Design for Flow: The Overlooked Power of DfMA in Modular Construction
Unlocking higher throughput, lower costs, and fewer redesigns by aligning Lean production flow with design for manufacturing and assembly.
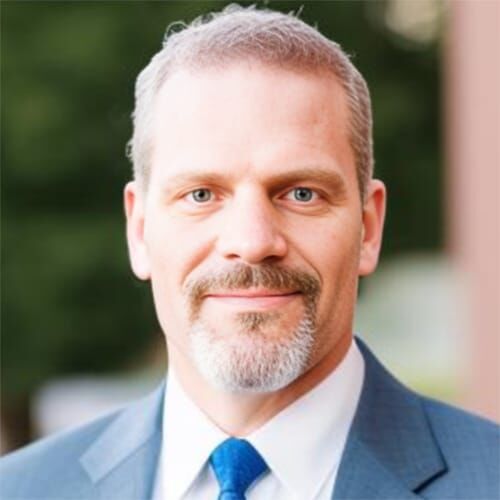
Daniel Small is the founder & CEO of Da Vinci Consulting.
The Missed Opportunity in Modular Design
Modular construction has reached an inflection point. As factories push to scale, many are realizing that traditional design approaches — even when optimized for assembly — often fall short of supporting true manufacturing flow. Despite growing awareness of Design for Manufacturing and Assembly (DfMA), too many designs are still conceived without consideration for takt time, station balance, or smooth product flow. The result? Bottlenecks, rework, and inconsistent throughput.
It doesn’t have to be this way. By aligning DfMA efforts with Lean production principles, modular manufacturers can achieve transformative gains in speed, efficiency, and quality. This article explores how to take DfMA beyond ease-of-assembly and turn it into a cornerstone of flow-based modular design.
What “Design for Flow” Really Means
In Lean thinking, “flow” refers to the smooth, uninterrupted movement of materials and work-in-progress through a value stream — ideally one piece at a time, paced to customer demand (takt time). Flow minimizes waste, reduces lead times, and enables predictable, scalable production.
