Revisiting ReMo Homes and its Modular Housing Revolution
The California-Based Start-Up Aims to Build a Sustainable Home in Just an Hour
ReMo Homes founder Vamsi Kumar Kotla has an ambitious goal: assemble a net zero, single-family home with a minimized carbon footprint in just one hour. Surprisingly, his team is close to making his goal a reality. They recently assembled a 400 square foot net zero model home on the National Mall in Washington, DC. Assembly took ten days.
Kotla believes his team can reach the magic one-hour mark. “If you look at Tesla, previously they’ve been spitting out a Model 3 every 43 seconds. Now I think they’re aiming for 30 seconds. And a car is a far more complex process than a house.”
ReMo Homes’ mission is to solve both the housing and climate change crises with industrialized and productized building construction. The company was featured in Modular Advantage about a year ago in an article that touted the revolutionary features of their homes. Now the team is focused on speeding up construction and improving the sustainable features of its products.
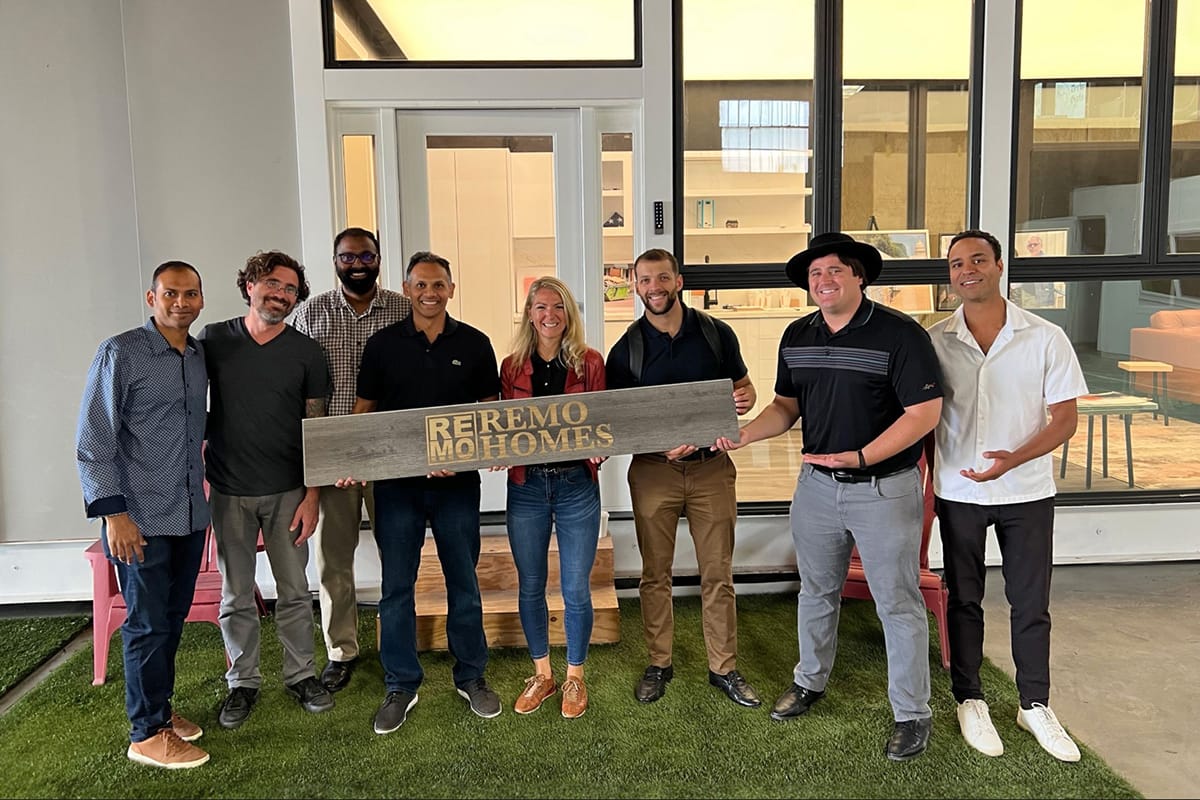
ReMo hosting Dassault Systèmes at its California factory.
Building Faster
From the beginning the ReMo Homes team was focused on speed of construction. “We realized if you can’t improve speed, you’re going to have the same labor overhead as traditional construction, on top of your factory overhead. And if you add in transportation and logistics costs, much of the cost advantage is lost.
