Turkish Manufacturer Has Long History of Responding to Disasters
On February 6, 2023, a 7.8 magnitude earthquake rocked southern and central Turkey, killing over 2,300 people and injuring 10,000 more. In the immediate aftermath, one company stepped up to provide temporary housing for those affected by the damage - DORCE Prefabricated Building and Construction. The company is currently producing 320 modular units a day for the continuing relief effort, and, even six months later, those units are going to the victims in the form of permanent housing.
DORCE responded with the force of its huge production capacity, dedicating all their abilities to producing emergency houses for those displaced by the disaster with help from AFAD (Disaster and Emergency Management Presidency of Turkish Republic). They also sent equipment such as excavators and cranes to help with search and rescue efforts, redirected their construction teams to the area, and provided winter clothing such as coats, boots, and sweaters. Thanks to the company’s administrative staff, workers, subcontractors, subcontractor workers, and material suppliers they were able to respond at this critical time.
Their current modular unit is 21 square meters and includes a living room, bedroom, kitchen, and toilet/shower area. The specialized construction of the base and roof contributes to the strength of the unit. Trapezoidal sheet metal protects the inside from outdoor conditions, while the base keeps the unit stable on the ground. Units used for temporary housing can be dismantled and shipped to other locations to provide housing for other projects.
Not only are the modular units strong, but they’re green as well. They are designed to be energy efficient, and since they are made of non-combustible materials, they’re fire resistant too. Units are transported by land, rail, or by air, and are designed to be “plug and play” with the site utilities (currently supplied by AFAD). Unit construction includes the electrical, telecommunications, plumbing, and heating/cooling systems. They can be assembled in 24 hours after arrival at the assembly yard.
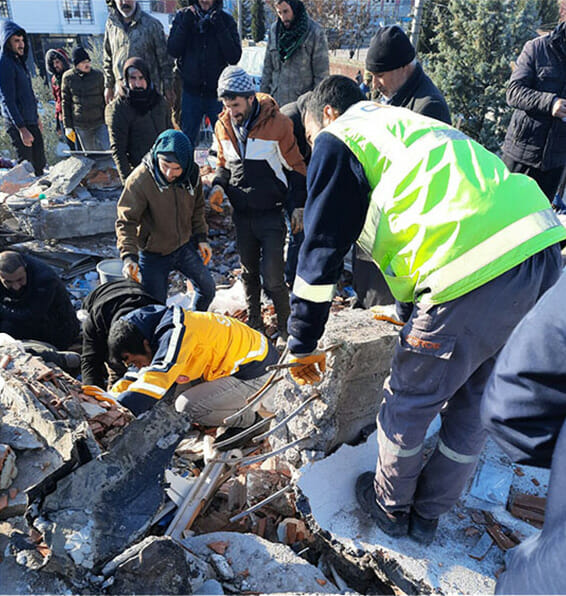
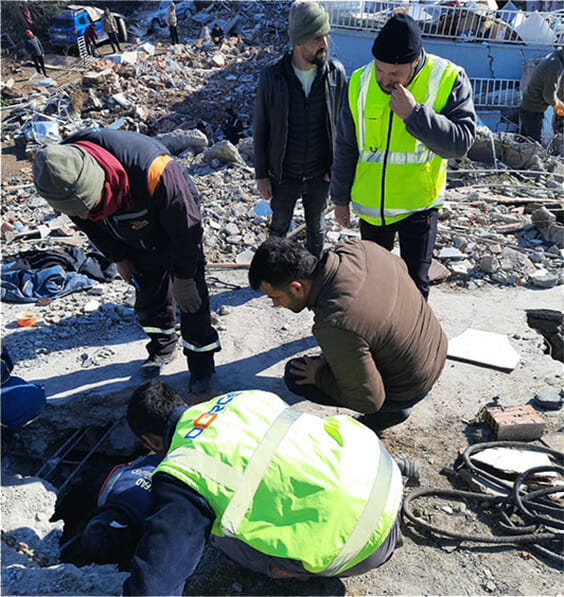
A History of Responding to Emergencies
Looking over the company’s history, this kind of response is the norm, rather than the exception. DORCE has a rich history of responding to disasters in the area, almost from its inception in the early 1980s. Due to its proximity to one of the most active earthquake zones in the world, they have invested a lot of time into the design and production of earthquake- resistant modular structures.