In modular factories, flow is often disrupted by designs that, while architecturally sound, are operationally clunky. Examples include:
- Modules that require non-sequential assembly steps
- Complex MEP layouts that slow down installation
- Heavy assemblies needing special handling or off-line work
To design for flow, we must start with a clear understanding of how the module will be built, moved, and finished in a factory setting. That means designing around station rhythm, minimizing special handling, and simplifying task sequencing. Good flow also depends on predictability. When design enables consistent outcomes with fewer variables, every downstream process becomes smoother.
Designing for flow also means removing decisions from the floor. A well-designed product doesn’t force workers to interpret or improvise. It standardizes their actions, allowing them to focus on execution. In this way, flow isn’t just about speed — it’s about removing friction.
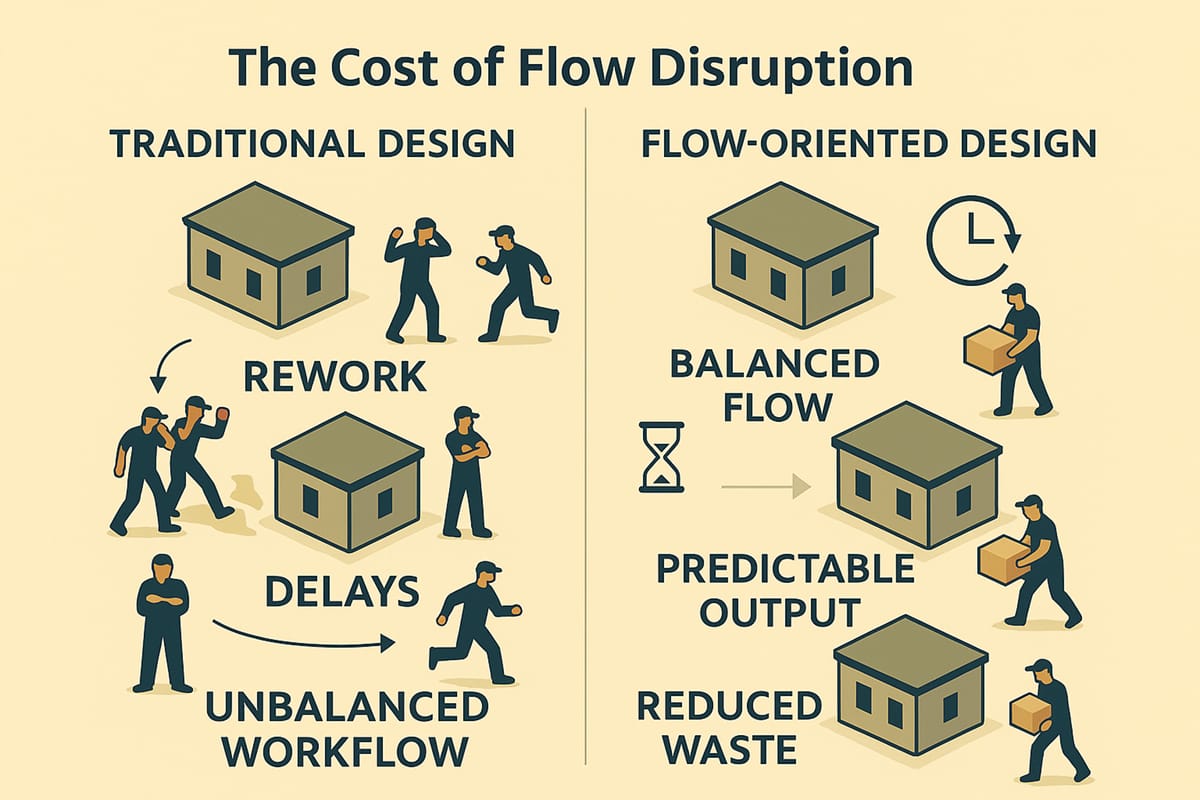
Traditional design causes chaos; flow-oriented design enables predictable, efficient modular production.
Done well, DfMA also enables flexible scalability. Once a system of flow-friendly, factory-fit modules is developed, it can be repeated, adapted, or mass-customized with minimal disruption. This is crucial for firms trying to meet rising demand without overextending resources.
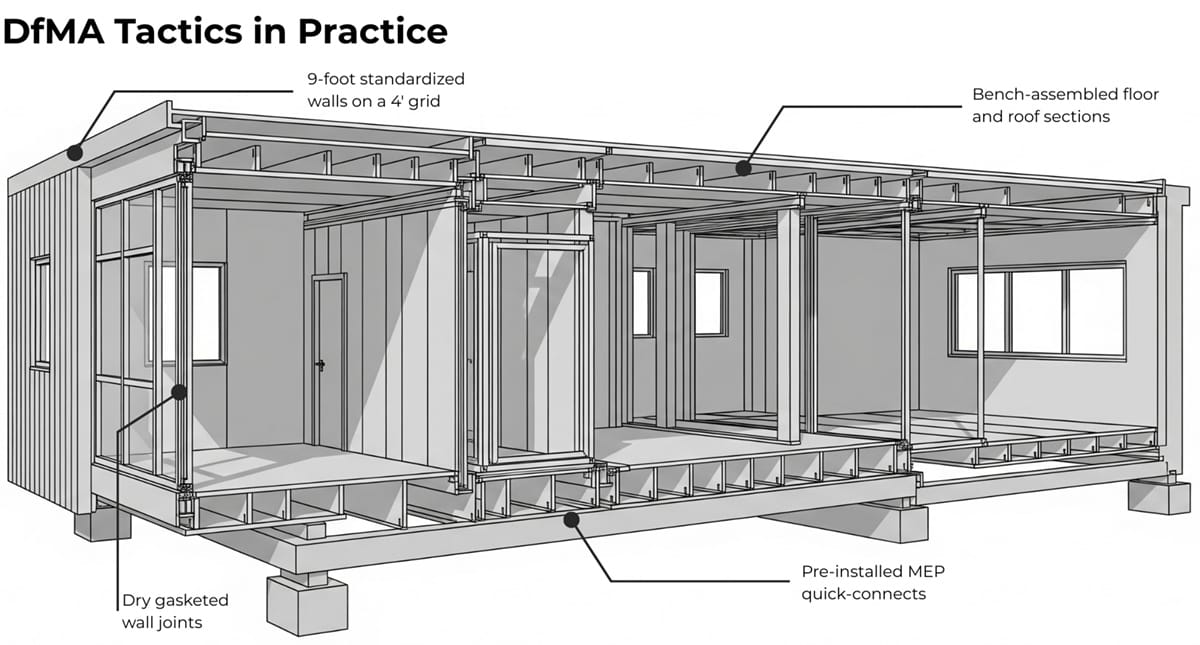
Key DfMA features that support modular flow — standardized grids, bench-built assemblies, and plug-and-play MEP.
