What is an Air Balance? The Comfort Zone
An "air balance" is a useful process for measuring the performance of a simple or complex hvac system, and for providing the occupants with a comfortably conditioned space. To understand how this process works, let's first look at the different types of air balance by defining the two extremes: Comfort Balance and AABC Certified Air Balance.
A "comfort balance" is simply checking to see whether the room feels comfortably conditioned. It may be as easy as walking from room to room, holding a hand up to the ceiling to see if sufficient air is coming out of the registers, and asking the occupants if they are comfortable. If they are not, your journey starts to discover how to resolve the HVAC problems associated with the situation. It may involve adjusting/moving registers, installing restrictors/dampers after the fact, or just insuring the air doesn't blow directly on an occupant. Many occupant complaints are associated with air circulation: too much and too little.
At the other end of the spectrum is the AABC Certified Air Balance. The purpose of this type is to insure all components of the hvac (heating, ventilating, air conditioning) system are working in harmony, at their optimum performance, providing total occupant comfort. While the journey toward a certified air balance starts before the testing stage, let's begin ours with the mechanical engineer.
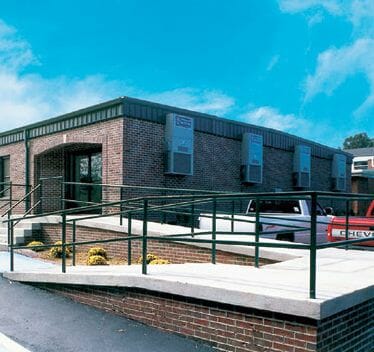
A mechanical engineer develops specifications and a set of mechanical drawings from a mix of occupant desires, local codes, ASHRAE standards, and many years of training. The correct ducting, airflow, registers, and unit performance are brought together with consideration for ventilation requirements and building exhaust needs.
The most important part of the mechanical plans used by the certified balance company is the list of "cfm" requirements next to each supply, return, intake, exhaust and ventilation opening. Without this important information a certified balance is not possible.
To conduct an AABC Certified Air Balance, the building must first be totally sealed/enclosed. Therefore this process would fall under the modular dealer's scope of work. If your project is complex, or your customer includes a certified air balance in the bid specs, be sure to include the following cost allowances on the front end:
- A mechanical engineer
- A system with products capable of a certified balance
- The cost for a balancing company
- An HVAC contractor on site during balance.
The HVAC contractor is advisable because, according to their association, a true AABC certified balance contractor must not be affiliated with any mechanical contractors, design engineers, or equipment manufacturers. So if the HVAC unit needs service during the air balance process, and an HVAC contractor is not on site, the balance will most likely stop.
A total air balance requires an opposed blade damper (OBD) behind the face of each intake and exhaust opening in each room and of the building. Other balancing dampers are required at all branch locations of the duct system.
At the building site prior to occupation, the certified balance technician will change all of the filters in the system, and insure that all dampers are fully open. Readings are taken at every opening inside, on the roof, etc. Slowly the dampers are closed in an effort to meet the cfm requirements set by the mechanical engineer. Adjusting one damper changes the cfm at all other openings. The air balance technician returns to every opening, making new adjustments and readings based on the changes from the previous one. Registers, grills, exhaust fans, and fresh air must all "balance" to meet the system performance requirements.
After the technician believes the system is all in tune, he locks down all of the dampers and other devices, so that the settings will not change. While this should keep the system "balanced," the system can be thrown out of balance by such things as dirty filters, the occupants changing the register setting, office remodeling, and reconfiguring registers and ducting.
The cost to do an AABC Certified Air Balance ranges from $75-150 per opening. You're paying for time, labor, expertise, equipment, and a Certified Balance Report. A building with five supply openings, five return openings, one exhaust fan, and one OSA intake has 12 openings to verify. Depending on the complexity and location of the openings, you can expect to pay $900-$2,000 for an AABC Certified Balance.
Is it worth it on large projects? Definitely. Remember, to avoid wasting money on your balance, be sure to install registers that the occupants cannot adjust.
