PROMET: Providing Award-Winning Workforce Housing in Chile & Beyond
South America is a mining powerhouse, producing a substantial amount of the world’s silver, copper, tin, zinc, lithium, and nickel, and the mining industry requires a substantial amount of infrastructure to operate. That infrastructure includes workforce housing and office space that modular builders such as PROMET provide.
PROMET is a family business based in Chile that has been in operation for more than 30 years. With a strong background serving the mining industry, PROMET also has a branch operating in the hotel industry, and another branch operating in Peru.
Providing A Variety of Services
According to Cristobal Schneider, CEO at PROMET, “Our typical clients are part of the mining industry, either mining companies or mining contractors. In addition, companies in the industrial and energy sectors use our services, due to our standards in terms of safety, food, and recreation areas, among others.”
As part of that commitment to managing work-focused hotels and camps, the company provides a variety of services. Those include hotel management, security, food service, cleaning, laundry service, periodic sanitation, and auxiliary rooms, among other things.
“We have built camps for more than 3,000 people, along with the auxiliary buildings necessary for their operation,” Schneider said. “In parallel, we can also build cafeterias, support buildings, offices and control rooms, among other facilities, all of which are modularized.”
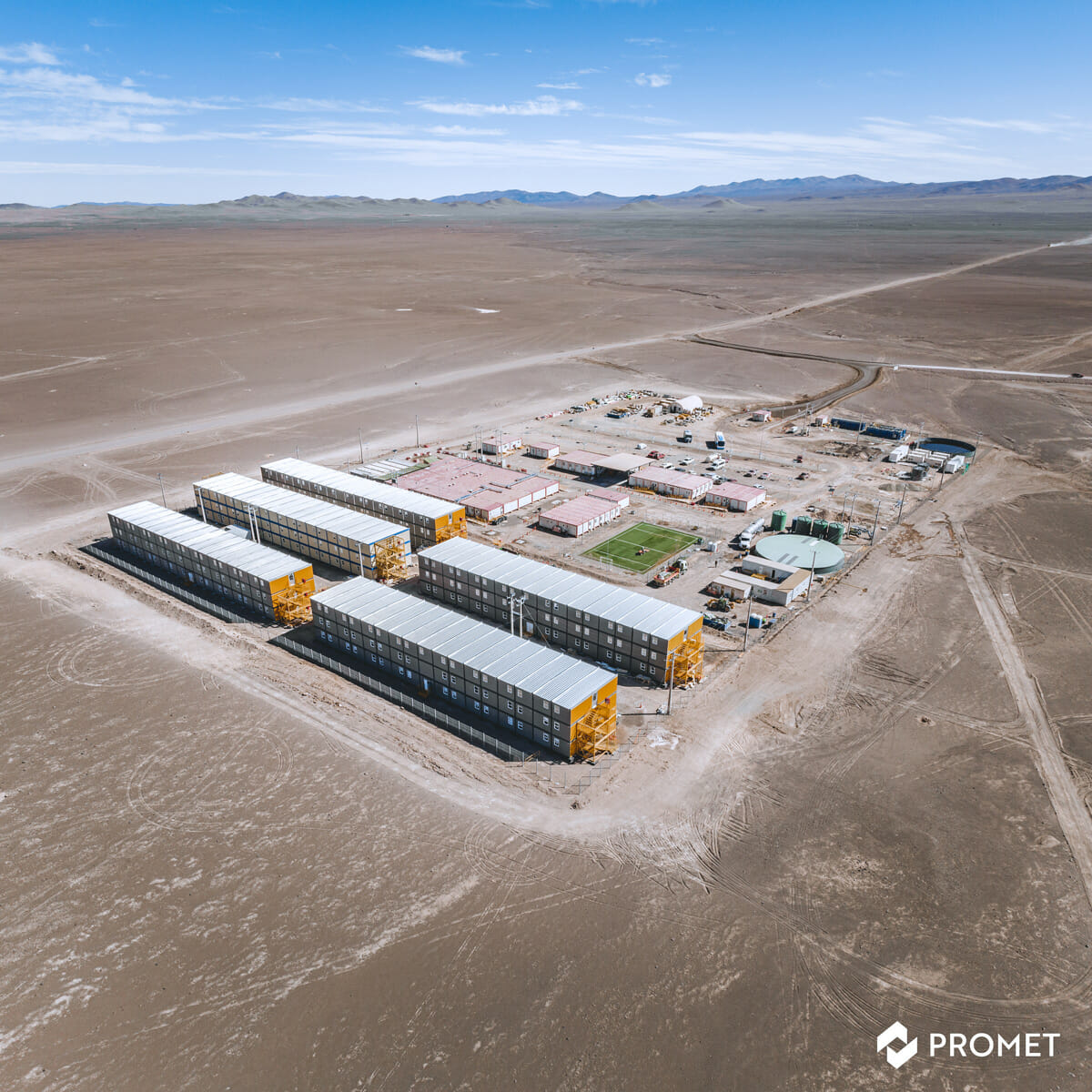
PROMET’s Campamento Parque Eólico Horizonte Colbún (Horizonte Colbún Wind Farm Camp) won first place for Relocatable Modular Workforce Housing Over 10,000 Sq. Ft. in MBI’s 2023 Awards of Distinction. See the complete case study.
A Recent MBI Award Winner
One of PROMET’s recent projects was the camp for the Horizonte de Colbún wind farm. That project won first place for Relocatable Buildings over 10,000 square feet in MBI’s 2023 Awards of Distinction. The wind farm is located 105 miles southeast of the city Antofagasta, which is north of Santiago on the Pacific coast. The project took 426 days to complete and totals 141,000 square feet.
This was a typical project for Promet, Schneider said. Early coordination with the client, though, was beneficial for the company and was atypical. “We were able to get into the engineering and design process with the customer earlier,” Schneider said, “which made for a successful project in the manufacturing and assembly process.”
