Women in Modular Construction
The modular construction industry is not afraid to challenge conventions. Women in our corner of the construction industry challenge conventions every day simply because of their gender. Here, thirteen women share their thoughts on the effect of their gender on their career, what they love about the industry, current challenges in the field, and the future of modular construction. It would be easy to have an entire story focused on each woman’s comments, but this article shares brief highlights of each conversation.
How is the Image of Modular Construction Changing?
Ewelina Woźniak-Szpakiewicz is the CEO and Managing Director of DMD Modular, based in Cracow, Poland. She’s also an inaugural member of MBI’s European Council.
“Modular construction combines many different values and attributes,” she says. “The combination of challenges, innovation, experimentation, and international relationships yields unique solutions.”
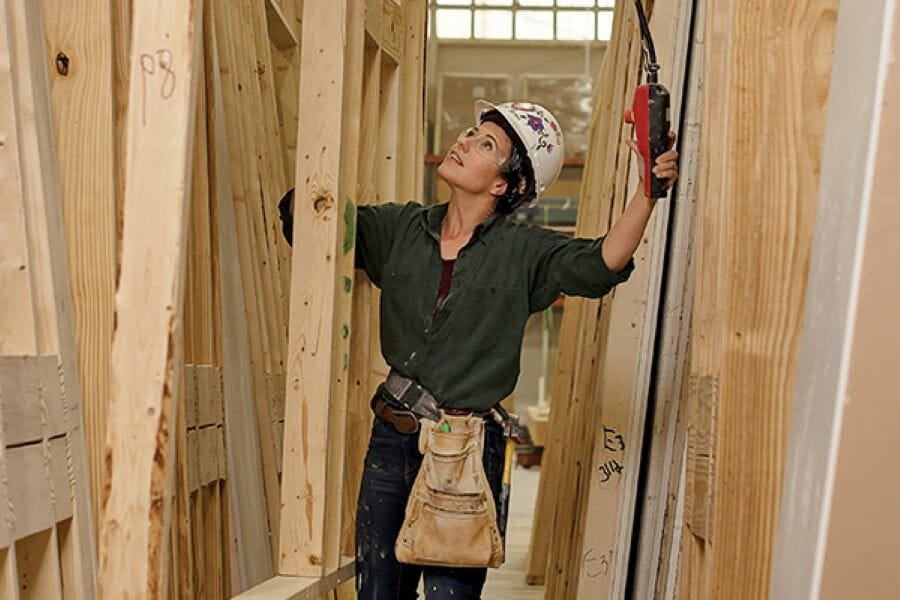
April Harmon, framer at Volumetric Building Companies
The result is the improved image of modular construction. “More architects are becoming interested, and the projects are getting more exciting. This has accelerated the delivery of high quality, complex, innovative solutions and is sweeping away the old perceptions of ugly, cheap, temporary solutions.” Woźniak-Szpakiewicz says. “The hospitality market is a serious driver of this change in perception. When industry titans like Marriott or Hilton launch modular programs, it has a huge impact on the image of modular construction."
How Does Modular Design Differ From Conventional Design?
Based in Chicago, USA, Angela Spadoni is the Director of Residential Architecture at Skender.
“In modular design, the architects and designers interact from the beginning with the construction and manufacturing team — even before schematic design. In conventional construction, architects often work in a bubble with consultants for quite some time before bringing the contractors on board.”
Although the process is different, the results are aesthetically comparable. “There’s nothing in my past work in conventional construction that I couldn’t do modularly. In fact, my interest in modular stemmed from my frustration that many architectural components for multi-family residential construction are repetitive. I hope as time progresses, we’ll standardize more of the repetitive elements such as bathrooms and kitchens, so we don’t have to spend so much time re-drawing those. Then we can focus more on elements like the exterior and be more creative there and push the boundaries, design-wise."
How Can Diversity Help in Modular Construction?
“Right now, modular is the sexy part of construction. It’s exciting and fun,” says Kathy Wilmot, Co-owner of Wilmot Modular Structures, based in Maryland, USA. “I’m glad to see more women getting involved — more women contractors, architects, engineers.”
But being a woman in construction can be challenging.
