Developing the Next Rising Stars of the Greater Construction Industry
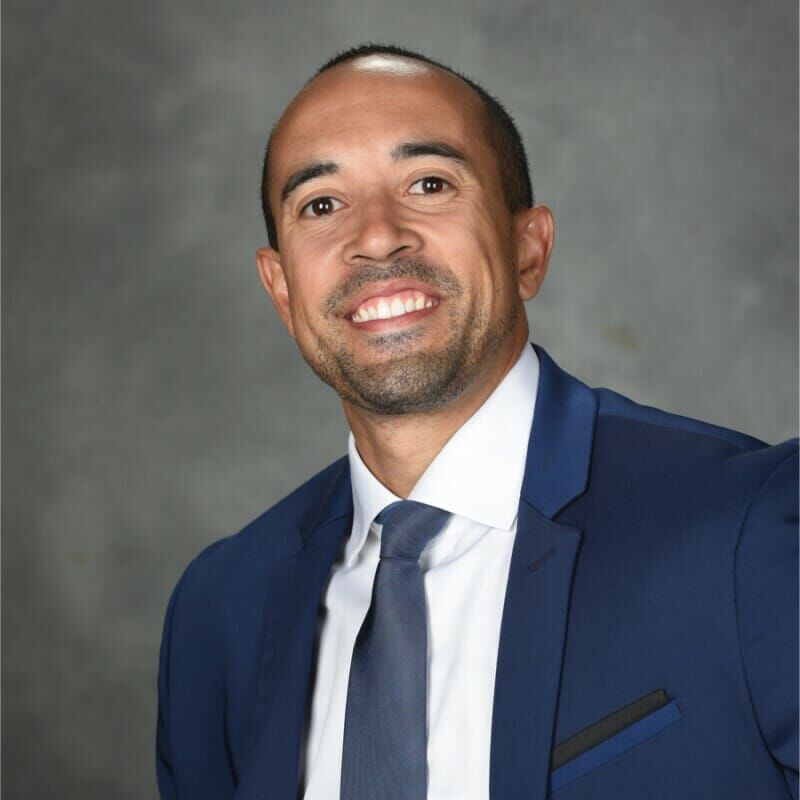
David Hutchinson is the leader of Tremco’s Deep Energy Retrofit Development and director of Rising Stars.
Like the construction industry at-large, Tremco is undergoing a transformation. The company has steadily broadened its product offerings beyond sealants and now, as Tremco Commercial Products Group, it’s expanding its mission as well.
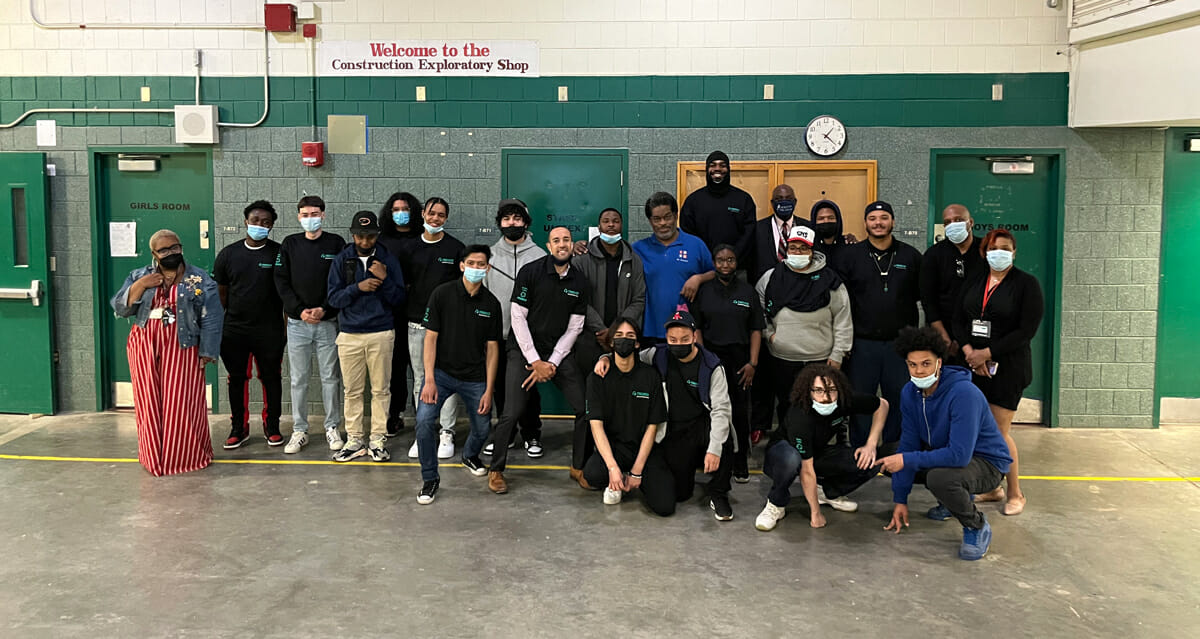
The graduating class of Boston's 2022 Rising Stars program.