Case Snapshot: A Design That Broke the Flow
Imagine a modular factory launching a new line of multifamily units. The design includes intricate MEP pathways through tight chase walls, along with ceiling drops requiring a multi-step buildout. On paper, the modules look great. But on the floor, workers must deviate from their normal sequence, wait for parts, and perform overhead work that could have been done more efficiently at bench height.
Despite a beautiful end product, the factory experiences a 40% reduction in throughput and a sharp rise in punch list items. Why? The design was never mapped against the factory workflow. It prioritized final appearance over process simplicity.
This is not uncommon. Many modular projects are designed with site assembly or architectural elegance in mind, but without fully considering factory sequencing. The cost of this oversight is usually borne by production teams — who then improvise, slow down, or escalate quality issues. Many modular projects are designed with site assembly or architectural elegance in mind, but without fully considering factory sequencing. The cost of this oversight is usually borne by production teams — who then improvise, slow down, or escalate quality issues.
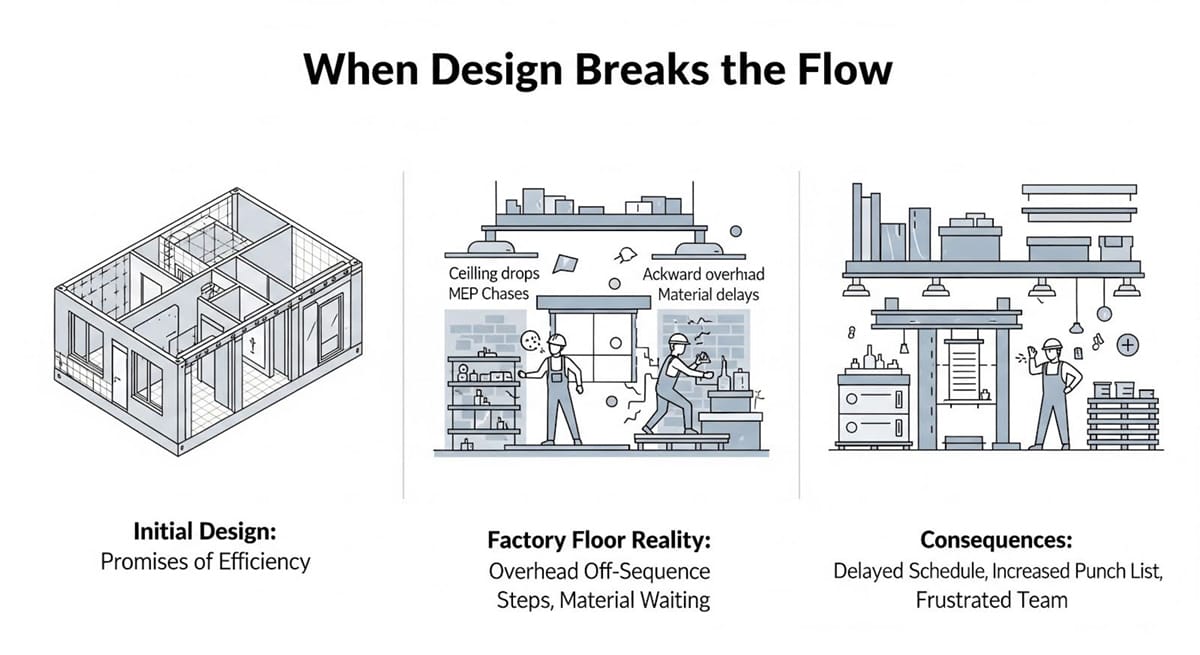
Poor alignment between design and production leads to delays, rework, and overwhelmed crews — while flow-based design avoids chaos.
