26 Stories in 5 Days - How BROAD Sustainable Building is Redefining the Speed of Modular
On January 7, 2024, BROAD Sustainable Building began assembling the new 26-story mixed-use Jindu Residential Tower. On January 11, just five days later, construction was completed.
But for BROAD, this was just another day at the office.
In fact, the Jindu Residential Tower represents the 16th generation of BROAD’s Holon Building concept, a modular construction design that uses foldable, container-sized units that BROAD first started developing nearly 15 years ago.
“BROAD Sustainable Building was founded in 2009,” said Jeremy Zimman, Director of Marketing, Holon Modular Building Systems at New Jersey-based BROAD USA, “in response to a large earthquake that happened in China in 2008, close to where our parent company, BROAD Group, is based. There were tens of thousands of people who lost their lives. Our chairman and founder saw that these buildings made of concrete were falling like dominoes, so he resolved to make more durable steel buildings.”
And while the use of steel wasn’t exactly revolutionary, BROAD’s embrace of stainless steel is.
“We transitioned to stainless steel about five years ago,” said Zimman, “because we realized the mechanical properties of stainless included not only non-corrosion, which is good for facades, but stainless steel also has a great ductility—the ability to withstand tensile stress. That's the reason we chose stainless for our load-bearing members. We're the first to do that.
“So now,” continued Zimman, “even though our volumetric product is just two years old, we’ve been in a continuous state of innovation. For instance, in the first Holon building that we built two years ago, the beams had to be put in on site. And now, when we lower the modules, the flooring system