How Air Caster Technology Has Helped Improve Modular Building Manufacturing
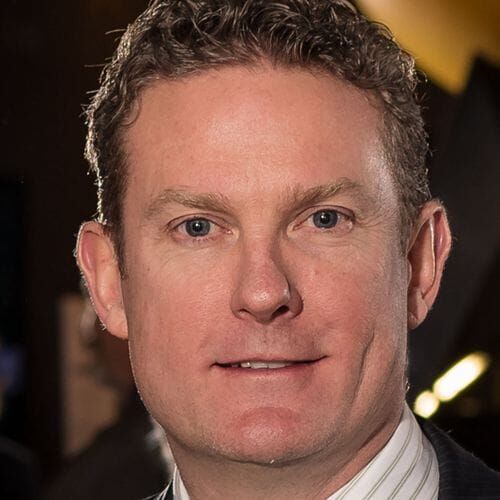
John Massenburg is the President and CEO of AeroGo, Inc.
By manufacturing houses and doing it repetitively, Fading West, a Colorado-based firm, has kept costs down and produced houses more quickly. To accomplish this goal, the company designed a manufacturing facility that can turn around hundreds of modular units, using a breakthrough process that utilizes the adoption of air casters, a low-profile material handling system inspired by hovercraft technology. Traditional systems, like cranes and forklifts, lack the capacity for larger modules, while rail systems are too inflexible and immobile.
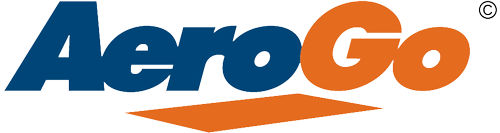
At Fading West, the company uses an unconventional U-shaped production line with nine stations down one row, one in the middle, and nine more stations up the other row. As a result, Fading West doubled its throughput and minimized travel and other forms of waste with consistently positive results.
Transforming the Construction Industry
Modular housing construction firm Fading West Development is anything but fading away. Indeed, the Buena Vista, Colorado-based company, named after an album from American rock band Switchfoot, has seen its success skyrocket in housing construction since its inception. That’s due to its clever and innovative solution to a massive and growing problem: building modular homes, apartments, and other value-engineered residential products in a factory setting to address the nationwide crisis in housing affordability. “I came here to Fading West to ask how we can revolutionize the construction industry to create more affordable housing and get it into the marketplace,” says Sean Brown, Fading West’s vice president of factory operations.
Revolutionize it they did. The Colorado Sun newspaper described Fading West as “a solution to the housing crisis.” Time Magazine even recognized Fading West as one of the 100 Most Influential Companies of 2022—ranking it alongside Amazon and Pfizer.
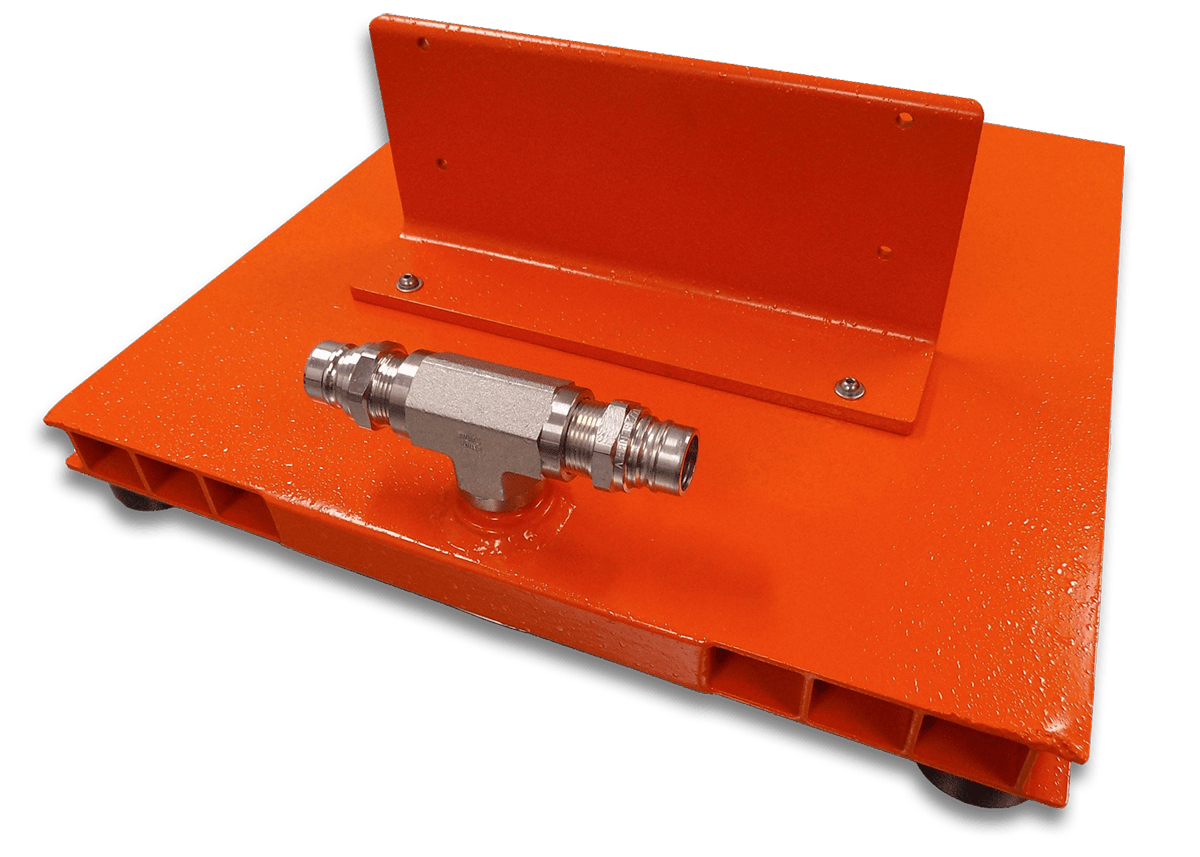
Typical load module for the modular industry allows for quick bolting to the structure through the pre-drilled holes.
