The Building Industry Needs a Moonshot Speech
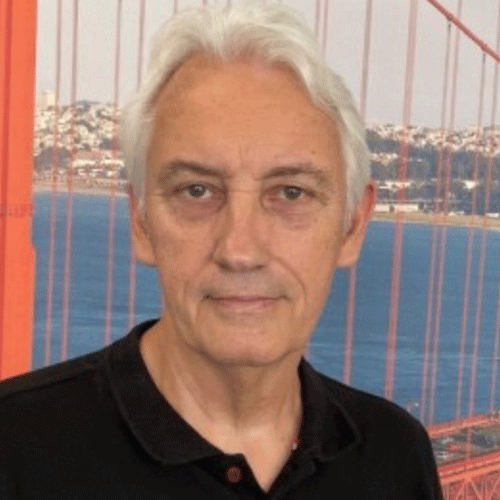
Carel van Duuren is the founder of True Modular Buildings.
In his “Moonshot” speech in 1962, President Kennedy challenged his fellow citizens to land a man on the moon and bring him safely back to earth before 1970. He showed leadership, reimagining human potential and progress, and this famous speech has been an inspiration for many to get things done.
Historically, the construction industry has underperformed (McKinsey June 2020). The building industry faces many problems such as slow production, a growing labor shortage, skills scarcity, high costs, a slow permitting process, the inability to scale, and the reluctance to use industrial approaches or new materials. In addition, the industry produces too much waste and CO2 emissions. Miscommunication, lack of skilled labor, and building regulations have slowed construction down and increased costs, with the result that for years not enough houses were built to meet the demand.
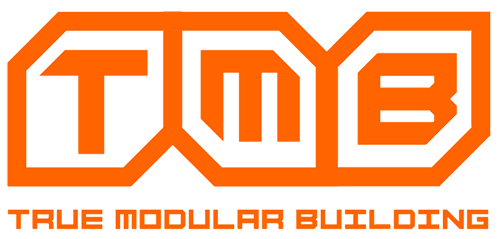
Due to an increasing world population, migration, and more one-person households, there is a growing demand for affordable housing. Worldwide, the design and construction of affordable housing is failing to meet demand, leaving low- and middle-income citizens with little choice but to accept substandard conditions or move in with parents or relatives. Many young people can’t find or pay for a home to start a family, while others resort to homelessness. Housing is not only a problem for young citizens, but also for people of all ages.
Builders need to comply with building regulations, which are not always clear and are subject to regional differences and the personal interpretations of inspectors. Because of this, flexibility and adaptability are crucial in any building system, conventional or modular.
A “Home-shot” speech that challenges citizens to remove lengthy procedures and “carefully” remove some of the mountain of red tape required for permitting before 2030 would certainly make a huge difference. We say ”carefully” remove red tape, because issues such as structural integrity, fire resistance, and health issues (e.g.no toxic materials), are paramount for builders and homeowners.
In my opinion, more than just changing building regulations is needed to speed up the building process. The sense of urgency and the mindset of those working in the building industry must change.
Who Cares and Why They Should
The building industry has not changed much over the past few decades. Many articles make comparisons between construction and the car industry, which is capable of mass production of quickly changing designs and models, including the latest gadgets and technology. In almost all of these comparisons, the building industry comes up short.
In my opinion, there has been no need for the building industry to change, and new initiatives have not been supported. For decades there has been no sense of urgency to change to a more advanced, less labor and material intensive way of building. Decarbonization is not a high priority for many builders (yet). The American dream of owning your own house ensures that there remains a huge demand for homes, which further ensures that the building industry will continue to build as they always have.
Real estate is still considered a good investment which appreciates in value over time, and a high percentage of billionaires gained their wealth through real estate transactions.
Why Modular
Modularization of the design and construction process simplifies design, creates more configuration and layout possibilities, and offers a universal solution to the problems of scarcity of housing and wasteful building methods.
In my opinion, moving conventional construction off-site into large factories, allowing workers to be able to work indoors under better conditions, and using the same building technology, is only conventional building done different. I embrace all builder initiatives to speed up the construction of homes, and don’t see them as competitors but as fellow warriors against the global housing crisis.
