Modular Design: The Software, The Process, The Future
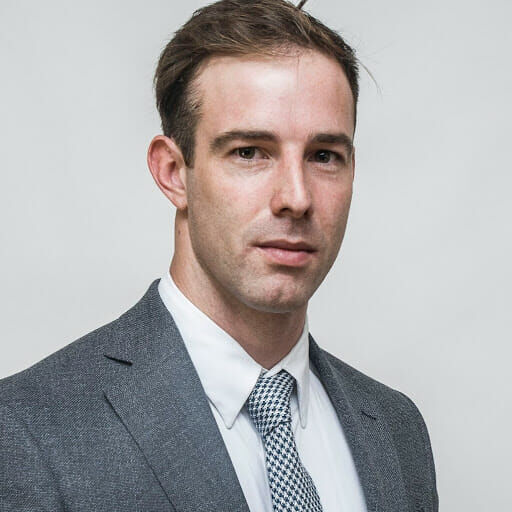
Anthony Gude is the Director of Operations at R & S Tavares Associates, a company based in San Diego, California. Founded in 2002 by Ralph and Silvana Tavares, the firm provides services that include design, structural engineering, consulting, and project management for construction clients across the United States. Most of the company’s work involves designing and engineering pre-fabricated buildings.
Early design
Anthony Gude emphasizes the familiar advice to bring all the key players on a project together early in the design process. “Everyone says this — because it’s true!” Gude says. “Nobody has all the necessary information at the start, especially on innovative or large-scale projects. A conference call with 20 or 30 people giving input at the pre-design stage is not uncommon.
”There will be numerous design iterations while the team explores project feasibility and it’s important to remain flexible during this process. “Re-designs — such as designing a whole building in steel and then re-designing in wood, or vice versa — often happen because someone was pulling in a particular direction too soon,” Gude says. “So have that group discussion first, and get all the information and constraints on the table from the beginning.”
If the design team is brought in too late, or if the wrong fabricator is chosen for a project, “then you’re setting yourself up for failure.”
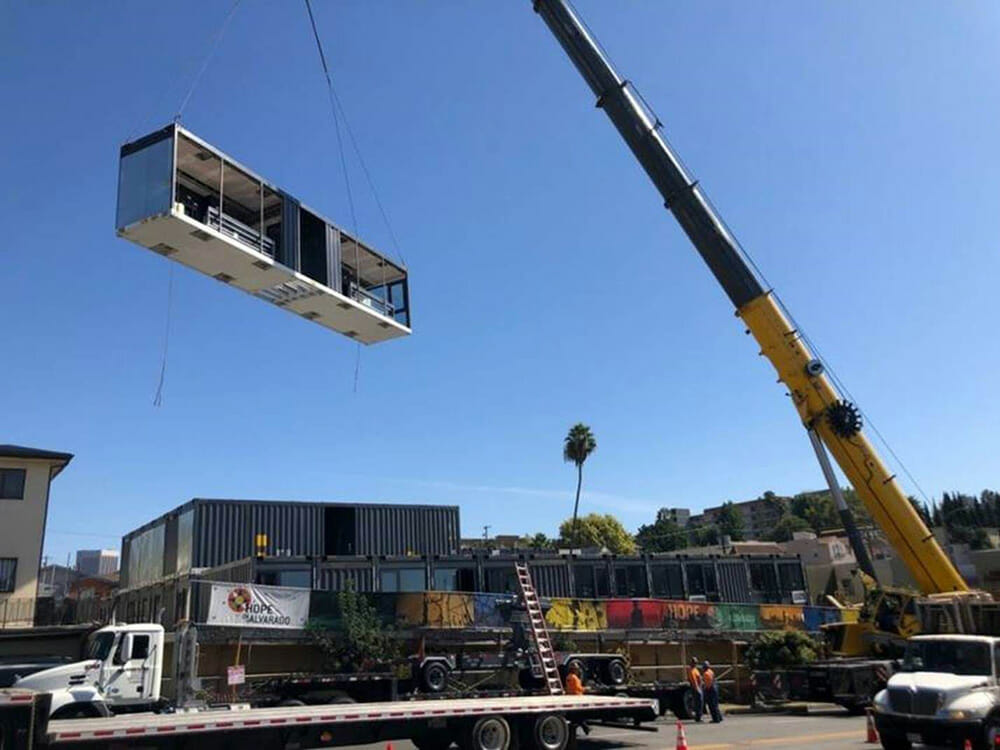
Processes vs execution
Speaking of failures, Gude says that when modular construction has been criticized for poor outcomes, it’s often been without considering the causes of those outcomes. “We need to distinguish between the processes of modular design and construction on the one hand, and the execution of those processes on the other. Problems executing the processes can result in poor outcomes — that doesn’t mean there’s something wrong with the processes themselves,” Gude says. “It’s like someone failing to reach their destination on a bicycle because they fell off. That poor outcome doesn’t mean there’s something inherently wrong with the process of bicycle-riding. It means that, on that occasion, there was a problem with executing that process.”