“The biggest challenge was building in the middle of the desert,” Schneider said, “without any type of services readily available. We had to generate a small service station in the middle of nowhere.”
For this project, PROMET designed, built, delivered, and installed 19 buildings. Five of those are dormitories made up of 280 modules and the rest, 150 modules, are for auxiliary services such as a water treatment plant, potable water, and electrical power generation.
The housing units provide room for one, two, or three people, and all of them include a private bathroom and basic amenities such as electricity, drinking water, and sanitation services. They also have internet service in the rooms and common areas, and air conditioning.
PROMET made use of prefabricated concrete foundations for the wind farm project. This technique minimized onsite construction work, Schneider said, saving time and money onsite. “The precast foundations we use at PROMET were produced in specialized workshops using ready-mix concrete and
modular formwork techniques. These foundations are designed for versatility and adaptability, making them suitable for a wide range of modular construction projects. Although their design can be adjusted to meet specific project requirements, their use provides significant advantages in terms of efficiency and speed of installation, especially on stable and well-prepared ground. Their high strength and reliability make them a reliable choice for various types of projects, ensuring a solid foundation for our modular buildings.”
The modules themselves were constructed in PROMET’s manufacturing facility in Santiago, then transported to the job site. Prior to setting the modules, the crew set up in the towns of Taltal and Agua Verde, which are approximately 30 miles from the construction zone. They then proceeded with sitework for the installation of drinking water, sewage, and electricity. Next came the installation of the prefabricated concrete foundations for the different buildings.
With that work done, the modules were delivered via truck and installed. The dormitory buildings can house 1,200 people and the auxiliary buildings handle the reception, administration, kitchen, dining rooms, utility functions, and game rooms.
