NYC Healthcare Facility Opens Nine Months Ahead of Site Built Schedule
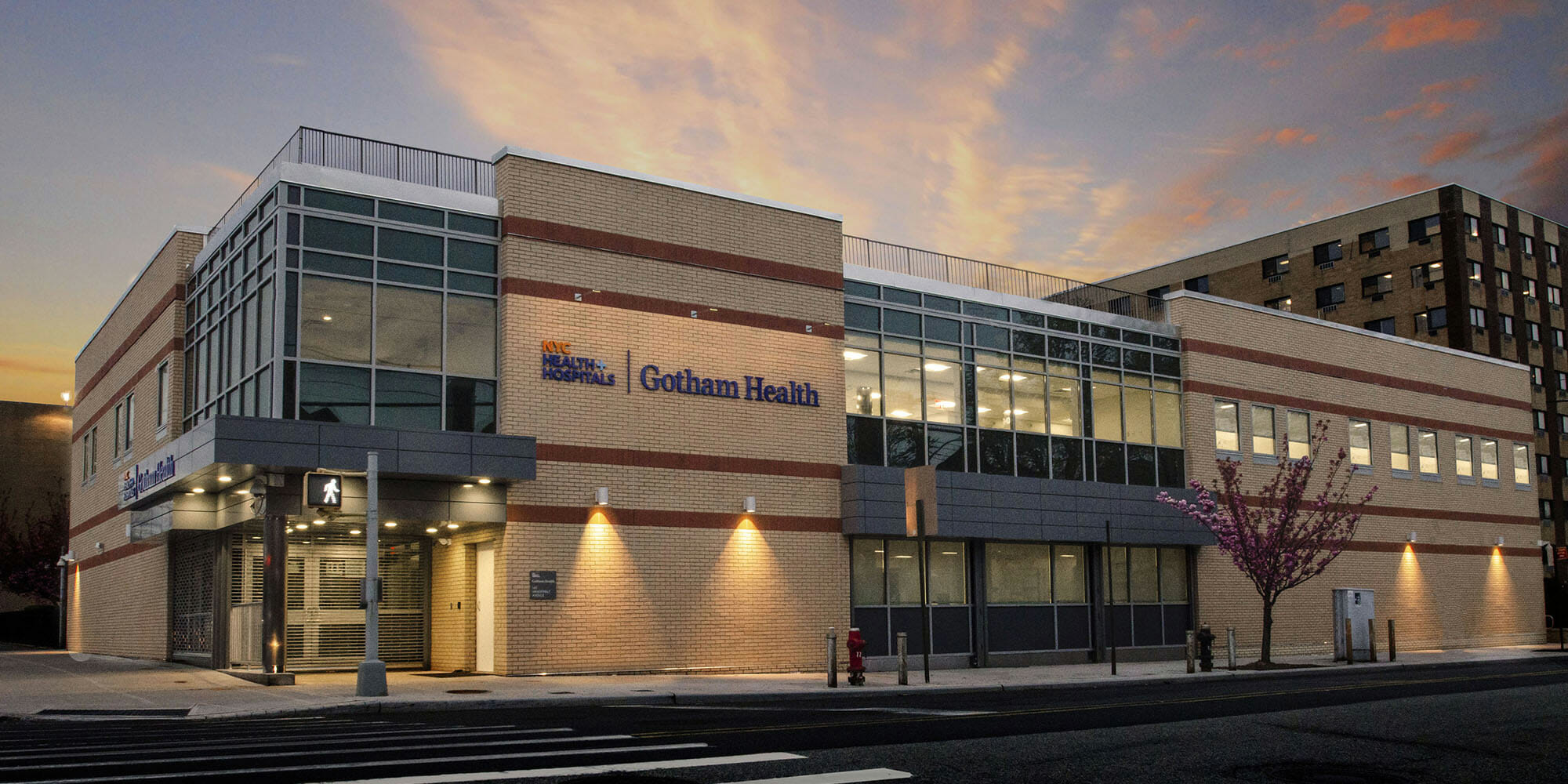
At MBI’s recent World of Modular Conference, more than 125 building projects were entered in the Awards of Distinction Contest. Participants at the event selected the Gotham Health, Vanderbilt Family Health Clinic as the “Best of Show” for all permanent construction projects. With Axis Construction serving as the general contractor and NRB, Inc as the modular fabricator, the nearly 20,000 sq. ft. facility was open in just 322 days – not an easy feat for a project in New York City. The owner estimated that using modular construction saved nine months on the overall schedule.
