Mike Bollero, Sr: A Leader in Modular Construction
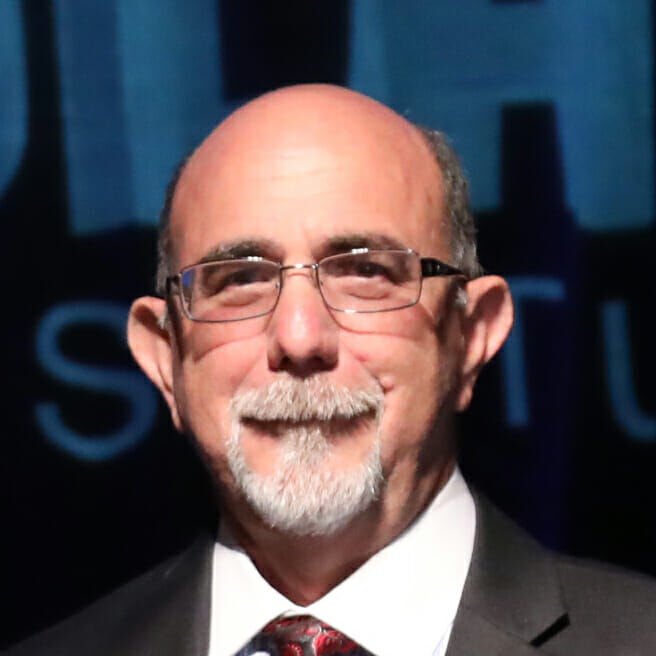
Mike Bollero, Sr., is the COO for Reliant Asset Management at Class Leasing.
“Location” is crucial for real estate, as we’ve all heard. It’s also a big factor in careers, as Mike Bollero shows. Thanks to its status as the recreational vehicle and modular building hub of the United States in the 1960s, Elkhart, Indiana, attracted plenty of local talent like Bollero.
Coming out of school in 1972, Bollero started a consulting business servicing the local modular office builders in Elkhart, such as Cliff Industries and Markline. Cliff Industries was launched by his uncle, Otto Miller, in fact. Bollero also benefited from good timing, as the modular construction industry was growing and starting to transition from the standard (for the time) 10x40 portable classrooms into construction camps and other uses for modular buildings.
A Nudge Into the MMOA
While running his business in 1983, Bollero established a business relationship with Bob McGrath of McGrath RentCorp. Incidentally, McGrath mentioned a new organization called the Mobile Modular Office Association and nudged Bollero into joining, which he did.
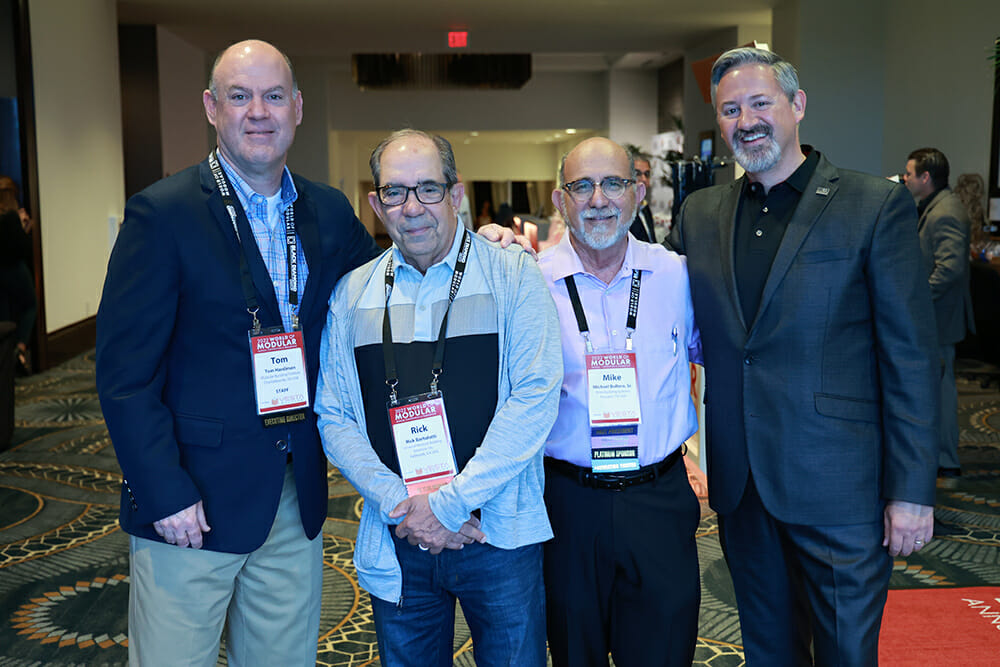
Tom Hardiman, Rick Bartolotti, Mike Bollero, Sr., and Steven Williams pose at the 2022 World of Modular in San Antonio.
