Automation: The Future for Offsite Modular Construction
Making the switch to automation is a big step for offsite modular construction companies. But it’s a necessary one if they want to succeed moving forward. Brave Control Solutions Inc. specializes in building customized automated solutions for offsite modular construction. It’s been Vice President Cooper Lane’s focus for the last seven years, and he’s developed a comprehensive roadmap to automation to guide customers to the best option to fit their needs now and in the future.

Automation of framed walls and post processing including drywall installation.
You could say manufacturing is in Cooper Lane’s DNA. Lane, vice president at Brave Control Solutions, grew up in Windsor, Ontario, an “automotive hotbed” with proximity to automotive suppliers and assembly plants from Windsor to Detroit. His family owns a stamping operation that supplies the automotive industry.
Upon graduating from the University of Windsor with honors, Lane looked for a position outside of the family business and wanted to be in more a of a job shop environment. He landed at a Tool and Die shop in the London, Ontario area. Here, while serving as operations manager, he discovered his love for sales.
In 2012, Lane accepted a position as vice president of sales and engineering with a Windsor-based structural steel fabricating company.
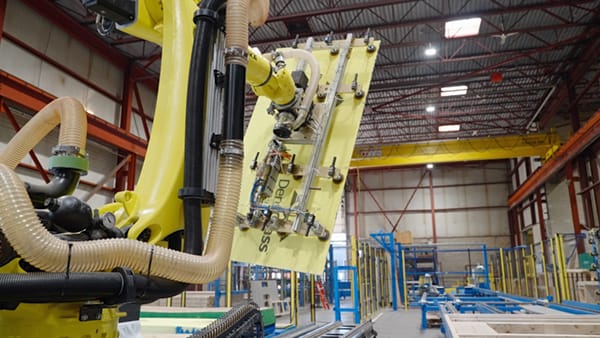
Lane’s sales efforts with the fabrication company helped diversify its client base to include aerospace, power generation, and defense work. He was first exposed to the offsite modular construction market when they were awarded a contract to build automated equipment for Z Modular. To complete the project, he partnered with Brave Control Solutions, a controls expert. It was a fortunate pairing for Lane.
When the project came to an end, Lane moved over to assume the role as Vice President of Sales with Brave Control Solutions.
Making the Move to Offsite Modular Construction
That was in July 2020 when COVID made it impossible to conduct face-to-face meetings. For the first six months, Lane and his team scheduled four to six virtual meetings per week.
“That wouldn’t have been possible if it weren’t for the acceptance of virtual meetings,” Lane said. “It was a big silver lining for us to have the reach and the impact that we did during those challenging times.”
Established in 2008, Brave designed and delivered automation solutions, primarily to the automotive industry. In 2017, it began the transition to the offsite modular construction sector, when it was approached by Z Modular. Over the last seven years, offsite modular construction has been Brave’s primary focus.
Today, Brave is a leader in customized automation for the offsite modular construction sector, which is 90% of its customer base. Now, potential customers often contact Brave to learn more about what the company can do.
"I’d like to think we’re seen as a company that’s driving more modern means of manufacturing,” Lane said. “We’re a leader in the space of custom automation, someone that brings a fresh set of eyes on how things might be able to be done better moving forward.”
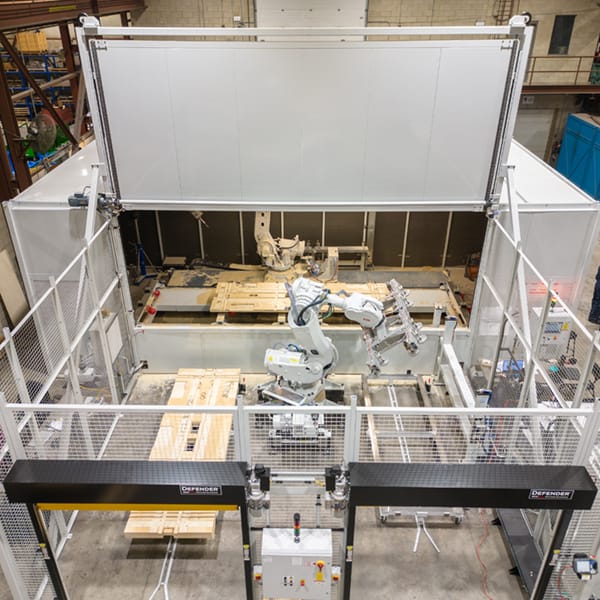
Custom CNC machining cell for mass timber for Intelligent City in Vancouver, BC.