What accounts for its stellar success? Efficiency. “By manufacturing houses and doing it in a repetitive fashion, we can keep costs down and we can get the number of houses out quicker,” Eric Schaefer, vice president of sales and strategic partnerships, told the Sun. The result is the company can build a modular three-bedroom home up to five times faster than a traditional stick-built house, with construction costs 15-30 percent lower and market costs at least 25 percent less expensive than comparable stick-built homes.
But what drives that efficiency? The answer might be surprising.
Turning Housing Structures into Hovercraft
The main obstacle for Fading West was designing a manufacturing facility that could turn around hundreds of these modular units, sometimes called “boxes,” quickly and efficiently. Since the company built its 110,000-square-foot factory in Buena Vista in 2021, it had an opportunity to design the perfect manufacturing process from the ground up.
Unfortunately, traditional material handling methods proved intractable in meeting its desired goals. Either they wouldn’t work in the way Fading West wanted, or they wouldn’t work at all. For example, cranes and forklifts lacked the capacity for larger modules, while rail systems were too inflexible and immobile. Fading West didn’t want a straight-line manufacturing process because that would require too large a facility and place incoming and outgoing areas on opposite ends of the facility, necessitating two staging areas. It also would force unnecessary travel for workers to monitor the process or move equipment or resources.
The breakthrough came with the adoption of air casters, a low-profile material handling system inspired by hovercraft technology. By inflating a series of donut-shaped bags with compressed air, the massive modules can hover above the ground, allowing for easy, nearly frictionless maneuverability. “In a 38-foot-long-house, we use six air casters,” says Brown. “With 40 psi, we lift the house up and, with four people, one at every corner, we just push the house across the stages. It is not difficult to move entire houses very smoothly.”