“A man is automatically perceived as knowing what he’s doing. A woman has to prove that she knows what she’s talking about. So, my biggest advice to women entering this industry is to become an expert at what you’re doing, and know how to explain it succinctly and simply — so you come across as the expert you are.”
Men in the industry can help, Wilmot adds.
“Women can bring a different perspective to boards. Diversity of all kinds results in better decisions. Once men in leadership roles appreciate that, they’ll want to have more women and minorities involved.”
Why Is It a Good Time for Women to Get Involved?
“I’m used to being in uncomfortable situations and feeling out of my element. I’m an immigrant, a minority, a business owner, an architect,” says Sara Logan, the Vice President of Design at Volumetric Building Companies in Boston, USA.
“I walk into a room and people are often surprised — they have no idea how I fit in. I’ve felt somewhat of an outsider since I came to the United States, so being a woman in construction doesn’t seem any different. There still aren’t a lot of women in the industry and I would encourage them to get into it.”
Logan thinks that now is an especially good time for women to get involved.
“The modular industry is in its relative infancy, so gender roles are less-ingrained. You have more freedom to forge your own path and that’s one of the reasons this industry is so exciting to me. Everyone is blazing their own trail.”
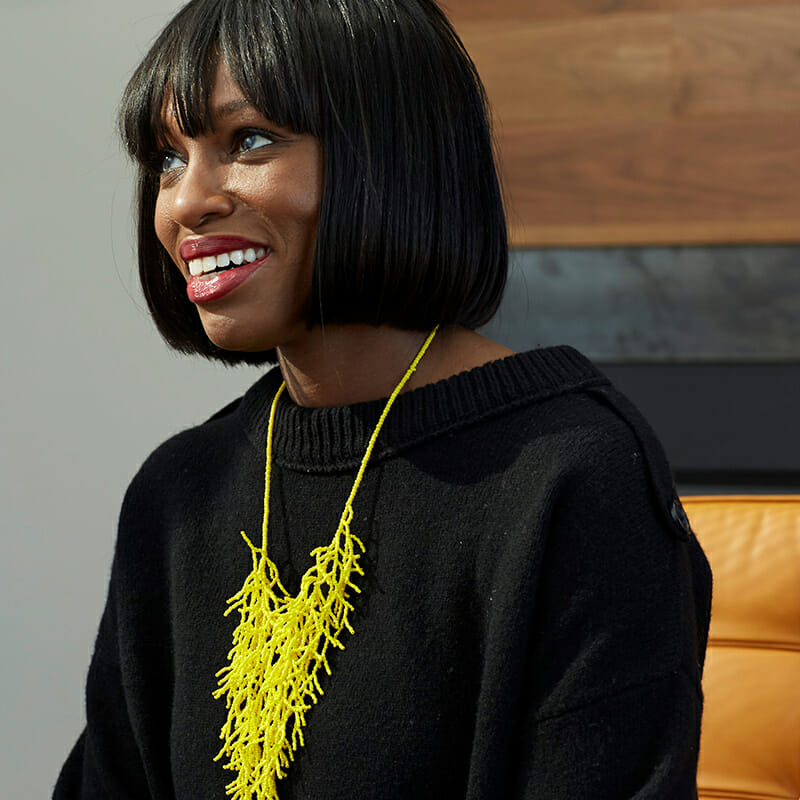
”The modular industry is in its relative infancy, so gender roles are less-ingrained. You have more freedom to forge your own path and that’s one of the reasons this industry is so exciting to me. Everyone is blazing their own trail.”
