Forge Craft Architecture + Design: Codes, Contracts, and Intellectual Property
Founding Principal and Director of Modular Practice for Forge Craft Architecture + Design, Rommel Sulit, discusses the implications of codes, contracts, and intellectual property on modular construction.
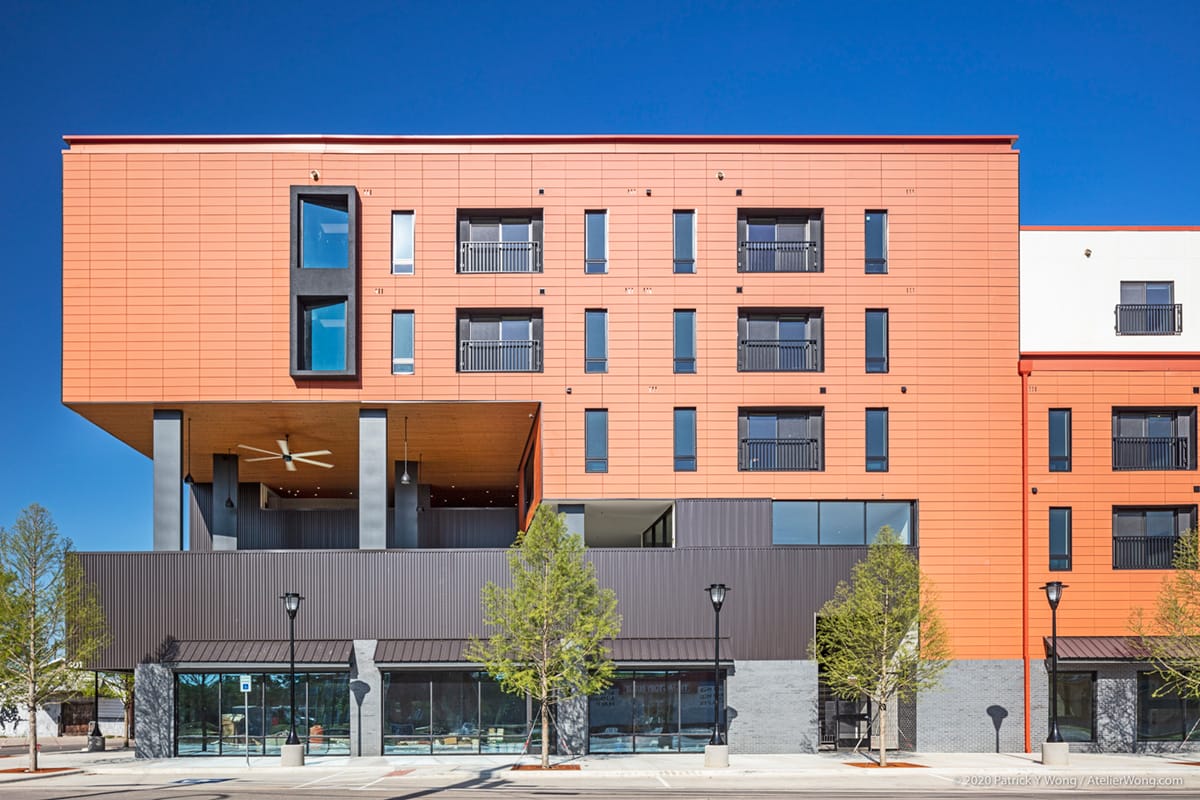
Rommel Sulit loved both art and science. He graduated from the University of Chicago with a degree in studio art after starting college enrolled in premed. He worked at an alternative news weekly after graduation to determine what path to follow as a career.
Architecture seemed a good balance between science and art, so he attended the University of Texas in Austin. He graduated with a master’s in architecture and a desire to call Austin his home.
He and business partner Scott Ginder founded Forge Craft Architecture + Design in 2013 in Sulit’s living room with two hires.
Right away, they landed two medium-sized conventional projects — a 100-unit multifamily project and a 135-unit affordable housing multifamily project, both featuring microunits.
Within a couple years, a client wanted to explore volumetric modular building for a student housing project.
“They came to us with this really interesting opportunity, and we just learned as we went,” Sulit said.
From 2015 to 2020 Forge Craft was immersed in modular construction projects for student housing, a quick serve restaurant, commercial office and affordable prefabricated vacation homes. Forge Craft built its platform based on those early projects.
