Advantages of Digital Prefabrication for the Modern Construction Industry
The cutting-edge of the modern construction industry revolution
In light of technological advances, the construction industry develops new methods to respond to customer needs and labor-related difficulties, and diversifies the Modern Methods of Construction (MMC) in order to increase productivity in the sector. Digital prefabrication is a type of production where digital data directs production equipment to create various building components. It is the cutting-edge of the modern construction industry revolution.
Today, it is seen that multicomponent prefabricated building elements offer high quality projects with lower costs and accelerated optimizable programs. Recently, concepts such as Design for Manufacturing and Assembly (DfMA) and Designing for Industrialized Methods of Construction (DIMC) constitute the most basic and modern elements of Off-Site Construction and Modern Methods of Construction (MMC). Both concepts not only support engineering methodology simultaneously but also the industry transition from fully on-site construction to on-site assembly of ready-made prefabricated building components.
Design for Manufacturing and Assembly (DfMA) in the simplest definition; It is the application of the factory production conditions realized in industrial facilities to modern construction projects. It also includes prefabricated modular building elements. In practice, building structural elements are manufactured off-site in a controlled environment, transported to the site and made ready for assembly
The Design for Industrialized Construction Methods (DIMC) aims to programmatically select and supply building components for use in the project. It aims to accomplish without compromising the improved design, construction quality, cost and project schedule (timeline).
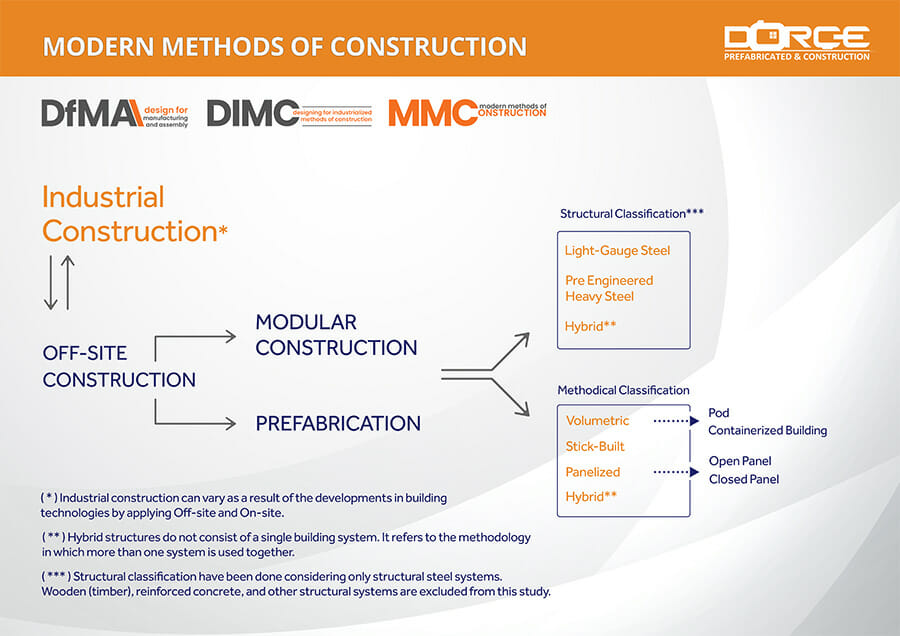
Exclusive solutions supported by virtual models
DORCE Prefabricated Building & Construction Industry Trade Inc. , manufactures prefabricated modular building components directly with Building Information Modeling (BIM) and completes their assemblies completely digitally off-site in total accordance with the project requirements; including load-bearing panel system structures, paneled exterior walls and internal walls with built-in electrical and sanitary installations. DORCE integrates the digital fabrication of the building components that make up the main structure into its projects from the very beginning of the design process. Modular building systems, manufactured by DORCE, are used for projects that require rapid solutions and must be completed in harsh climatic and geographical conditions. The components of these modular buildings are manufactured in a controlled environment at the industrialized facility (factory conditions) and transported to the construction site as units and assembled on-site.
Customized (customer-oriented) prefabricated modular structures are built to suit the unique needs of each project, utilizing Virtual Design and Construction (VDC) processes and data-rich Building Information Modeling (BIM). DORCE works in integration with its in-house engineering, design and project management department in order to maximize and optimize the architectural design for the Design for Manufacturing and Assembly (DfMA) process without changing the design.
Related Listening:
Examining the Global Modular Construction Market w/ DORCE Ltd.
In this episode of Inside Modular, Mehmet Yucesoy, business development manager at Turkey's DORCE Ltd. shares DORCE's 40-year story of international success and details how modular construction can be applied to almost any construction market around the world. Mehmet also gives advice on how modular companies can begin and expand their globalization efforts.
Is it possible to enhance construction efficiency with improved digital programs?
Digital prefabrication reduces costs and workforce on site, increases quality, and accelerate the construction schedule. Enhanced digital modeling applications that facilitate the link between design and construction put prefabrication at the forefront of the technology revolution that transforms construction industry.