Geldimurat Annageldiyev, who has worked for DORCE since 2003 and is their current Deputy General Manager responsible for Global Business Development, says the company’s first involvement in earthquake relief missions came in 1999 when a 7.6 magnitude quake hit the city of İzmit, Kocaeli Province of Turkey. In three months, the company manufactured modular housing for 20,000 people.
Then in 2003, they responded to a quake in the city of Bam, Iran, providing temporary emergency accommodation units that were later transferred to different regions of the country to be used as dormitory housing for students.
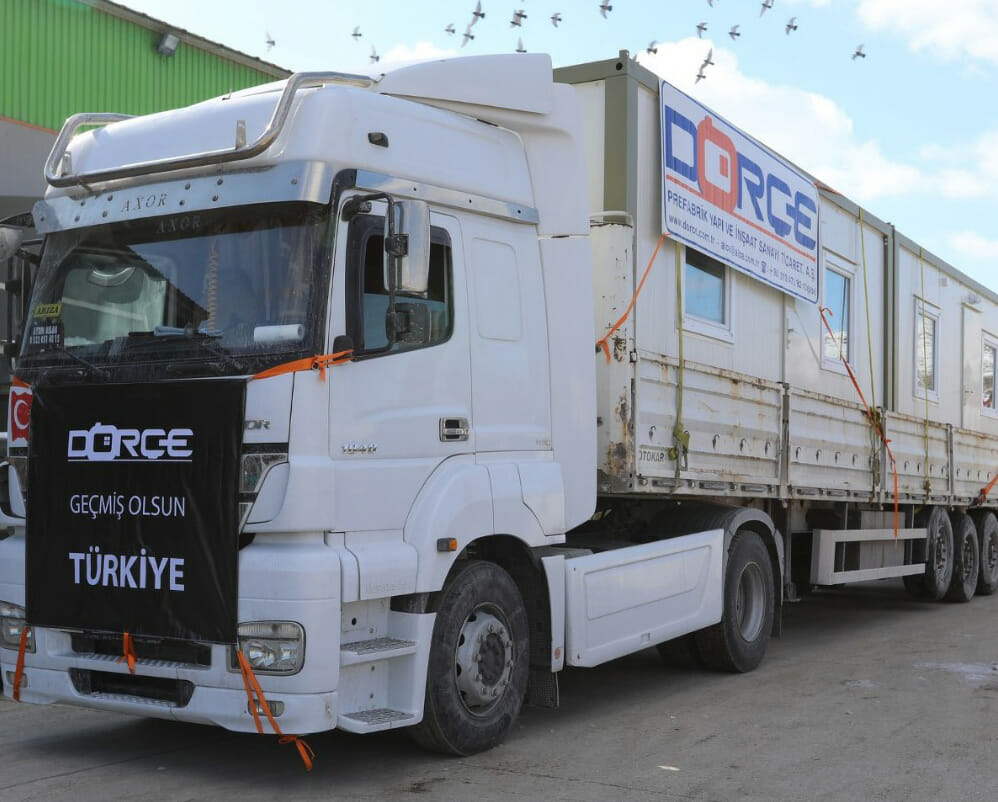
In 2011, 3,000 modules were provided over a 45-day period to house more victims in Ercis and Van, Turkey.
The 2023 earthquake affected some of the most densely populated cities in the country: Hatay, Adıyaman, Kahramanmaraş and Malatya. The most affected people were those living in substandard housing in informal settlements. It also greatly affected several industries in the country, including textiles, automotive, technology, manufacturing, and construction.