of those modules have the beams built in. So, there's no welding on site. It's only bolting. We have the cranes ready; we just pick and place, stack, bolt, connect utilities, and we're good to go.”
“Our building is turnkey,” said Zimman. “When construction is over, it's move-in ready. It includes all the fixtures like air conditioning, our own ventilation system—energy-recovery ventilation, which is a principle of Passive House—that’s included. Even water tanks are in place.
“The only thing not included is movable appliances. Refrigerators, washers, dryers, dishwashers, microwaves; other than those appliances, the building is ready to occupy.”
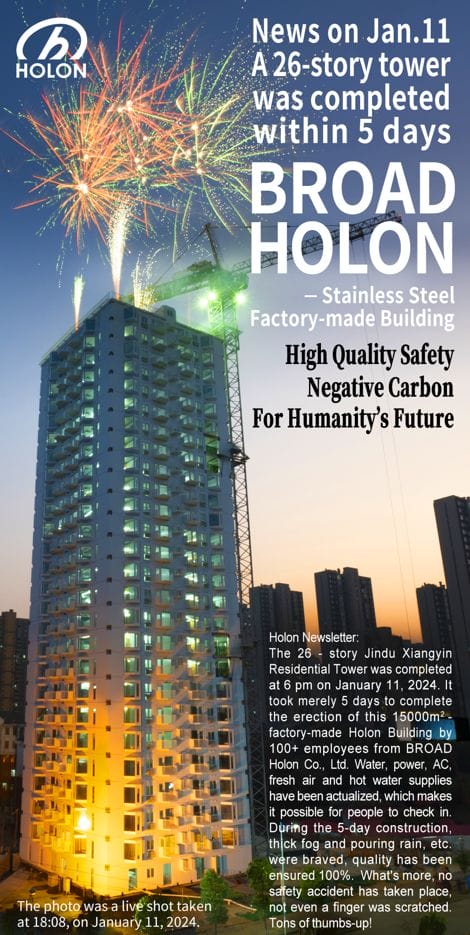
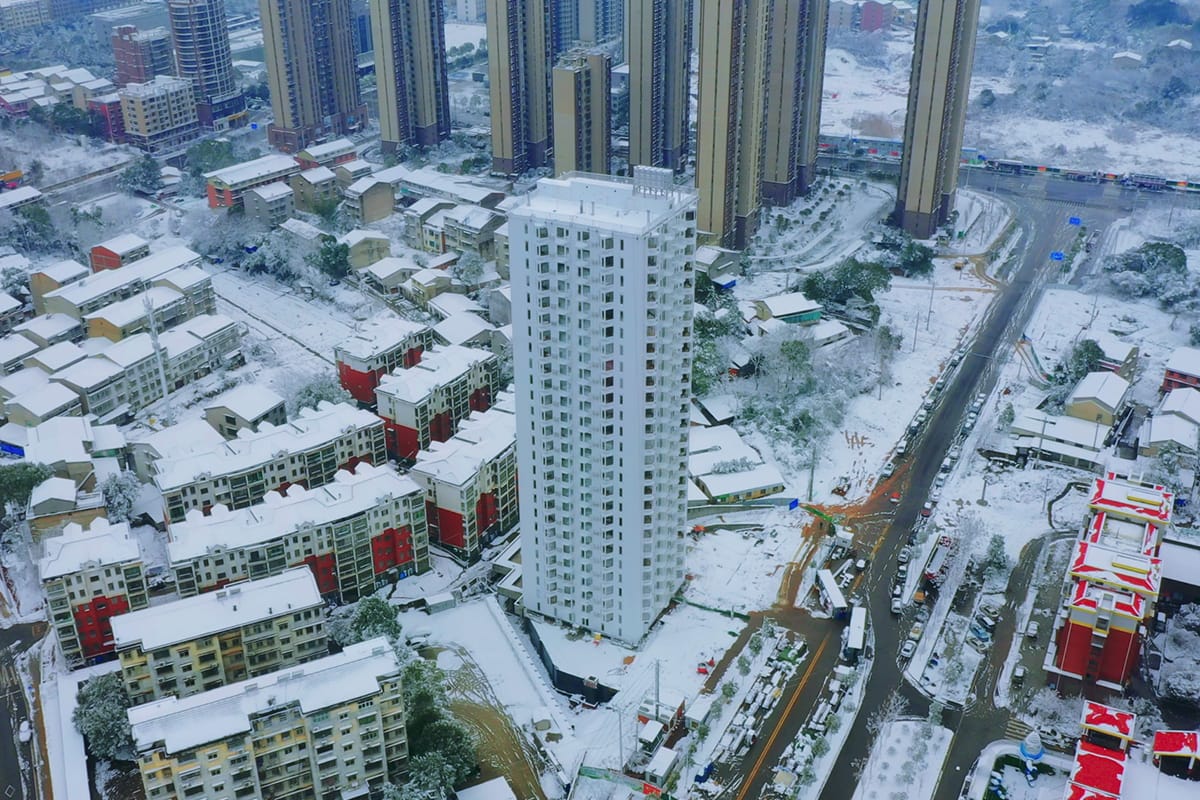
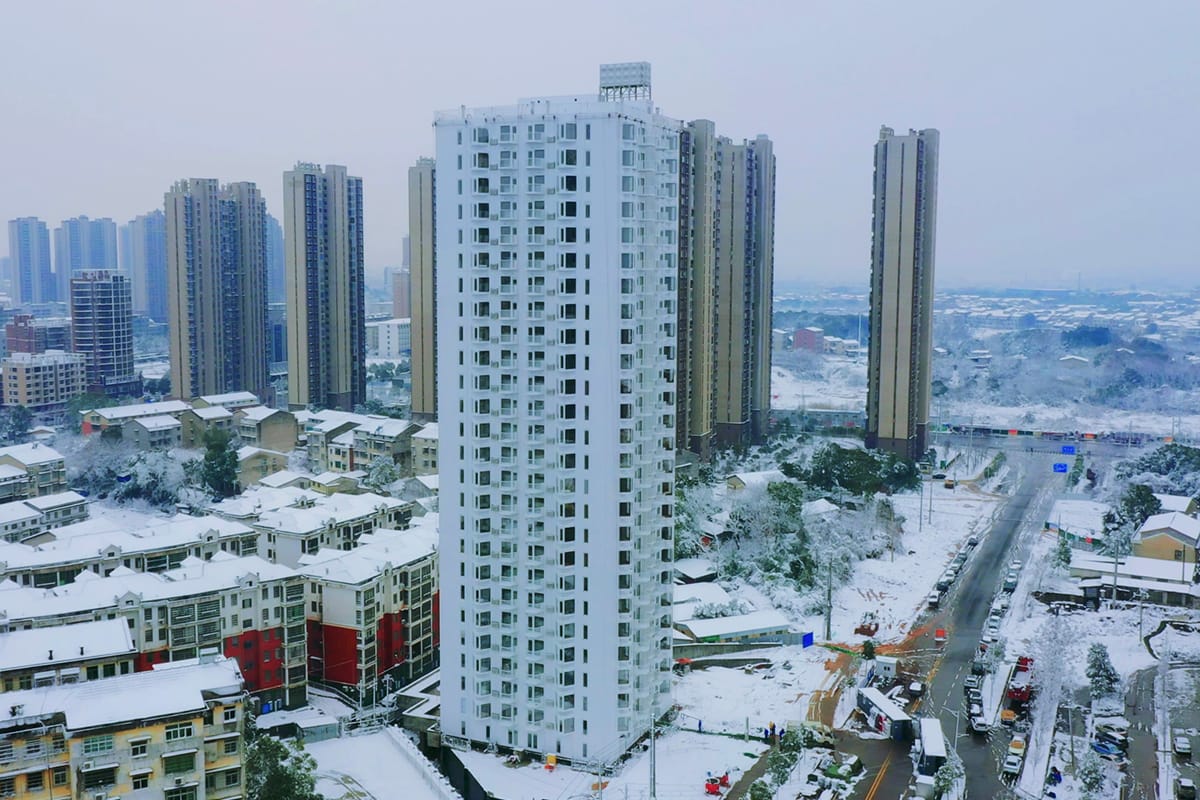
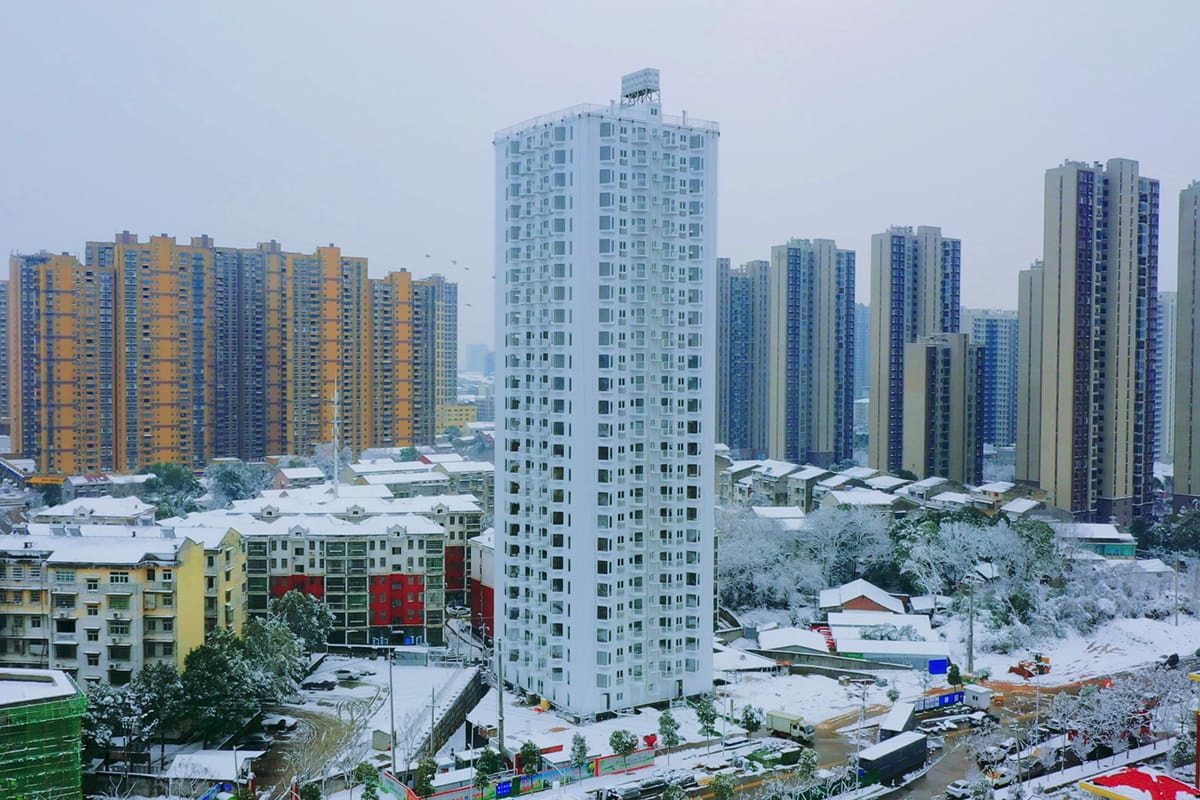
The Jindu Residential Tower was assembled in just 5 days by BROAD Sustainable Building.