Built-in Flexibility with CAD2FAB™
The beauty of automated equipment is the efficiency, speed, and precision with which it makes the same part repeatedly. Introducing variables to the product after the machine is built can be difficult, even impossible. “We were in our first project, and we started to realize that the amount of product variability in offsite construction doesn’t bode well with conventional automation,” Lane said. “We knew customers had to have some way to change the machine after it was delivered to their floor.”
That’s how CAD2FAB software, Brave’s invention for the offsite modular construction space, was born. CAD2FAB drives the equipment and allows the owner to reprogram it within minutes. For example, the frame sizes for offsite wall panel framing production can be customized to meet the owner’s current needs.
“CAD2FAB is built into the machines and eliminates the need for retooling, reteaching, and retouching,” Lane said. “Flexibility is now embedded in every machine we make.”
That said, Lane explained that Brave is a systems integrator and inventing new technology is not typically their repertoire. “We’re not looking to develop new technologies,” Lane said. “We’re looking at technologies being used in other industries and crossing those technologies over to offsite construction to make our customers more efficient.”
Why Automate?
“Coming into modular construction, it was a huge eyeopener for us to discover that a lot of the technology we were used to seeing on a regular basis, wasn’t present there,” Lane said.
Offsite modular construction lags far behind other industries in embracing and adopting automation. Some people believe it will decrease jobs. Others feel they’ve done okay without it, so why change? In reality, conventional construction methods simply cannot keep up. Lane points to the labor shortage and the housing crisis that’s rampant in Canada, the U.S., and globally.
“Unlike the automotive industry, there’s been no focus on using more technology to build houses better, faster, and cheaper,” Lane said. “We believe that automation can be at the heart of that.”
Although automation can’t transform a company into a “lights out” operation, with everything automated, when implemented properly, automation can increase productivity, reduce costs, and improve safety—a huge concern for construction companies.
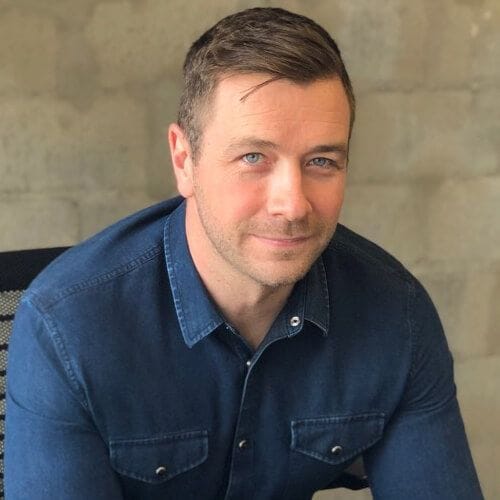
Talking Automation at the 2024 World of Modular
Cooper Lane, Vice President of Sales, Brave Control Solutions
Building a business case around automation will be the major emphasis of Cooper Lane’s presentation. It will appeal to offsite modular builders, investors, or anyone interested in bolstering productivity at their facilities.
After the session, attendees should understand what efficient automation will mean for their operation and how it can easily be justified.
“Certain aspects of offsite construction are prime for the application of automation and certain processes and applications are a better fit for a manual process,” Lane said.
The shortage of skilled labor is another reason to consider automation. Some of those jobs could be automated and an employee trained to operate the equipment. “If automation is implemented properly, it empowers employees,” Lane said. “It drives the operation so it is more successful.”
Related Listening:
Design for Automated Modular Manufacturing w/ Brave Control Solutions
In this episode of Inside Modular, Brent McPhail, founder and CEO of Brave Control Solutions, returns to discuss the current state of automation within the modular construction industry and what lies ahead as both designers and manufacturers embrace the benefits and challenges of modular automation.
The Onboarding Process and Beyond
Brave has a comprehensive process for helping potential customers understand what automation is capable of and their options. Potential customers complete an automation questionnaire to gather basic information prior to the onsite visit.