Including digital prefabrication in the design process of the project provides the following advantages:
Higher Quality
Digitally prefabricated modular building component in a factory-controlled environment improves quality control. Identical products are created on the basis of models and then components requested in the field are presented.
Cost Control
Waste material is minimized since construction materials are grouped. The workforce managed in the factory environment offers greater predictability by providing higher productivity, safer working environments and cost advantages. The cost of site workforce is approximately 2.2 times that of factory workforce, and factory productivity is approximately twice that of construction site.
Accelerated Work Plan
Prefabricated modular building components such as panels, walls and roof are manufactured in parallel with infrastructure, concrete, installation and site preparation works etc. In this way we ensure that the project is completed earlier. Since the weather conditions do not affect the production activities in the factory environment, less negative factors are encountered in the production processes.
Less Workforce
Off-site construction requires fewer workers on-site, thus provides a safer working environment. Since it provides consistency, it is defined as the most attractive sector of the construction industry in terms of workforce. The controlled factory environment also offers the opportunity to cross-train in specific tasks, which helps to balance the workforce and develop various skills.
Sustainability
Since mass production is carried out in the prefabricated modular construction sector and it takes place in a controlled environment, the waste material is significantly reduced or even totally avoided. In addition, fossil fuel consumption and related emissions are reduced as the number of vehicles traveling to and from the construction site decrease.
Site Restrictions
Weakened mobility due to pandemic has made site restrictions become even more common. Prefabricated modular construction minimizes the number of workers needed on site. For this reason, the applicability of off-site constructions gains more importance with each day passing.
More from Modular Advantage
How BIM & AI are Improving Modular Construction Outcomes Across Europe
Digitalization and ever-advancing project modelling software have been aiding traditional manufacturers, builders, and designers for years. More recently, tech-savvy modular and offsite construction stakeholders have also embraced these tools, adding their own knowledge and data to create newer, faster, more efficient ways of building. Together with new BIM- and AI-powered tools, these builders are now pushing the boundaries of what’s possible with offsite construction and energy management.
Oregon’s Prevailing Wage Proposal: A Wake-Up Call for Modular Construction
Should House Bill 2688A become law, building projects would increase in price, face longer completion timelines, and produce significantly more waste. The bill also incentivizes contract awards to out of state businesses who would not reinvest their earnings into the local Oregon economy.
Behind the Design of Bethany Senior Terraces, NYC’s First Modular Passive House Senior Housing Project
As more developers seek to meet new regulations for energy efficiency, the team at Murray Engineering has set a new record. With the Bethany Senior Terraces project, Murray Engineering has helped to develop NYC’s first modular structure that fully encompasses passive house principles — introducing a new era of energy efficiency in the energy-conscious city that never sleeps.
How LAMOD is Using Modular to Address Inefficiency, Sustainability, and the Future of Construction
As developers, designers, and contractors seek to understand the evolving needs of the modular industry, no one is as well-versed in the benefits of going modular as Mārcis Kreičmanis. As the co-founder and CBDO of LAMOD in Riga, Latvia, Mārcis has made it his ultimate goal to address the inefficiencies of traditional construction.
From Furniture Builder to ‘Activist Architect’: Stuart Emmons’ Unique Journey
Stuart Emmons was fascinated by buildings at a young age. He remembers building sand cities with his brother during trips to the Jersey shore. His father gave him his first drawing table at the age of ten. Today, he is an experienced architect who received his FAIA in June 2025. The road he took is unique, to say the least.
Forge Craft Architecture + Design: Codes, Contracts, and Intellectual Property
Founding Principal and Director of Modular Practice for Forge Craft Architecture + Design, Rommel Sulit, discusses the implications of codes, contracts, and intellectual property on
modular construction.
Eisa Lee, the “Bilingual” Architect
Now as the founder of XL
Architecture and Modular Design in Ontario, Canada, she applies not just her education as a traditional architect but an entire holistic view on modular design. It’s this expansive view that guides her work on being a true partner that bridges the gap between architects and modular factories as they collaborate on the design process.
Tamarack Grove Engineering: Designing for the Modular Sector
The role of a structural engineer is crucial to the success of a modular project, from initial analysis to construction administration. Tamarack Grove offers structural engineering services — project analysis, plan creation, design creation, and construction administration — for commercial, manufacturing, facilities, public services, and modular. Modular is only one market sector the company serves but it is an increasingly popular one.
Engineer Masters the Art of Listening to His Customers
Since founding Modular Structural Consultants, LLC. in 2014, Yurianto has established a steady following of modular and container-based construction clients, primarily manufacturers. His services often include providing engineering calculations, reviewing drawings, and engineering certification
Inside College Road: Engineering the Modules of One of the World’s Tallest Modular Buildings
College Road is a groundbreaking modular residential development in East Croydon, South London by offsite developer and contractor, Tide, its modular company Vision Volumetric (VV), and engineered by MJH Structural Engineers.