Integrated Approach: Co-Designing for Flow + Assembly
To avoid these pitfalls, DfMA must be paired with flow mapping from the outset. Here’s how modular firms can align design and production:
- Involve factory stakeholders early: Bring manufacturing, logistics, and quality leads into the schematic design phase. They’ll spot issues architects miss and flag features that increase takt time.
- Design around takt time: If your factory has a 4-hour takt, make sure the module can be completed in repeatable, leveled work packages within that window. Design tasks to fit tactically within each station’s cadence.
- Use a standardized grid:
A 4’/2’ planning grid aligned with material sizes reduces cuts, waste, and layout errors. Standardization also supports training, cross-functional flexibility, and procurement efficiency. - Simplify connections: Use plug-and-play MEP assemblies, universal headers, and snap-together framing details. Minimize fastener variety and ensure all joints are tool-accessible without repositioning.
- Build in layers: Enable each station to complete its layer of work fully before the module moves on. Avoid any task that requires a module to be brought back upstream or held out of flow.
These actions require shifting from a siloed to an integrated design process. Architects, engineers, and production teams must co-develop solutions. When they do, the factory becomes a co-creator of value rather than a downstream constraint.
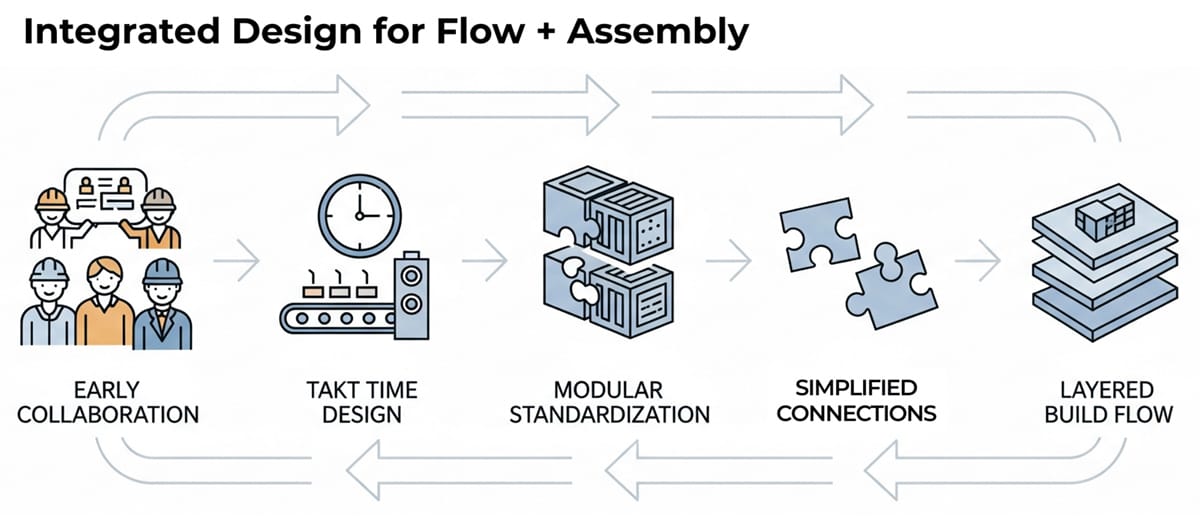
Co-design loop integrating factory flow principles into every design phase — from collaboration to layered production.
The ROI of Flow-Driven DfMA
When done right, designing for flow unlocks impressive returns:
- Throughput increases of 2X to 5X, even without adding labor or equipment
- Cycle time reductions of 30-50%
- Dramatic quality improvements, due to reduced handling and rework
- Happier teams, with clearer roles and less firefighting
There are also indirect gains: improved factory morale, fewer change orders, and stronger client trust. When output becomes predictable, sales teams can promise confidently — and deliver.