Joining the MMOA led to serving the organization during the struggles with the International Code Council (ICC). At that time, the ICC was starting to exercise more control over more facets of the building industry. In particular, the ICC was threatening to refuse to accept already-built modular units as code compliant. Grandfathering” is the commonly used term for that process, and an unfavorable decision would have meant that hundreds of thousands of existing modular units would be essentially worthless. “We were looking at probably 400,000 leased units, and a couple billion dollars worth of assets,” Bollero said.
The ICC battle led Bollero into joining the MBI board of directors, and then later into the role of President. As President of MBI, Bollero identified several key business factors that drew his attention. “I really wanted to get our finances stronger than what they were,” he noted. “Second, we wanted to decrease the membership or the amount of board members but increase the stature of the board members. We wanted to get the owners and operators back into the board, making decisions for the industry.”
Also at that time, MBI established the Awards of Distinction to recognize great work in the industry. The Awards of Distinction were a milestone for any recipient, Bollero noted, and though he’s no stranger to taking home some accolades, there was also a bigger theme at work. “In all honesty, our first Awards of Distinction were more awards and recognition for company service, as much as for the actual building that you put in,” he said. Bollero also received the Lifetime Achievement Award for service to the industry.
That notion speaks to the overall growth of the industry from the mom-and-pop model to the vertically integrated model. “It was just nice to see that the business had evolved to where as an industry, we were no longer this cottage industry of a bunch of small, self-made businesses but we were actually turning into an industry that was recognized and doing some really neat stuff,” he said.
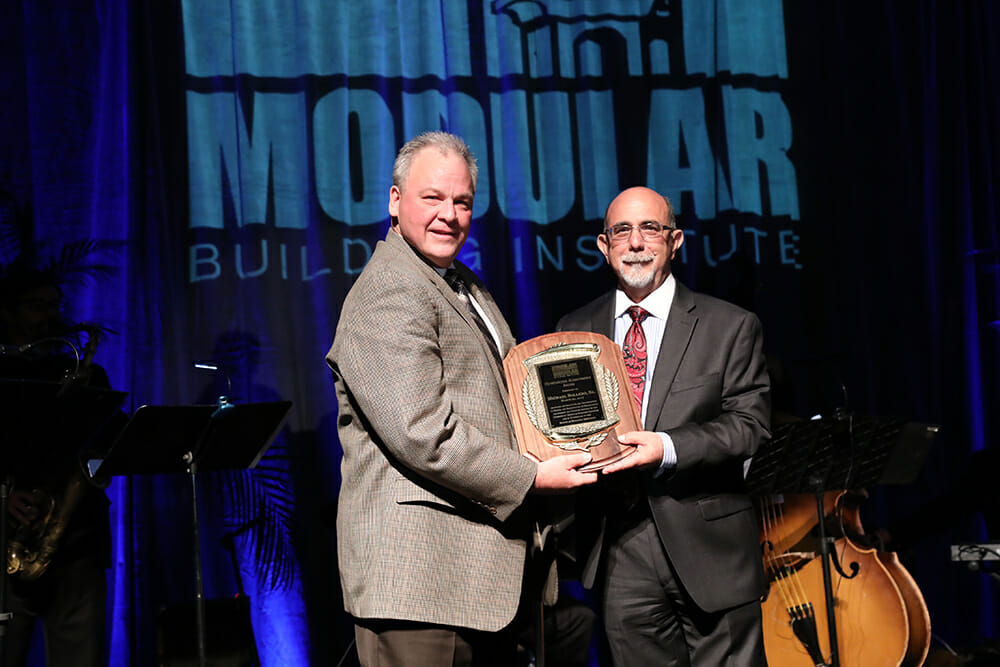
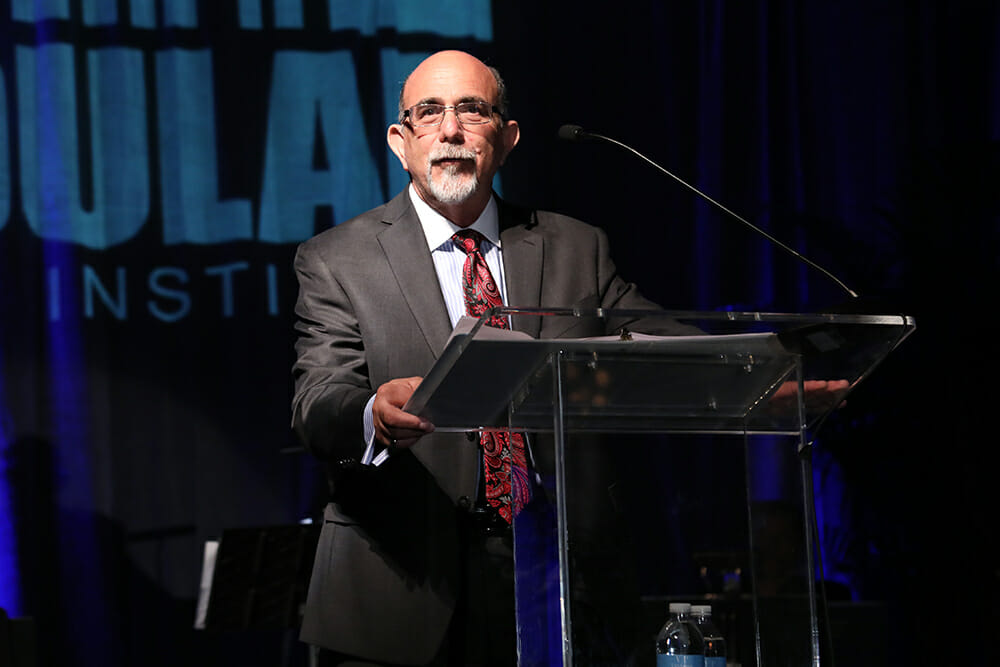
Mike Bollero, Sr., accepts MBI’s Outstanding Achievement award at the 2017 World of Modular.