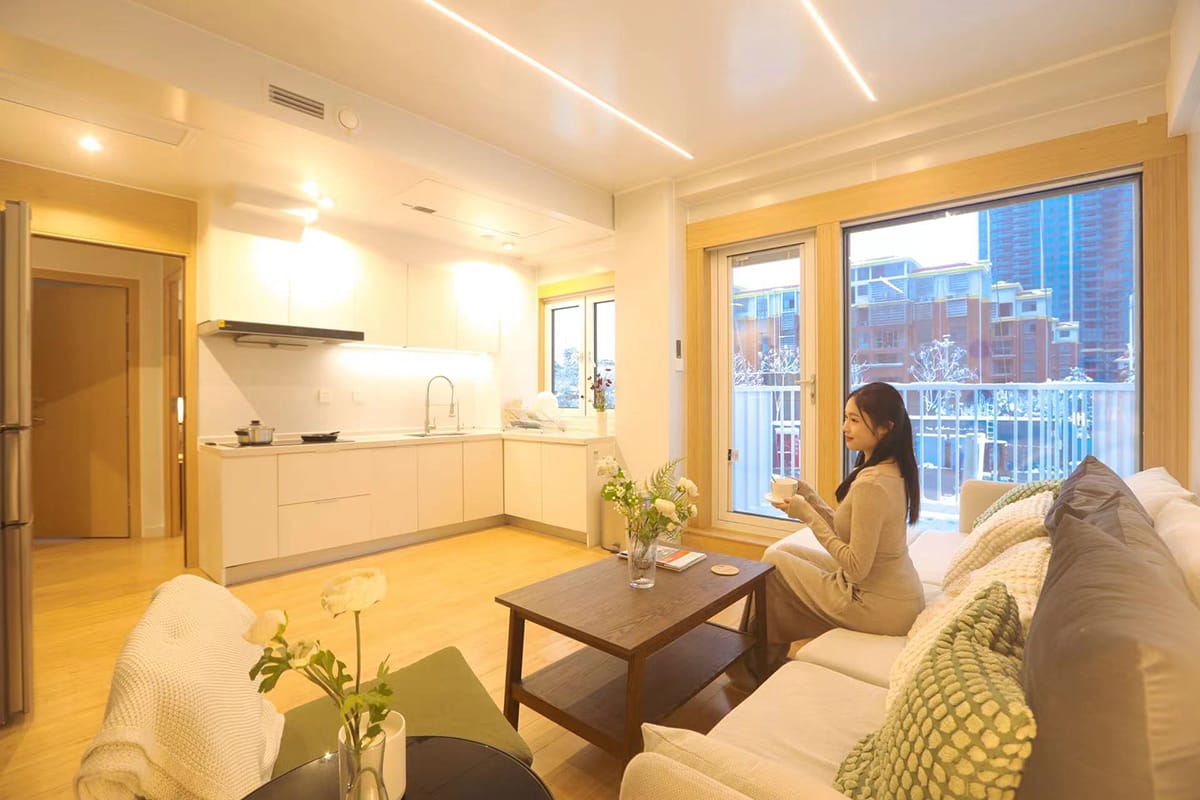
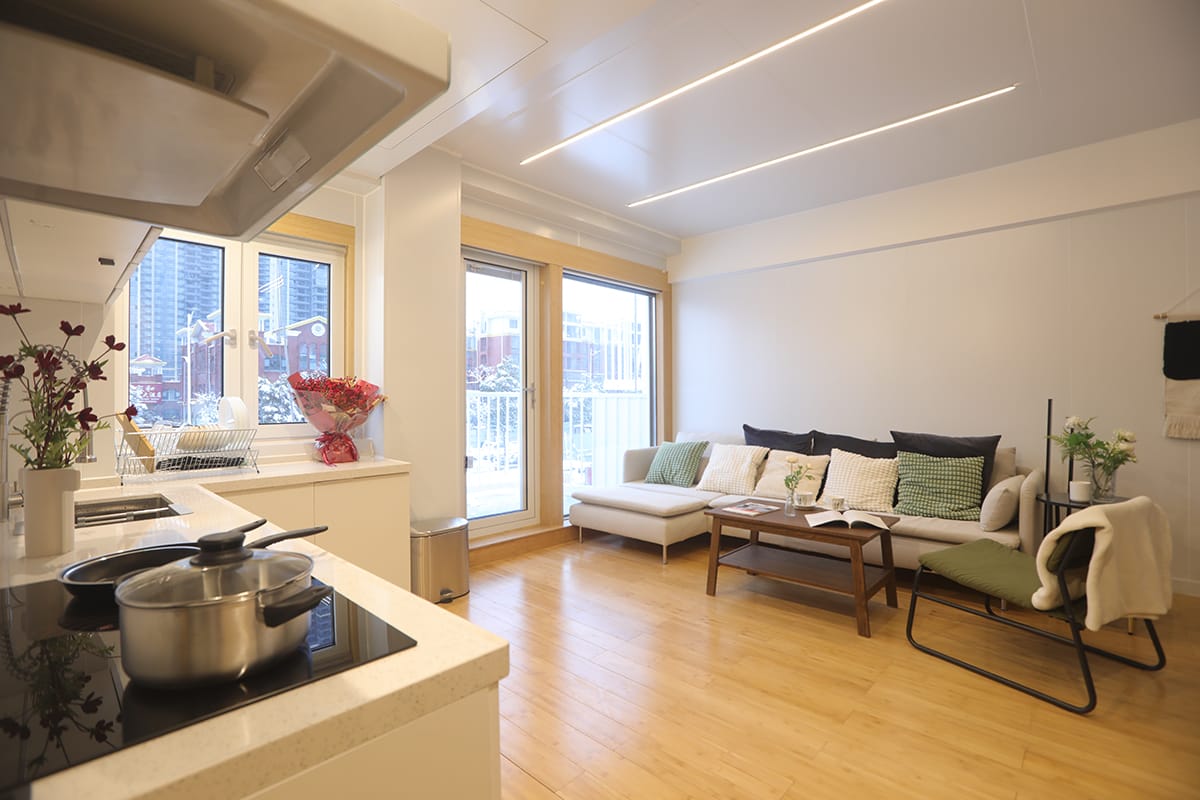
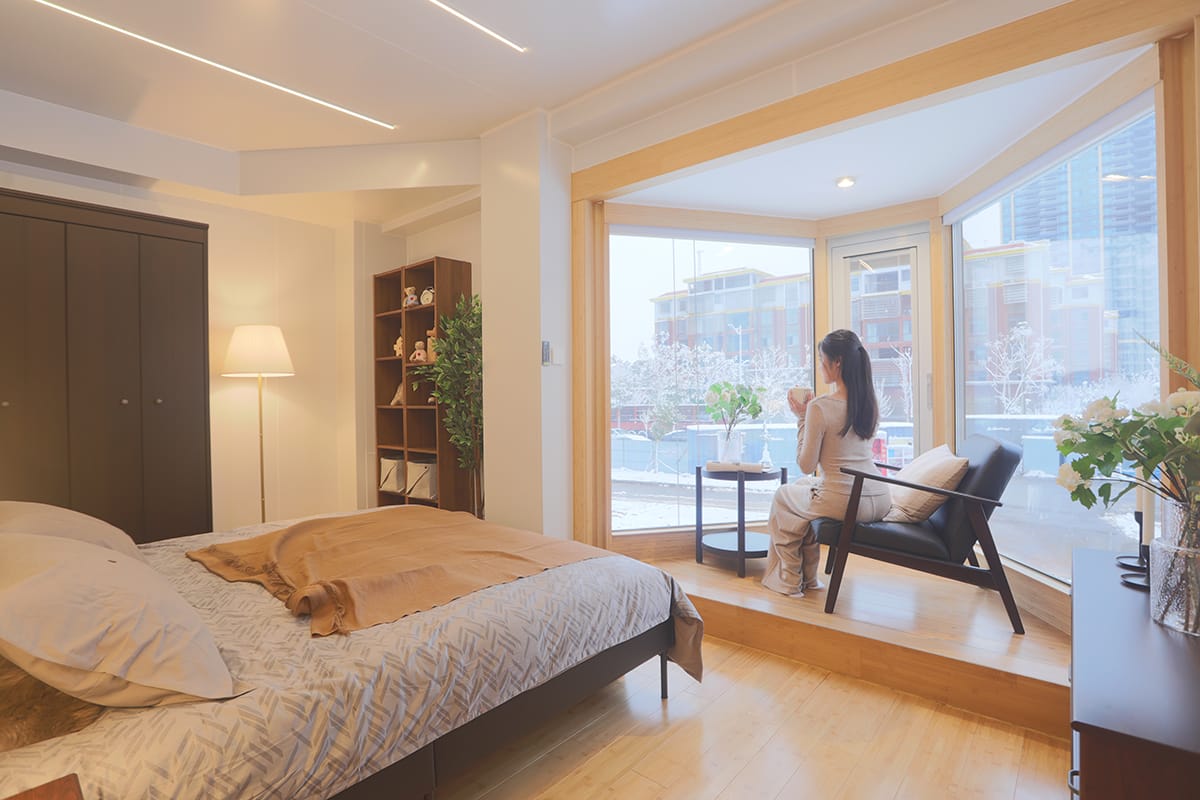
After the 5-day assembly was complete, the building was move-in ready; the only things missing were the appliances.