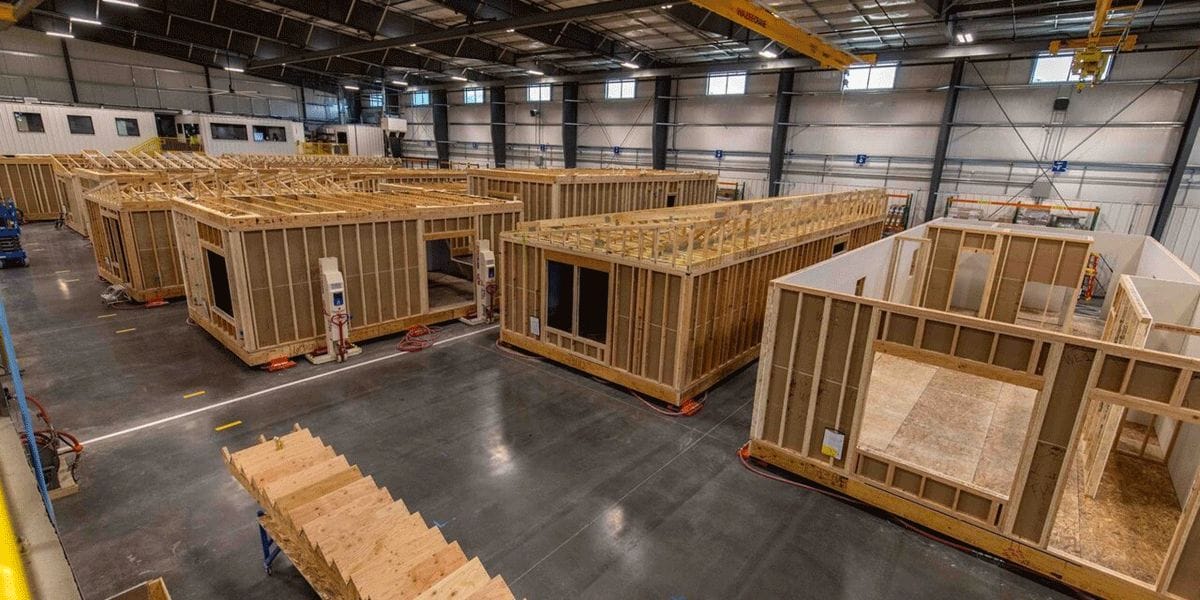
Fading West’s production line can be moved safely and efficiently while floating on air.
U-shaped? You Bet
Better yet, the air casters made it possible to create an unconventional U-shaped production line with nine stations down one row, one in the middle, and nine more stations up the other row. That way, Fading West could double throughput, minimize travel and other forms of waste, and move structures in and out through the same opening. “We can move the entire factory through all 19 stations in the line in under 30 minutes,” says Brown. It enabled Fading West to build the assembly process around a central mezzanine holding tooling and other resources, with elevated offices offering complete visibility over the whole manufacturing line, all at once.
Notably, air casters also mean flexibility, not just in terms of movement but also in terms of change. For example, one structure might be 56-feet-long and another 76-feet-long. Air casters allow the company to easily accommodate a variety of shapes and sizes of boxes and then make changes on the fly. Even better, if Fading West needs to pause production on one unit to handle one-off issues, it can simply float the box to the side and allow the remainder of the production line to continue moving uninterrupted. When ready, employees can seamlessly float the unit back into production.
Solving Real-world Problems While Floating on Air
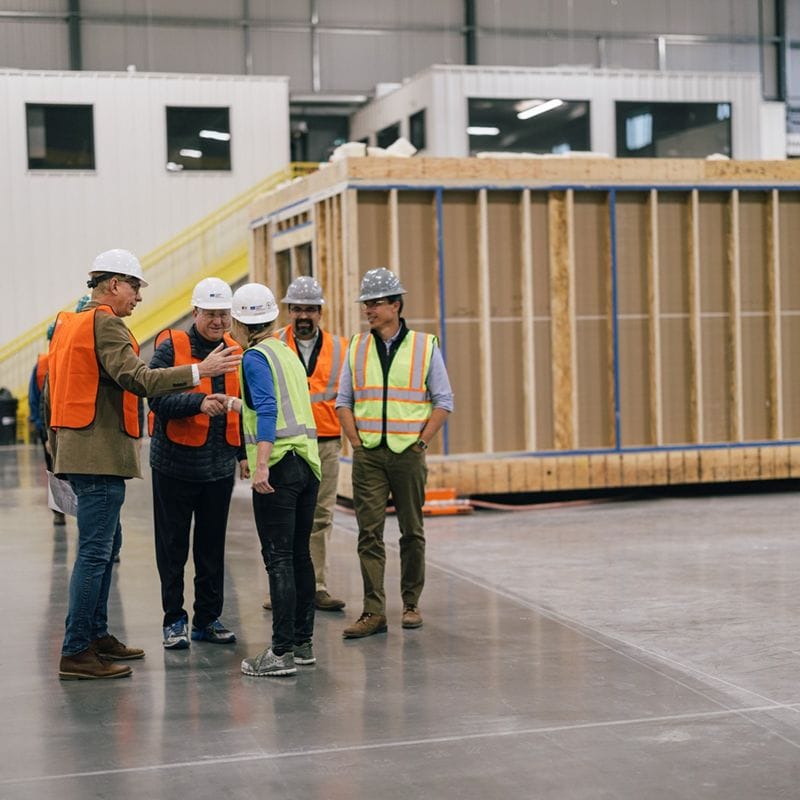
The team at Fading West discusses their efficient production line.