The Industry Grows Up
From his time as a greenhorn in the early 1970s, Bollero has seen the modular construction industry mature through several phases. “When I entered it, people were basically doing construction trailers. What you put on the jobsite, and they were small,” he said. From there, though, the industry began to expand into much higher-quality products as well as into producing permanent structures. The businesses themselves also matured from the local “mom and pop” type of business into large, publicly traded companies, as well.
“In the 1990s we started building real buildings, multi-story permanent buildings. And then people started to become vertically integrated, like we are now with Class Leasing, where you manufacture your product and you sell your product. You’re not one or the other,” he noted.
In addition, the big players have come to dominate the industry, in contrast to past decades when smaller companies found their niches. “Now today, because businesses have grown to where the days of the Ma and Pa dealer are gone, basically it’s now big business,” Bollero said. “And if you don’t have $100–$200 million to get into the leasing business,
The Trend for Modular Construction
Bollero does not forecast radical changes in the modular construction industry in the next three to five years. Continued business maturation will happen, though.
“You’re going to continue to see vertical integration increase because of supply chain issues,” he said. Vertical integration requires a more robust business model overall, meaning manufacturers will be selling and leasing their output. They will also be more sophisticated in designing their products.
“I think that you’re going to see the manufacturers become much more project engineering oriented,” he said. “I think you’re going to see the bandwidth and the skill set of the industry overall increase as we push into a larger percentage of the total construction dollar mark.”
Enjoying the Ride
Since those early days more than 50 years ago, Bollero has seen the modular construction industry grow and mature remarkably. The industry has provided both enduring relationships with colleagues as well as interesting challenges along the way.
