Low-Income Housing Can Blaze the Trail for the Modular Industry
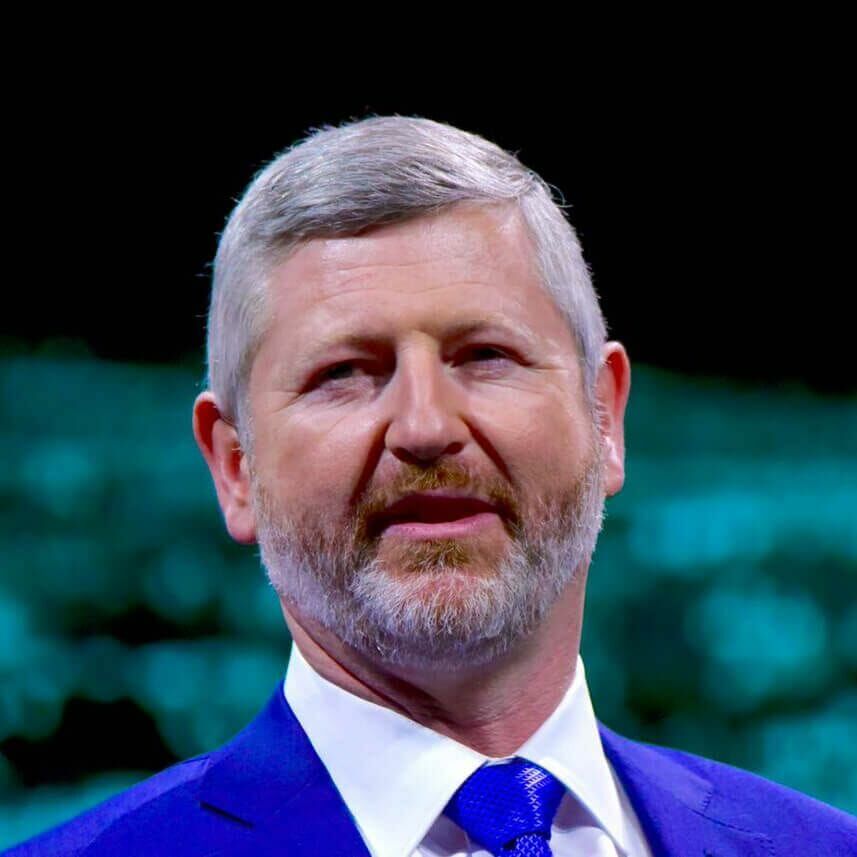
Jim McGeever, the former and well-known technology executive at Oracle NetSuite for 21 years, is turning his attention to construction as the new chief executive officer of Silver Creek Industries, a modular building manufacturer in Southern California. Having lived and worked in the San Francisco Bay area, Jim is familiar with the affordable housing crisis that plagues large and small cities worldwide and has been inspired to make a difference by using modular construction.
Now the Chief Executive Officer at California-based Silver Creek Industries, Jim McGeever spent almost two decades working at Oracle NetSuite. After being involved in the software industry for so long, you might wonder why McGeever became interested in construction. But the two interests were actually the other way around. “My dad worked in construction and the very first job I ever had was in construction, with a shovel in my hands, digging foundations in Birmingham, England. Construction is in my blood,” McGeever says.
His experience with conventional construction continued on this side of the Atlantic. While he was working in tech in the Bay Area, he built his first house. “The general contractor turned out to be really bad. It took two and a half years to build a 2500 square foot house, and everything that could go wrong, did go wrong,” McGeever recalls. “In the first three months of the project, I got a letter from the IRS saying that the GC owed them money, and that instead of paying him I needed to write them the check. It was a very bad experience as a consumer.”