The Vanderbilt Family Health Center is the first new healthcare facility constructed on Staten Island in over 10 years and is strategically located in a neighborhood that has the greatest and most convenient access to mass transit for patients and staff. The building incorporates Clinical Programs including Pediatrics, Women’s Health, Ophthalmology, Podiatry, Radiology, Diabetes Care as well as Behavioral Health, all meeting the stringent NYC building codes and Department of Health regulations.
The building blended the right mix of architectural, structural, mechanical/electrical features while maintaining strict adherence to budget requirements, critical to the success of the project, as it was funded by New York City. The building features a two-story curtain wall entry system allowing natural light to fill the entryway, factory applied thin-brick exterior with full parapet, ceramic tiled toilet rooms and clean, smooth interior finishes of the offices and clinic spaces for ease of maintenance.
The non-combustible design is a structural steel post and beam assembly with light-gauge infill and pre-poured concrete floors in a composite steel deck to help achieve sound deadening and fire ratings. The customized facility was built completely together at the plant as a two-story structure to ensure precision fit and finish of all features and systems, resulting in a shorter site installation time and reduced on-site activity and disruption to the community.
Once completed, the building was deconstructed and loaded to transporters. This process allowed the building to arrive with all the exterior brick installed as well as a high level of completion on the interior, reducing site completion time significantly. The building was designed with minimal interior columns to allow for maximum flexibility in use. Each module was designed with engineered lifting lugs for fast and simple offloading on to the foundations and a more efficient stacking process meeting exacting tolerances.
NYC Health & Hospitals wanted to minimize disputation to the local residents as the site chosen was in a residential neighborhood. By utilizing “off-site” construction not only were they able to open the facility, treat patients and generate revenue more than nine months ahead of a conventional construction schedule, but also significantly reduced neighborhood disruption. Building this facility in a controlled environment and away from the site helped reduce time and costs in project management and general conditions, allowing NYC Health & Hospitals to meet the budget set for this capital project.
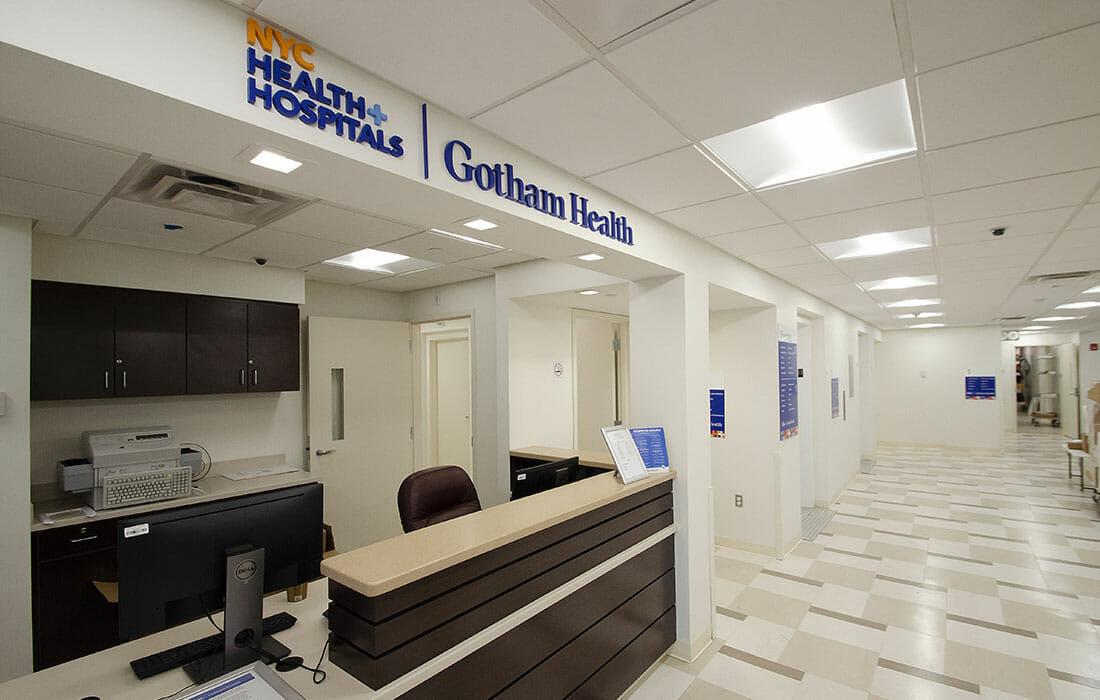
Logistically the project site presented numerous challenges during the delivery and installation phase of the project. Cooperation and careful planning between all stakeholders, as well as the use of a 600-ton hydraulic crane, allowed the building to be installed in just six days with minimal impact to the community.