The Turkish government recently announced a new housing development program to help those affected by this year’s event. It involves the construction of 650,000 new homes in the next five years in the affected areas. All homes will be built to the highest earthquake safety standards and will be located in safer areas of each city.
The company has gained a reputation for providing a quick response with a large volume of modular structures to accommodate and house people,
either temporarily or permanently. With units specially designed for easy transportation and assembly, they are being looked to as a resource for emergency responses around the world.
International From the Start
DORCE started out as a manufacturer of minor steel construction materials like chairs, doors, windows, and furniture. Within about two years they had expanded to light gauge steel and container buildings, modular units, and pre-engineered heavy steel structures. Throughout its history, its performed projects in over 60 countries, all from its 100,000 square meter manufacturing hub in Ankara, Turkey. The facility is one of the largest active manufacturing plants in the world and has been pumping out 180,000 square meters of prefabricated buildings or 5,000 modular units per month for decades without a slowdown.
The speed with which they are able to produce these units is thanks to the use of modern construction technology, including building information modeling (BIM), Modern Methods of Construction (MMC), Design for Manufacturing and Assembly (DFMA), and Designing for Industrialized Methods of Construction (DIMC). In particular, they rely on BIM to increase the efficiency of the construction process, reduce waste, and to improve the quality and lifespan of the structures.
Their goal has always been to expand internationally, and they’ve done that in a unique way. “As the first step to being successful in international markets, we learned to appreciate and respect the culture and attitude of the countries where we work. Through time, we truly understood the nuances of different cultures, hiring people from around the globe. Today we proudly say that more than 20 nationalities are working in DORCE globally,” says Annageldiyev.
With the growing popularity of modular construction, both in Turkey and other countries, DORCE’s services are in demand, and they are looking to expand their operations accordingly. They already have a history of working with many US and Canadian companies and the military, including the US Army, and NATO in Iraq, Afghanistan, Qatar, and Somalia. They’ve also provided housing for mining companies, modular embassy structures for the US government, and a mass housing project for different US-based companies.
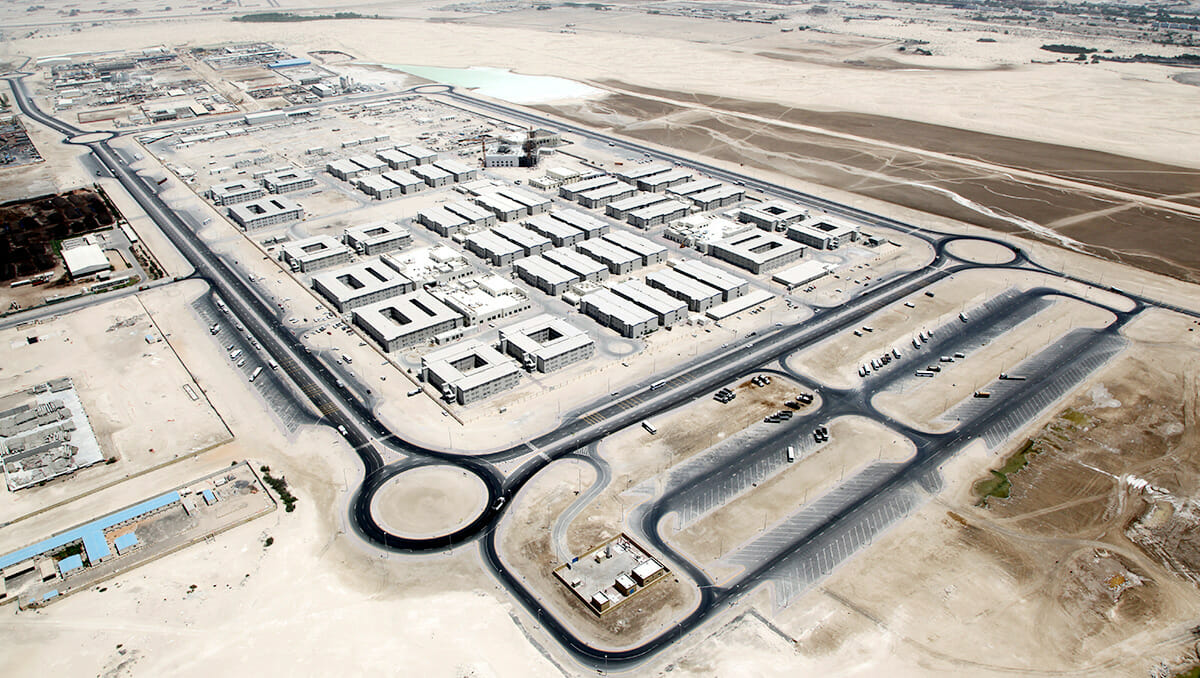
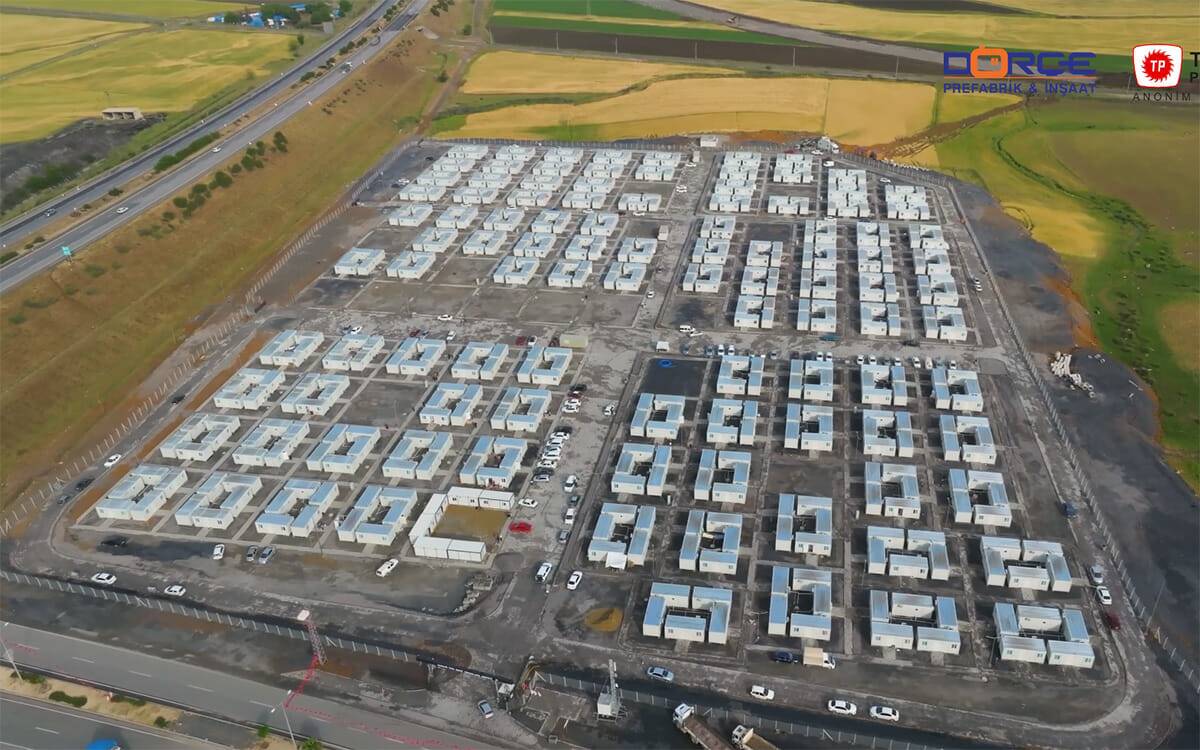
Emergency housing communities manufactured by DORCE
To cement their place in the American market, they’re looking to produce a high-rise volumetric project in the next 5-10 years.