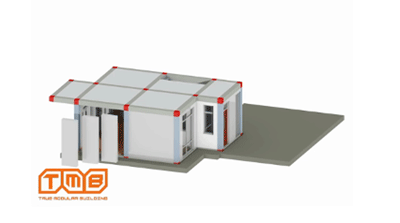
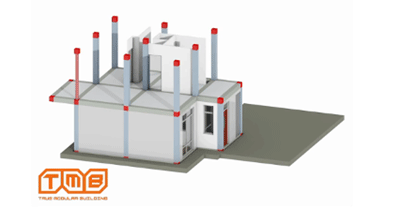
Basic example of the TMB system. Our buildings can be built in any shape or a variety of finishes.
It makes no sense to build large housing manufacturing factories for various reasons, including their massive overhead, lack of flexibility, fixed routing, the need for a steady pipeline of orders, transportation issues, and more. Large factories are not the solution to the affordable housing crisis.
Modern Methods of Construction (MMC) are accepted ways to speed up the building process. Although modular construction has not lived up to the industry’s expectations yet, many lessons have been learned and it’s obvious that the future of construction needs to be truly modular.
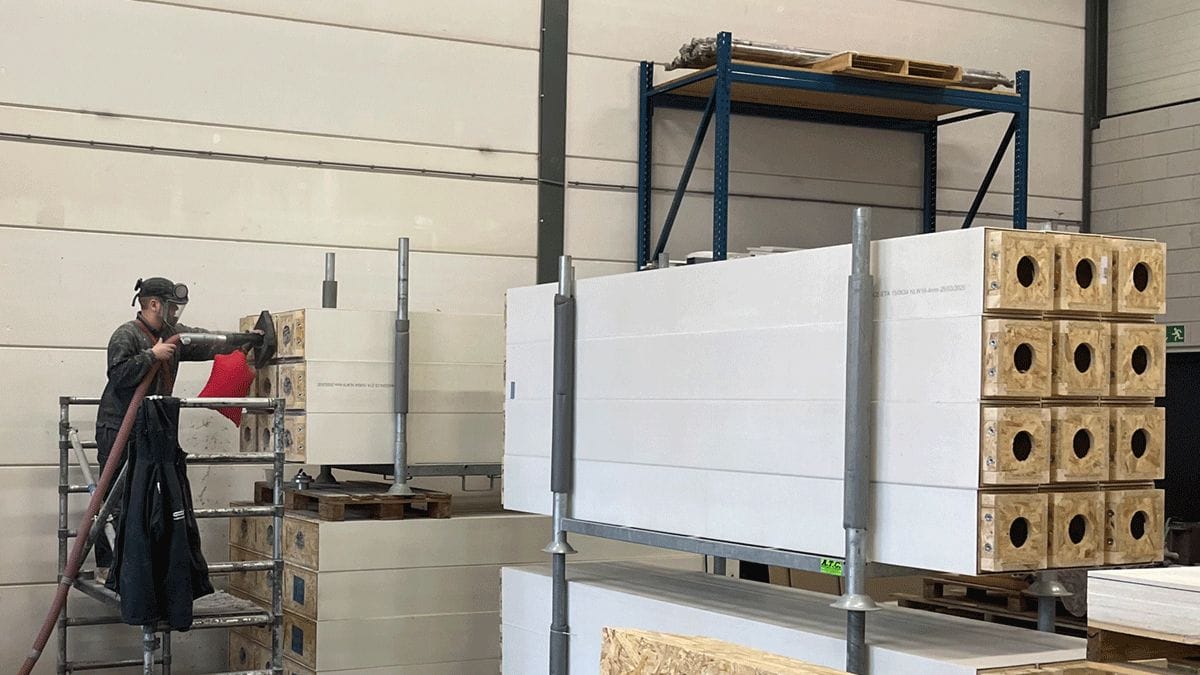
Bio-based insulation of prototype components.
For leaders in local government and communities it’s becoming more and more apparent that the building industry needs to change and speed up production to meet the need for affordable housing. People without shelter or affordable homes don’t care about the difference between conventional and modular building. For them the preferred method is the method that brings results.
What all builders have in common is that they are part of the fragmented construction value and supply chain and work with many stakeholders. Required, demanded, or preferred changes by local authorities through laws, different interpretations of those regulations (safety, fire, or zoning), and the changing preferences and needs of their customers need to be addressed. When different climate zones and the increasing number of natural disasters are added to the list, it’s obvious that the capacity for constant change must be a key factor in design and must be integrated into the process of production.