“We noticed that for every one square foot of factory space in a modular factory, they produced two square feet annually (2:1), which I feel is not good enough. If you look at Tesla’s Fremont factory, they’re spitting out about 700,000 cars in their 5 million square foot factory, which comes to about 66.5 million square feet. So, they’re doing roughly 13:1 factory productivity. I feel that if we want to, we can beat the automotive benchmarks for labor and factory productivity based on how many square feet we produce in our factory space.”
With production speed in mind, they’ve made several updates to their products and the manufacturing process. First, they’ve worked with their suppliers to tighten the tolerances for building materials. Since they work with steel and composite materials mostly, slight variances in measurements are difficult to correct on site. Next, they’ve reduced delays for drying time. The use of drywall, paint, grout, and caulking have been eliminated or minimized, reducing the time needed to let these materials dry. An added benefit is that these products aren’t off gassing into the air, creating the potential for respiratory irritation. Thirdly, they’ve modified the building process to include more sub-assemblies that are then delivered to the main assembly line. These assemblies come from other stations in the factory or third-party providers. Using these sub-assemblies allows the company to allocate more workers to those tasks that take the longest time, reducing the overall production schedule.
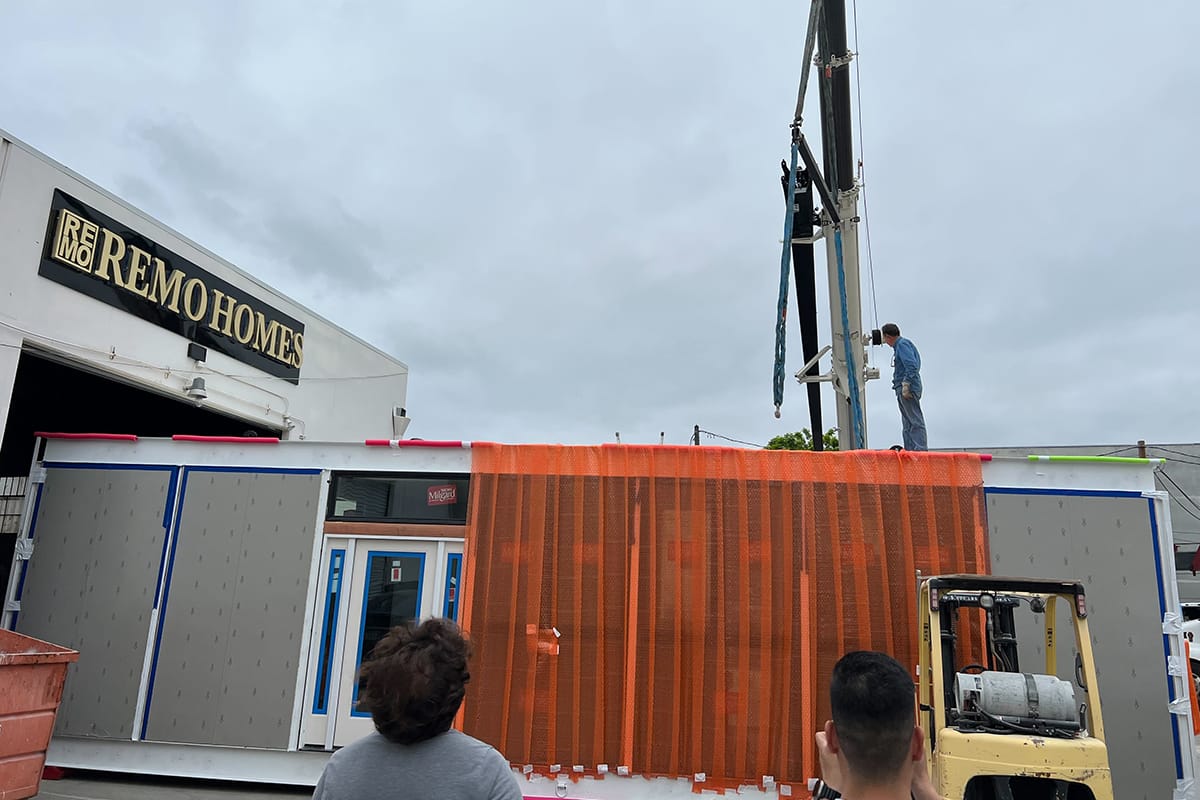
ReMo Homes preparing to send a model modular home to Washington DC to exhibit on the National Mall.
