CO Developer ‘Attacks’ Attainable Housing Crisis
City, county, and state government bodies are reaching out to Fading West Development, a modular manufacturer and developer in Buena Vista, CO, to learn more about how they are using modular construction to solve the affordable housing crisis in Colorado. Governments are eager to learn how they’ve made modular development successful and profitable while meeting the growing need for affordable housing.
Fading West was formed in 2016, when CEO Charlie Chupp built a development called The Farm at Buena Vista to address the lack of affordable housing in the area. Chupp owned a couple of businesses in town but couldn’t find employees because of the high cost of buying a home. He was familiar with modular and panelized construction, coming from a lean manufacturing background, so he decided to tackle the problem himself.
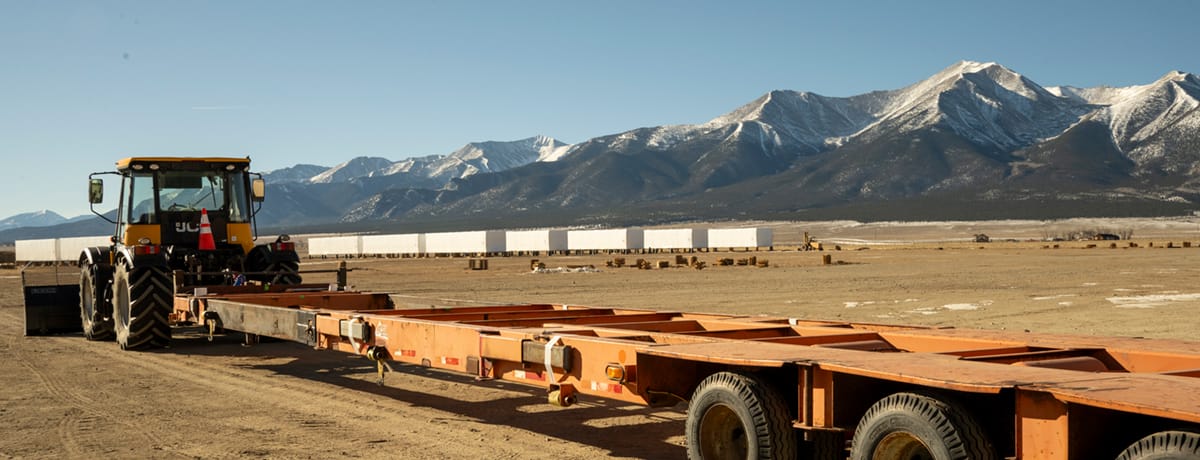
One of Fading West’s neighbors is Colorado Mountain College. The college owns 24 acres just south of the company’s factory, which is on an 8-acre parcel. “We needed a construction easement on the college property, so we contacted them about that. We told them what we’re doing and they were excited about it,” Fading West CEO Charlie Chupp recalls. Now Fading West is partnering with the college. “We have a long-term lease on some of their land, which we use to store finished modules.”
He bought some land and began to build a mixed-use community for workers using modular construction. The Farm includes townhouses, detached single-family homes, several small parks, and a central pavilion that contains grills and a fire pit for residents to use to foster a sense of community. An apartment complex with over 100 units is also planned. The first phase of the project sold out, and phase two was in high demand.
With this successful proof of concept, Chupp began to look at how he could improve the quality of the units and reduce costs and construction time. He’d purchased modular homes for phase one from another company, but as the development grew he saw an opportunity to utilize his lean manufacturing background to efficiently build modular homes in Buena Vista, so he decided to start his own manufacturing company.
Enter Fading West
Fading West began modular manufacturing operations in November 2021. Their factory is 110,000 square feet and it houses a twenty station U-shaped assembly line with a central mill area where all the cutting and fabricating takes place. All sub-assemblies, such as walls and ceilings, are constructed in the central mill, then delivered to the appropriate assembly station for installation. There are no saws or tape measures on the assembly line.
The factory currently runs one ten-hour shift, and they can build a single-family home in eight days. The assembly line moves every four hours, and they complete one house a day, averaging 22 to 25 houses per month. When they build apartments or other multi-family buildings, the line moves every seven hours, and it takes about twelve days to complete one unit.
Currently they are producing four single-family home models: (1) 1,000 square foot, two bedroom, one and a half bathrooms; (2) 1,200 square foot, three bedroom, two bathrooms; (3) 1,600 square foot, three bedrooms, two and a half bathrooms; and (4) 1,600 square foot, four bedrooms, two and a half bathrooms. All homes are two stories and are made from two connected modular units.