Sara Logan, Vice President of Design at Volumetric Building Companies
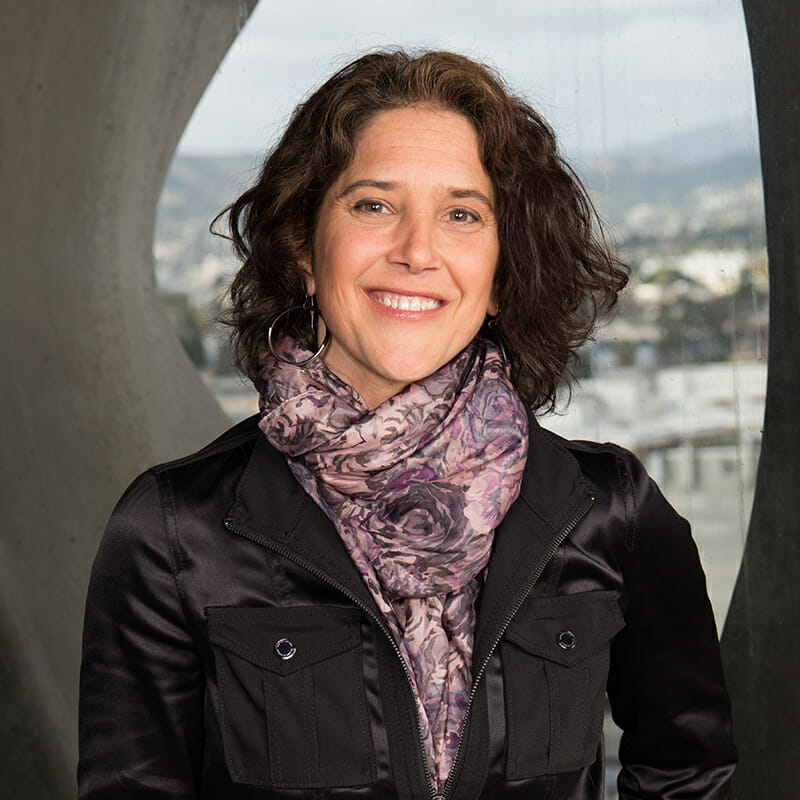
"I believe that the industry is in a place that rewards collaboration and knowledge-sharing. That collaboration excites me. It’s a thrilling time to be involved with modular construction.”
Dafna Kaplan, Founder and CEO of Cassette
How Can Education Help?
Mitzi Garcia is the Federal Contracts Manager for Modular Solutions in Arizona, USA.
"When I speak to girls and young women, they often don't know what construction involves, or what modular construction is. I tell them about the many opportunities in construction that arent' just hammering nails."
As well as educating others, Garcia had benefited from education about modular construction herself.
"I came from an administrative background, and when I decided to stay in the modular industry, MBI helped me learn. They have classes, training opportunities, and will even take one-on-one time with you. Through their mentor programs, you can meet people to discuss what they've tried and learned."
"Education is key. Going into schools, talking with vocational students, using MBI resources-and also using our own websites and social media. People are looking online for information. We can provide it and help educate people about modular construction."
What’s Another Good Way to Learn?
“Find a mentor,” says Melissa Potter, a Journeyman Plumber at an ATCO facility in Calgary, Canada.
“When I was doing maintenance plumbing work for the University of Alberta, I worked with a group of older gentlemen. They taught me so many cool tricks! I was warned about one fellow, though. I was told he didn’t like women getting into plumbing. They avoided putting me with him,” Potter says. “Then, about eight months into the job, I got stuck with him. We ended up having a blast! I’ve been lucky — my gender has never been an issue.”
Potter loves learning, which is part of the appeal of working in modular construction. “Usually, a jobsite is huge and you have a big area to work in by yourself. Modular is more challenging for a plumber. Here, you could have five or six people working in one room at the same time. It’s a quicker pace and we need to come up with safe solutions for tight working quarters.”
What Challenges Have You Faced With Modular Construction?
At ICON Architecture in Boston, USA, Kendra Halliwell is the Associate Principal, Practice and Design Team Leader.
"In general, you should be able to save four to six months of construction time by using modular construction. On one of our recent projects, the client's goal was to get the building operational and rented out earlier, so off-sire fabrication was the best option."
That worked well and the building was rented out significantly sooner than would have happened if they’d used conventional construction. But there were logistical challenges. “There are very few modular construction companies in the northeast and they’re very busy. Some of them are booked a year and a half into the future. Our fabricator was a five-hour drive away,” Halliwell says. “I’d love to see more modular factories serving this part of the country. The market is in need of more housing, and off-site fabrication may be the answer.”
Is Cost a Challenge?
Until recently, Zoe Kennedy was Marketing and Sales Manager for the UK subsidiary of De Meeuw, a large European modular manufacturing company. She’s now switched gears and is doing a Masters in Off-Site Housing Construction.