They’ve also focused not just on the affordability of purchasing a home, but the affordability of living in a home. “What we realized was the world needs an affordable home that’s cheaper to own on a long-term basis. So, that means lower maintenance and utility costs.” But instead of just creating an energy efficient home, Kotla chose to take it one step further: net zero energy.
They are achieving net zero through integrating solar power generation with extreme energy efficiency. For example, a lot of energy is lost when converting power from AC to DC and back. Many appliances, light fixtures, and even HVAC equipment can work on low voltage power, which is less expensive and easier to install.
Another focus is water efficiency. They’ve looked at strategies like recycling water from the sink to the toilet, or reusing water within the shower for the same person.
Another feature of their homes is full spectrum LED lighting that helps improve the quality of life for everyone, including those with mood disorders and/or sleep issues. And since it was recently found that using natural gas for cooking can cause cancer-related illnesses, their kitchens are fully electric, with an induction stove, microwave, and an electric oven.
A Smarter Home
Kotla’s vision of a smart home is miles ahead of even what we have today. He’s set his sights clearly on the future, when we may be able to run a diagnostic on a home and have it tell us what’s wrong and how to fix it. “For example, when I had an issue with charging my Tesla, support performed a diagnostic test and in 30 seconds said there was nothing wrong with anything in the car. ‘It’s just your cable that needs to be replaced.’ How do we get to that with homes?”
Connectivity and recordkeeping are the backbone of his newly imagined smart home. Everything will need to be connected to the IoT and records will need to be kept about where all the parts, materials, and equipment were sourced from, including when it was last serviced and where it was manufactured. Kotla predicts that this type of home will be able to tell homeowners about an issue, like a potential leak in a pipe fitting, before the damage is done.
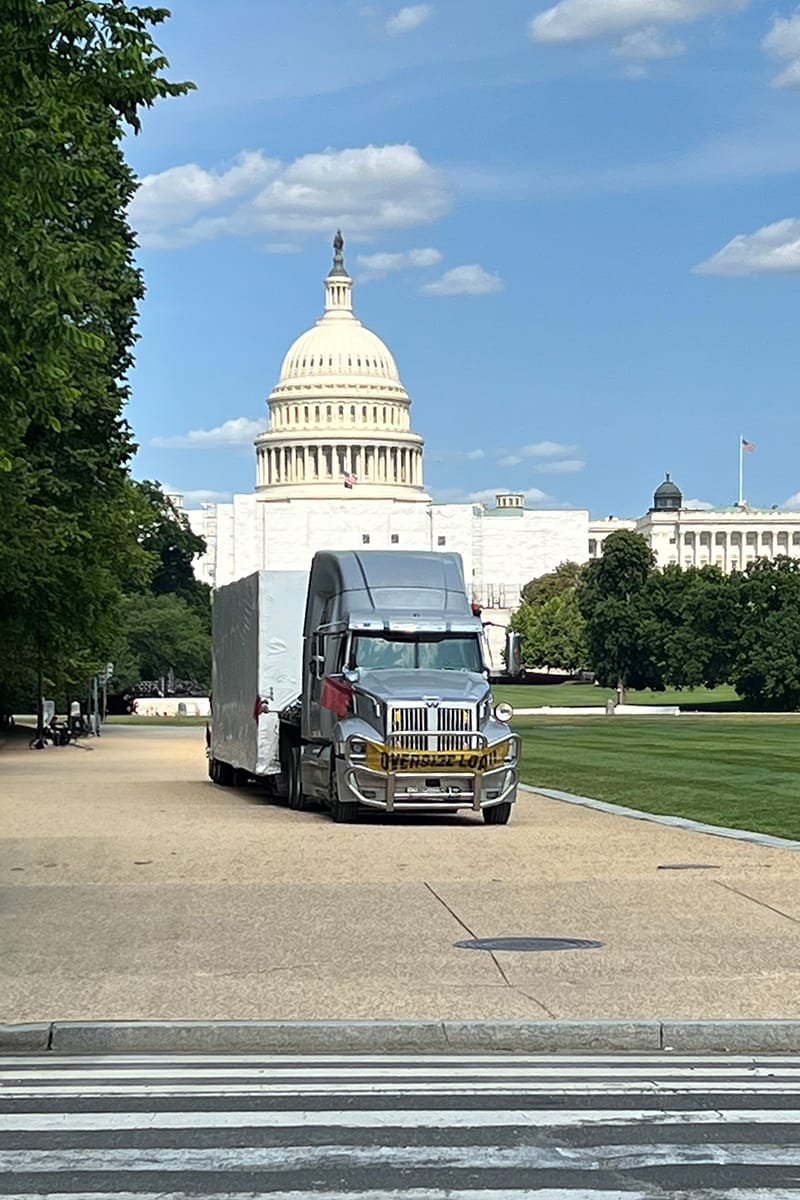
A modular building from ReMo Homes arriving at the National Mall in Washington, DC.