It’s particularly important to make sure everyone on the team for a project is well-suited to it. For example, an owner might require a large cantilevered deck on the top floor of a building. A specific fabricator may be better suited to design and custom-manufacture that building because they’re experienced with the details of the required connections. However, if the owner has contracted with a fabricator who doesn’t have that experience, “then the project may not be able to overcome the design constraint due to the mis-match in capabilities. The shortcoming in this case is not in the modular design and manufacturing processes themselves — but rather it’s due to the specific decisions of those leading the project.”
Similarly, start-up ventures may lack the right kind of knowledge and experience. They might have a type of end product in mind, but have a mismatch with the type of fabrication or material they want to use. “For example, shipping containers are not suitable for every type of end product,” Gude says. “There comes a point where you have to do so much re-work or structural re-design of containers that the project team should have used one of the other solutions available to the volumetric modular industry.”
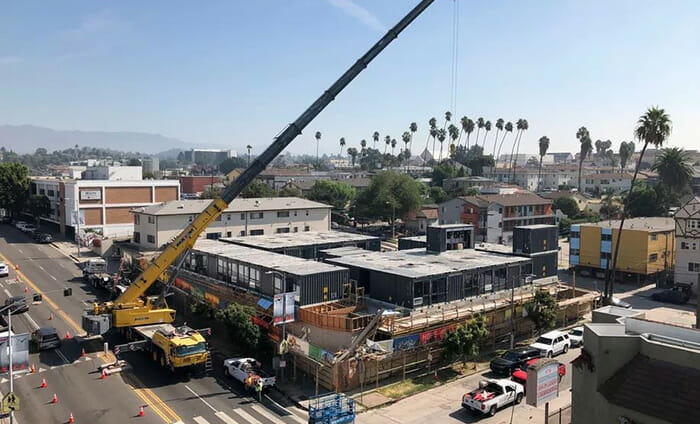
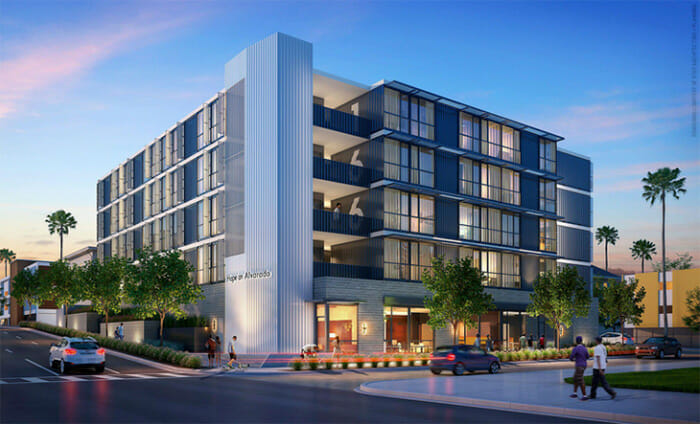
Photo credit: KTGY Architects
Related Listening:
How Owner/Developers Can Best Get Started with Modular Construction w/ R & S Tavares Associates
In this episode, Pedro Tavares and Anthony Gude of R & S Tavares Associates share best practices for owner/developers looking to incorporate modular construction into their upcoming projects.
Re-using design elements
A major advantage of modular construction is the ability to re-use design elements on multiple projects, thus reducing costs. R & S Tavares recently put this into practice on the HOPE projects, which are supportive housing developments in the greater Los Angeles area.
These developments have been sponsored and supported by local governments that are committed to a longer pipeline — not just one or two projects. This means the entire design and construction team can also commit to multiple projects and deliver on modular’s promise of more economical housing. “Because the team was invested in multiple projects, we developed core designs that could be reconfigured in a variety of ways to best suit each individual project,” says Gude.
Design software
Gude mentions some software products, such as Archistar, Hypar, and Kreo, which “help with everything from site feasibility, all the way through to parametric design and modeling.” These kinds of software create renderings based on “the general parameters of the building — how the modules connect, the type of building, the number of stories, wind loads, snow loads, etc.”