Annageldiyev believes the timing is right, citing increased housing demand in urban areas, the rising cost of traditional construction methods, favorable government policies, a focus on safety and quality, and the rising demand for sustainable volumetric modular buildings. He also sees a great opportunity providing both temporary and permanent housing for the homeless.
Their focus, understandably, is on providing modular production for earthquake prone areas, like California. Their experiences working with these disasters in their own country have them poised to provide a great deal of insight to the US market. They’ve already invested heavily, with plans to open manufacturing facilities in the US and Canada and create partnerships with companies there.
About the Author: Dawn Killough is a freelance construction writer with over 25 years of experience working with construction companies, subcontractors and general contractors. Her published work can be found at dkilloughwriter.com.
More from Modular Advantage
Celebrating the Winners of MBI’s 2025 Awards of Distinction
MBI’s Awards of Distinction are presented annually, traditionally on the final evening of its North American World of Modular conference and tradeshow. This year’s Awards were presented in a variety of categories, including several each for permanent modular construction projects and relocatable buildings. Excellence in “green” modular construction and marketing were also recognized.
MBI Welcomes R.I. Group Founder & President Salvatore Tafuro to the Industry’s Hall of Fame
In 1973, Salvatore Tafuro, only in his twenties and already supporting a family of three children, set out to realize his entrepreneurial dream. From a humble garage in Leverano, in the heart of Salento, he began producing metal structures and aluminum fixtures for the construction industry.
The Best-Kept Secret in Housing
What can we do to right the ship, overcome these circumstances, capitalize on the opportunity, and address this epidemic in the housing sector? It’s easier than you might think.
The Blueprint for Accountability: How Mastery, Autonomy, and Purpose Drive Performance in Construction & Manufacturing
Accountability is one of the most critical elements of a thriving organization, yet many leaders in the construction and manufacturing industries struggle to create a culture where it truly thrives. High-performance teams require more than just technical skills and efficiency—they need strong accountability, alignment with the company’s vision, and a deep sense of ownership.
AI, Faster Sets, and Automation: The Future of Modular is at World of Modular
While the modular building industry has long known that it can be an effective solution to increase affordable housing, the word is slowly spreading to more mainstream audiences. Three presentations at this year’s World of Modular in Las Vegas hope to provide insight and direction for those seeking a real solution to the crisis.
An Insider’s Guide to the 2025 World of Modular
The Modular Building Institute is bringing its global World of Modular (WOM) event back to Las Vegas, and with it comes some of the industry’s best opportunities for networking, business development, and education. Over the course of the conference’s four days, there will be numerous opportunities for attendees to connect, learn, and leverage event resources to get the most out of the conference.
Affordable Housing Now: The Industry’s Best Bring New Solutions to World of Modular
While the modular building industry has long known that it can be an effective solution to increase affordable housing, the word is slowly spreading to more mainstream audiences. Three presentations at this year’s World of Modular in Las Vegas hope to provide insight and direction for those seeking a real solution to the crisis.
Opportunities for Innovation in Modular Offsite Construction
Modular Offsite Construction has already shattered the myth that it only produces uninspired, box-like designs. Architectural innovations in module geometry, configurations, materials, and products make it possible to create visually stunning buildings without sacrificing functionality or efficiency.
Safe Modular Construction with Aerofilm Air Caster Transport
In collaboration with Aerofilm Systems, Heijmans developed innovative skids using air caster technology for moving modules easily and safely. These pallets are equipped with an auto-flow system, making operation extremely simple.
Miles, Modules, and Memes: Building a Modular Network One Flight at a Time
At the end of the day, social media is just another tool for building connections, and like any other tool, needs to be used skillfully to work properly. Use social media thoughtfully, and it will open doors to real opportunities and relationships you didn’t even see coming.