Brave starts by getting an understanding of their customer’s unique need. Most of the time a facility visit is conducted to better understand a company’s process, its pain points, local labor situation, and whether technology already exists that can improve the company’s productivity. Brave doesn’t build off-the-shelf solutions. All automation is customized to the customer’s needs, wants, budget, and situation.
“One of the biggest services we provide is a roadmap to automation,” Lane said. “If a customer has a limited budget, but wants to begin modernizing, we’ll find a solution that fits their budget to get them started.”
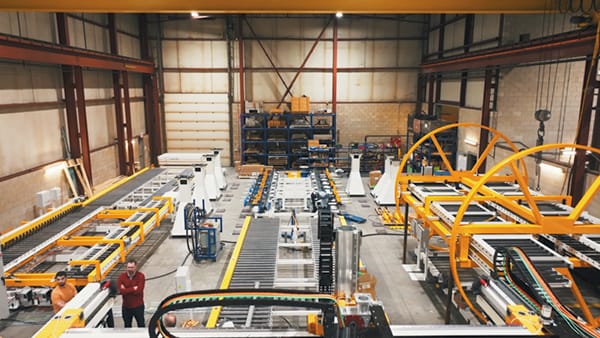
Automated panel assembly and processing cell for Boxabl in Las Vegas, Nevada.
The process is one of collaboration and partnership. “What sets us aside in this space, besides the production systems we design and build, is we offer a high standard of service,” Lane said. “And we want our customers to become accustomed to it and to expect it, moving forward.”
Brave has learned many lessons over the years, such as machine operators need to be trained and ready to go before the machines hit the floor. The company works with customers’ human resources teams to help them understand the skillsets necessary for machine operators. Once the machine is up and running, customer employees can get a head-start on training at Brave, plus continued training once the equipment is installed at their plant.
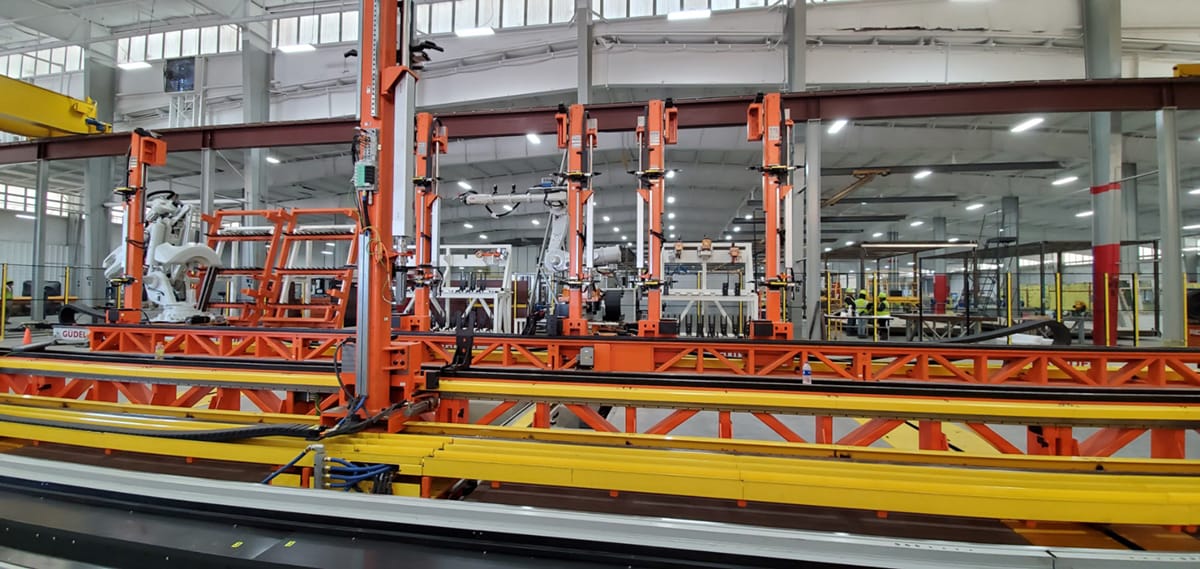
Automated steel fabrication cell for Z Modular at multiple plants across North America.
Customers are always welcome to visit during fabrication to see how their machines are built. Familiarity with that process helps them better understand maintenance issues. Brave also offers production support, both remote and onsite, to ensure the equipment runs continuously.
Brave can also provide an ROI analysis to project when the equipment will pay for itself, allowing the company to create sound business plans around their capital expenditure.