Tackling housing affordability is an ambitious goal, but with its ingenious manufacturing setup, Fading West has found the formula to produce high-quality housing quickly and affordably. Air casters play a quiet but critical role in this formula for success. With their ease of use, low cost, and unbeatable flexibility, Fading West designed a factory from the ground up that could maximize output and adaptability without disruption while minimizing waste. Ultimately, using air casters means Fading West can produce over 700 modular homes and apartments annually.
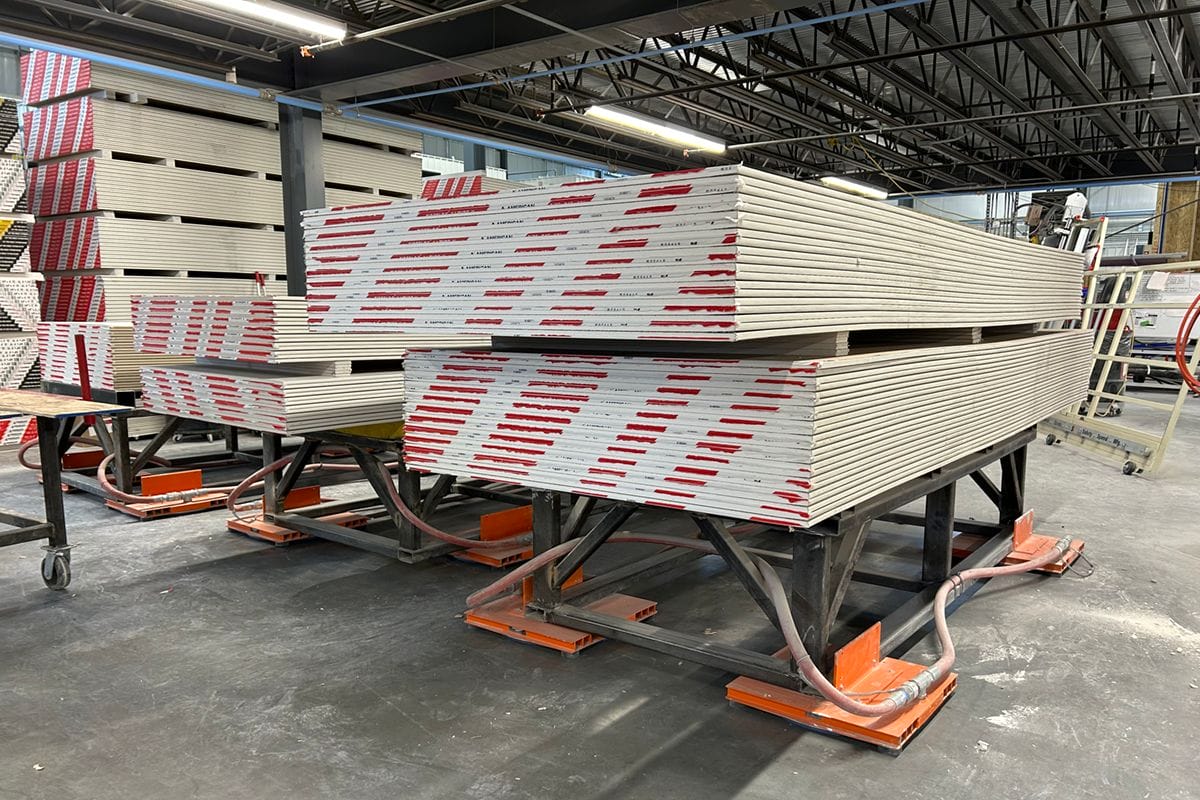
Moving building materials across the shop floor with air bearings.
