Panel Built Provides Custom Modular Enclosure for Major Beverage Manufacturer
In October 2023, CE Thurston contacted Panel Built Inc., a modular building company, on behalf of a major beverage manufacturer. The manufacturer a place to house their large facility crane and a means of expanding office space within their existing plant. Panel Built Inc. was tasked with delivering a high-quality, functional structure that could meet those needs and do so quickly and efficiently.
The Challenge
The challenge was twofold. Firstly, Panel Built needed to create a spacious enclosure that could accommodate a large facility crane. This enclosure required a design that provided ample storage space and integrated seamlessly with the existing infrastructure. Secondly, the structure needed to incorporate office space that offered personnel an unimpeded, 360-degree view of the factory floor. Achieving these objectives within a stringent timeline was essential to ensure minimal disruption to the manufacturer's operations.
About Panel Built Inc.: Panel Built was founded in 1995 by brothers Pat and Mike Kiernan and began with the construction of pre-manufactured buildings. Today, Panel Built offers a complete line of custom modular offices, mezzanines, security booths, pre-assembled exterior buildings, and cleanrooms. All our product lines are manufactured on-site in one of our state-of-the-art modular production facilities. We offer "A Better Way to Create Space" for all your building projects.
The Solution
Panel Built Inc. responded to this challenge with a comprehensive modular building solution. The team designed, fabricated, and installed a 37' x 27' enclosure with a mezzanine, effectively augmenting the available space by 1,365 square feet. The enclosure featured 45 surrounding windows, which ensured panoramic visibility of the factory floor and enhanced operational oversight.
Project Timeline and Quality Assurance
Despite the project's complexity and the need for rapid completion, Panel Built Inc. completed the structure within approximately three months from the date of the order. Throughout the process, the company maintained a steadfast commitment to quality, ensuring that every aspect of the structure met high standards of craftsmanship and functionality.
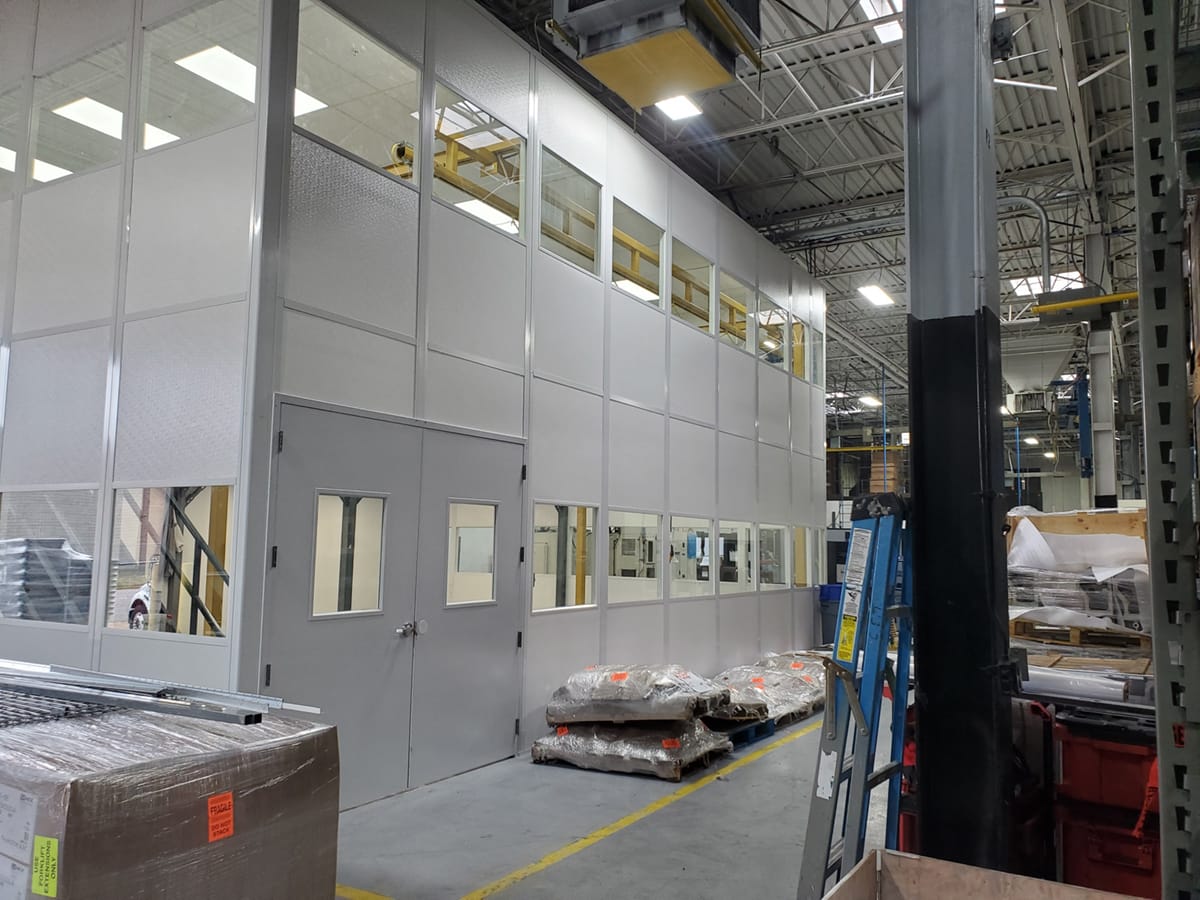
The completed modualr enclosure featured 45 surrounding windows, which ensured panoramic visibility of the factory floor and enhanced operational oversight.