“The key advantage of modular construction is the consistent high quality. Modular can als o produce time savings of up to 50% compared to conventional construction, which means quicker ROC [return of capital]. We still have to be competitive on cost, though. And I’ve seen off-site come in at 30% more expensive than conventional construction.”
To counter this cost challenge, Kennedy says that modular construction companies need to think like manufacturers. “Manufacturing companies need consistent volume, otherwise fixed overheads result in uncontrolled costs. Consistent throughput is the only way we are going to see off-site construction go mainstream and help solve the housing shortage.”
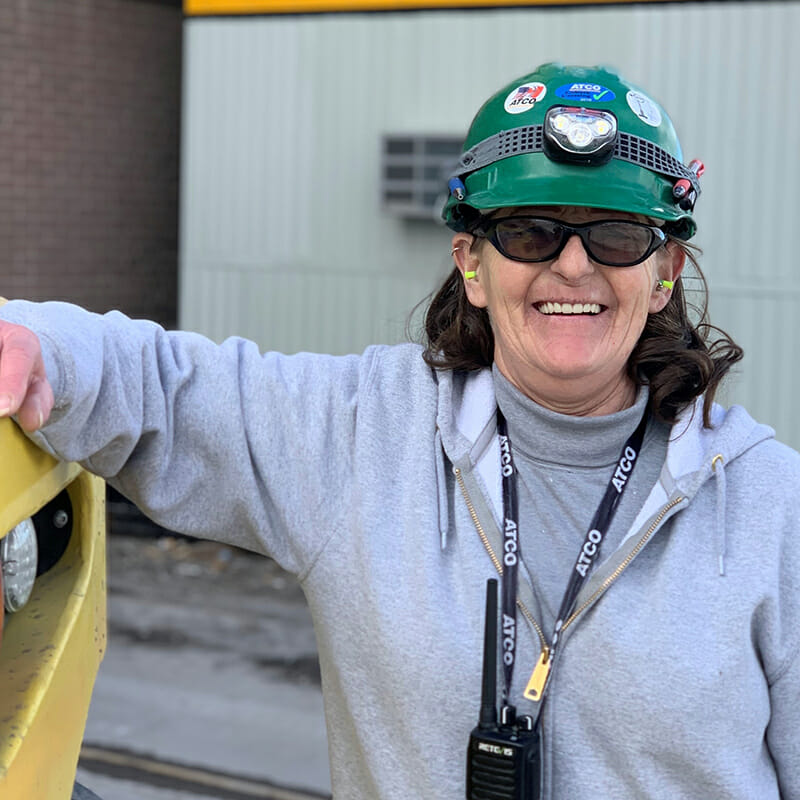
”Here, we’ve got women in framing, in HVAC, in our final finishing area. Women are starting to migrate into modular construction and they’re finding that it’s good work.”
Ronda Orchard, ATCO Facility Finishing Lead
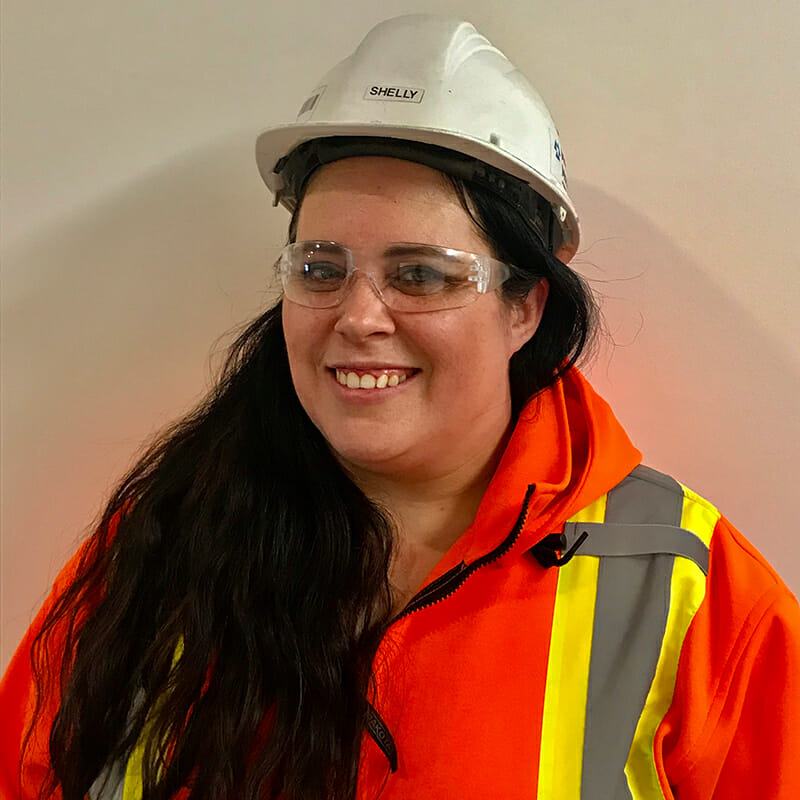
”The first couple of weeks were hard when I didn’t really know how to do very much, and didn’t know the safety procedures. There’s a big learning curve at the beginning. But I stuck it out and now I love working here.”