Hiring a good air balance company with skillful technicians is also important. Visit www.aabchq.com for more information on the Associated Air Balance Council and a member list. The website also lists the requirements for membership, the types of certified technicians, their code of ethics, and their performance guarantee.
We have looked at the simple and the perfect air balance types, just hitting the high spots toward explaining certified air balance requirements and results. This understanding may help you avoid the temptation to put only $50 in your bid when you see your customer specifications requiring an AABC Certified Air Balance. The $50 only covers the cost of the "waving the hand" comfort balance.
More from Modular Advantage
A Huge Win for the Modular Construction Industry in Massachusetts
In early February, 2024, the Massachusetts Board of Building Regulations and Standards (BBRS) released its proposed 10th Edition building codes. This draft included several amendments targeting modular construction that would have created an extremely difficult environment for the entire modular industry and could have eliminated the industry entirely in the state.
FEMA Announces Hawaii Housing Plan Using Modular Construction
Utah becomes the second state in the country, following Virginia, to fully adopt ICC/MBI standards 1200 and 1205. MBI will continue to work with leadership in Utah to implement the new program.
Supply and Demand: Solving Canada’s Housing Crisis One Relocatable Housing Unit at a Time
Not only do Moda Modular’s repurposed employee housing solutions cut the emissions related to construction down to nearly zero, but they also keep building materials that are often not biodegradable from slowly decaying in storage facilities.
It’s the classic environmental mantra of reduce, reuse, and recycle, scaled up and applied to building after building.
ICC/MBI Standards 1200 & 1205 Provide Foundation for Utah’s First-Ever State Modular Program
Utah becomes the second state in the country, following Virginia, to fully adopt ICC/MBI standards 1200 and 1205. MBI will continue to work with leadership in Utah to implement the new program.
Repetition, Communication, and Coordination: A QSR Case Study
This modular QSR project seemed like any another modular building on the surface. Inside, it was anything but. The rhythm, the desire to iterate and repeat, and the constant communication between all parties made it stand out.
Modular Architecture: Thinking Outside of the Box with Sara.Ann Logan
At a time when modular buildings were still seen as less than by many in the architecture and construction world, Sara.Ann Logan took the plunge and partnered to launch a design-build firm that designed, built, and constructed modular high-end single-family homes. But even though she could see the value of this kind of construction, it wasn’t universally accepted.
Colorado Developer ‘Attacks’ Attainable Housing Crisis
City, county, and state government bodies are reaching out to Fading West Development, a modular manufacturer and developer in Buena Vista, CO, to learn more about how they are using modular construction to solve the affordable housing crisis in Colorado. Governments are eager to learn how they’ve made modular development successful and profitable while meeting the growing need for affordable housing.
CES Group’s Stuart Cameron Will Convince You the Moon Is Achievable with Modularized MEP
While most people think of construction as a gradually layered process, MEP assemblies—such as the modular ones—tend to provide all-in-one installs, like a car factory. A modular MEP product helps developers, architects, and fellow modular manufacturers reach their goals through early integration and planning. MEP assemblies address all the unseen things like electrical, heating, and plumbing when looking at a finalized building. The very nature of MEP assemblies are crucial to any initial prospectus.
Automation: The Future for Offsite Modular Construction
Offsite modular construction lags far behind other industries in embracing and adopting automation. Some people believe it will decrease jobs. Others feel they’ve done okay without it, so why change? In reality, conventional construction methods simply cannot keep up. Cooper Lane of Brave Control Solutions points to the labor shortage and the housing crisis that’s rampant in Canada, the U.S., and globally.
Seizing the Modular Construction Opportunity
The CSA Public Policy Centre’s new report, Seizing the Modular Construction Opportunity, highlights how innovative modular methods can help to bring various building forms—from single unit housing to complex high-rises—online more quickly. Owing to efficient manufacturing practices and controlled factory environments, modular can achieve completion rates that are 25% to 50% faster than conventional construction approaches.