Warming Up to Snowflake Manufacturing
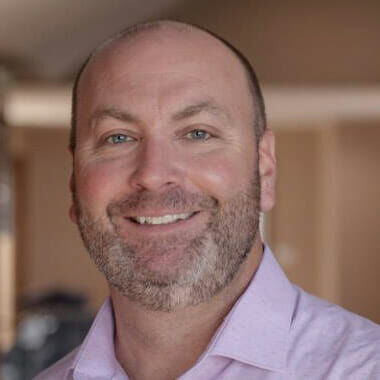
Brent McPhail is the Founder and Chief Executive Officer of Brave Control Solutions. For modular manufacturers, Brave integrates various robotic components to create machines to manufacture buildings offsite. Given that there are thousands of different robotic components, and that different manufacturers have different needs, it’s no simple matter to design a machine that will work for a specific manufacturer. Here, we look into Brave’s process for helping modular manufacturers introduce automation.
Getting started with robotics
Although more manufacturers are considering automation, McPhail acknowledges it can be intimidating. The first thing Brave Control Solutions does is determine a manufacturer’s automation readiness on a scale of 1 to 4. “Once we know this, we can begin to map out their ‘Gap to Good’. It’s about more than technology,” McPhail explains. “We look at their company culture, their management systems. We determine if they’re practising Lean manufacturing. One of the biggest challenges in construction automation is DfMA [design for manufacturing and assembly]. This term is talked about a lot but really understanding it is essential for an automated system to work effectively.”
Modular manufacturing companies differ greatly in how ready they are for automation. McPhail says some have overly-ambitious ideas about what automation can do for them when they’re nowhere near ready. “It would be like handing them the keys to a rocket ship when they have nobody who can pilot it.”
When a company turns out not to be ready for automation, it can still be valuable for a manufacturing expert to look into its processes. “Sometimes there are ways we can help them manufacture better without adding robots.” For example, Brave can identify bottlenecks, make recommendations for how to move materials, and suggest ways to make their operations more Lean.
When the in-depth assessment is complete, “we can figure out what the low-hanging fruit are” — the places where a factory can most easily, quickly, and effectively automate with a satisfying return on investment.