“Our goal was to develop a company that was relevant in the 21st century in terms of how we designed and deployed projects for the community,” Sulit said.
Their design interest is concentrated in what they call Craft Studios — affordable housing, passive building design, and modular building.
Sulit, believes modular is a better-quality product compared to stick-built construction because it is created in a controlled environment by workers with a higher skill set than day workers on a construction site.
That could be why the delivery method, as Sulit calls modular building, is starting to escalate in the construction world. “Modular practice is still evolving,” Sulit said. “It evolves with the code, new materials, and new strategies.”
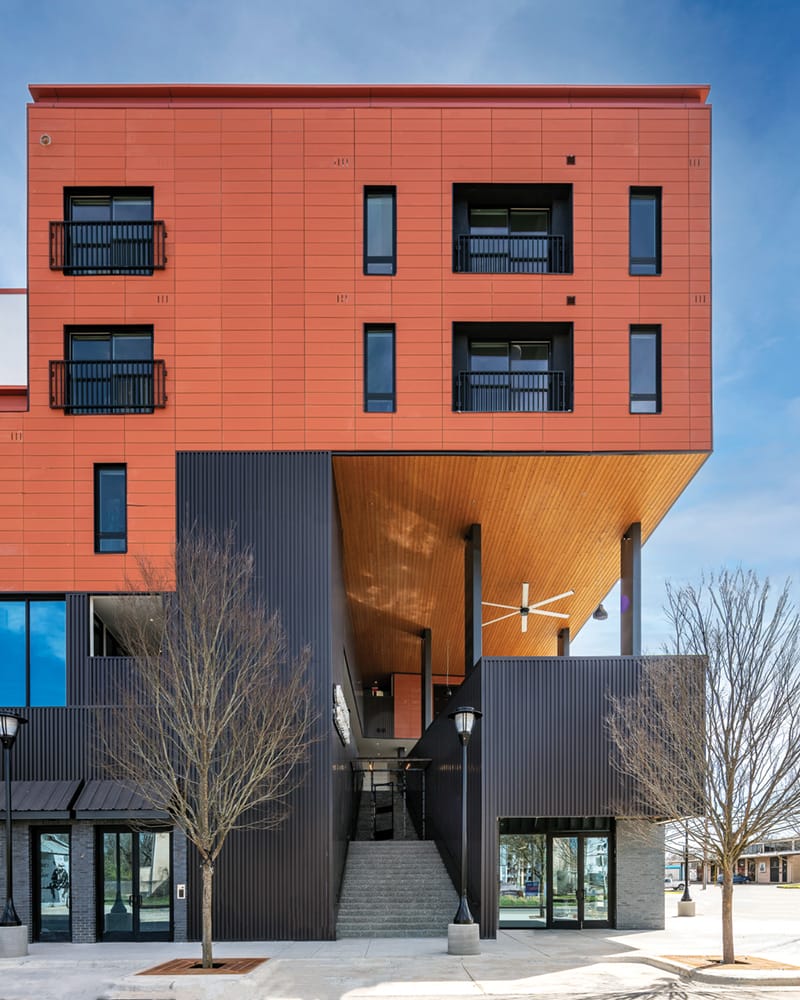
Designed by Forge Craft Architecture + Design, built by Z Modular.
The Importance of Modular Building Codes and Standards
Currently there aren’t any modular-specific building codes beyond standard building code. Modular design and building is usually governed by the state in which the modular building is deployed.
But every code is subject to local amendments. And a municipality and a state may not necessarily use the same version of the International Building Codebook (IBC). For example, the state of Indiana uses the 2014 IBC code while the city of Austin, Texas is now adopting the 2024 code.
It’s left to the architect to reconcile the codes, which takes time, especially if those in charge of regulations aren’t familiar with modular construction. This is an area of concern, because one of the big advantages of modular construction is that it speeds the construction process up to 40% faster than conventional construction.
Codes are developed to standardize the building process, so the finished product lives up to a certain standard of performance. But codes must also align with the current socioeconomic atmosphere of where those buildings will be located. For different climates, geographic and even geopolitical contexts, the same code is often interpreted in different ways.