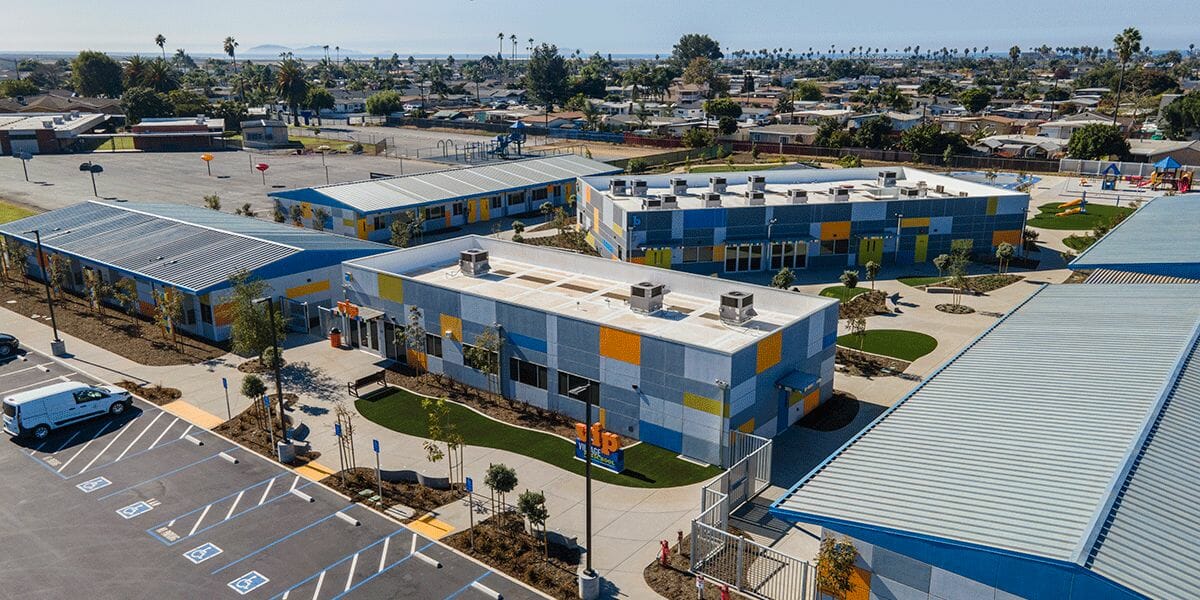
Silver Creek has a long history of modular projects—particularly schools, including this 2021 MBI Award of Distinction-winning preschool in California—but McGeever believes the modular industry has the opportunity to rapidly expand through affordable housing.
During his years in tech, McGeever started looking into alternative methods of construction, and came across modular, which intrigued him. About 10 years later, “I still had this construction-related itch I needed to scratch, and so we tried building a house using modular construction.” He says the experience wasn’t perfect, and there were lots of challenges, but “it was night and day compared to my previous experience, using conventional construction.” The experience was sufficiently positive that he “got into the habit of building modular homes and experimenting with different means and methods.” By the time he left the tech industry in 2019, McGeever felt that modular construction was “still missing some pieces crucial to its really taking off.” So he decided to dive in himself and try to solve some of its problems.
Scaling Up
McGeever joined NetSuite as its 15th employee, and by the time he left there were 8,000 employees. He says many lessons learned as the company scaled up are transferable to other industries. One lesson is that although being “super-creative” might work well for a start-up, it may not be what’s needed when a company has matured and its product has become more complex. “As we grew, the biggest transition was when we stopped trying to be the smartest people in the room. We stopped trying to reinvent the wheel,” McGeever says. “The key was how to make a complex product easy for the customer to consume.”
He thinks the modular industry needs to answer the same question: How do we make modular construction easier for developers and owners to consume?
After owners and developers have tried modular construction once, they “see how well it works and it tends to blossom into a high volume of projects,” McGeever says. When they’ve seen it in action, owners are impressed by modular’s speed to completion, and the resulting shorter time to revenue. “Having an extra 6 months of rent is a far bigger deal even than the actual cost savings with modular construction,” McGeever explains. “About 30% of the savings is on hard costs. The value of the shorter time to revenue is about 70%.”
Making it easier for owners and developers to consume their initial taste is a challenge the industry needs to address. McGeever will explore how to accomplish that in his World of Modular presentation.
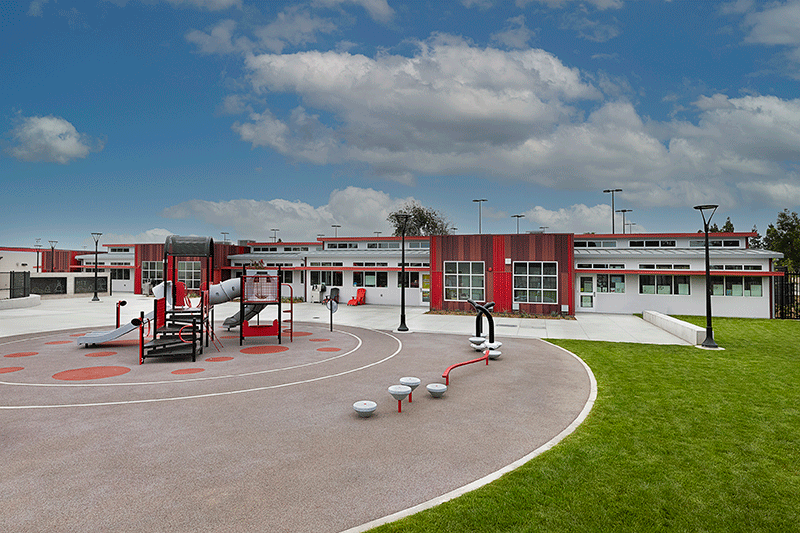
McFadden Elementary School, Single Story
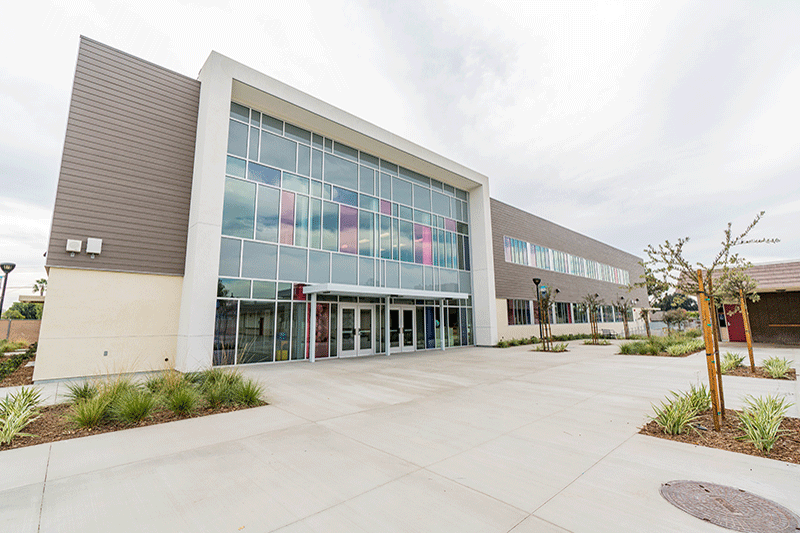