The low-hanging fruit varies from plant to plant, but McPhail says it’s often related to materials handling. In other cases, workers are wasting too much time walking around. “In traditional manufacturing, the goal is an OEE [overall equipment efficiency] of 85%. You can’t get 85% efficiency if the worker who operates the machinery is wandering around looking for things 60% of the time.”
Walking is the kind of tedious task that it’s a waste of a human’s brain and skills to spend time on. Brave’s goal is to gain maximum efficiency from the manufacturer’s current workforce.
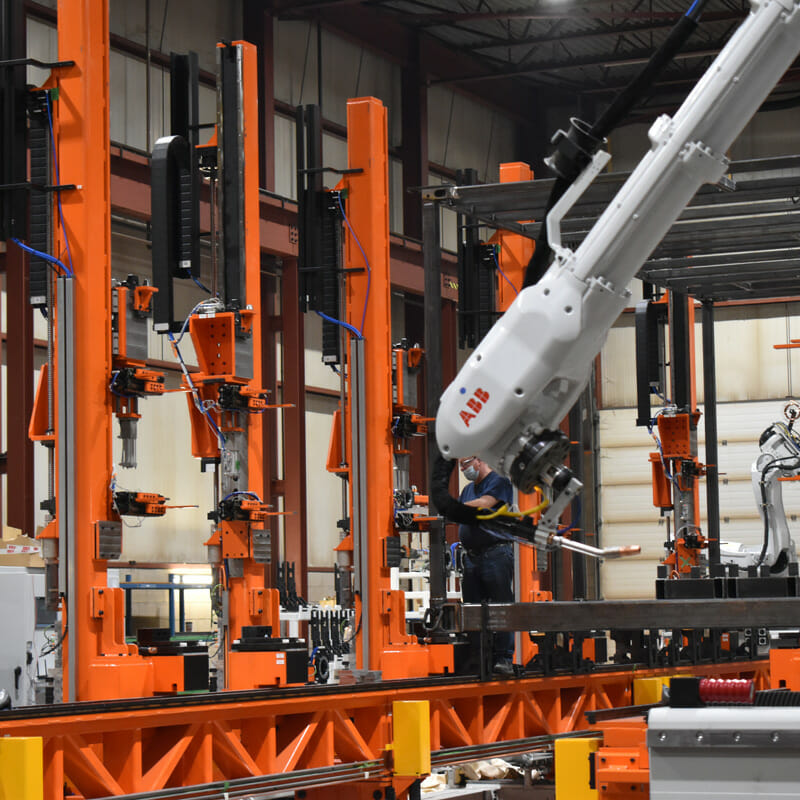
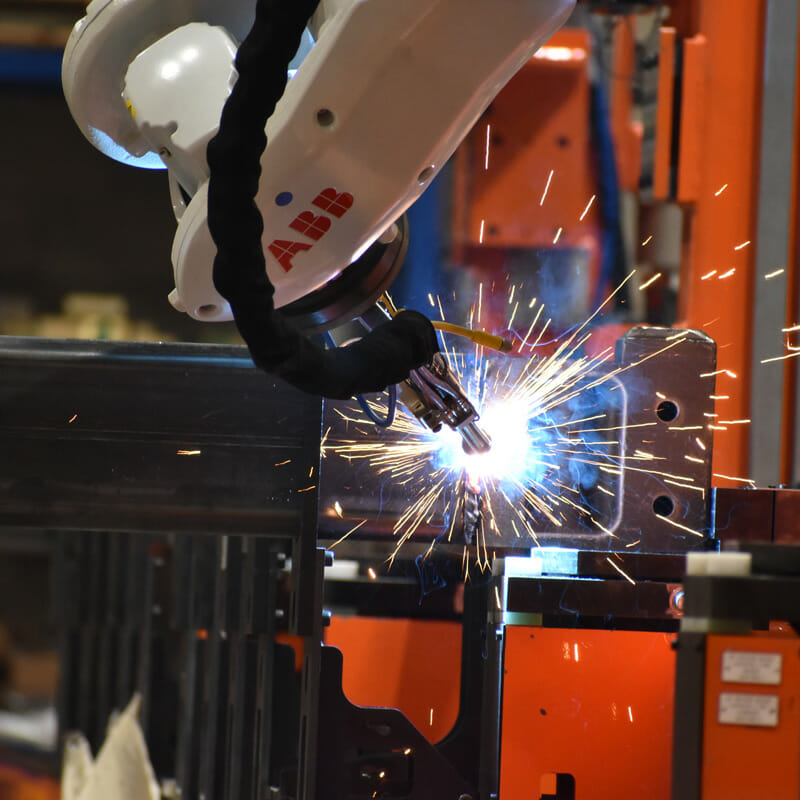
Learn More in this Podcast:
Design for Automated Modular Manufacturing w/ Brave Control Solutions
In this episode of Inside Modular, Brent McPhail, founder and CEO of Brave Control Solutions, returns to discuss the current state of automation within the modular construction industry and what lies ahead as both designers and manufacturers embrace the benefits and challenges of modular automation.
Labor
Contrary to the commonly expressed fear that robots replace workers, McPhail says, “Automation for construction won’t remove a single construction job. It’ll mean we can come closer to meeting the demand for new construction with the existing skilled labor we already have.”
He also says that workers on the factory floor are typically pleased when robots are introduced. “Nobody likes to waste time and energy being inefficient at work,” he says. “If automation can help them produce five or ten times as many drywall sheets per hour, with no greater effort or stress, who wouldn’t want that?”
Ideally, humans do the jobs they’re best at and find most satisfying — and robots do the jobs they’re best at. And that’s often the dull, tedious, repetitive tasks that humans find boring, or heavy-lifting tasks that are unsafe for them to do for long periods. For example, to make the best use of a skilled carpenter’s expertise, “A general laborer can run the machine and the carpenter should be in a supervisory role,” McPhail explains. “The carpenter can make sure the raw material is to specification, and do quality control on the product going out. They know when adjustments need to be made to the system.”
