Building a Better World with Modern Methods of Construction (MMC)
As a global general contractor with 40+ years of experience, DORCE’s projects have run the gamut of modular and prefabricated construction.
DORCE Prefabricated Building & Construction—with production, export, and international contracting operations—is one of Turkey’s strongest brands in the global market. DORCE is also one of the first established and now-leading companies in Turkey for prefabricated modular steel structures. As a general contractor in more than 60 countries, DORCE meets all kinds of needs on a turnkey basis in different geographical regions under harsh climatic conditions at the same time with in-house engineering, procurement, production, logistics, assembly, infrastructure and superstructure works, including testing and commissioning.
In fact, DORCE owns one of the largest prefabricated steel structure production facilities in Europe, operating within the scope of local and international quality standards. In different continents and countries across the globe, DORCE has been able to realize multiple projects at the same time in different sectors including: oil & gas, mining, defense, humanitarian aid & disaster management (refugee facilities, earthquake housing units, residential projects, etc.), healthcare, construction industry, and housing.
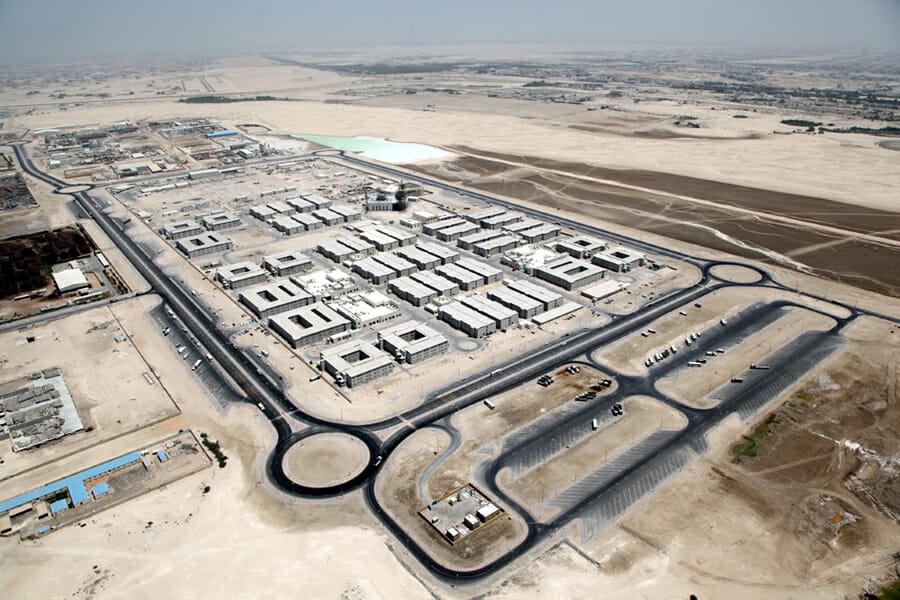
Prefabricated Residential City for 26.000 Workers: All work for this massive workforce housing complex, including the design, engineering, infrastructure, and superstructure, was completed by DORCE. The contract model for the project on was based on a 40-year Build-Operate-Transfer (BOT) model. Construction lasted approximately four years while the superstructure was completed much more quickly—around 290 days—using DORCE’s prefabricated modular & pre-engineered steel systems.
Oil, Gas, and Renewable Energy
DORCE is involved in many turnkey energy pipeline projects ranging from camp structures, accommodation facilities, and management offices with prefabricated modular steel structures to remote, temporary camps that span thousands of kilometers along a pipeline’s route.
Mining
DORCE provides production and contracting services within the scope of turnkey construction of mining accommodation cities such as:
- Shelters, residences / accommodation facilities, and management offices;
- Hospitals and clinics;
- Markets, dry food stores, cold rooms, high-capacity kitchens, industrial dining halls & industrial laundries;
- Mining storage & processing warehouses; and
- Operational and service buildings.
DORCE has completed mining support projects in Chile, Mongolia, Australia, Canada, Africa, and Turkey.
