Offsight’s Digital Certification Program Can Accelerate Modular Industry Growth
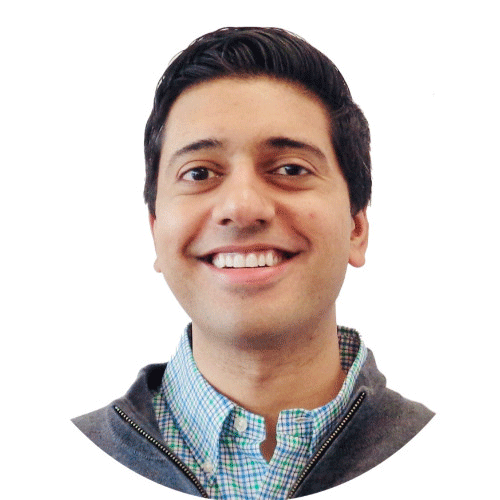
Vikas Murali is the CEO & Co-Founder at Offsight
When it comes to modular and offsite construction the benefits and advantages are widely known and accepted. Industry analysts have forecasted that the traditional construction value chain is ripe for disruption and a $256 Billion annual profit pool can be accessed by new offsite and modular businesses.
Analysis by McKinsey & Company already confirms that modular techniques accelerate construction timelines by 20 to 50 percent and can reduce overall costs by 20 percent. The benefits of modular construction over traditional methods are obvious and include faster project delivery, reduced overall project cost, and far greater overall project quality excellence. However, in the same analysis the authors directly address the key factors that must be addressed to accelerate modular adoption:
“The benefits of modular buildings come from the industrialization of key construction tasks. Modular companies aim to standardize, streamline, and automate big parts of the value chain, allowing buildings to be treated like products rather than projects. To get that right, modular players need best-in-class manufacturing capabilities, including sophisticated digital design platforms and lean, efficient production lines.”
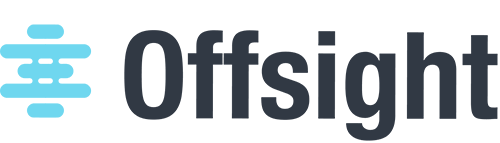
In other words, simply moving work from a traditional job site into a factory doesn’t ensure that the true benefits of modular and offsite construction including speed, cost savings, and quality excellence are achieved. In order to truly realize the return on investment of offsite construction, companies must run a highly efficient manufacturing and production process. Investing in digitization and training your workforce to capitalize on the move to modular will be the key to truly harnessing the full potential and value add of offsite construction.
Going Digital, Getting Certified & Capturing The Full ROI of Modular Construction
At Offsight, we’ve built a solution specifically for the modular, offsite, and prefab industry. Our platform is robust enough to manage all forms of building project manufacturing over the full scope of prefab and modular product lines, from fully volumetric modules and bath pods to panels, trusses, and floor cassettes.
By developing a solution specific to the needs of the industry, we meticulously considered each aspect of managing a modular and prefab project at the factory level and built a full feature set to address the entire scope of factory operations. This includes Production & Quality Tracking, Reporting & Auditing, Advanced Analytics & Insights, Labor Tracking & Timesheets and Materials & Inventory Management.
To achieve the full potential from Offsight, our customers needed to drive adoption internally through educating their workforce and developing internal champions to learn our platform and train others. After witnessing our most successful modular customers deploy and expand our solution to their other factories successfully, Offsight was able to track progress and quality across several major commercial projects in parallel. We incorporated these insights into a digital certification and training program curated to foster shared knowledge among industry leaders within our customer base.
Related Listening:
The Value-Add of Offsite Construction Project Management Software w/ Offsight
Vikas Murali, CEO of Offsight, discusses the advantages that offsite factory owners and manufacturers can realize through the use of customized project management software. Vikas also talks about the development and capabilities of his company's Offsight software platform, as well as about how his background in enterprise-level software development—combined with the modular and offsite industry experience of his key staff—has led to Offsight's growth as an industry software solution.
To achieve the full potential from Offsight, our customers needed to drive adoption internally through educating their workforce and developing internal champions to learn our platform and train others. After witnessing our most successful modular customers deploy and expand our solution to their other factories successfully, Offsight was able to track progress and quality across several major commercial projects in parallel. We incorporated these insights into a digital certification and training program curated to foster shared knowledge among industry leaders within our customer base.