“I’ve enjoyed the whole ride. I mean, I have been blessed to make great friends, and have gone through some really good and really bad experiences,” he said. “But through it all there has always been a sense of camaraderie.”
Working on interesting projects has been another enjoyable experience for Bollero. “I’ve always felt like we’ve tried to be on the cutting edge of trying to take the projects that maybe other people weren’t going to take and doing something new and different. It never got boring. And there was always a new challenge. And that was what made it fun.”
As for coaching his younger self if he were starting now, Bollero said, “Probably to be a little bit less of a risk taker from a professional standpoint, but other than that, I don’t know that I would change much.”
About the Author: Steve Hansen is a Colorado-based writer with a focus on the built environment—architecture, construction, renewable energy, and transportation. He can be reached on LinkedIn.
More from Modular Advantage
How BIM & AI are Improving Modular Construction Outcomes Across Europe
Digitalization and ever-advancing project modelling software have been aiding traditional manufacturers, builders, and designers for years. More recently, tech-savvy modular and offsite construction stakeholders have also embraced these tools, adding their own knowledge and data to create newer, faster, more efficient ways of building. Together with new BIM- and AI-powered tools, these builders are now pushing the boundaries of what’s possible with offsite construction and energy management.
Oregon’s Prevailing Wage Proposal: A Wake-Up Call for Modular Construction
Should House Bill 2688A become law, building projects would increase in price, face longer completion timelines, and produce significantly more waste. The bill also incentivizes contract awards to out of state businesses who would not reinvest their earnings into the local Oregon economy.
Behind the Design of Bethany Senior Terraces, NYC’s First Modular Passive House Senior Housing Project
As more developers seek to meet new regulations for energy efficiency, the team at Murray Engineering has set a new record. With the Bethany Senior Terraces project, Murray Engineering has helped to develop NYC’s first modular structure that fully encompasses passive house principles — introducing a new era of energy efficiency in the energy-conscious city that never sleeps.
How LAMOD is Using Modular to Address Inefficiency, Sustainability, and the Future of Construction
As developers, designers, and contractors seek to understand the evolving needs of the modular industry, no one is as well-versed in the benefits of going modular as Mārcis Kreičmanis. As the co-founder and CBDO of LAMOD in Riga, Latvia, Mārcis has made it his ultimate goal to address the inefficiencies of traditional construction.
From Furniture Builder to ‘Activist Architect’: Stuart Emmons’ Unique Journey
Stuart Emmons was fascinated by buildings at a young age. He remembers building sand cities with his brother during trips to the Jersey shore. His father gave him his first drawing table at the age of ten. Today, he is an experienced architect who received his FAIA in June 2025. The road he took is unique, to say the least.
Forge Craft Architecture + Design: Codes, Contracts, and Intellectual Property
Founding Principal and Director of Modular Practice for Forge Craft Architecture + Design, Rommel Sulit, discusses the implications of codes, contracts, and intellectual property on
modular construction.
Eisa Lee, the “Bilingual” Architect
Now as the founder of XL
Architecture and Modular Design in Ontario, Canada, she applies not just her education as a traditional architect but an entire holistic view on modular design. It’s this expansive view that guides her work on being a true partner that bridges the gap between architects and modular factories as they collaborate on the design process.
Tamarack Grove Engineering: Designing for the Modular Sector
The role of a structural engineer is crucial to the success of a modular project, from initial analysis to construction administration. Tamarack Grove offers structural engineering services — project analysis, plan creation, design creation, and construction administration — for commercial, manufacturing, facilities, public services, and modular. Modular is only one market sector the company serves but it is an increasingly popular one.
Engineer Masters the Art of Listening to His Customers
Since founding Modular Structural Consultants, LLC. in 2014, Yurianto has established a steady following of modular and container-based construction clients, primarily manufacturers. His services often include providing engineering calculations, reviewing drawings, and engineering certification
Inside College Road: Engineering the Modules of One of the World’s Tallest Modular Buildings
College Road is a groundbreaking modular residential development in East Croydon, South London by offsite developer and contractor, Tide, its modular company Vision Volumetric (VV), and engineered by MJH Structural Engineers.