Born during a leadership discussion in the summer of 2020, Tremco’s Rising Stars program was developed to offer students and young adults interested in construction a wholistic view of the industry. Currently operating in Boston, Brooklyn, and Newark, Rising Stars has seen increasing interest, both from students and new industry partners.
Among those new partners, in furtherance of its own mission to educate workers and professionals across the industry about modular construction, is the Modular Building Institute. As part of MBI’s initial involvement, as well as to learn more about the program and Tremco’s goals for it, I corresponded with David Hutchinson, leader of Tremco’s Deep Energy Retrofit Development and director of Rising Stars.
John McMullen (JM): Tell me about yourself, David. What’s your background?
David Hutchinson (DH): I had a circuitous path to the construction industry, as I had no one in family that was in this field. I came from a business communications background (Penn State) but fell in love with the idea of being able to see the and show the end product of my work. It began in Pittsburgh while my wife was completing school and really began to flourish in NYC, where we still reside. My day-to-day role is in Tremco’s Deep Energy Retrofit Development where I’m busy updating our energy inefficient building stock.
JM: And tell me about Tremco. How has it evolved over the years?
DH: Tremco has been around for nearly 100 years as a building products manufacturer, with a focus in roofing products. Over the last 3-5 years the company has transformed into a complete building envelope company. With products and services ranging from roof to ICF and every ancillary product in between, the company has embraced prefabrication and changing construction methodology. This wholistic view at not only building but the way we build has been a critical part of how this program came to be.
JM: How did the Rising Stars program get started?
DH: The original concept was born in the summer of 2020 during a conversation with my company executives. I felt strongly that we as a company should be better stewards in the communities in which we operate. As a leadership team, it was agreed that we could have an impact, so I started the process to bring this idea to life. A key factor was the growing concern in the lack of young people joining our industry and the imminent “brain drain.”
JM: As director, what’s your current goal for the program? How do you hope the program will grow?
DH: We focus on knowledge and opportunity, so the current goal is to provide an internship/job for any graduate who meets our criteria. It’s a very small goal but we want to avoid the “summer camp” feel and focus more on development. The ultimate goal is to grow to a new city a year; but, more than that, we want to have enough industry partners so that our graduates can choose the path that best fits their skillset.
JM: Who’s eligible to benefit from the program? How do they enroll?
DH: The program is open to 16–24-year-olds that show interest in our industry. The enrollment is currently based on our host locations (Brooklyn, Newark, Boston) and their recruitment strategies/capacity. Enrollment is twice a year (Fall -Spring cohorts).
JM: Tell me about the curriculum. How was it developed and what goals do you have for expanding it?
DH: The current curriculum is two-fold. We bring in presenters from every sector of the construction process (architect through subcontractor) and show not only the nuance to each field, but the career opportunities tied to them. What differentiates our program is the focus on sustainability, construction, and thinking to the future. A lot of our residents come from communities where the built environment is, for lack of a better term, poor. We want them to think about being capable and knowledgeable to change their neighborhoods. The next step has always been to integrate green, clean, and innovative construction into the course.
JM: Tell me about the experience of a student in the program. What can prospective enrollees look forward to?
DH: The students get a good mix of training on skills, construction knowledge, and, most importantly, learning career pathways. The enrollees will get to use their hands to build and create but there is also a big focus on exposure. The markets we have targeted don’t always get to see what is beyond the city limits and we try and break that trend to show how expansive and interesting the industry can be. And we have some exciting new items coming to our Boston program this year from solar, wind, and green tech companies as well.