The Importance of B-CORE
BROAD’s patented B-CORE flooring system is the key to these efficiencies. It is a sandwich structure brazed in a special oven at 2000 degrees, which enhances the inherent mechanical properties of stainless steel. One 40x8 B-CORE "slab” can be produced every two minutes.
“The Jindu Residential Tower has 264 modules, which are all either a room module or a lift module. And because the walls in the Holon Building aren’t load-bearing, we’re able to configure the room modules flexibly. That enables us to produce a very small number of physical module types, and to crank them out at high volume. And that keeps our costs relatively low. So, even though we're using stainless—which is not the lowest cost material—we gain economy of scale through very high volume production.”
Related Reading:
B-CORE: The Modern Material from BROAD
“B-CORE is composed of two stainless steel plates with an array of stainless steel tubes fused between them,” says Sunny Wang, General Manager at BROAD USA. “Copper foil is fused to the stainless steel base material during brazing. Because the metals have different melting points, they can stick together very strongly. It looks very simple, but it’s super-light and super-strong.”
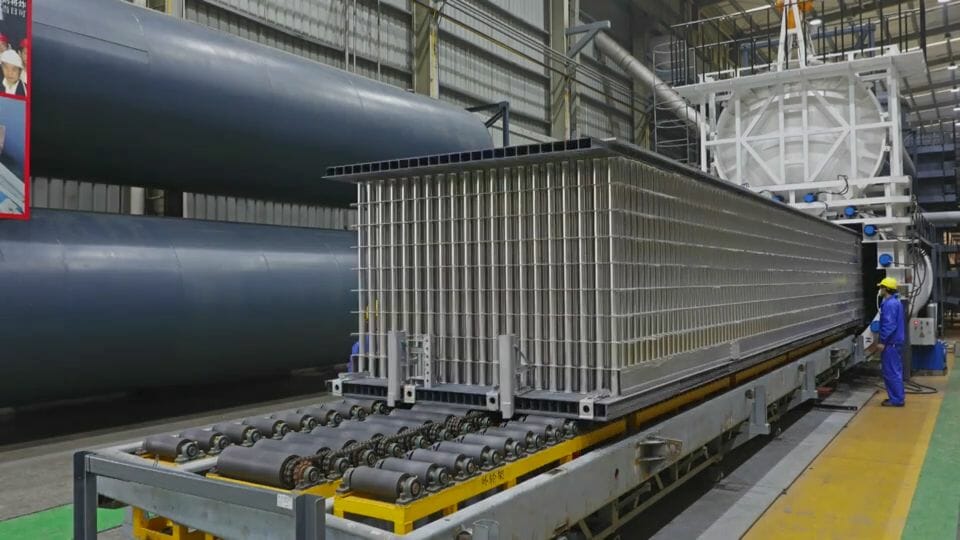
Production, Construction, and Logistics
BROAD’s latest project utilized 100 individual builders working alternating shifts, plus one mobile crane and one tower crane. But despite the constant onsite activity, BROAD’s Holon builds go up quickly and smoothly thanks to the predictable, standardized nature of the building’s components and the efficiency of their production.
“For this project,” said Zimman, “the logistics were relatively simple because the building is going up not far from our factory. But wherever we build, we can utilize a standard flatbed truck. We designed the modules to the size of a standard 40-foot-long shipping container for easy global transport, maritime and on land. So, we can go across any jurisdiction in the US, for instance, on a flatbed.