A home’s records will also make refreshing or remodeling much simpler. The database would include a catalog of available options to fit your needs, and they could be easily swapped out. Owners could simply choose the upgrade, like a new backsplash or light fixture. The system would have the size or quantity needed, and ReMo would send a contractor out to perform the installation.
For those who want to reconfigure their space, their homes are designed for disassembly. Walls can be removed or moved into a new configuration. “We want to do it in a few minutes. Disassemble a wall instead of breaking something and wasting it.” And at the end of the building’s life, it can be easily dismantled, and the materials salvaged for other purposes.
One roadblock to modular construction he has seen is the failure of financing institutions to adapt to this new way of constructing a building. Most provide funds based on percentage of completion, which steadily progresses as time goes along. “But with modular, you buy all your materials upfront, and then you start building it. So, you want larger upfront payments, and you want all the money before the product leaves the factory. Governments and institutions need to be educated about this process.”
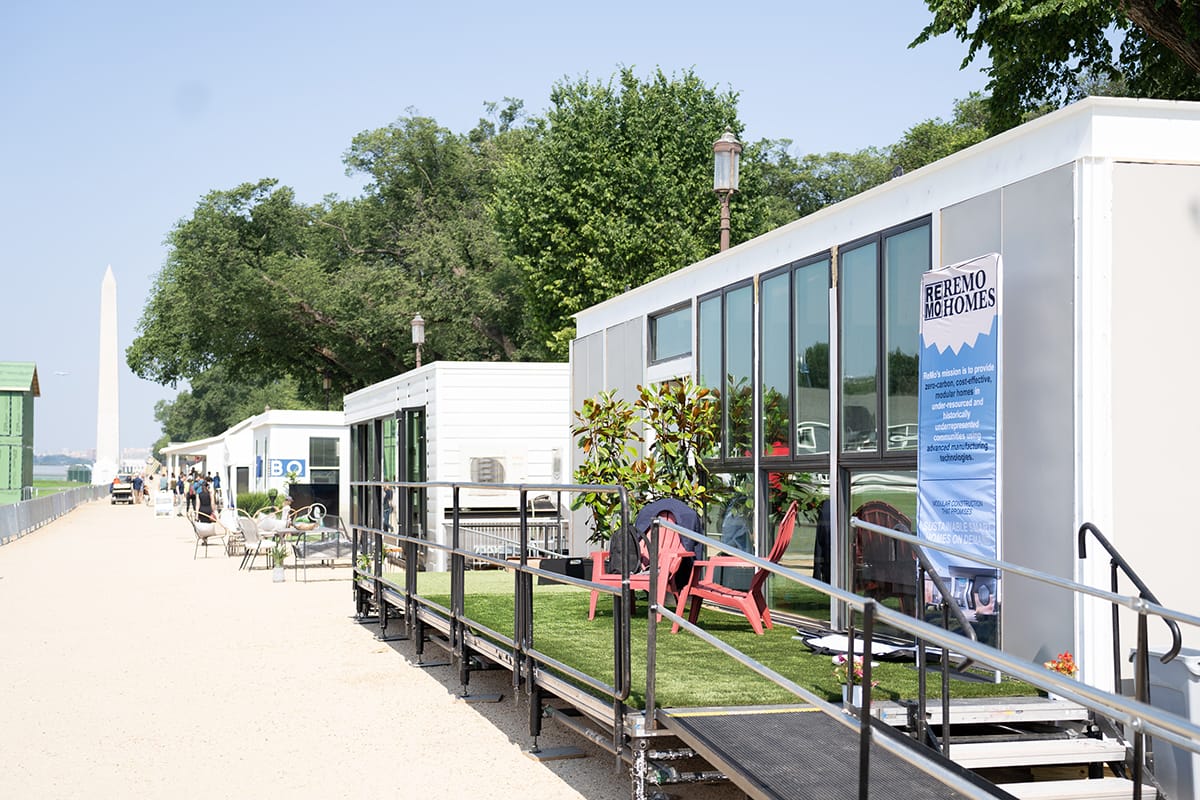
Future Plans
In the near future, ReMo Homes would like to expand to multi-family developments by developing stacking units. However, they need to address the issue of double common walls first. “For traditional homes in an apartment complex, one unit’s ceiling is also the floor for the unit above. But in modular, there’s a duplicate floor and ceiling that increases the height by one foot. And if there are height limitations in a particular zone, that might break the project and/or cause the use of excessive materials.” The same issue applies to shared walls. “Every inch matters when building in a big city.”