I believe it’s imperative to control the value and supply chain in order to streamline the production of residential homes. Vertical integration is not the answer (think Katerra). Asset light, quasi vertical integration is a better solution. This means no heavy investments in factories or equipment, ownership of the product specifications at each vertical level, and control of components via OEM manufacturing by co-makers and preferred suppliers.
Why Modular
“Panta Rhei”- words of a Greek philosopher, meaning that all phenomena are characterized by constant change. I strongly believe that affordable housing can only become a reality through true modularization and being able to easily adapt to constant change. This can only be achieved by creating a new building method and a modularized construction system, with control over the AEC process and the value and supply chains.
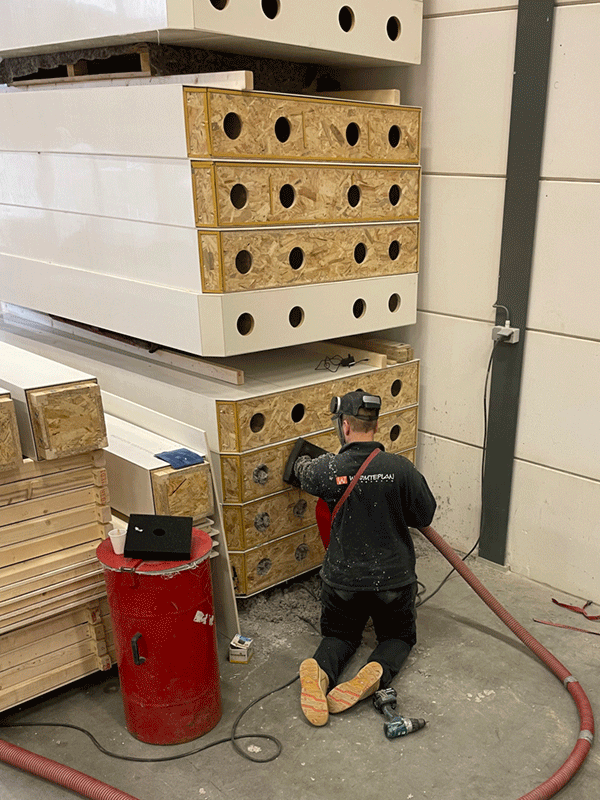
Construction of residential buildings is complex. Equally (or more) important than adaptability is structural integrity, especially with the changing climate. Structural integrity is achieved through smart construction methods that use add-ons, not by using more and heavier building materials.
Also important is Design for Manufacturing and Assembly (DFMA), which focuses on prioritizing both the ease of manufacturing building components and their simplified assembly into a final product.
Design for Disassembly allows for the reuse of building components and materials in a circular economy.
Finally, but not any less important, is Aesthetic Design, which focuses on pleasing qualities such as color, balance, pattern, shape, and scale.
We don't all want to live in a plain box. The distinction between the types and function of design (AEC) shows its importance as a key element in affordable housing. Construction needs holistic design, where forward thinking is a must.
Legacy Project
I am 71, have roots in auditing and finance, started various companies, and worked over 25 years as an interim manager in various business sectors where I gained a skill set for thinking about systems and solving business problems. I once read, “You don’t find your passion, your passion finds you,” and that’s exactly what happened. I spent the last four years creating a universal solution to to the scarcity of housing and wasteful building methods, which I call my legacy project, to put the wheels in motion. With the current industry knowledge and technology, the right funding structure, and co-ownership, it can be done. I think it’s easier than putting a man on the moon.
By keeping it simple, aligning with conventional methods and standards, and using systems thinking and reverse engineering, we developed a new method and building system which we call True Modular Building.
Orange Kit
The transformation of a construction project into an industrialized product approach involves scalable repeatable manufacturing processes and industrialization, which are enabled by utilizing a digital library of parts-based systems and templates. Physical components are created from their virtual representation with minimum tolerances. TMB believes in flexibility within standards, a balance between standardization and individualization which is rigid enough to allow for customized, cost effective, mass production but flexible enough to meet the needs of local circumstances and allow for inclusion of new materials.
By breaking our product architecture down and modularizing it, the building components can be arranged in different ways to create buildings to meet unique customer needs. Components are designed in greater detail and managed like pieces of a jigsaw puzzle. Functions, features, and performance levels are encapsulated in individual components, which are protected from each other by smart interfaces. That’s where the magic happens.