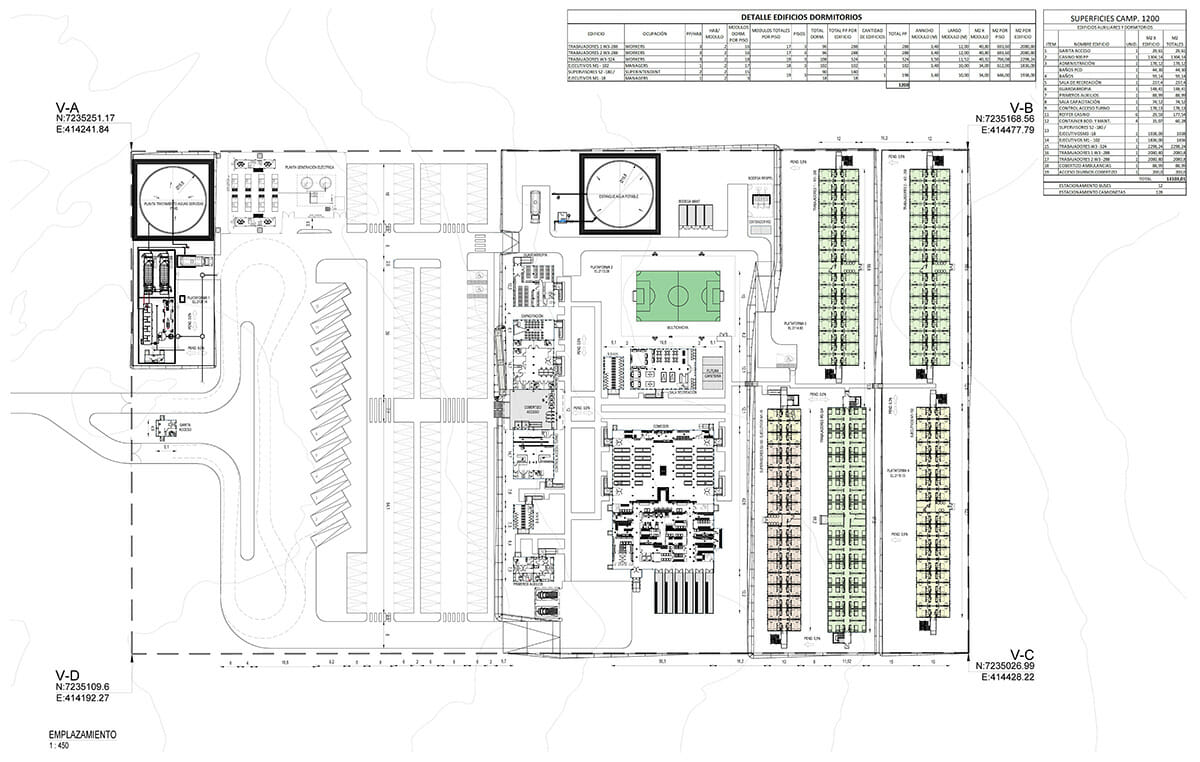
Not Wasting A Drop
Chile’s Atacama Desert is one of the most arid regions on earth, and water is a precious resource. With that in mind, the Horizonte de Colbún wind farm includes a wastewater treatment system that purifies the water until it is suitable for irrigation. “In this sense, all the water consumed at the camp can be reused, either for dampening roads or for community use,” Schneider said. “This is relevant considering that this is an extremely arid context, which makes water a very precious commodity.”
Electrical needs for the camp are handled by a variety of systems, Schneider said. “An electrical power generation yard was developed for the entire camp, as opposed to previous projects in which there were several generators feeding individual isolated sectors. For this project, a study was conducted, and the decision was made to use larger and more powerful generators, saving energy and reducing fuel consumption. Other renewable energy systems were also incorporated, such as solar energy panels for parking lot lighting and automatic on/off sensors for lighting in certain areas.”