Kotla sees the future of construction moving from “construction” to “mass manufacturing and assembly.” Seeing each project as one product that you learn from and improve each time. But this change would greatly affect how designs are created. Traditional CAD tools won’t measure down to the level of accuracy needed for production manufacturing. So Kotla has been using manufacturing software instead. “We tend to use these tools so that we can get to higher tolerances and ensure that assemblies fit exactly. We don’t use traditional CAD tools, which are good for construction documents and schematics, but bad for fabrication.”
The future seems bright for ReMo Homes, and who knows, some day they may be constructing homes in just an hour.
About the Author: Dawn Killough is a freelance construction writer with over 25 years of experience working with construction companies, subcontractors and general contractors. Her published work can be found at dkilloughwriter.com.
More from Modular Advantage
Samantha Taylor: Leading the (Modular) Design of Tomorrow
“With modern technology and the way we’ve all embraced things like BIM, file sharing, and video conferencing since COVID, it’s easy to collaborate with companies in Austria, or Singapore, or anywhere else in the world.”
Greg DeLeon: Military Engineering to Modular Design
Greg DeLeon, a structural engineer at ISE Structural Engineers in Temecula, California, can tell you not only how large a beam needs to be to support a house, but also how much explosives you’ll need to take it down, thanks to his unique combination of professional and military experience.
To Remake North Minneapolis, Devean George Swaps Basketball for Buildings
He’s lived in Los Angeles, Dallas, and San Francisco (to name a few). He’s delivered championships with the Los Angeles Lakers and made career-defining moves with the Dallas Mavericks and the Golden State Warriors. No matter the wins, the championships, or even the seemingly impossible 3-pointers, Devean George has always returned to where it all started for him: Minneapolis.
Chelsi Tryon: Making the World a Better Place
For Chelsi Tryon, Director of Environmental, Social, and Governance (ESG) for WillScot Mobile Mini, nothing is more enjoyable than increasing the
company’s sustainability efforts while simultaneously doing her bit to save the environment.
Joshua Hart: Pushing Boundaries
Joshua Hart, P.E., vice president at Modular
Solutions, can sum up his job responsibilities in one sentence: “I do whatever needs to be done.” Hart thrives on the variety and the opportunity to be involved in every aspect of the company. And it shows! You might say Hart has come full circle.
Jamie Metzger: From Construction to Apparel and Back Again
Growing up in a blue-collar city like Edmonton, Alberta, Canada, it’s no surprise that Jamie Metzger spent some time working labor jobs on construction sites. It’s one of the most common summer jobs in the city. But that’s probably the last predictable thing about this particular story.
Victor Masso: Expanding Modular in Puerto Rico
Victor Masso joined 2 Go Storage, a company started by his grandfather and father, in 2018 to develop a modular building division in the wake of the devastation caused by Hurricane Maria in 2017. Prior to joining the company, he had worked in the industry for about four years focusing on pharmaceutical, commercial, and government projects.
Eliyah Ryals: Finding the Perfect Fit
It’s not common for people to find their perfect career fit straight out of college. It’s even less common to find it in the town you grew up in. But that’s exactly what happened when Eliyah Ryals was told about vacancies at Panel Built and made the decision to apply.
Through It All, It’s Still About the Workers
By February 2024, the number of available, unfilled construction job openings had reached an all-time high. At some point, interest rates will fall, creating another surge in demand for such workers. In short, solving the nation’s skilled worker shortage issue has never been more important.
Navigating Insurance Challenges in the Modular Construction Industry
Utilizing practical written minimum insurance and indemnity requirements, along with monitoring certificates of insurance by someone who has COI training will not yield a perfect risk transfer strategy, but the exposure will be managed much better than it likely is currently.