Optimizing the Factory
Current Vice President of Factory Operations, Sean Brown, started at Fading West in August 2022. With an education in engineering, he brought 15 years of factory optimization experience with the aerospace and energy sectors. He was intrigued by the opportunity to become part of the solution to the housing crisis, so he moved his family to Colorado to join the team.
Brown said they are “attacking the entire cost of housing. We’re more than just a modular factory, we’re also a turnkey community provider. We call it the ‘easy’ button.” Many don’t realize that the cost of housing includes not only construction of the home itself, but also site work and utilities, purchasing the land, permits and fees, and design and engineering. Fading West is working to reduce these costs by creating attainable modular homes that can be set quickly (in as little as five weeks). They are also working with local and state governments to change codes and regulations to make it more affordable and enticing to build economical housing.
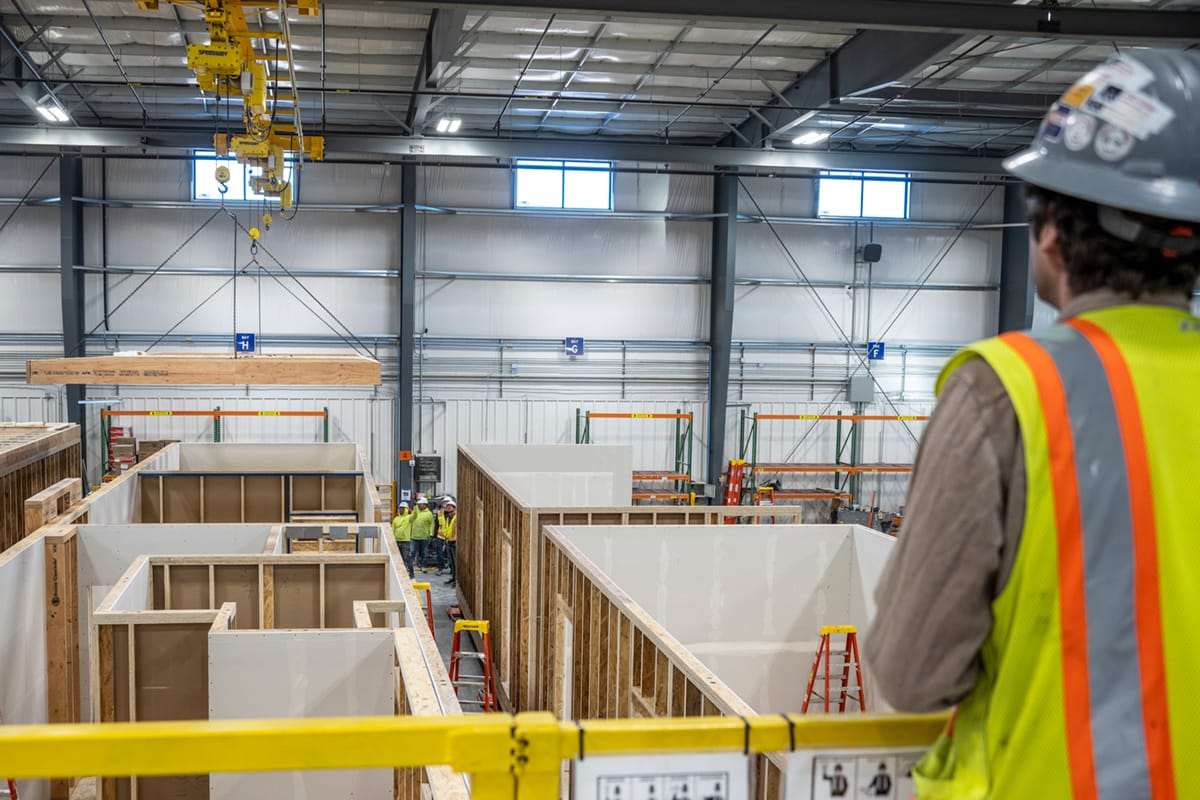
Fading West Area Manager Lawson Odom flying a completed ceiling cassette assembly to meet up with the floor/wall assembly.