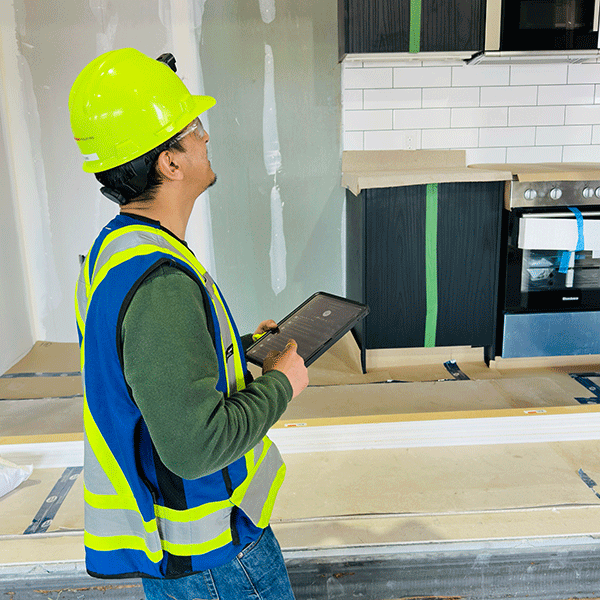
Commercial modular builder Z Modular utilizes Offsight to manage projects across multiple factories in the U.S. and Canada.
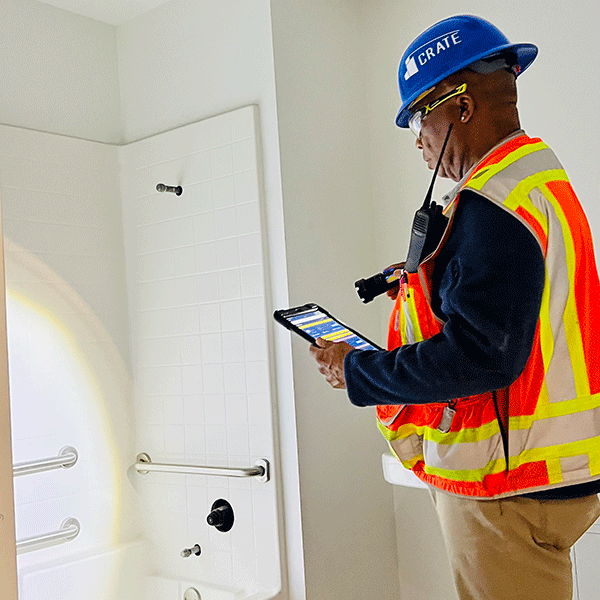
Multifamily residential builder CRATE Modular, leverages Offsight to manage full factory operations and production.
Therefore, we launched the Offsight Certification Program in January 2024. Our program is designed to equip production managers, quality inspectors, plant managers, and operators with a deeper understanding of how technology and digitization can be a game-changer in driving process improvements and productivity benefits, which will ultimately allow our customers to capture the full value of modular and offsite construction.
As Offsight Solutions Engineering Manager, Jason Dixon states: “Before joining Offsight, I held quality manager and operations roles at modular manufacturing companies. It was my responsibility to implement Offsight across our workforce of 50+ operators and managers. My biggest takeaway was the importance of training a technical lead responsible for learning how Offsight works and the value it can provide the factory. Our Offsight Certification Program will enable our clients to better train and recognize these internal leads and drive technological changes throughout the company.”
Our program consists of two major certifications that help operators, managers, and inspectors apply digitization to all aspects of factory operations. The Offsight Factory Operations Project Management Certification trains modular industry leaders in leveraging Offsight’s production, quality, analytics, and material and labor tracking capabilities to manage overall prefab project progress, collaborate with other project stakeholders, and accurately manage project costs. The Offsight Digital Quality Building Inspections Certification is designed to help quality personnel, managers and accredited building inspectors leverage digitization to manage complex code conformance and tracking, including mandatory and State-regulated reporting and auditing.
Through both programs, modular professionals learn how digitization can be a game-changer in driving modular construction adoption and delivering on the innate benefits the process offers.
As Offsight customer, Keizah Coye, Plant Project Manager at CRATE Modular, states: “As a production leader, I interact with Offsight daily. It’s a very robust solution that helps manage all factory operations and provides crucial visibility to our management. Their Certification and training program is exactly what production leaders in the modular, offsite, and prefab industry, like myself, need to quickly get up to speed on how Offsight’s technology can be utilized to meet our major operations and project goals and scale our business.”
At Offsight, our vision is to be the leading provider of digital tools and products that empower companies to unlock the complete potential of modular and offsite construction. We invite you to join us on this journey and hope that we can partner with you to help push the industry forward.