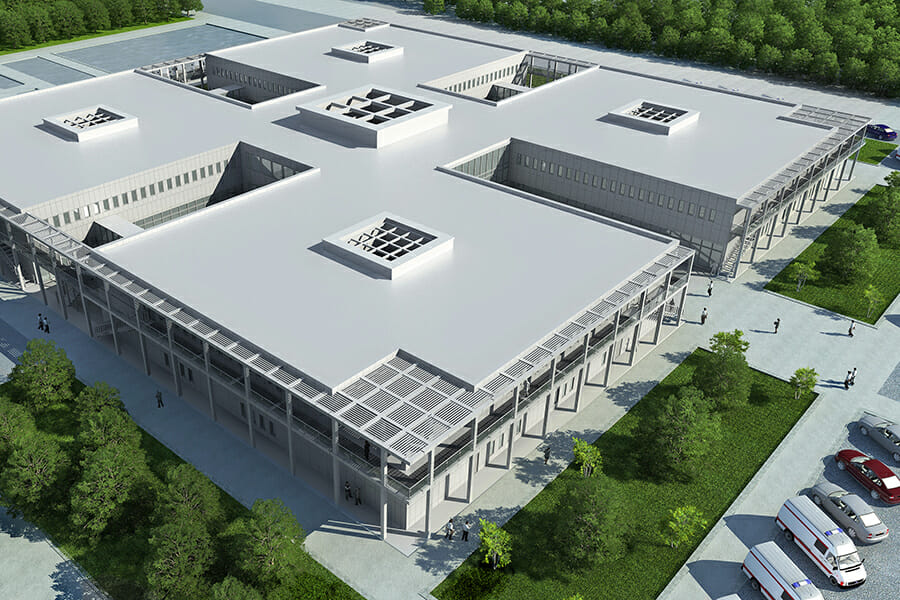
160 Bed Capacity 4 General Hospital: Utilizing Front End Engineering Design (FEED) and an Engineering, Procurement and Construction (EPC) process, the infrastructure and superstructure work for this hospital was completed by DORCE. A “hybrid building system” was utilized due to use of both light steel panels and a heavy steel structure system.
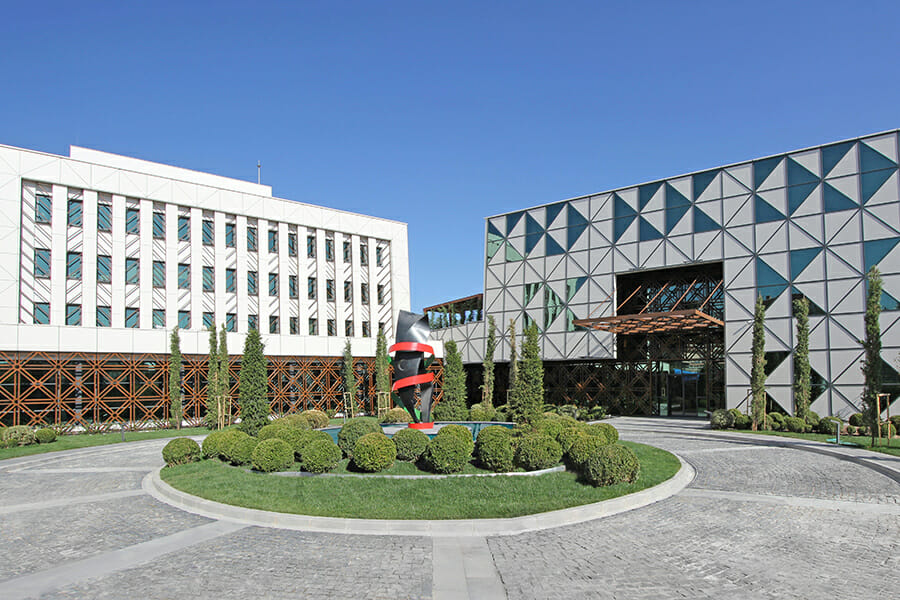
A Modular Building Fit for a King (or an Ambassador): Libyan Embassy & Administration Buildings in Ankara, Turkey, built by DORCE.
Related Listening:
Examining the Global Modular Construction Market w/ DORCE Ltd.
In this episode of Inside Modular, Mehmet Yucesoy, business development manager at Turkey's DORCE Ltd., shares DORCE's 40-year story of international success and details how modular construction can be applied to almost any construction market around the world. Mehmet also gives advice on how modular companies can begin to expand their globalization efforts.
Defense Industry
For over 35 years, DORCE has completed defense industry projects in 30+ countries, especially for NATO and NATO-member countries, the United Nations, and the Turkish Armed Forces. DORCE is a leading manufacturer of multi-purpose modular container systems such as; field (mobile) hospitals, bullet-proof facilities, turnkey military bases / camps, Air Portable Containers, education centers, and many others.
In addition, DORCE is a leading manufacturer of aircraft and helicopter hangar projects. These high-end projects—which often require prefabricated heavy steel structures—often house military helicopters, as well as F-16 & F-35 fighter jets.
Health Sector
DORCE is a manufacturer and turnkey supplier of steel prefabricated, modular, and/or mobile hospitals. During the COVID-19 pandemic, DORCE completed intensive care units, quarantine hospitals, and emergency aid facilities in 20+ countries by offering excellent flexibility and customizability on a variety of advanced hospital solutions.
Housing Sector
DORCE is also one of the preeminent companies providing prefabricated steel housing to affordable, mid-class, and luxury home buyers.
For example, more than 560,000 detached houses in California were completed with prefabricated modular building systems with evolving technology due to speed and strength of construction. DORCE took part in thousands of square meters of prefabricated housing projects in more than 20 countries with its capabilities, know-how and experience on building design, manufacturing, and construction.