This article originally appeared in the Modular Advantage Magazine - Second Quarter 2019 released in May 2019.
More from Modular Advantage
AI, Faster Sets, and Automation: The Future of Modular is at World of Modular
While the modular building industry has long known that it can be an effective solution to increase affordable housing, the word is slowly spreading to more mainstream audiences. Three presentations at this year’s World of Modular in Las Vegas hope to provide insight and direction for those seeking a real solution to the crisis.
An Insider’s Guide to the 2025 World of Modular
The Modular Building Institute is bringing its global World of Modular (WOM) event back to Las Vegas, and with it comes some of the industry’s best opportunities for networking, business development, and education. Over the course of the conference’s four days, there will be numerous opportunities for attendees to connect, learn, and leverage event resources to get the most out of the conference.
Affordable Housing Now: The Industry’s Best Bring New Solutions to World of Modular
While the modular building industry has long known that it can be an effective solution to increase affordable housing, the word is slowly spreading to more mainstream audiences. Three presentations at this year’s World of Modular in Las Vegas hope to provide insight and direction for those seeking a real solution to the crisis.
Opportunities for Innovation in Modular Offsite Construction
Modular Offsite Construction has already shattered the myth that it only produces uninspired, box-like designs. Architectural innovations in module geometry, configurations, materials, and products make it possible to create visually stunning buildings without sacrificing functionality or efficiency.
Safe Modular Construction with Aerofilm Air Caster Transport
In collaboration with Aerofilm Systems, Heijmans developed innovative skids using air caster technology for moving modules easily and safely. These pallets are equipped with an auto-flow system, making operation extremely simple.
Miles, Modules, and Memes: Building a Modular Network One Flight at a Time
At the end of the day, social media is just another tool for building connections, and like any other tool, needs to be used skillfully to work properly. Use social media thoughtfully, and it will open doors to real opportunities and relationships you didn’t even see coming.
Falcon Structures: Thinking Inside the Box
Some of Falcon’s latest projects include creating container solutions for New York’s Central Park and an East Coast professional baseball team. More and more, Falcon is shipping out container bathrooms and locker rooms to improve traditionally difficult work environments, like those in oil and gas or construction.
UrbanBloc—From Passion to Industry Leader
UrbanBloc specializes in three main categories or markets – what they call “Phase 0” projects, amenities, and urban infill. Clients are often attracted to shipping containers because from a real estate perspective they are considered an asset. Having the flexibility to move and transport these assets allows owners to respond to different circumstances in a fluid manner that they can’t get with standard construction.
The Hospitality Game-Changer
“Hospitality is about more than just providing a service – it’s about delivering an experience,” says Anthony Halsch, CEO of ROXBOX. “And that’s where containers thrive. They allow us to create spaces that are unique, efficient, and sustainable.”
Container Conversions Counts on Simplicity to Provide Critical Solutions
Container Conversions has fabricated and developed thousands of containers for varied projects, including rental refrigeration options, offices, kitchens, temporary workplace housing, and mobile health clinics.