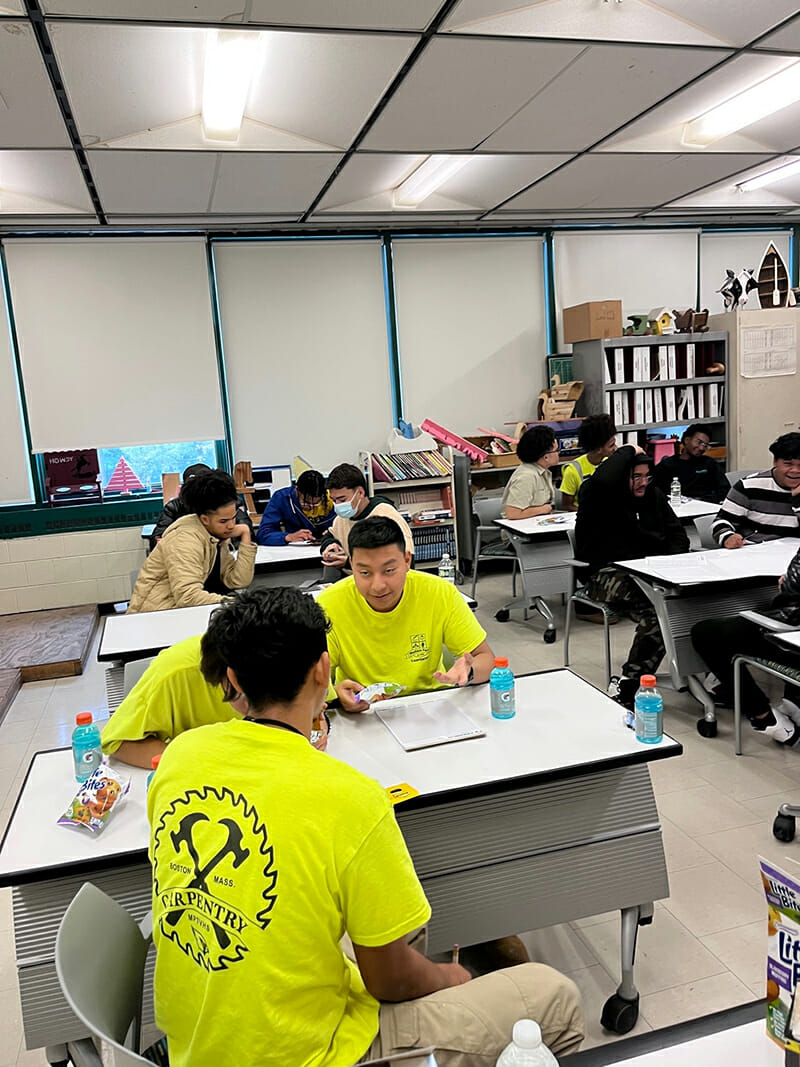
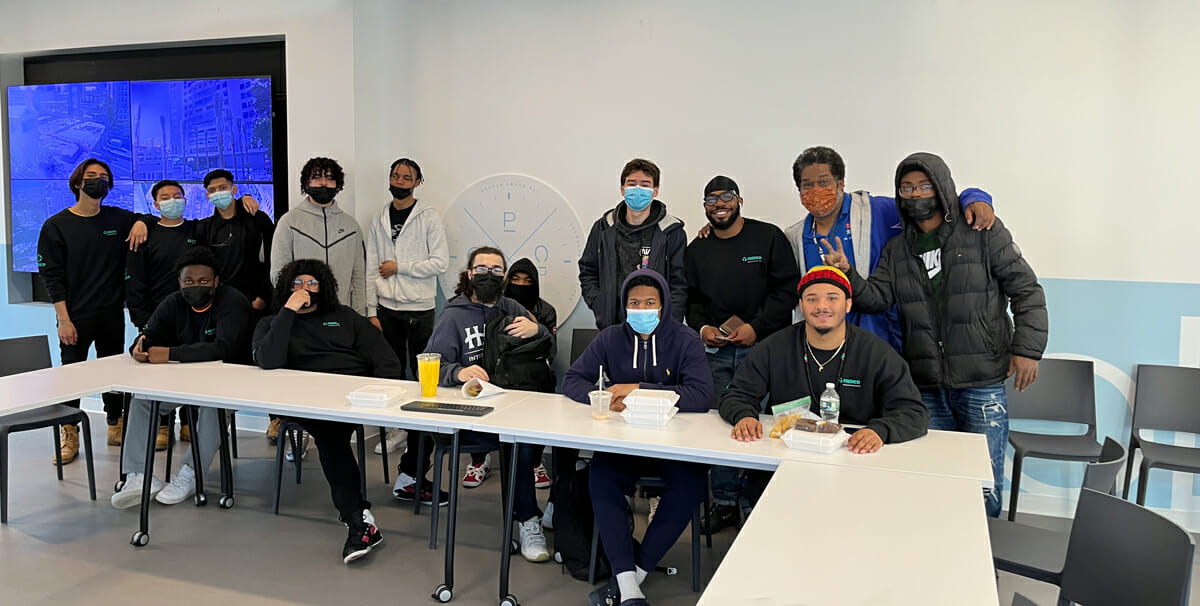
JM: What do you hope students will walk away with after completing the program?