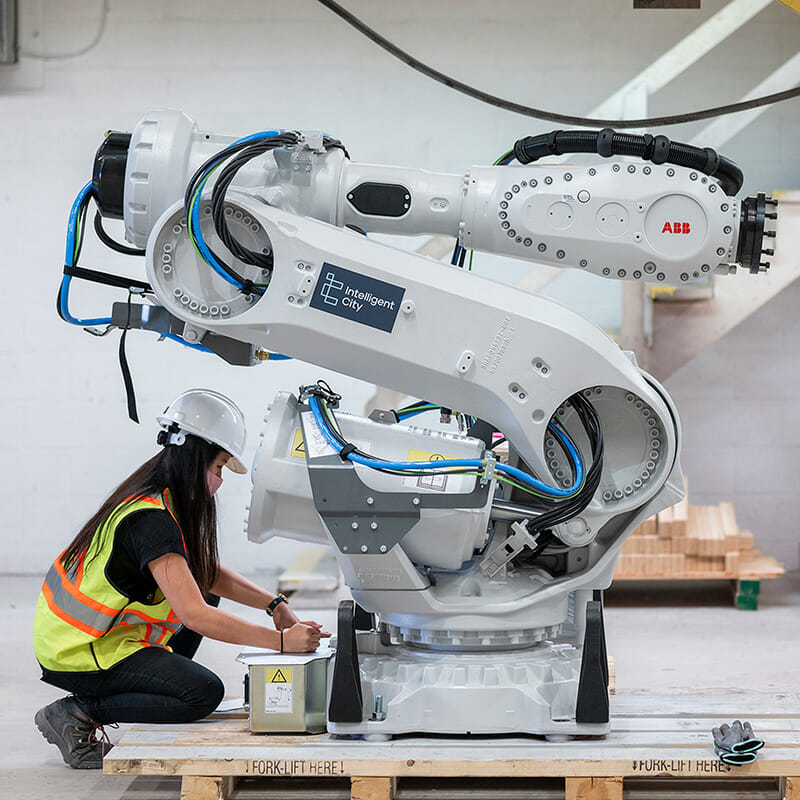
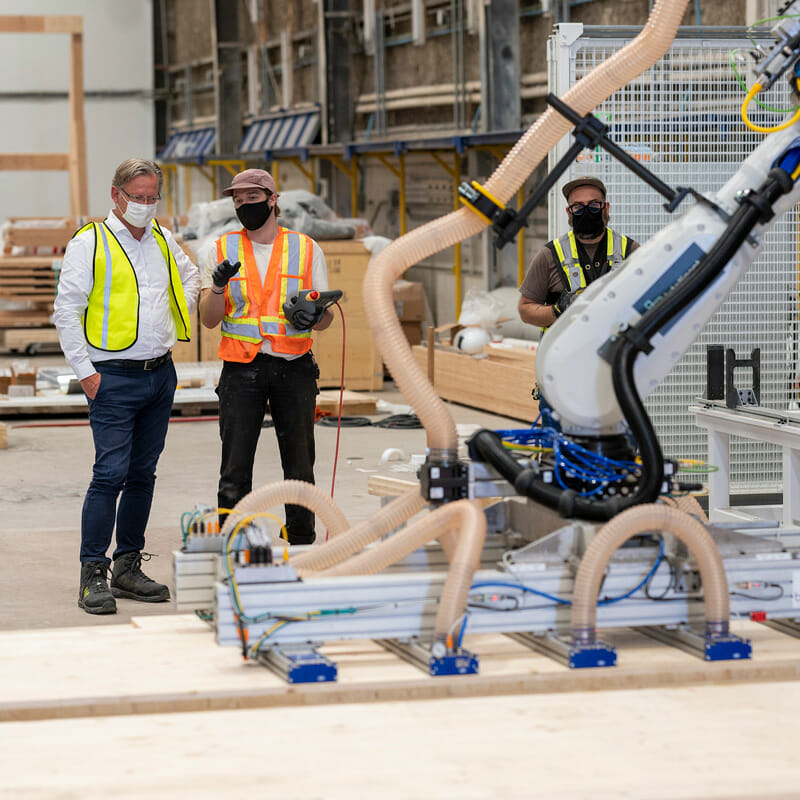
Mature manufacturing and early adopters
As a system integrator, Brave prefers to apply off-the-shelf technology and then customize it for specific tasks. Automated construction is a new field, so they sometimes have to develop original tools which initially might increase risk and lengthen project timelines.
Another complication is what McPhail calls “snowflake manufacturing”. Every building is unique, depending on the requirements of the site and the owner’s needs. In contrast, although there are minor variations between Ford F-150s — such as paint color and seat fabric options — they are basically all the same, down to an incredible level of detail. So the robots in an automotive manufacturing plant can be programmed to do the same thing over and over again.
In contrast, modular manufacturers need enough flexibility in their robotic systems to accommodate snowflake manufacturing. At the same time, they need to accept that any robotic system needs to be designed so that different projects can be made with fundamentally the same equipment. “You’re never going to make a good business case for continually redeveloping the machinery for each new project.”
Design for automated manufacturing
For an automated facility, products need to be designed so robots can manipulate and assemble the parts. If the robots’ constraints mean that manufacturing is “only 70% automated and the rest has to be done manually, then you’re losing efficiencies you should’ve gained with automation.”
In a mature automated industry, knowledge of how to design for automated assembly has been passing from senior to junior designer for 60 years. Designers know where to put the slots and pins and holes on a car component so robots can manipulate it. In the modular industry, that generational knowledge doesn’t exist and, in its absence, architects, robotics experts, and manufacturers all need to consult with one another at the beginning of the design process, so they can all inform the design.