Key Features of the Solution
Class A Interior Walls: The walls were crafted with 3" thick composite sandwich panels featuring 1/8" Fiberglass Reinforced Plastic on the exterior and interior surfaces, finished in pristine white. An aluminum extruded binder post system, positioned every 4', housed all electrical components, maintaining functionality and aesthetic coherence.
Ceiling: A suspended ceiling system spanning 945 square feet was implemented to integrate seamlessly with the existing structure. The Class "A" suspension system and acoustic materials enhanced the interior ambiance and provided a platform for essential utilities, including lighting, heating, ventilation, and air conditioning systems.
Doors and Windows: The building was equipped with double doors to facilitate the easy transportation of equipment. Entry points were outfitted with 20-gauge insulated steel doors featuring half-glass panels to allow natural light to penetrate the interior. The interior picture windows were glazed with 1/4" clear tempered glass, ensuring complete visibility while maintaining safety standards.
Electrical Package: The entire enclosure was pre-wired with a modular electrical package. This package included wall switches, duplex receptacles, and 110-volt LED fixtures, allowing for future HVAC installation. The modular wiring allowed for easy set-up of the building's electrical grid, saving the project time and sparing facility installers the risk of electrical injury.
Mezzanine: The mezzanine was engineered to withstand 125 pounds per square foot, meeting the standards for a loading mezzanine system. This multifunctional space accommodated storage needs and housed a dedicated in-plant office. The elevated platform featured steel decking sub-flooring and resilient recessed decking for enhanced durability.
Stair Systems & Handrails: Safety was a top priority for Panel Built Inc. As such, the 42" tall railings and diamond plate stairs were designed to meet factory, storage use groups, and OSHA standards. The stair system and handrails received a powder coat finish, with the handrails colored a bright safety yellow for optimal visibility.
Conclusion
Panel Built Inc.'s innovative approach and modular building techniques effectively solved the major beverage manufacturer's dual challenge of storage and office space expansion. This case study exemplifies the capabilities of modular construction in addressing complex industrial needs and shows Panel Built Inc.'s expertise in delivering tailored solutions that enhance operational efficiency and safety.
More from Modular Advantage
Behind the Design of Bethany Senior Terraces, NYC’s First Modular Passive House Senior Housing Project
As more developers seek to meet new regulations for energy efficiency, the team at Murray Engineering has set a new record. With the Bethany Senior Terraces project, Murray Engineering has helped to develop NYC’s first modular structure that fully encompasses passive house principles — introducing a new era of energy efficiency in the energy-conscious city that never sleeps.
How LAMOD is Using Modular to Address Inefficiency, Sustainability, and the Future of Construction
As developers, designers, and contractors seek to understand the evolving needs of the modular industry, no one is as well-versed in the benefits of going modular as Mārcis Kreičmanis. As the co-founder and CBDO of LAMOD in Riga, Latvia, Mārcis has made it his ultimate goal to address the inefficiencies of traditional construction.
From Furniture Builder to ‘Activist Architect’: Stuart Emmons’ Unique Journey
Stuart Emmons was fascinated by buildings at a young age. He remembers building sand cities with his brother during trips to the Jersey shore. His father gave him his first drawing table at the age of ten. Today, he is an experienced architect who received his FAIA in June 2025. The road he took is unique, to say the least.
Forge Craft Architecture + Design: Codes, Contracts, and Intellectual Property
Founding Principal and Director of Modular Practice for Forge Craft Architecture + Design, Rommel Sulit, discusses the implications of codes, contracts, and intellectual property on
modular construction.
Eisa Lee, the “Bilingual” Architect
Now as the founder of XL
Architecture and Modular Design in Ontario, Canada, she applies not just her education as a traditional architect but an entire holistic view on modular design. It’s this expansive view that guides her work on being a true partner that bridges the gap between architects and modular factories as they collaborate on the design process.
Tamarack Grove Engineering: Designing for the Modular Sector
The role of a structural engineer is crucial to the success of a modular project, from initial analysis to construction administration. Tamarack Grove offers structural engineering services — project analysis, plan creation, design creation, and construction administration — for commercial, manufacturing, facilities, public services, and modular. Modular is only one market sector the company serves but it is an increasingly popular one.
Engineer Masters the Art of Listening to His Customers
Since founding Modular Structural Consultants, LLC. in 2014, Yurianto has established a steady following of modular and container-based construction clients, primarily manufacturers. His services often include providing engineering calculations, reviewing drawings, and engineering certification
Inside College Road: Engineering the Modules of One of the World’s Tallest Modular Buildings
College Road is a groundbreaking modular residential development in East Croydon, South London by offsite developer and contractor, Tide, its modular company Vision Volumetric (VV), and engineered by MJH Structural Engineers.
Design for Flow: The Overlooked Power of DfMA in Modular Construction
Unlocking higher throughput, lower costs, and fewer redesigns by aligning Lean production flow with design for manufacturing and assembly.
Choosing the Right Ramp
Modular construction offers a compelling alternative to traditional methods for designing and building ADA and IBC-compliant entrances. By addressing the challenges of traditional construction, such as time-consuming processes, unavailable specialized labor, and variable field conditions, modular solutions provide a more efficient, cost-effective, and reliable approach.