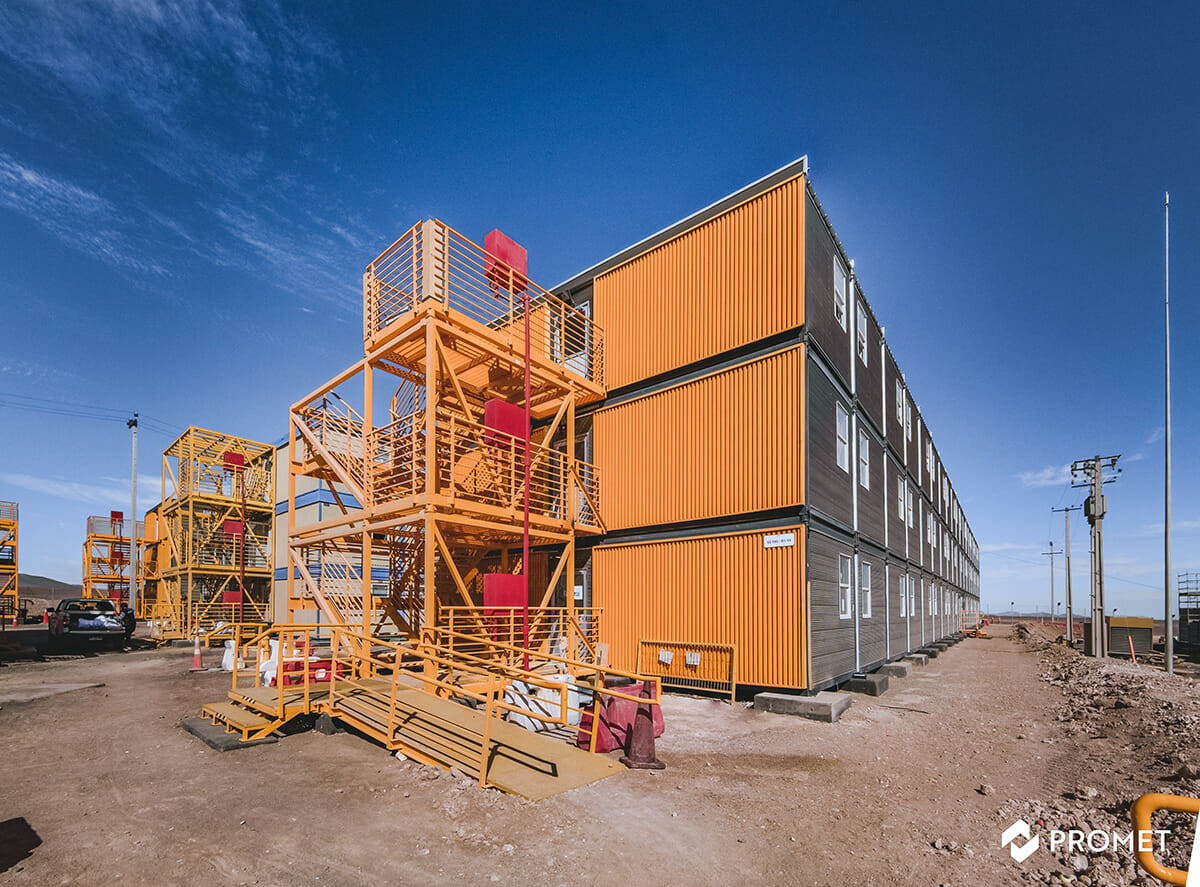
Modular Growth In Chile
As in North America, a variety of factors are challenging builders to keep up with demand in Chile, Schneider said. In addition, the modular industry has grown significantly in recent years. “The new challenges that are across industry, such as climate, regulations, lack of skilled labor, related costs and the constant search for time and cost efficiency have accelerated the incorporation of new ways of building,” she said. “This phenomenon has been developing particularly in Chile in recent years, driven mainly by regulatory issues, the current housing shortage, climatic conditions, logistical difficulties and accessibility of some projects and high labor costs,” she said. All those variables have significantly accentuated the problems of the construction industry and undoubtedly will continue to be concerns in years ahead, she added.