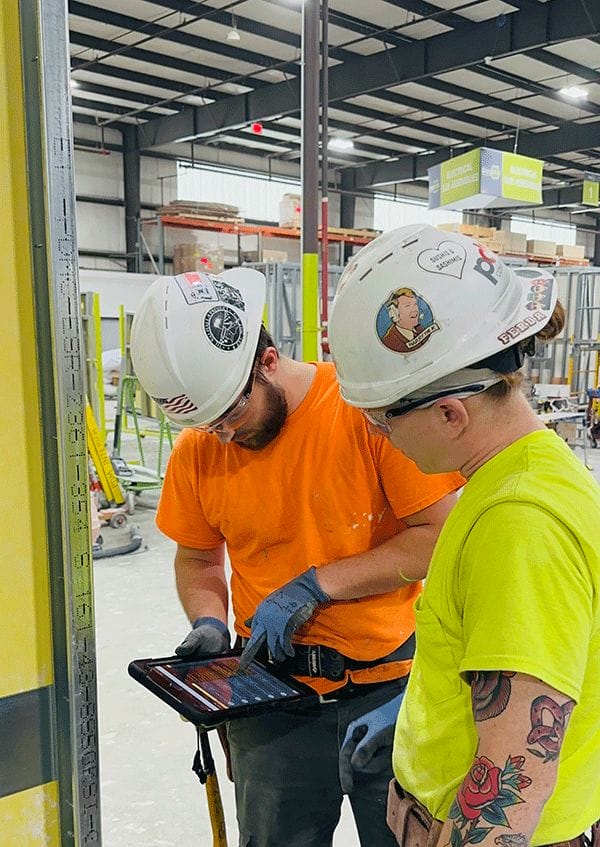
Specialty contractor PDM Constructors manages production across thousands of modular bath pods for major healthcare projects, through Offsight.
More from Modular Advantage
Samantha Taylor: Leading the (Modular) Design of Tomorrow
“With modern technology and the way we’ve all embraced things like BIM, file sharing, and video conferencing since COVID, it’s easy to collaborate with companies in Austria, or Singapore, or anywhere else in the world.”
Greg DeLeon: Military Engineering to Modular Design
Greg DeLeon, a structural engineer at ISE Structural Engineers in Temecula, California, can tell you not only how large a beam needs to be to support a house, but also how much explosives you’ll need to take it down, thanks to his unique combination of professional and military experience.
To Remake North Minneapolis, Devean George Swaps Basketball for Buildings
He’s lived in Los Angeles, Dallas, and San Francisco (to name a few). He’s delivered championships with the Los Angeles Lakers and made career-defining moves with the Dallas Mavericks and the Golden State Warriors. No matter the wins, the championships, or even the seemingly impossible 3-pointers, Devean George has always returned to where it all started for him: Minneapolis.
Chelsi Tryon: Making the World a Better Place
For Chelsi Tryon, Director of Environmental, Social, and Governance (ESG) for WillScot Mobile Mini, nothing is more enjoyable than increasing the
company’s sustainability efforts while simultaneously doing her bit to save the environment.
Joshua Hart: Pushing Boundaries
Joshua Hart, P.E., vice president at Modular
Solutions, can sum up his job responsibilities in one sentence: “I do whatever needs to be done.” Hart thrives on the variety and the opportunity to be involved in every aspect of the company. And it shows! You might say Hart has come full circle.
Jamie Metzger: From Construction to Apparel and Back Again
Growing up in a blue-collar city like Edmonton, Alberta, Canada, it’s no surprise that Jamie Metzger spent some time working labor jobs on construction sites. It’s one of the most common summer jobs in the city. But that’s probably the last predictable thing about this particular story.
Victor Masso: Expanding Modular in Puerto Rico
Victor Masso joined 2 Go Storage, a company started by his grandfather and father, in 2018 to develop a modular building division in the wake of the devastation caused by Hurricane Maria in 2017. Prior to joining the company, he had worked in the industry for about four years focusing on pharmaceutical, commercial, and government projects.
Eliyah Ryals: Finding the Perfect Fit
It’s not common for people to find their perfect career fit straight out of college. It’s even less common to find it in the town you grew up in. But that’s exactly what happened when Eliyah Ryals was told about vacancies at Panel Built and made the decision to apply.
Through It All, It’s Still About the Workers
By February 2024, the number of available, unfilled construction job openings had reached an all-time high. At some point, interest rates will fall, creating another surge in demand for such workers. In short, solving the nation’s skilled worker shortage issue has never been more important.
Navigating Insurance Challenges in the Modular Construction Industry
Utilizing practical written minimum insurance and indemnity requirements, along with monitoring certificates of insurance by someone who has COI training will not yield a perfect risk transfer strategy, but the exposure will be managed much better than it likely is currently.