“We build a digital replica of the equipment. The architect can export their Revit model into the digital factory and watch the robots work. If the robot collides with something in the virtual design, the architect can adjust the design to avoid the crash,” McPhail explains. “This trial and error method is inefficient, but at this early-adopter stage, it’s what we have. As the industry develops more automated solutions and gains DfMA experience, the BIM [building information modeling] models will integrate with the automation and eliminate the need for trial and error.”
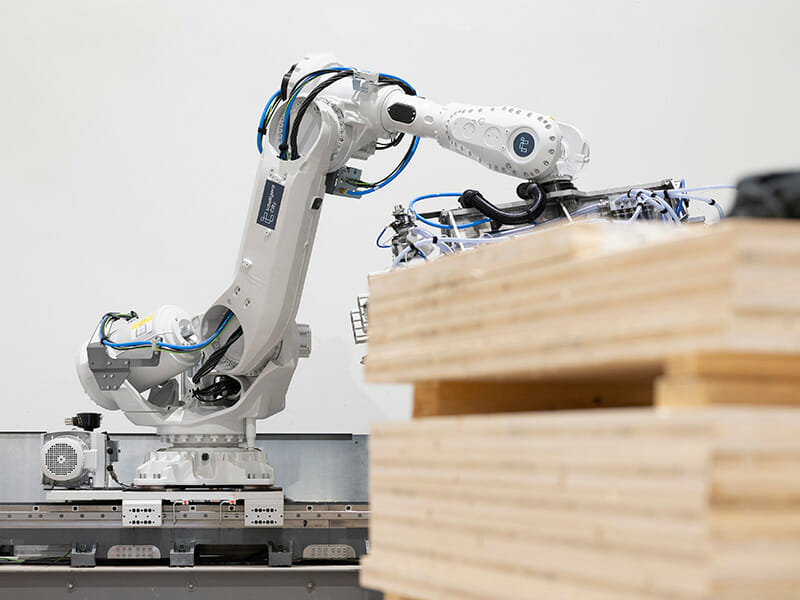
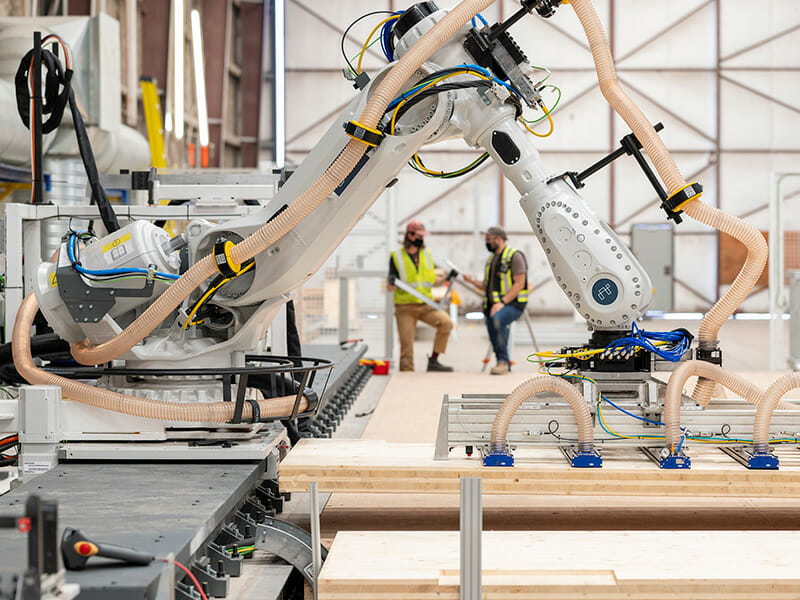
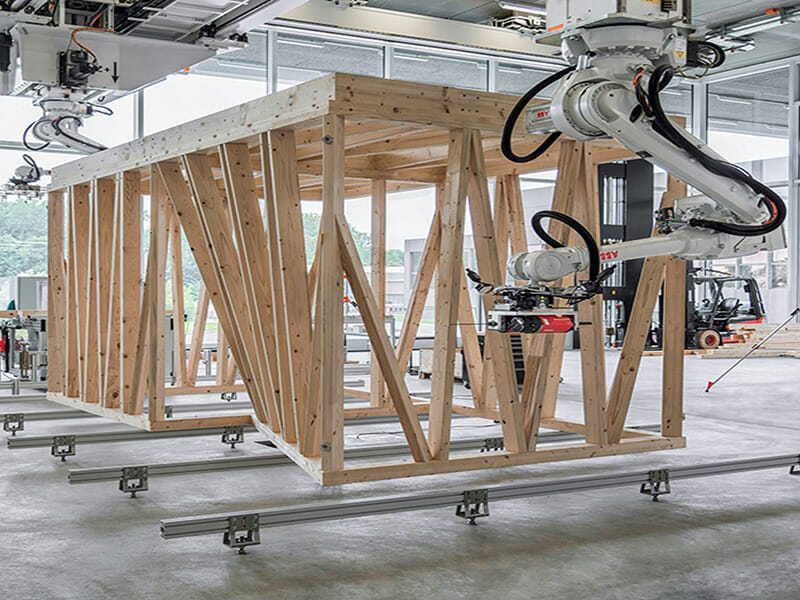
Mobile factories
McPhail doesn’t shy away from considering new ideas, and while his company is currently “building the tools and equipment the modular industry needs, and solving their manufacturing problems” he’s imagining other ways that the industry might adapt to automation in the future.