Looking Ahead
As in North America, Schneider said modular construction is becoming more attractive as a cost-effective alternative in different projects today. “For most it’s a technical/financial evaluation initially,” she said. “The current housing shortage in the region, which is growing year by year, coupled with the constant and intensive technical/regulatory requirements that exist today in South America—more markedly in countries such as Brazil, Chile, Colombia and Peru—are trends that have been growing and incorporated year by year in other regional countries’ agendas lead us to believe that this type of construction system is a real need and will be fundamental to achieving crucial industry requirements.”
Preparing for the Future
Schneider said PROMET sees robust growth and opportunities, along with some challenging market conditions ahead. “Our initial focus is on the area of engineering at the height of its needs,” Schneider said, “capable of solving diverse and multiple types of projects, thus becoming real partners with our clients while focusing on efficiency and technology in our production plant, which must be in line with those needs and respond to the demands of the market.”
About the Author: Steve Hansen is a Colorado-based writer with a focus on the built environment—architecture, construction, renewable energy, and transportation. He can be reached on LinkedIn.
More from Modular Advantage
Behind the Design of Bethany Senior Terraces, NYC’s First Modular Passive House Senior Housing Project
As more developers seek to meet new regulations for energy efficiency, the team at Murray Engineering has set a new record. With the Bethany Senior Terraces project, Murray Engineering has helped to develop NYC’s first modular structure that fully encompasses passive house principles — introducing a new era of energy efficiency in the energy-conscious city that never sleeps.
How LAMOD is Using Modular to Address Inefficiency, Sustainability, and the Future of Construction
As developers, designers, and contractors seek to understand the evolving needs of the modular industry, no one is as well-versed in the benefits of going modular as Mārcis Kreičmanis. As the co-founder and CBDO of LAMOD in Riga, Latvia, Mārcis has made it his ultimate goal to address the inefficiencies of traditional construction.
From Furniture Builder to ‘Activist Architect’: Stuart Emmons’ Unique Journey
Stuart Emmons was fascinated by buildings at a young age. He remembers building sand cities with his brother during trips to the Jersey shore. His father gave him his first drawing table at the age of ten. Today, he is an experienced architect who received his FAIA in June 2025. The road he took is unique, to say the least.
Forge Craft Architecture + Design: Codes, Contracts, and Intellectual Property
Founding Principal and Director of Modular Practice for Forge Craft Architecture + Design, Rommel Sulit, discusses the implications of codes, contracts, and intellectual property on
modular construction.
Eisa Lee, the “Bilingual” Architect
Now as the founder of XL
Architecture and Modular Design in Ontario, Canada, she applies not just her education as a traditional architect but an entire holistic view on modular design. It’s this expansive view that guides her work on being a true partner that bridges the gap between architects and modular factories as they collaborate on the design process.
Tamarack Grove Engineering: Designing for the Modular Sector
The role of a structural engineer is crucial to the success of a modular project, from initial analysis to construction administration. Tamarack Grove offers structural engineering services — project analysis, plan creation, design creation, and construction administration — for commercial, manufacturing, facilities, public services, and modular. Modular is only one market sector the company serves but it is an increasingly popular one.
Engineer Masters the Art of Listening to His Customers
Since founding Modular Structural Consultants, LLC. in 2014, Yurianto has established a steady following of modular and container-based construction clients, primarily manufacturers. His services often include providing engineering calculations, reviewing drawings, and engineering certification
Inside College Road: Engineering the Modules of One of the World’s Tallest Modular Buildings
College Road is a groundbreaking modular residential development in East Croydon, South London by offsite developer and contractor, Tide, its modular company Vision Volumetric (VV), and engineered by MJH Structural Engineers.
Design for Flow: The Overlooked Power of DfMA in Modular Construction
Unlocking higher throughput, lower costs, and fewer redesigns by aligning Lean production flow with design for manufacturing and assembly.
Choosing the Right Ramp
Modular construction offers a compelling alternative to traditional methods for designing and building ADA and IBC-compliant entrances. By addressing the challenges of traditional construction, such as time-consuming processes, unavailable specialized labor, and variable field conditions, modular solutions provide a more efficient, cost-effective, and reliable approach.