“I don’t think we are ever going to have a universal code because where we build and the people who use modular buildings are so varied,” Sulit said. “The challenge is how to take this universal concept and apply it to multiple places where the codes differ. What creates the illusion that the codes aren’t keeping up with modular is that those codes exist for other reasons than to serve the modular industry.”
Almost every project requires a creative or innovative design solution to ensure it is code compliant.
One example is UL fire ratings, which currently assume everything is stick-built. The architect needs to show that the modular project methodology is equivalent to the standard methodology.
Typically, this means getting engineers, consultants, and the people in charge of regulatory compliance together. They all study
the issue, and once they agree it works, the project can move forward. It’s not an ideal situation since it can delay the project, but it’s a necessary one for now.
“No one’s trying to get around the code and no one should be,” Sulit said. “We’re just trying to interpret it in a way that aligns with the modular processes.”
Modular Specific Contracts Can Help
Meanwhile, newly developed project contracts can help standardize the modular building processes and aid communication between modular stakeholders.
“There’s a clamor now for finding ways to standardize our processes for multiple reasons,” Sulit said. “One is so we can develop processes consistent from project to project. Project contracts also allow us to establish some parity in how we price and deliver buildings.”
Today there is no established recorded modular process that everyone agrees to. But having a contract helps define the instruments of service, the project scope, and fee structures.
In the past design architects have modified these four contracts to align with the modular delivery method.
- The B101, an American Institute of Architects (AIA) long form standard agreement between the owner and the architect.
- The B105, a short document for smaller jobs.
- The B143, the contract between the architect and the design-builder.
- The Master Agreement Contract, a flexible, comprehensive contract between the contractor and client.
From an architect’s point of view, the B143 contract is especially beneficial.
“As an architect, I could serve as the architect of record and also the modular architect,” Sulit said. “That’s ideal from my standpoint because then I get to manage the whole process.”
This April, the AIA released four new contracts focused on volumetric modular construction at MBI's 2025 World of Modular conference.
Sulit is looking forward to working with the AIA’s new B181 contract, a standard agreement between the owner and the architect. It’s the equivalent of the B101 but designed specifically for the modular industry.
“Now we have something we can utilize to further improve our delivery and helps us manage our organizational structure better moving forward,” he said.
Recently, the MBI with ConsensusDocs also developed two new contracts for modular building for the project owner and the manufacturer.
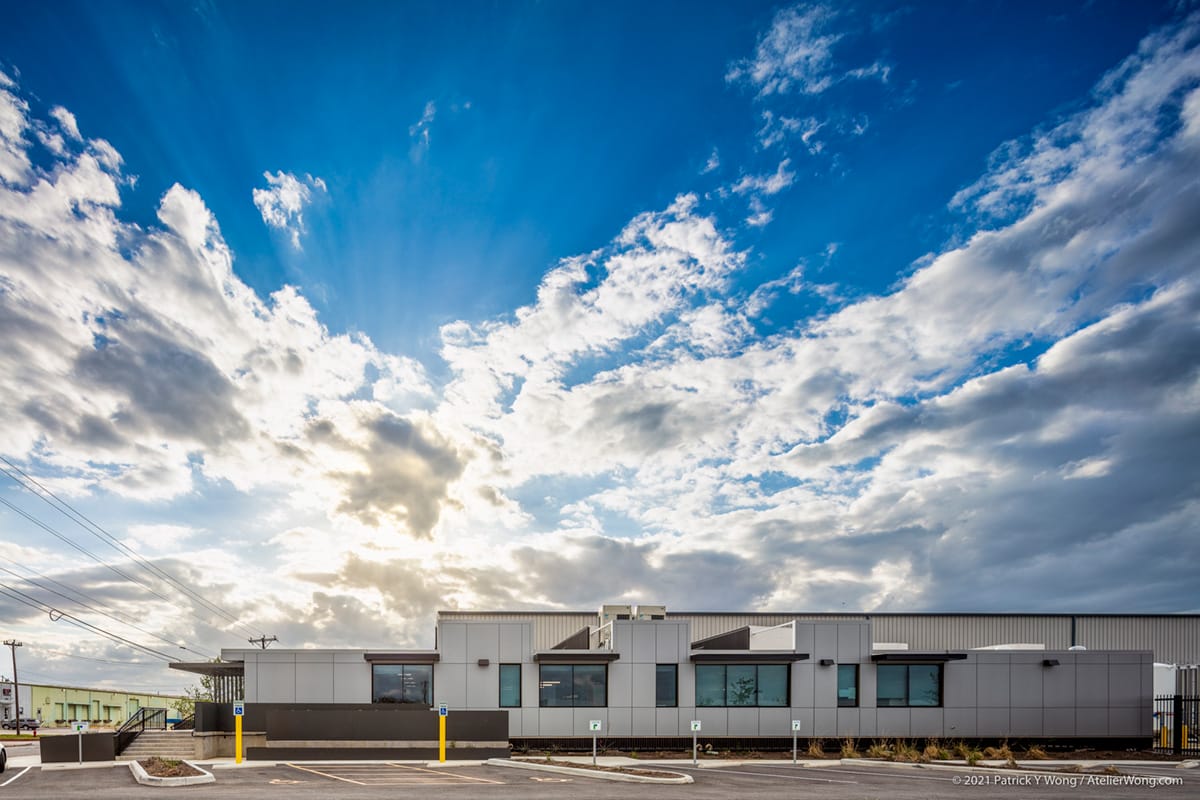
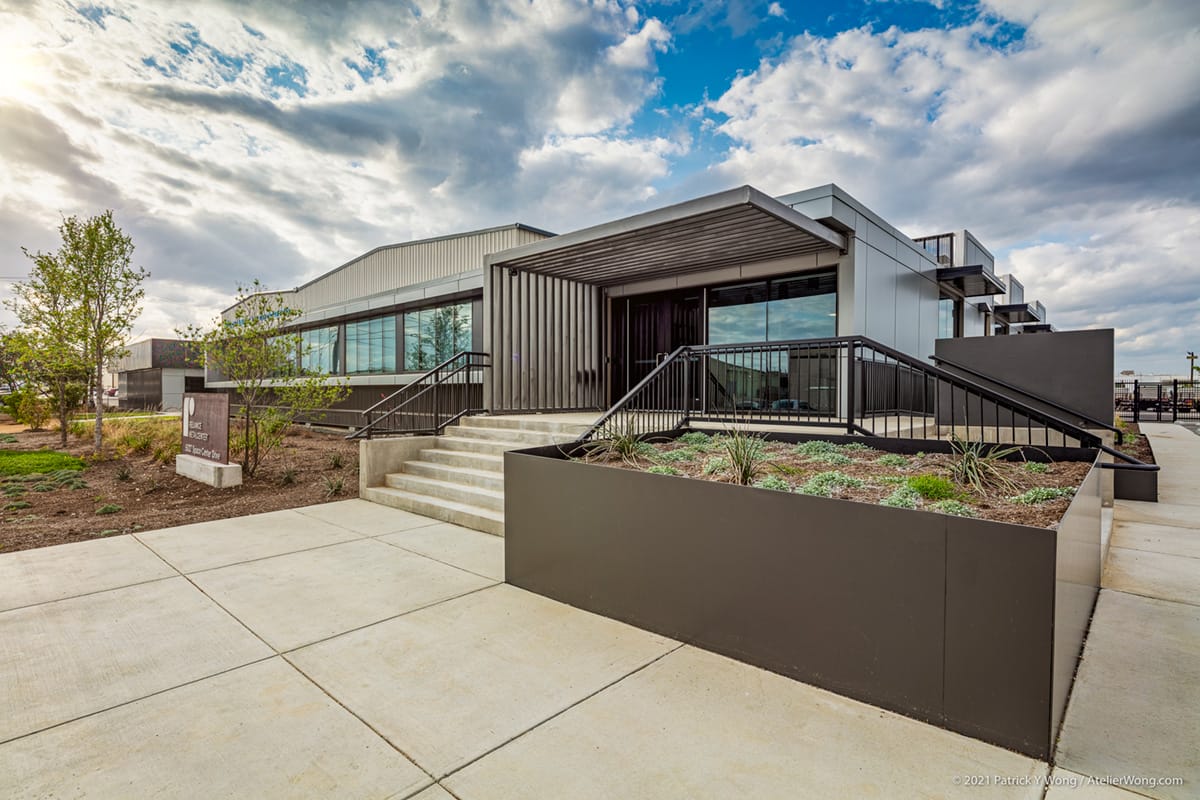
Reliance Metalcenter was awarded 1st Place in the Permanent Modular Office (under 10,000 sq.ft.) category at MBI’s 2022 Awards of Distinction. Built by Z-Modular.