It starts with the careful design and selection of primitives, which are the fundamental building parts that cannot be broken down further. We engineer components with a minimum of parts, which are easy to assemble even without specific skills.
Catalogues and templates of building components and products allow for easy configuration, rather than engineering a building from scratch. The extra time we spend on engineering and prototyping these components results in a much smoother production/assembly process and lower failure cost. The different parts and features are grouped in product platforms, which we call Orange Kit. Why orange? The color orange is present throughout much of our Dutch culture.
Product Catalog
“People don’t know what they want until you show it to them,” said Steve Jobs in his now famous quote. TMB has created a product catalogue of over 75 building types to choose from. There are choices from a variety of building types, such as single-story, multifamily, low- or mid-rise apartments, and different floor plans. Each building type can be customized with bespoke parts from the Orange Kit library. The shape, size, and building finishes can be adapted to user preference. Our aim is not to build standalone houses, but attractive, affordable BTR residential communities.
The building components fit into our digital building kit, can be mass produced, and are easily assembled (think plug and play). The size of the components allows for easy flatpack transportation in containers to any place in the world. Our design is a streamlined, integrated approach with continuous improvement as a core tenet. All Orange Kit components can be repurposed and reused, closing the materials loop for a circular economy.
More from Modular Advantage
Behind the Design of Bethany Senior Terraces, NYC’s First Modular Passive House Senior Housing Project
As more developers seek to meet new regulations for energy efficiency, the team at Murray Engineering has set a new record. With the Bethany Senior Terraces project, Murray Engineering has helped to develop NYC’s first modular structure that fully encompasses passive house principles — introducing a new era of energy efficiency in the energy-conscious city that never sleeps.
How LAMOD is Using Modular to Address Inefficiency, Sustainability, and the Future of Construction
As developers, designers, and contractors seek to understand the evolving needs of the modular industry, no one is as well-versed in the benefits of going modular as Mārcis Kreičmanis. As the co-founder and CBDO of LAMOD in Riga, Latvia, Mārcis has made it his ultimate goal to address the inefficiencies of traditional construction.
From Furniture Builder to ‘Activist Architect’: Stuart Emmons’ Unique Journey
Stuart Emmons was fascinated by buildings at a young age. He remembers building sand cities with his brother during trips to the Jersey shore. His father gave him his first drawing table at the age of ten. Today, he is an experienced architect who received his FAIA in June 2025. The road he took is unique, to say the least.
Forge Craft Architecture + Design: Codes, Contracts, and Intellectual Property
Founding Principal and Director of Modular Practice for Forge Craft Architecture + Design, Rommel Sulit, discusses the implications of codes, contracts, and intellectual property on
modular construction.
Eisa Lee, the “Bilingual” Architect
Now as the founder of XL
Architecture and Modular Design in Ontario, Canada, she applies not just her education as a traditional architect but an entire holistic view on modular design. It’s this expansive view that guides her work on being a true partner that bridges the gap between architects and modular factories as they collaborate on the design process.
Tamarack Grove Engineering: Designing for the Modular Sector
The role of a structural engineer is crucial to the success of a modular project, from initial analysis to construction administration. Tamarack Grove offers structural engineering services — project analysis, plan creation, design creation, and construction administration — for commercial, manufacturing, facilities, public services, and modular. Modular is only one market sector the company serves but it is an increasingly popular one.
Engineer Masters the Art of Listening to His Customers
Since founding Modular Structural Consultants, LLC. in 2014, Yurianto has established a steady following of modular and container-based construction clients, primarily manufacturers. His services often include providing engineering calculations, reviewing drawings, and engineering certification
Inside College Road: Engineering the Modules of One of the World’s Tallest Modular Buildings
College Road is a groundbreaking modular residential development in East Croydon, South London by offsite developer and contractor, Tide, its modular company Vision Volumetric (VV), and engineered by MJH Structural Engineers.
Design for Flow: The Overlooked Power of DfMA in Modular Construction
Unlocking higher throughput, lower costs, and fewer redesigns by aligning Lean production flow with design for manufacturing and assembly.
Choosing the Right Ramp
Modular construction offers a compelling alternative to traditional methods for designing and building ADA and IBC-compliant entrances. By addressing the challenges of traditional construction, such as time-consuming processes, unavailable specialized labor, and variable field conditions, modular solutions provide a more efficient, cost-effective, and reliable approach.