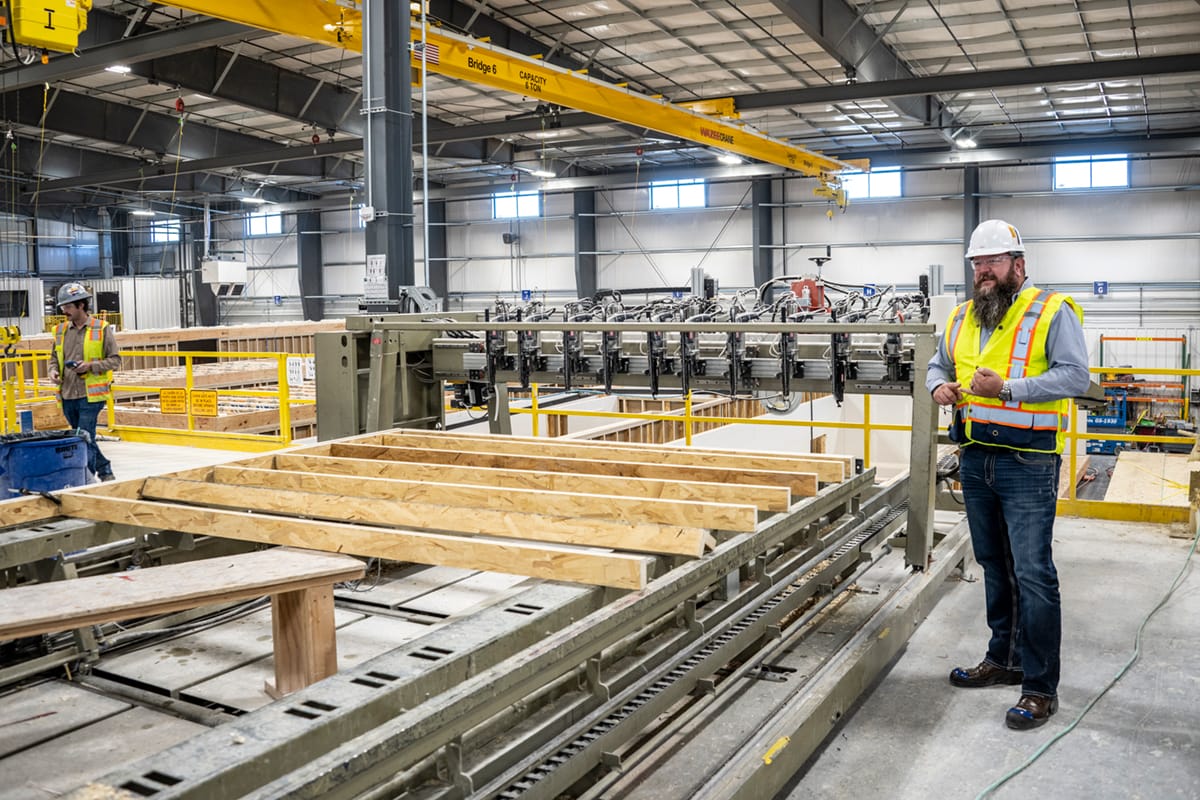
Sean Brown reviews standardization in an exterior wall build.
Meeting the Urgent Need for Housing
Their solution is in high demand. Brown said the company is currently working with a couple of Colorado towns to create affordable housing. “They’re coming to us and we’re acting as consultants to them on how to build the development. We’re doing most of the design, we’re building the houses, then, our construction company will either sell the boxes and perform the site work, or we will work as consultants with another general contractor to ensure that everything gets set in place carefully. That’s what we call our ‘easy button.’”
One of lean manufacturing’s concepts is continual improvement. The leadership team at Fading West is always looking for ways to refine and optimize their processes. This has led to a tripling in production since manufacturing began in 2021. And, with only one shift working, there’s room for more production when it’s needed. Their goal is to continually increase production to help an ever growing list of communities in need of attainable housing.
Ironically, the lack of affordable housing may be the biggest challenge they face when it comes to increasing production. They already rent local houses for their employees, but there aren’t many options available. So, they’ve taken the problem into their own hands, and are working on the design and construction of a dormitory for their workers.
Another challenge was their mindset. Brown said, “There’s a lot of thought in the industry that modular is just construction indoors. At Fading West, we don’t think of ourselves as a construction company. We think of ourselves as a manufacturing company.” They brought in manufacturing experts, not construction experts. Those experts understood factory workflow, lean manufacturing, how to eliminate waste, and how to set targeted goals and analyze the data when those goals are missed. The change “allowed us to break some of the entrenched faults with construction and approach those challenges in a different way and with an open mind,” Brown said.