R & S Tavares is working on a portal where clients can pick from a library of pre-designed elements and, combined with the input of high-level design constraints, the software will render a rough draft model to use as a basis for early discussions. The rough draft functions like an initial feasibility study for the client.
“With this technology, we can effectively download our early project feasibility decision tree, and have an algorithm make those assumptions for us,” says Gude. “And then we can do the detailed design based on the resulting draft model — instead of investing time and effort into a detailed design that it turns out later the client isn’t on board with.”
Sharable digitized designs
Gude says sharable digitized designs will help move modular construction towards truly industrialized design and manufacturing, making the industry more efficient and reducing costs. He says modular fabrication is not yet homogenous enough to share designs widely and he predicts that, first, “engineering firms that specialize in fabrication and manufacturing will learn to own and distribute their design details as digital products.”
One problem with sharing digitized designs is that the original designer can lose control of the design. “Illegal use of design details is rampant the architecture, engineering, and construction industries,” Gude says.
The solution lies with technology-enabled ledgers, Gude explains. This allows code to serve like a unique barcode that attachs to a digital product, which acts like a certificate of authenticity. These certificates can guarantee that the original designer will reap some benefit every time someone acquires a copy of the design — like royalties going to an author every time a copy of their e-book is sold.
“All the technology for this already exists,” Gude says. “As it becomes more widely adopted, it’ll be a game-changer for permitting and design workflows. It will allow us all to maximize the benefit of modularization and industrial design in construction.”
This article was first published in the Modular Advantage - May/June 2021 Edition.
About the Author: Zena Ryder is a freelance writer, specializing in writing about construction and for construction companies. You can find her at Zena, Freelance Writer or on LinkedIn.
More from Modular Advantage
AI, Faster Sets, and Automation: The Future of Modular is at World of Modular
While the modular building industry has long known that it can be an effective solution to increase affordable housing, the word is slowly spreading to more mainstream audiences. Three presentations at this year’s World of Modular in Las Vegas hope to provide insight and direction for those seeking a real solution to the crisis.
An Insider’s Guide to the 2025 World of Modular
The Modular Building Institute is bringing its global World of Modular (WOM) event back to Las Vegas, and with it comes some of the industry’s best opportunities for networking, business development, and education. Over the course of the conference’s four days, there will be numerous opportunities for attendees to connect, learn, and leverage event resources to get the most out of the conference.
Affordable Housing Now: The Industry’s Best Bring New Solutions to World of Modular
While the modular building industry has long known that it can be an effective solution to increase affordable housing, the word is slowly spreading to more mainstream audiences. Three presentations at this year’s World of Modular in Las Vegas hope to provide insight and direction for those seeking a real solution to the crisis.
Opportunities for Innovation in Modular Offsite Construction
Modular Offsite Construction has already shattered the myth that it only produces uninspired, box-like designs. Architectural innovations in module geometry, configurations, materials, and products make it possible to create visually stunning buildings without sacrificing functionality or efficiency.
Safe Modular Construction with Aerofilm Air Caster Transport
In collaboration with Aerofilm Systems, Heijmans developed innovative skids using air caster technology for moving modules easily and safely. These pallets are equipped with an auto-flow system, making operation extremely simple.
Miles, Modules, and Memes: Building a Modular Network One Flight at a Time
At the end of the day, social media is just another tool for building connections, and like any other tool, needs to be used skillfully to work properly. Use social media thoughtfully, and it will open doors to real opportunities and relationships you didn’t even see coming.
Falcon Structures: Thinking Inside the Box
Some of Falcon’s latest projects include creating container solutions for New York’s Central Park and an East Coast professional baseball team. More and more, Falcon is shipping out container bathrooms and locker rooms to improve traditionally difficult work environments, like those in oil and gas or construction.
UrbanBloc—From Passion to Industry Leader
UrbanBloc specializes in three main categories or markets – what they call “Phase 0” projects, amenities, and urban infill. Clients are often attracted to shipping containers because from a real estate perspective they are considered an asset. Having the flexibility to move and transport these assets allows owners to respond to different circumstances in a fluid manner that they can’t get with standard construction.
The Hospitality Game-Changer
“Hospitality is about more than just providing a service – it’s about delivering an experience,” says Anthony Halsch, CEO of ROXBOX. “And that’s where containers thrive. They allow us to create spaces that are unique, efficient, and sustainable.”
Container Conversions Counts on Simplicity to Provide Critical Solutions
Container Conversions has fabricated and developed thousands of containers for varied projects, including rental refrigeration options, offices, kitchens, temporary workplace housing, and mobile health clinics.