Shelly Coutu, Production Worker, Metric Modular
Is Sexism a Challenge in Construction?
“When I first started looking for a construction job, companies around here said they needed people,” says April Harmon, a framer at Volumetric Building Companies in North Carolina, USA.
“But as soon as they found out I was a woman, they said, ‘No, we can’t use you.’ I was told flat out that the problem was that I’m a woman. One person said, ‘That would be great if you’d work with us. Also, are you single?’ As soon as I didn’t want to date him, he didn’t want to hire me.”
Things are different at VBC. "I was able to get in here and prove myself. To some of the guys, I do still have to prove myself every day. A few will never come around." Most co-workers have, though. "I love that my co-workers come to me to answer their questions. It took a while for some of them, but they know I know my stuff. That's been very rewarding."
Are More Women Getting Involved?
Ronda Orchard has worked in modular construction since 1989 when she started at R Homes. She is now the Lead in Final Finishing at an ATCO facility in Idaho, USA and has worked there for seven years.
“When I started my first job, there were a few people who took me under their wing and taught me how to build floors, frame walls, everything. Some of those people are now working here at ATCO. When I first started at R Homes, it was all men. I never had a problem with that. I just respected them, and they’ve always respected me back. It’s only here at ATCO that I’ve noticed more women getting involved. Here, we’ve got women in framing, in HVAC, in our final finishing area. Women are starting to migrate into modular construction and they’re finding that it’s good work.”
What’s It Like To Work in a Modular Construction Factory?
Shelly Coutu is a Production Worker at Metric Modular, in British Columbia, Canada. She’s worked in five different factory departments during her eight years there, including as a saw operator. She now spends some of her workday in the plant, and some helping with the company’s admin.
“It’s nice that I work eight-hour days indoors, sometimes ten, if there’s overtime. I have friends and family who work long, hard days outside on conventional construction sites. They think it would be good to have my job!” she laughs. “You do need to have a bit of a thick skin when you first start, though. The first couple of weeks were hard when I didn’t really know how to do very much, and didn’t know the safety procedures. There’s a big learning curve at the beginning. But I stuck it out and now I love working here.”<
How Does Networking Help?
Phoenix Modular Elevator is based in Illinois, USA. Allison Allgaier is the Owner and President.
“We’re a teeny-tiny slice of the overall elevator market. There’s only one other company in the United States that makes modular elevators, but there are hundreds of conventional elevator companies. When contractors first discover us, they’re intrigued. But even if they hate the problems with site-built elevators and dealing with difficult elevator companies — it’s a case of the devil you know. With something new and unfamiliar to them, like modular construction, they don’t know what might go wrong.”
This current lack of awareness and acceptance of modular construction is partly why networking has been so important for Allgaier.
"MBI is a great network. We can be in the exhibition section at the World of Modular and everyone gets modular. The value proposition is very apparent to them. We have a lot of repeat customers who are MBI members."
How Can Collaboration Help?
“I’ve asked general contractors, ‘If you could get modular manufacturers to do one thing, what would it be?’” says Dafna Kaplan, Founder and CEO of Cassette, a modular design-build startup based in Los Angeles, USA.