Importantly, these gains scale. Flow-based DfMA creates a resilient operational backbone that allows for site variability without sacrificing internal consistency. That’s a key to achieving modular’s promise of mass customization.
DfMA Is Not Enough Without Flow
DfMA is a powerful tool — but only when wielded in service of Lean flow. The modular industry can’t afford to treat design and manufacturing as separate domains. When they’re integrated, factories hum, projects deliver on time, and customers get exactly what they were promised.
If we want modular construction to fulfill its potential, we must move beyond designing for assembly and start designing for flow. That means embedding flow principles in the earliest design conversations, empowering production teams to shape those designs, and viewing every product through the lens of factory fit and sequencing.
The future of modular isn’t just smarter design — it’s synchronized design. And that begins with DfMA that flows.
More from Modular Advantage
Oregon’s Prevailing Wage Proposal: A Wake-Up Call for Modular Construction
Should House Bill 2688A become law, building projects would increase in price, face longer completion timelines, and produce significantly more waste. The bill also incentivizes contract awards to out of state businesses who would not reinvest their earnings into the local Oregon economy.
Behind the Design of Bethany Senior Terraces, NYC’s First Modular Passive House Senior Housing Project
As more developers seek to meet new regulations for energy efficiency, the team at Murray Engineering has set a new record. With the Bethany Senior Terraces project, Murray Engineering has helped to develop NYC’s first modular structure that fully encompasses passive house principles — introducing a new era of energy efficiency in the energy-conscious city that never sleeps.
How LAMOD is Using Modular to Address Inefficiency, Sustainability, and the Future of Construction
As developers, designers, and contractors seek to understand the evolving needs of the modular industry, no one is as well-versed in the benefits of going modular as Mārcis Kreičmanis. As the co-founder and CBDO of LAMOD in Riga, Latvia, Mārcis has made it his ultimate goal to address the inefficiencies of traditional construction.
From Furniture Builder to ‘Activist Architect’: Stuart Emmons’ Unique Journey
Stuart Emmons was fascinated by buildings at a young age. He remembers building sand cities with his brother during trips to the Jersey shore. His father gave him his first drawing table at the age of ten. Today, he is an experienced architect who received his FAIA in June 2025. The road he took is unique, to say the least.
Forge Craft Architecture + Design: Codes, Contracts, and Intellectual Property
Founding Principal and Director of Modular Practice for Forge Craft Architecture + Design, Rommel Sulit, discusses the implications of codes, contracts, and intellectual property on
modular construction.
Eisa Lee, the “Bilingual” Architect
Now as the founder of XL
Architecture and Modular Design in Ontario, Canada, she applies not just her education as a traditional architect but an entire holistic view on modular design. It’s this expansive view that guides her work on being a true partner that bridges the gap between architects and modular factories as they collaborate on the design process.
Tamarack Grove Engineering: Designing for the Modular Sector
The role of a structural engineer is crucial to the success of a modular project, from initial analysis to construction administration. Tamarack Grove offers structural engineering services — project analysis, plan creation, design creation, and construction administration — for commercial, manufacturing, facilities, public services, and modular. Modular is only one market sector the company serves but it is an increasingly popular one.
Engineer Masters the Art of Listening to His Customers
Since founding Modular Structural Consultants, LLC. in 2014, Yurianto has established a steady following of modular and container-based construction clients, primarily manufacturers. His services often include providing engineering calculations, reviewing drawings, and engineering certification
Inside College Road: Engineering the Modules of One of the World’s Tallest Modular Buildings
College Road is a groundbreaking modular residential development in East Croydon, South London by offsite developer and contractor, Tide, its modular company Vision Volumetric (VV), and engineered by MJH Structural Engineers.
Choosing the Right Ramp
Modular construction offers a compelling alternative to traditional methods for designing and building ADA and IBC-compliant entrances. By addressing the challenges of traditional construction, such as time-consuming processes, unavailable specialized labor, and variable field conditions, modular solutions provide a more efficient, cost-effective, and reliable approach.