One suggestion is that automation makes smaller, mobile factories more feasible. Currently, hiring is difficult, so moving a temporary facility from place to place and hiring local people is impractical. McPhail’s alternative idea is to “set up a temporary factory near where you’re going to build 1000 houses. You transport your robotic equipment to the factory, connect it all together, and build those houses. When you’re done, you pack everything up and move it all to the next project site.” In this scenario, there’d be no need for long-distance transportation of modules and no need for a huge, centralized manufacturing plant. Will future modular factories involve robots roaming from jobsite to jobsite?
About the Author: Zena Ryder is a freelance writer, specializing in writing about construction and for construction companies. You can find her at Zena, Freelance Writer or on LinkedIn.
More from Modular Advantage
Celebrating the Winners of MBI’s 2025 Awards of Distinction
MBI’s Awards of Distinction are presented annually, traditionally on the final evening of its North American World of Modular conference and tradeshow. This year’s Awards were presented in a variety of categories, including several each for permanent modular construction projects and relocatable buildings. Excellence in “green” modular construction and marketing were also recognized.
MBI Welcomes R.I. Group Founder & President Salvatore Tafuro to the Industry’s Hall of Fame
In 1973, Salvatore Tafuro, only in his twenties and already supporting a family of three children, set out to realize his entrepreneurial dream. From a humble garage in Leverano, in the heart of Salento, he began producing metal structures and aluminum fixtures for the construction industry.
The Best-Kept Secret in Housing
What can we do to right the ship, overcome these circumstances, capitalize on the opportunity, and address this epidemic in the housing sector? It’s easier than you might think.
The Blueprint for Accountability: How Mastery, Autonomy, and Purpose Drive Performance in Construction & Manufacturing
Accountability is one of the most critical elements of a thriving organization, yet many leaders in the construction and manufacturing industries struggle to create a culture where it truly thrives. High-performance teams require more than just technical skills and efficiency—they need strong accountability, alignment with the company’s vision, and a deep sense of ownership.
AI, Faster Sets, and Automation: The Future of Modular is at World of Modular
While the modular building industry has long known that it can be an effective solution to increase affordable housing, the word is slowly spreading to more mainstream audiences. Three presentations at this year’s World of Modular in Las Vegas hope to provide insight and direction for those seeking a real solution to the crisis.
An Insider’s Guide to the 2025 World of Modular
The Modular Building Institute is bringing its global World of Modular (WOM) event back to Las Vegas, and with it comes some of the industry’s best opportunities for networking, business development, and education. Over the course of the conference’s four days, there will be numerous opportunities for attendees to connect, learn, and leverage event resources to get the most out of the conference.
Affordable Housing Now: The Industry’s Best Bring New Solutions to World of Modular
While the modular building industry has long known that it can be an effective solution to increase affordable housing, the word is slowly spreading to more mainstream audiences. Three presentations at this year’s World of Modular in Las Vegas hope to provide insight and direction for those seeking a real solution to the crisis.
Opportunities for Innovation in Modular Offsite Construction
Modular Offsite Construction has already shattered the myth that it only produces uninspired, box-like designs. Architectural innovations in module geometry, configurations, materials, and products make it possible to create visually stunning buildings without sacrificing functionality or efficiency.
Safe Modular Construction with Aerofilm Air Caster Transport
In collaboration with Aerofilm Systems, Heijmans developed innovative skids using air caster technology for moving modules easily and safely. These pallets are equipped with an auto-flow system, making operation extremely simple.
Miles, Modules, and Memes: Building a Modular Network One Flight at a Time
At the end of the day, social media is just another tool for building connections, and like any other tool, needs to be used skillfully to work properly. Use social media thoughtfully, and it will open doors to real opportunities and relationships you didn’t even see coming.