“Another critical factor in our logistics is the capacity of our factories. We’ve streamlined our production to the point where we can easily produce each module in 21 minutes.”
BROAD livestreamed the building's complete onsite assembly on YouTube.
Looking Ahead
Twenty-six stories may seem like a lot for a modular building, but the plan, eventually, is to go much higher. “There is actually no limitation for the height,” says Sunny Wang, President of BROAD USA, “because we take advantage of the stainless steel. It's strong enough that we can go as high as we can design it.”
With the proverbial wind at its back, it’s only a matter of time before BROAD’s Holon buildings are seen far and wide. And besides their upcoming projects in China, the Philippines, and the UAE, plans are also in place for Holon Buildings in the Unites States.
“The Holon modular system enables the construction of tall residential buildings at great speed, and we look forward to deploying this technology to shorten the construction cycle and alleviate the severe housing shortage in the U.S. and Canada,” concluded Zimman. “Right now, we’ve got plans in place for Ohio, Texas, and California. As soon as we can say more, we absolutely will.”
About the Author: John McMullen, PCM, is the marketing director for the Modular Building Institute. You can reach him directly at mcmullen@modular.org or on LinkedIn.
More from Modular Advantage
Behind the Design of Bethany Senior Terraces, NYC’s First Modular Passive House Senior Housing Project
As more developers seek to meet new regulations for energy efficiency, the team at Murray Engineering has set a new record. With the Bethany Senior Terraces project, Murray Engineering has helped to develop NYC’s first modular structure that fully encompasses passive house principles — introducing a new era of energy efficiency in the energy-conscious city that never sleeps.
How LAMOD is Using Modular to Address Inefficiency, Sustainability, and the Future of Construction
As developers, designers, and contractors seek to understand the evolving needs of the modular industry, no one is as well-versed in the benefits of going modular as Mārcis Kreičmanis. As the co-founder and CBDO of LAMOD in Riga, Latvia, Mārcis has made it his ultimate goal to address the inefficiencies of traditional construction.
From Furniture Builder to ‘Activist Architect’: Stuart Emmons’ Unique Journey
Stuart Emmons was fascinated by buildings at a young age. He remembers building sand cities with his brother during trips to the Jersey shore. His father gave him his first drawing table at the age of ten. Today, he is an experienced architect who received his FAIA in June 2025. The road he took is unique, to say the least.
Forge Craft Architecture + Design: Codes, Contracts, and Intellectual Property
Founding Principal and Director of Modular Practice for Forge Craft Architecture + Design, Rommel Sulit, discusses the implications of codes, contracts, and intellectual property on
modular construction.
Eisa Lee, the “Bilingual” Architect
Now as the founder of XL
Architecture and Modular Design in Ontario, Canada, she applies not just her education as a traditional architect but an entire holistic view on modular design. It’s this expansive view that guides her work on being a true partner that bridges the gap between architects and modular factories as they collaborate on the design process.
Tamarack Grove Engineering: Designing for the Modular Sector
The role of a structural engineer is crucial to the success of a modular project, from initial analysis to construction administration. Tamarack Grove offers structural engineering services — project analysis, plan creation, design creation, and construction administration — for commercial, manufacturing, facilities, public services, and modular. Modular is only one market sector the company serves but it is an increasingly popular one.
Engineer Masters the Art of Listening to His Customers
Since founding Modular Structural Consultants, LLC. in 2014, Yurianto has established a steady following of modular and container-based construction clients, primarily manufacturers. His services often include providing engineering calculations, reviewing drawings, and engineering certification
Inside College Road: Engineering the Modules of One of the World’s Tallest Modular Buildings
College Road is a groundbreaking modular residential development in East Croydon, South London by offsite developer and contractor, Tide, its modular company Vision Volumetric (VV), and engineered by MJH Structural Engineers.
Design for Flow: The Overlooked Power of DfMA in Modular Construction
Unlocking higher throughput, lower costs, and fewer redesigns by aligning Lean production flow with design for manufacturing and assembly.
Choosing the Right Ramp
Modular construction offers a compelling alternative to traditional methods for designing and building ADA and IBC-compliant entrances. By addressing the challenges of traditional construction, such as time-consuming processes, unavailable specialized labor, and variable field conditions, modular solutions provide a more efficient, cost-effective, and reliable approach.