Related Listening:
Contract Clarity: Templates Tailored for Modular Construction Success w/ AIA Contract Documents
Listen as Sara Betancorth from AIA Contract Documents and Sal Verrastro from Spillman Farmer Architects detail how these new contracts were created through years of collaboration between architects, attorneys, and industry experts. Now available to the public, these contracts represent a balanced approach that acknowledges the realities of modern modular construction. The result? Contracts that reduce risk, clarify responsibilities, and ultimately facilitate smoother project delivery for all stakeholders.
Intellectual Property’s Role in Modular Architecture
Under conventional construction contracts, which are based on common law, architects produce designs or contract documents, and they own copyright to their instruments of service. The owner receives a limited license to use those designs for that project only once.
With modular construction the potential for repeating the designs is inherent in the delivery method.
“The closest thing I’ve seen that addresses this is this concept called derivative rights, which is when you’re creating new work from existing work,” Sulit said.
The new B181 contract recognizes that architects will design a building and will utilize those drawings for one time for this project. Their instruments of service are not turned over to the project owner to be repeated beyond the contract. To do that would require a continuation, negotiation, licensing fee, or royalty.
The topic of intellectual property in the modular industry is a polarizing question. Some feel the design and all the details should be open source. Others feel everything should be considered proprietary.
“This is a conversation that is going to continue for quite some time in our field,” Sulit said.
He considers bracing systems and components that are unique to a company as well as anything that needs to be tested could arguably be deemed intellectual property for that company, since the company did all the engineering and spent money to have something tested.
A company could have a certain design philosophy that could be part of its intellectual property, but manufacturing processes are trickier to determine.
“If a company wants to own their own intellectual property, I think the proper way to do it is to take our designs and invest the proper amount of research and dollars to produce their own manufacturing documentation,” Sulit said. “That way they can produce the product over and over again consistently. But that can be expensive.”
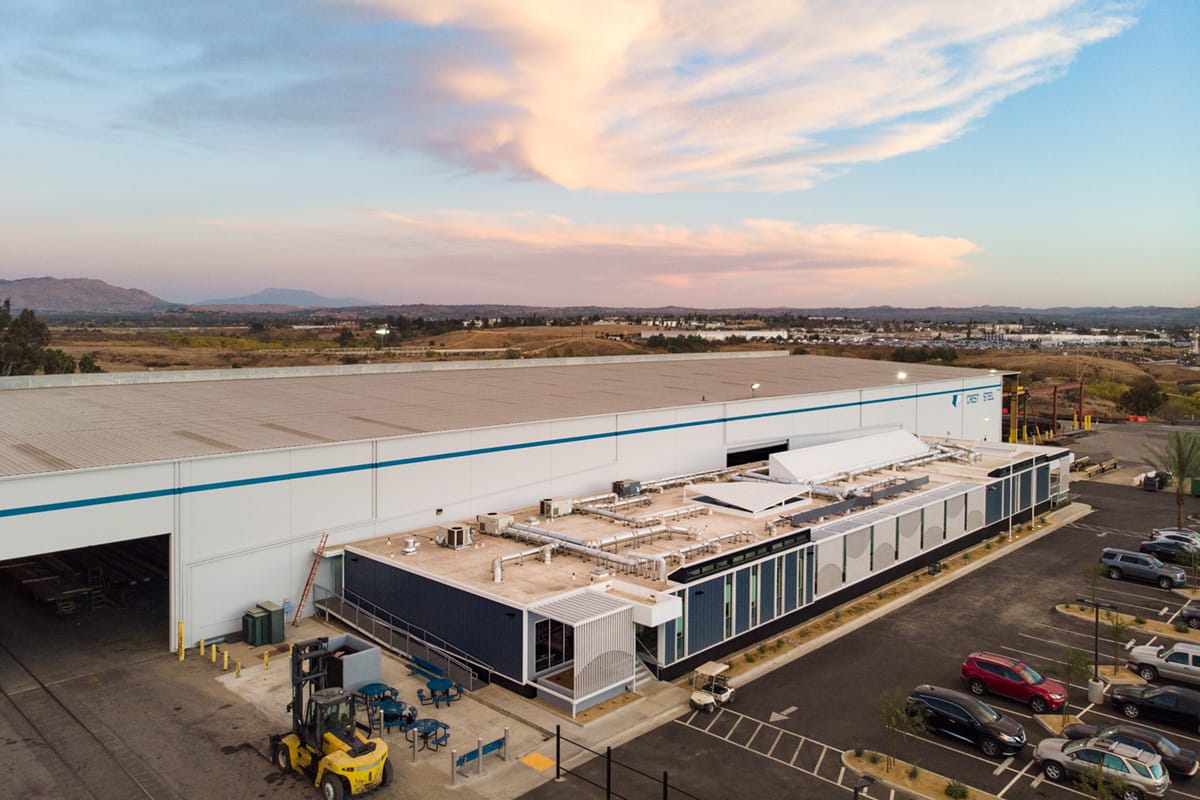
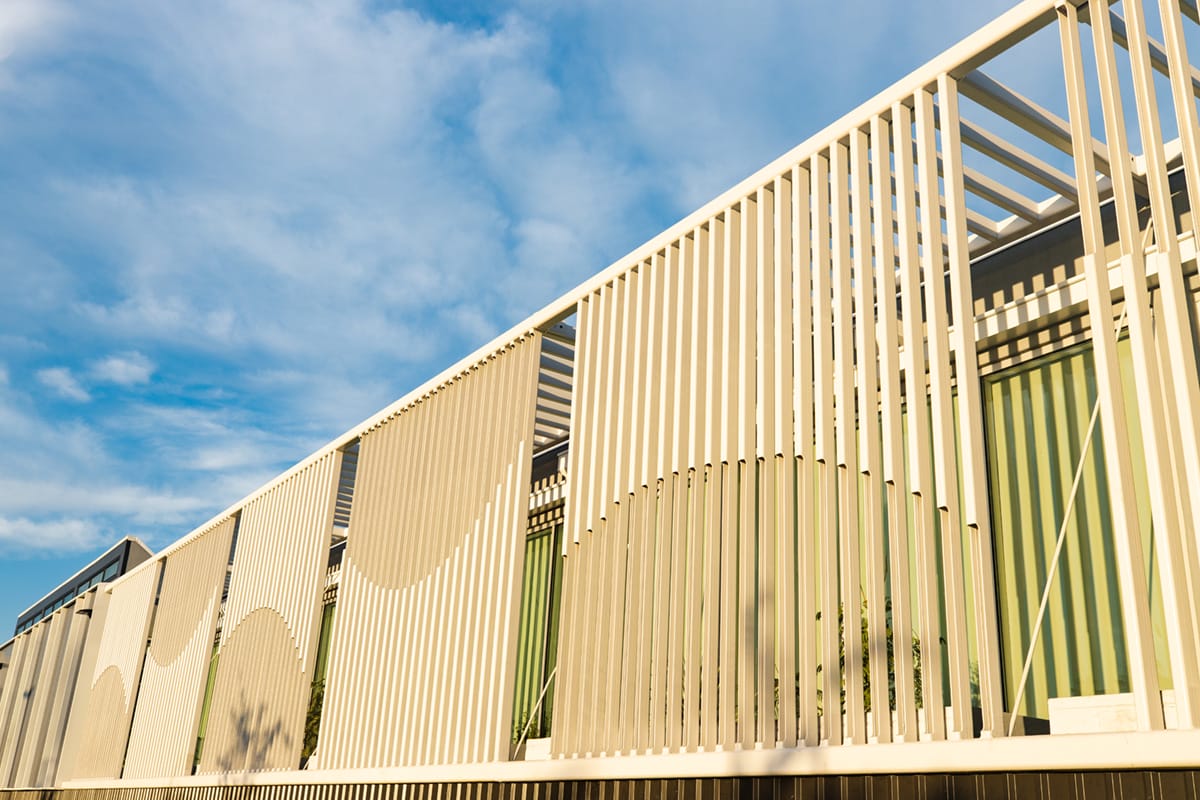
Designed by Forge Craft Architecture + Design. Built by Z Modular.
How does intellectual property distinguish between custom-designed features and standard details?