With the increased demand for affordable housing and their solution in particular, they are eyeing expansion of their service areas in 2024. Brown said projects in New Mexico, Utah, and Wyoming may be on the horizon. They are also making plans to build a second factory within the next three years. A location hasn’t been selected yet, and they are receiving regular calls from municipalities wanting them to build in their communities.
They are considering all their options and want to make sure the location can provide the workforce they need and that there’s enough affordable housing to support it. The new factory will have dual assembly lines, allowing them to optimize each line for the specific unit types they’re making.
Building Communities
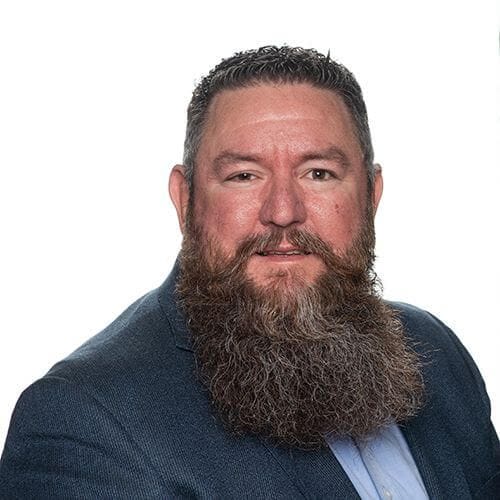
What to Expect at the 2024 World of Modular
Sean Brown, Vice President of Factory Operations, Fading West
Sean Brown will be presenting at the 2024 World of Modular conference, giving attendees valuable insight into the productization of construction and how to improve manufacturability and affordability. The focus will be on factors that need to be considered when designing single-family homes and multi-family units for modular construction. His hope is that designers, architects, and engineers will learn how designing for modular construction is different from traditional construction methods and that they’ll walk away with fresh ideas on how to improve their designs.
Brown sees Fading West’s mission as more than just building homes, they’re building communities. “Our communities were dying because restaurants were closing because they couldn’t get waiters. Our schools were struggling because they couldn’t get teachers. We have placed 300 homes in small mountain towns within the last two years. That’s 300 families that would be struggling to find a place to live if it wasn’t for us.”
The Farm at Buena Vista
Fading West Development, Building Systems, Construction, Properties
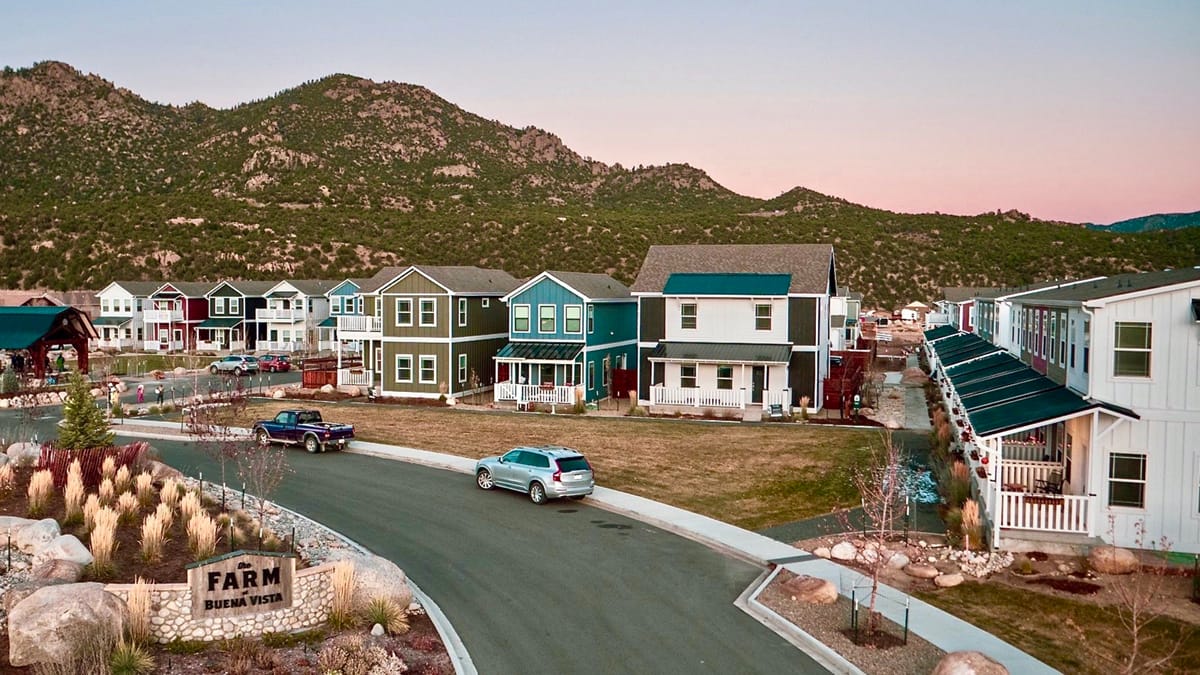
Fading West has shown robust demand for its product through the highly successful ongoing build-out of The Farm at Buena Vista. The project has sold all 90 units in Phase I with continued strong demand for Phase II deliverables. Substantial price appreciation in units sold demonstrates both build quality and the desirability of a thoughtfully designed community.