DH: The goal has always been to instill confidence in their abilities as well as given them knowledge that may separate them from the pack as they start their construction journey. To create that carrot of knowing and hopefully striving to learn more. You want well-rounded individuals to be in the workforce, and our hope is that the graduates from this program understand how to communicate up and down the construction order of operations.
JM: Where do you see Rising Stars in the next 3-5 years?
DH: I want this to grow a city per year starting in 2023. We have had a lot of interest on the East Coast—particularly in Baltimore and Atlanta—from various companies that want to partner with us. The biggest goal and plan for the program is to have enough industry partners that we can effectively place our graduates in fields that best suit their talents and goals. The program has done a great job of connecting with existing non-profits as industry advocate groups through the first two years, I would like to see a more formal structure to really be able to scale this and support as many individuals as possible.
To learn more about Tremco’s Rising Stars program, its students and graduates, and to see its growing list of partners, visit https://info.tremcosealants.com/rising-stars-program.
About the Author: John McMullen, PCM, is the marketing director for the Modular Building Institute. You can reach him directly at mcmullen@modular.org or on LinkedIn.
More from Modular Advantage
Celebrating the Winners of MBI’s 2025 Awards of Distinction
MBI’s Awards of Distinction are presented annually, traditionally on the final evening of its North American World of Modular conference and tradeshow. This year’s Awards were presented in a variety of categories, including several each for permanent modular construction projects and relocatable buildings. Excellence in “green” modular construction and marketing were also recognized.
MBI Welcomes R.I. Group Founder & President Salvatore Tafuro to the Industry’s Hall of Fame
In 1973, Salvatore Tafuro, only in his twenties and already supporting a family of three children, set out to realize his entrepreneurial dream. From a humble garage in Leverano, in the heart of Salento, he began producing metal structures and aluminum fixtures for the construction industry.
The Best-Kept Secret in Housing
What can we do to right the ship, overcome these circumstances, capitalize on the opportunity, and address this epidemic in the housing sector? It’s easier than you might think.
The Blueprint for Accountability: How Mastery, Autonomy, and Purpose Drive Performance in Construction & Manufacturing
Accountability is one of the most critical elements of a thriving organization, yet many leaders in the construction and manufacturing industries struggle to create a culture where it truly thrives. High-performance teams require more than just technical skills and efficiency—they need strong accountability, alignment with the company’s vision, and a deep sense of ownership.
AI, Faster Sets, and Automation: The Future of Modular is at World of Modular
While the modular building industry has long known that it can be an effective solution to increase affordable housing, the word is slowly spreading to more mainstream audiences. Three presentations at this year’s World of Modular in Las Vegas hope to provide insight and direction for those seeking a real solution to the crisis.
An Insider’s Guide to the 2025 World of Modular
The Modular Building Institute is bringing its global World of Modular (WOM) event back to Las Vegas, and with it comes some of the industry’s best opportunities for networking, business development, and education. Over the course of the conference’s four days, there will be numerous opportunities for attendees to connect, learn, and leverage event resources to get the most out of the conference.
Affordable Housing Now: The Industry’s Best Bring New Solutions to World of Modular
While the modular building industry has long known that it can be an effective solution to increase affordable housing, the word is slowly spreading to more mainstream audiences. Three presentations at this year’s World of Modular in Las Vegas hope to provide insight and direction for those seeking a real solution to the crisis.
Opportunities for Innovation in Modular Offsite Construction
Modular Offsite Construction has already shattered the myth that it only produces uninspired, box-like designs. Architectural innovations in module geometry, configurations, materials, and products make it possible to create visually stunning buildings without sacrificing functionality or efficiency.
Safe Modular Construction with Aerofilm Air Caster Transport
In collaboration with Aerofilm Systems, Heijmans developed innovative skids using air caster technology for moving modules easily and safely. These pallets are equipped with an auto-flow system, making operation extremely simple.
Miles, Modules, and Memes: Building a Modular Network One Flight at a Time
At the end of the day, social media is just another tool for building connections, and like any other tool, needs to be used skillfully to work properly. Use social media thoughtfully, and it will open doors to real opportunities and relationships you didn’t even see coming.