“A big one was the standardization of the MEP [mechanical, electrical, plumbing] connections on modules. It’s an investment for general contractors to learn on their first modular project. But that investment pays off less if, when they go to the next project, things are done completely differently.”
“As providers, let’s come together and make it easier for the bold GCs who are learning to work on modular projects. Let’s try to agree on some standard things, like connections. Now’s the time to do this, while the industry is still small. It’s on my to-do list this year to reach out to colleagues in steel modular. I believe that the industry is in a place that rewards collaboration and knowledge-sharing. That collaboration excites me. It’s a thrilling time to be involved with modular construction.”
About the Author: Zena Ryder is a freelance writer, specializing in writing about construction and for construction companies. You can find her at Zena, Freelance Writer or on LinkedIn.
More from Modular Advantage
How BIM & AI are Improving Modular Construction Outcomes Across Europe
Digitalization and ever-advancing project modelling software have been aiding traditional manufacturers, builders, and designers for years. More recently, tech-savvy modular and offsite construction stakeholders have also embraced these tools, adding their own knowledge and data to create newer, faster, more efficient ways of building. Together with new BIM- and AI-powered tools, these builders are now pushing the boundaries of what’s possible with offsite construction and energy management.
Oregon’s Prevailing Wage Proposal: A Wake-Up Call for Modular Construction
Should House Bill 2688A become law, building projects would increase in price, face longer completion timelines, and produce significantly more waste. The bill also incentivizes contract awards to out of state businesses who would not reinvest their earnings into the local Oregon economy.
Behind the Design of Bethany Senior Terraces, NYC’s First Modular Passive House Senior Housing Project
As more developers seek to meet new regulations for energy efficiency, the team at Murray Engineering has set a new record. With the Bethany Senior Terraces project, Murray Engineering has helped to develop NYC’s first modular structure that fully encompasses passive house principles — introducing a new era of energy efficiency in the energy-conscious city that never sleeps.
How LAMOD is Using Modular to Address Inefficiency, Sustainability, and the Future of Construction
As developers, designers, and contractors seek to understand the evolving needs of the modular industry, no one is as well-versed in the benefits of going modular as Mārcis Kreičmanis. As the co-founder and CBDO of LAMOD in Riga, Latvia, Mārcis has made it his ultimate goal to address the inefficiencies of traditional construction.
From Furniture Builder to ‘Activist Architect’: Stuart Emmons’ Unique Journey
Stuart Emmons was fascinated by buildings at a young age. He remembers building sand cities with his brother during trips to the Jersey shore. His father gave him his first drawing table at the age of ten. Today, he is an experienced architect who received his FAIA in June 2025. The road he took is unique, to say the least.
Forge Craft Architecture + Design: Codes, Contracts, and Intellectual Property
Founding Principal and Director of Modular Practice for Forge Craft Architecture + Design, Rommel Sulit, discusses the implications of codes, contracts, and intellectual property on
modular construction.
Eisa Lee, the “Bilingual” Architect
Now as the founder of XL
Architecture and Modular Design in Ontario, Canada, she applies not just her education as a traditional architect but an entire holistic view on modular design. It’s this expansive view that guides her work on being a true partner that bridges the gap between architects and modular factories as they collaborate on the design process.
Tamarack Grove Engineering: Designing for the Modular Sector
The role of a structural engineer is crucial to the success of a modular project, from initial analysis to construction administration. Tamarack Grove offers structural engineering services — project analysis, plan creation, design creation, and construction administration — for commercial, manufacturing, facilities, public services, and modular. Modular is only one market sector the company serves but it is an increasingly popular one.
Engineer Masters the Art of Listening to His Customers
Since founding Modular Structural Consultants, LLC. in 2014, Yurianto has established a steady following of modular and container-based construction clients, primarily manufacturers. His services often include providing engineering calculations, reviewing drawings, and engineering certification
Inside College Road: Engineering the Modules of One of the World’s Tallest Modular Buildings
College Road is a groundbreaking modular residential development in East Croydon, South London by offsite developer and contractor, Tide, its modular company Vision Volumetric (VV), and engineered by MJH Structural Engineers.