“We’ve learned a lot from the offsite construction industry. We have domain knowledge in this space that, when combined with our automotive background, will lead to game-changing solutions moving forward,” Lane said.
Lane said offsite modular construction companies need to realize that once automation is introduced, it’s not going to be “business as usual.” Change will be necessary for it to be successful. They also need to ensure that whomever they turn to for automated equipment, it will be a partner that helps them understand how to run the machines efficiently.
Brave has several large projects currently underway. The company has, to date, finished multiple retrofits on wall panel and truss machines for building component manufacturers across North America. They have a panel assembly and machining cell on the go for Boxabl, an ADU manufacturer based in Las Vegas, Nev. Also on the books, is building floor, ceiling, and wall automation equipment for a Canadian volumetric modular construction company and working with a mass timber company on the West Coast of Canada.
About the Author: Shari Held is an Indianapolis-based freelance writer who has been covering the construction industry for more than 20 years.
More from Modular Advantage
DORÇE Navigates Mountainous Terrain, Extreme Weather to Help Rebuild Türkiye
The February 6 earthquakes in 2023 were enormous. In response, DORÇE moved quickly, obtaining a government bid to help create housing and multipurpose structures—both temporary and permanent—for earthquake victims and laborers hired for reconstruction efforts.
Modern Desert Oasis: Building Reset Hotel the Modular Way
While the off-site construction part of the Reset Hotel project has been carefully controlled and with every necessity close at hand at BECC Modular’s factory in Ontario, Canada, the remote location of the project site has created additional challenges for the on site portion of the build.
Revisiting Yellowstone Canyon Village—a Groundbreaking Modular Construction Feat—Ten Years On
With such a short building period due to impending cold, it made the most sense for park developer Xanterra to pursue modular. Yellowstone’s high visitor traffic also required some odd transportation scheduling, as traffic from the West Yellowstone entrance determined the times when trucks could unload modules. Guerdon was up to the challenge.
Built for Brutal Cold, This Modular Office Building Shines
Houlton, the county seat of Aroostook County, Maine, is a small town with a population of about 6,000 residents. Situated along the border between the U.S. and Canada, what the town is most known for is bitterly cold winters. When the U.S. Border Patrol needed new office space, a modular building approach from Modular Genius offered the perfect solution.
Panel Replacement Adds Years of Life to Navy Vessel
Panel Built, Inc., recently replaced all the wall and roof panels on a two-story US Navy barge deck house that the company had originally installed 30 years ago, giving the vessel new life. Now, the commanding officer of the unit that uses the barge said the difference between the condition and appearance from when the barge left their facility to when the project was complete was beyond his expectations of what was possible.
True Modular Building Seeks to Revolutionize Housing. It’s Next Stop: MBI’s World of Modular Europe
True Modular Building (TMB) specializes in crafting attainable, eco-friendly, and comfortable build-to-rent (BTR) housing with modern designs and customizable features, ensuring that residents feel at home both today and tomorrow.
From Toronto to Suriname: A Global Modular Building Story
When I AM Gold – a Canadian gold mining operation based in Toronto, Ontario – wanted to expand its mining operations in Suriname, it knew it would also need to expand its infrastructure. More specifically, they needed to build a mechanical services compound that would allow their local crews to maintain and equipment critical to their mining operations. They also knew that it would be a challenge.
There Were a “Sea of Challenges” for this Modular, Island Development
Question: Can modular construction be used to build a series of affordable, unique housing buildings, all styled to look like they were built in 1845, on an
island that caters to the wealthy? The answer is, of course, yes, but how the
team at Signature Building Systems and KOH Architecture got there is quite a story.
America’s Construction Economy: A Race Against Time
If the economy has been able to handle higher interest rates thus far, undoubtedly it will be able to manage the lower interest rates to come. But many economists are pointing out that the Federal Reserve may already be too late to the game. While they gradually reduce interest rates, the U.S. economy could quickly decelerate, at least based on theoretical grounds if not on the most recent data releases, culminating in that long-predicted recession. Only time will tell.
Top Five Benefits of Modular Office Space
Modular office spaces are transforming how businesses think about their work environments. These innovative structures offer a mix of flexibility, efficiency, and sustainability, making them a smart choice for companies looking to gain an advantage.