Conventional designs are typically constructed using best practices, so the architect doesn’t have to go deep into the detailing. These documents fall under LOD (level of development) 300.
Most architects can take a design up to LOD 350, which is a higher level of detailing.
“At that point, I have to tell them to get their own engineers and their own design team to record this if they want it to be a standard product that they can guarantee,” Sulit said. “If I work with that company down the road again, they could give me those standard details and I would work with them. That’s how I think the process should work.”
Advice for New Architects Entering the Modular Space
Sulit suggests architects first study conventional contracts to understand the protections they provide. That will make it easier to comprehend the new modular contracts.
Secondly, they should gain as much exposure to the field of modular construction as they can and talk with the companies involved to determine where their work ends and the other entities’ work begins. Then, dedicate your team to full immersion.
“My biggest superpower is that I know what it takes to get a plant certified,” Sulit said. “Understanding the certification process is a helpful thing to learn, but it’s a much deeper dive into the code and the building systems. Are you prepared for the commitment?”
About the Author: Shari Held is an Indianapolis-based freelance writer who has been covering the construction industry for more than 20 years.
More from Modular Advantage
Oregon’s Prevailing Wage Proposal: A Wake-Up Call for Modular Construction
Should House Bill 2688A become law, building projects would increase in price, face longer completion timelines, and produce significantly more waste. The bill also incentivizes contract awards to out of state businesses who would not reinvest their earnings into the local Oregon economy.
Behind the Design of Bethany Senior Terraces, NYC’s First Modular Passive House Senior Housing Project
As more developers seek to meet new regulations for energy efficiency, the team at Murray Engineering has set a new record. With the Bethany Senior Terraces project, Murray Engineering has helped to develop NYC’s first modular structure that fully encompasses passive house principles — introducing a new era of energy efficiency in the energy-conscious city that never sleeps.
How LAMOD is Using Modular to Address Inefficiency, Sustainability, and the Future of Construction
As developers, designers, and contractors seek to understand the evolving needs of the modular industry, no one is as well-versed in the benefits of going modular as Mārcis Kreičmanis. As the co-founder and CBDO of LAMOD in Riga, Latvia, Mārcis has made it his ultimate goal to address the inefficiencies of traditional construction.
From Furniture Builder to ‘Activist Architect’: Stuart Emmons’ Unique Journey
Stuart Emmons was fascinated by buildings at a young age. He remembers building sand cities with his brother during trips to the Jersey shore. His father gave him his first drawing table at the age of ten. Today, he is an experienced architect who received his FAIA in June 2025. The road he took is unique, to say the least.
Eisa Lee, the “Bilingual” Architect
Now as the founder of XL
Architecture and Modular Design in Ontario, Canada, she applies not just her education as a traditional architect but an entire holistic view on modular design. It’s this expansive view that guides her work on being a true partner that bridges the gap between architects and modular factories as they collaborate on the design process.
Tamarack Grove Engineering: Designing for the Modular Sector
The role of a structural engineer is crucial to the success of a modular project, from initial analysis to construction administration. Tamarack Grove offers structural engineering services — project analysis, plan creation, design creation, and construction administration — for commercial, manufacturing, facilities, public services, and modular. Modular is only one market sector the company serves but it is an increasingly popular one.
Engineer Masters the Art of Listening to His Customers
Since founding Modular Structural Consultants, LLC. in 2014, Yurianto has established a steady following of modular and container-based construction clients, primarily manufacturers. His services often include providing engineering calculations, reviewing drawings, and engineering certification
Inside College Road: Engineering the Modules of One of the World’s Tallest Modular Buildings
College Road is a groundbreaking modular residential development in East Croydon, South London by offsite developer and contractor, Tide, its modular company Vision Volumetric (VV), and engineered by MJH Structural Engineers.
Design for Flow: The Overlooked Power of DfMA in Modular Construction
Unlocking higher throughput, lower costs, and fewer redesigns by aligning Lean production flow with design for manufacturing and assembly.
Choosing the Right Ramp
Modular construction offers a compelling alternative to traditional methods for designing and building ADA and IBC-compliant entrances. By addressing the challenges of traditional construction, such as time-consuming processes, unavailable specialized labor, and variable field conditions, modular solutions provide a more efficient, cost-effective, and reliable approach.