John Muir Fundamental Elementary, Two-Story
Low-Income Housing as the Vanguard
Low-income housing is a key sector for modular construction, McGeever believes. Not only is there high demand for it in the United States, but “to build at scale, and fast, you really have no choice but to use high volume production methods, which modular construction is ideal for.”
However, to gain greater market share, there are some advances the industry needs, including better financing, improved perceptions, and greater standardization.
Financing
McGeever is paying attention to how the financial industry is changing and responding to modular construction. Some banks are beginning to understand modular, but there are still valid issues, he says. “We’re missing out on opportunities to help solve some serious problems, just because of the funding mechanisms. We still have work to do to solve this problem.”
With conventional construction, “if a building’s partially completed on-site, you can touch it and feel it. It has value for the bank. If something goes wrong with the contractor, someone else can be brought on to finish the project.” In contrast, if a modular project goes wrong, it’s riskier from the bank’s point of view. It’s harder for them to salvage a project when it “involves half-built modules in a factory that goes bankrupt.”
Perceptions
“Modular is still associated with low quality portable classrooms and mobile homes,” McGeever says. “The only way to get past mistaken perceptions is with proof. We have to keep building examples of modular construction that we’re proud of.”
He wants to build buildings that nobody can tell from looking at them that they’re modular. Even when a building is for low-income housing or for a homeless shelter, “I want people to think it’s the nicest building in a 10-block radius. Low-income housing that looks like a camp made from tiny boxes isn’t going to change the perception of modular.”
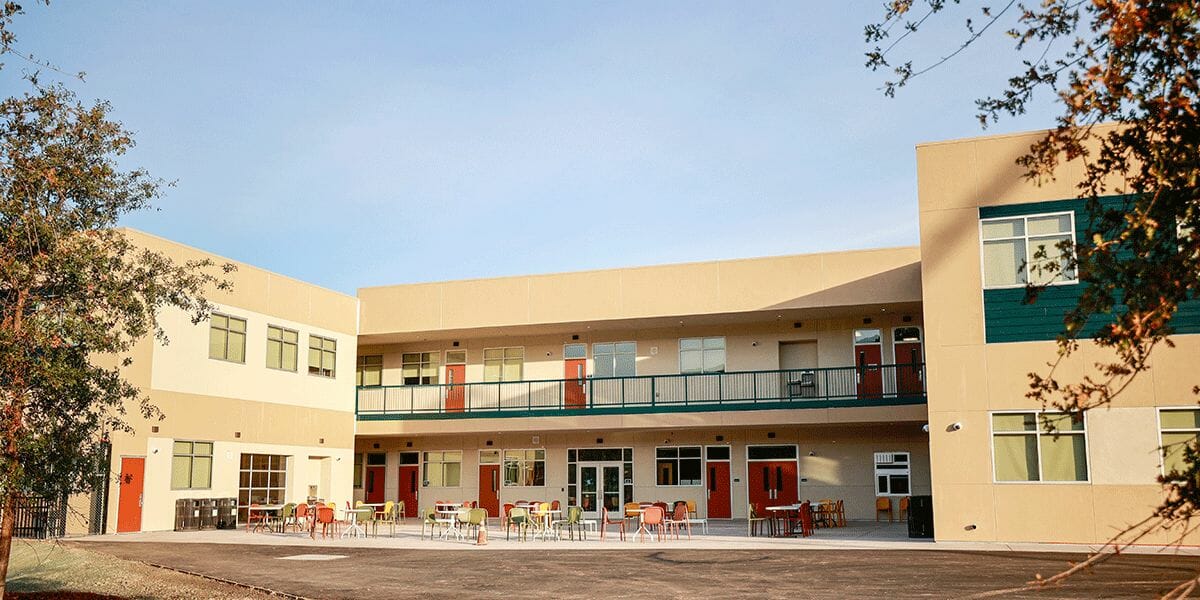
Camille Creek Community School, Two-Story
Standardization
The modular industry needs to further embrace standardization — and the low-income housing market is perfect for this. Most developers of low-income housing aren’t especially concerned about the layout of individual living spaces, McGeever says. “They’re more concerned about the layout of the building as a whole and the exterior.” So to accomplish greater standardization, while also allowing some flexibility, “We’ve developed what we call an architect’s toolkit,” McGeever explains. “We give architects CAD drawings or Revit files of the components and they can lay them out however they like and incorporate them into the building. And we advise them on how they can make the exterior unique.”