In addition to the growing need for stronger houses, the volume of housing units needed—especially in urban areas—is rapidly growing. The increasing population and the emerging need for affordable housing in urban areas can be solved with Prefabricated Modular Rapid Mass Housing Projects.
With the support of its contracting services, DORCE has the capacity to quickly produce thousands of turnkey housing units. Prefabricated Modular Rapid Mass Housing is a new building trend in which production, transportation, and construction stages are all transparent, which can lead to easier access to warranties, insurance, and financing. Prefabricated Modular Rapid Mass Housing projects completed by DORCE’s off-site construction methods increase the prestige of the project owner, local community, public and private authorities with thousands of houses.
Government and Administrative Sector
DORCE completes turnkey construction of embassies as well as municipal and public buildings in more than 30 countries.
The Libyan embassy building in Ankara, Turkey, is the newest and most modern project in Turkey as of 2020. Renovation of one of the buildings was completed through rough construction. After the other structures were completely demolished, the rest of the embassy was rebuilt in accordance with modern design qualities and integrated into the remaining building.
The entire scope of the project—in accordance with the highest security measures—included bullet-proof rooms, a parking garage, conference-reception areas, meeting rooms, accommodation and office areas, as well as landscape and design services, engineering, superstructure, infrastructure, furniture, equipment, and testing and commissioning processes, and were completed on a turnkey basis.
A Building for Every Need
From humanitarian support to defense to residential, prefabricated modular steel building systems are the preferred construction method for buildings around the world. DORCE has the capability to produce large quantities of turnkey projects to suit any need.
More from Modular Advantage
How BIM & AI are Improving Modular Construction Outcomes Across Europe
Digitalization and ever-advancing project modelling software have been aiding traditional manufacturers, builders, and designers for years. More recently, tech-savvy modular and offsite construction stakeholders have also embraced these tools, adding their own knowledge and data to create newer, faster, more efficient ways of building. Together with new BIM- and AI-powered tools, these builders are now pushing the boundaries of what’s possible with offsite construction and energy management.
Oregon’s Prevailing Wage Proposal: A Wake-Up Call for Modular Construction
Should House Bill 2688A become law, building projects would increase in price, face longer completion timelines, and produce significantly more waste. The bill also incentivizes contract awards to out of state businesses who would not reinvest their earnings into the local Oregon economy.
Behind the Design of Bethany Senior Terraces, NYC’s First Modular Passive House Senior Housing Project
As more developers seek to meet new regulations for energy efficiency, the team at Murray Engineering has set a new record. With the Bethany Senior Terraces project, Murray Engineering has helped to develop NYC’s first modular structure that fully encompasses passive house principles — introducing a new era of energy efficiency in the energy-conscious city that never sleeps.
How LAMOD is Using Modular to Address Inefficiency, Sustainability, and the Future of Construction
As developers, designers, and contractors seek to understand the evolving needs of the modular industry, no one is as well-versed in the benefits of going modular as Mārcis Kreičmanis. As the co-founder and CBDO of LAMOD in Riga, Latvia, Mārcis has made it his ultimate goal to address the inefficiencies of traditional construction.
From Furniture Builder to ‘Activist Architect’: Stuart Emmons’ Unique Journey
Stuart Emmons was fascinated by buildings at a young age. He remembers building sand cities with his brother during trips to the Jersey shore. His father gave him his first drawing table at the age of ten. Today, he is an experienced architect who received his FAIA in June 2025. The road he took is unique, to say the least.
Forge Craft Architecture + Design: Codes, Contracts, and Intellectual Property
Founding Principal and Director of Modular Practice for Forge Craft Architecture + Design, Rommel Sulit, discusses the implications of codes, contracts, and intellectual property on
modular construction.
Eisa Lee, the “Bilingual” Architect
Now as the founder of XL
Architecture and Modular Design in Ontario, Canada, she applies not just her education as a traditional architect but an entire holistic view on modular design. It’s this expansive view that guides her work on being a true partner that bridges the gap between architects and modular factories as they collaborate on the design process.
Tamarack Grove Engineering: Designing for the Modular Sector
The role of a structural engineer is crucial to the success of a modular project, from initial analysis to construction administration. Tamarack Grove offers structural engineering services — project analysis, plan creation, design creation, and construction administration — for commercial, manufacturing, facilities, public services, and modular. Modular is only one market sector the company serves but it is an increasingly popular one.
Engineer Masters the Art of Listening to His Customers
Since founding Modular Structural Consultants, LLC. in 2014, Yurianto has established a steady following of modular and container-based construction clients, primarily manufacturers. His services often include providing engineering calculations, reviewing drawings, and engineering certification
Inside College Road: Engineering the Modules of One of the World’s Tallest Modular Buildings
College Road is a groundbreaking modular residential development in East Croydon, South London by offsite developer and contractor, Tide, its modular company Vision Volumetric (VV), and engineered by MJH Structural Engineers.