A Fading West Community
Designed around communal green spaces and parklets, the Farm’s mix of townhomes and detached single-family homes is highly space efficient, seamlessly blending attainability with livability.
Integrated Advantage
From initial development to manufacturing and site construction, up through property management and sales, Fading West’s fully integrated value stream has helped make the Farm a highly successful project.
About the Author: Dawn Killough is a freelance construction writer with over 25 years of experience working with construction companies, subcontractors and general contractors. Her published work can be found at dkilloughwriter.com.
More from Modular Advantage
Samantha Taylor: Leading the (Modular) Design of Tomorrow
“With modern technology and the way we’ve all embraced things like BIM, file sharing, and video conferencing since COVID, it’s easy to collaborate with companies in Austria, or Singapore, or anywhere else in the world.”
Greg DeLeon: Military Engineering to Modular Design
Greg DeLeon, a structural engineer at ISE Structural Engineers in Temecula, California, can tell you not only how large a beam needs to be to support a house, but also how much explosives you’ll need to take it down, thanks to his unique combination of professional and military experience.
To Remake North Minneapolis, Devean George Swaps Basketball for Buildings
He’s lived in Los Angeles, Dallas, and San Francisco (to name a few). He’s delivered championships with the Los Angeles Lakers and made career-defining moves with the Dallas Mavericks and the Golden State Warriors. No matter the wins, the championships, or even the seemingly impossible 3-pointers, Devean George has always returned to where it all started for him: Minneapolis.
Chelsi Tryon: Making the World a Better Place
For Chelsi Tryon, Director of Environmental, Social, and Governance (ESG) for WillScot Mobile Mini, nothing is more enjoyable than increasing the
company’s sustainability efforts while simultaneously doing her bit to save the environment.
Joshua Hart: Pushing Boundaries
Joshua Hart, P.E., vice president at Modular
Solutions, can sum up his job responsibilities in one sentence: “I do whatever needs to be done.” Hart thrives on the variety and the opportunity to be involved in every aspect of the company. And it shows! You might say Hart has come full circle.
Jamie Metzger: From Construction to Apparel and Back Again
Growing up in a blue-collar city like Edmonton, Alberta, Canada, it’s no surprise that Jamie Metzger spent some time working labor jobs on construction sites. It’s one of the most common summer jobs in the city. But that’s probably the last predictable thing about this particular story.
Victor Masso: Expanding Modular in Puerto Rico
Victor Masso joined 2 Go Storage, a company started by his grandfather and father, in 2018 to develop a modular building division in the wake of the devastation caused by Hurricane Maria in 2017. Prior to joining the company, he had worked in the industry for about four years focusing on pharmaceutical, commercial, and government projects.
Eliyah Ryals: Finding the Perfect Fit
It’s not common for people to find their perfect career fit straight out of college. It’s even less common to find it in the town you grew up in. But that’s exactly what happened when Eliyah Ryals was told about vacancies at Panel Built and made the decision to apply.
Through It All, It’s Still About the Workers
By February 2024, the number of available, unfilled construction job openings had reached an all-time high. At some point, interest rates will fall, creating another surge in demand for such workers. In short, solving the nation’s skilled worker shortage issue has never been more important.
Navigating Insurance Challenges in the Modular Construction Industry
Utilizing practical written minimum insurance and indemnity requirements, along with monitoring certificates of insurance by someone who has COI training will not yield a perfect risk transfer strategy, but the exposure will be managed much better than it likely is currently.