It’s not just air casters themselves that matter; it’s also the company that provides them. “AeroGo was the only partner that could meet all of our needs,” says Brown. “I wish they could have provided everything in this plant. AeroGo is the only one who delivered what was promised and on time.”
AeroGo has made an impression—and not just on factory workers. “The AeroGo product is so nice, so unique, it’s commented on by every single person that walks through the factory,” says Brown. Playing a part in making housing affordable again and impressing passers-by? That’s just the everyday reality of AeroGo air casters making otherwise impossible moves happen.
Facilitating Growth with Air Caster Technology
Competition in the construction industry is fierce. Historically, two out of these three customer demands—economy, speed, and quality—were adequate. In today’s world, everyone wants all three and then some. Using modern air caster technology in the modular building sector is one way to help meet the fast-moving, high-demand expectations of the industry and its expected growth through 2024 and beyond.
More from Modular Advantage
Samantha Taylor: Leading the (Modular) Design of Tomorrow
“With modern technology and the way we’ve all embraced things like BIM, file sharing, and video conferencing since COVID, it’s easy to collaborate with companies in Austria, or Singapore, or anywhere else in the world.”
Greg DeLeon: Military Engineering to Modular Design
Greg DeLeon, a structural engineer at ISE Structural Engineers in Temecula, California, can tell you not only how large a beam needs to be to support a house, but also how much explosives you’ll need to take it down, thanks to his unique combination of professional and military experience.
To Remake North Minneapolis, Devean George Swaps Basketball for Buildings
He’s lived in Los Angeles, Dallas, and San Francisco (to name a few). He’s delivered championships with the Los Angeles Lakers and made career-defining moves with the Dallas Mavericks and the Golden State Warriors. No matter the wins, the championships, or even the seemingly impossible 3-pointers, Devean George has always returned to where it all started for him: Minneapolis.
Chelsi Tryon: Making the World a Better Place
For Chelsi Tryon, Director of Environmental, Social, and Governance (ESG) for WillScot Mobile Mini, nothing is more enjoyable than increasing the
company’s sustainability efforts while simultaneously doing her bit to save the environment.
Joshua Hart: Pushing Boundaries
Joshua Hart, P.E., vice president at Modular
Solutions, can sum up his job responsibilities in one sentence: “I do whatever needs to be done.” Hart thrives on the variety and the opportunity to be involved in every aspect of the company. And it shows! You might say Hart has come full circle.
Jamie Metzger: From Construction to Apparel and Back Again
Growing up in a blue-collar city like Edmonton, Alberta, Canada, it’s no surprise that Jamie Metzger spent some time working labor jobs on construction sites. It’s one of the most common summer jobs in the city. But that’s probably the last predictable thing about this particular story.
Victor Masso: Expanding Modular in Puerto Rico
Victor Masso joined 2 Go Storage, a company started by his grandfather and father, in 2018 to develop a modular building division in the wake of the devastation caused by Hurricane Maria in 2017. Prior to joining the company, he had worked in the industry for about four years focusing on pharmaceutical, commercial, and government projects.
Eliyah Ryals: Finding the Perfect Fit
It’s not common for people to find their perfect career fit straight out of college. It’s even less common to find it in the town you grew up in. But that’s exactly what happened when Eliyah Ryals was told about vacancies at Panel Built and made the decision to apply.
Through It All, It’s Still About the Workers
By February 2024, the number of available, unfilled construction job openings had reached an all-time high. At some point, interest rates will fall, creating another surge in demand for such workers. In short, solving the nation’s skilled worker shortage issue has never been more important.
Navigating Insurance Challenges in the Modular Construction Industry
Utilizing practical written minimum insurance and indemnity requirements, along with monitoring certificates of insurance by someone who has COI training will not yield a perfect risk transfer strategy, but the exposure will be managed much better than it likely is currently.