He illustrates the usefulness of standardization for developers and owners with ADA-compliant bathrooms. “Lots of low-income housing has disability requirements that can be tough to meet. We have a battle-tested, ADA-compliant bathroom design that’s passed inspections, which we can use again and again,” McGeever explains. He tells developers that they’re welcome to use their own bathroom design, but then they’ll have to take responsibility for it passing inspections. Developers immediately see the benefits of sticking with a standardized design. “The conversation tends to end real quick at that point.”
McGeever is optimistic. “If we do it right, once people see the benefits of the modular approach through the low-income housing market, other sectors will be more open to modular construction too.”
About the Author: Zena Ryder is a freelance writer, specializing in writing about construction and for construction companies. You can find her at Zena, Freelance Writer or on LinkedIn.
More from Modular Advantage
Celebrating the Winners of MBI’s 2025 Awards of Distinction
MBI’s Awards of Distinction are presented annually, traditionally on the final evening of its North American World of Modular conference and tradeshow. This year’s Awards were presented in a variety of categories, including several each for permanent modular construction projects and relocatable buildings. Excellence in “green” modular construction and marketing were also recognized.
MBI Welcomes R.I. Group Founder & President Salvatore Tafuro to the Industry’s Hall of Fame
In 1973, Salvatore Tafuro, only in his twenties and already supporting a family of three children, set out to realize his entrepreneurial dream. From a humble garage in Leverano, in the heart of Salento, he began producing metal structures and aluminum fixtures for the construction industry.
The Best-Kept Secret in Housing
What can we do to right the ship, overcome these circumstances, capitalize on the opportunity, and address this epidemic in the housing sector? It’s easier than you might think.
The Blueprint for Accountability: How Mastery, Autonomy, and Purpose Drive Performance in Construction & Manufacturing
Accountability is one of the most critical elements of a thriving organization, yet many leaders in the construction and manufacturing industries struggle to create a culture where it truly thrives. High-performance teams require more than just technical skills and efficiency—they need strong accountability, alignment with the company’s vision, and a deep sense of ownership.
AI, Faster Sets, and Automation: The Future of Modular is at World of Modular
While the modular building industry has long known that it can be an effective solution to increase affordable housing, the word is slowly spreading to more mainstream audiences. Three presentations at this year’s World of Modular in Las Vegas hope to provide insight and direction for those seeking a real solution to the crisis.
An Insider’s Guide to the 2025 World of Modular
The Modular Building Institute is bringing its global World of Modular (WOM) event back to Las Vegas, and with it comes some of the industry’s best opportunities for networking, business development, and education. Over the course of the conference’s four days, there will be numerous opportunities for attendees to connect, learn, and leverage event resources to get the most out of the conference.
Affordable Housing Now: The Industry’s Best Bring New Solutions to World of Modular
While the modular building industry has long known that it can be an effective solution to increase affordable housing, the word is slowly spreading to more mainstream audiences. Three presentations at this year’s World of Modular in Las Vegas hope to provide insight and direction for those seeking a real solution to the crisis.
Opportunities for Innovation in Modular Offsite Construction
Modular Offsite Construction has already shattered the myth that it only produces uninspired, box-like designs. Architectural innovations in module geometry, configurations, materials, and products make it possible to create visually stunning buildings without sacrificing functionality or efficiency.
Safe Modular Construction with Aerofilm Air Caster Transport
In collaboration with Aerofilm Systems, Heijmans developed innovative skids using air caster technology for moving modules easily and safely. These pallets are equipped with an auto-flow system, making operation extremely simple.
Miles, Modules, and Memes: Building a Modular Network One Flight at a Time
At the end of the day, social media is just another tool for building connections, and like any other tool, needs to be used skillfully to work properly. Use social media thoughtfully, and it will open doors to real opportunities and relationships you didn’t even see coming.