfect career fit straight out of college. It’s even less common to find it in the town you grew up in. But that’s exactly what happened when Eliyah Ryals was told about vacancies at Panel Built and made the decision to apply.
Through It All, It’s Still About the Workers
By February 2024, the number of available, unfilled construction job openings had reached an all-time high. At some point, interest rates will fall, creating another surge in demand for such workers. In short, solving the nation’s skilled worker shortage issue has never been more important.
Navigating Insurance Challenges in the Modular Construction Industry
Utilizing practical written minimum insurance and indemnity requirements, along with monitoring certificates of insurance by someone who has COI training will not yield a perfect risk transfer strategy, but the exposure will be managed much better than it likely is currently.