Dynamic Automation Helps Company Create “Snowflakes”
House of Design, located in Nampa, Idaho, provides a unique solution to building trusses, walls, and other building assemblies: they call it dynamic automation. Shane Dittrich, CEO, explained the term as “the robots have no idea what they’re building today.”
Instead of tasking a robot to build only one type and size of assembly, their software analyzes the most efficient order to produce a variety of similar products in, no matter what size they are. The software takes advantage of efficiencies to shave off milliseconds and full seconds from standard automated fabrication.
House of Design’s proprietary software translates 3D models into machine code, which then communicates with the robot to tell it what size assembly to build. Because buildings are designed uniquely and no truss looks the same, the dimensions and how they are assembled look different. Each is a unique size and shape, or a “snowflake,” as Dittrich calls them. “When a robot picks up a stud,” said Dittrich, “it doesn’t care how long it is. The same End of Arm Tool can pick up a stud if it’s a 7-foot wall or a 10-foot wall, it doesn’t matter.”
Their system is able to switch between assembly sizes and shapes quickly and easily, and make each one in succession in the most efficient way. There are some constraints, such as the size of the assembly table, but otherwise the available configurations are endless.
This level of production customization is more complicated than it seems, as customers don’t always request their materials in the same way. Some want trusses stacked from biggest to smallest for shipping, others want them stacked in the order they’ll be installed.
Luckily, their system doesn’t care and simply fulfills the requested order in the most efficient way given the customer’s requests.
Before production begins, the software analyzes and validates the design, helping to ensure that the assembly is in the proper sequence and that there aren’t any problematic areas that need to be addressed. This helps keep the manufacturing process running smoothly. There are design constraints and material tolerances that must be taken into consideration, but otherwise the system can build almost anything.
“In my mind it’s relatively easy to program a robot to build a wall with studs 16 inches on center. It’s just a stud every 16 inches on the top and bottom plate. It’s a little more difficult to program it to do laminations, staggered studs, blocking, lay flats, and double top plates.” Even complex designs, like wall panels with window and door openings, are able to be programmed into the system.
The software is programmed in multiple languages, including ABB’s proprietary robot language called Rapid, and more standard languages like Rust and PLC-structured text.
Although the rest of the world is fascinated with artificial intelligence, Dittrich said its influence on his process is limited. “Right now, to look at a process and take milliseconds out of a robot’s move takes an experienced robot person. These experts can take a process that takes five seconds down to three and a half. When you’re running that process 24/7, that second and a half adds up. I do believe that AI is going to be able to help us with that in the future.”
The company stays with its customers, working with them on system installation, training, and operations. They provide resident engineers with each system to work side by side with operations workers until it is up and running smoothly.
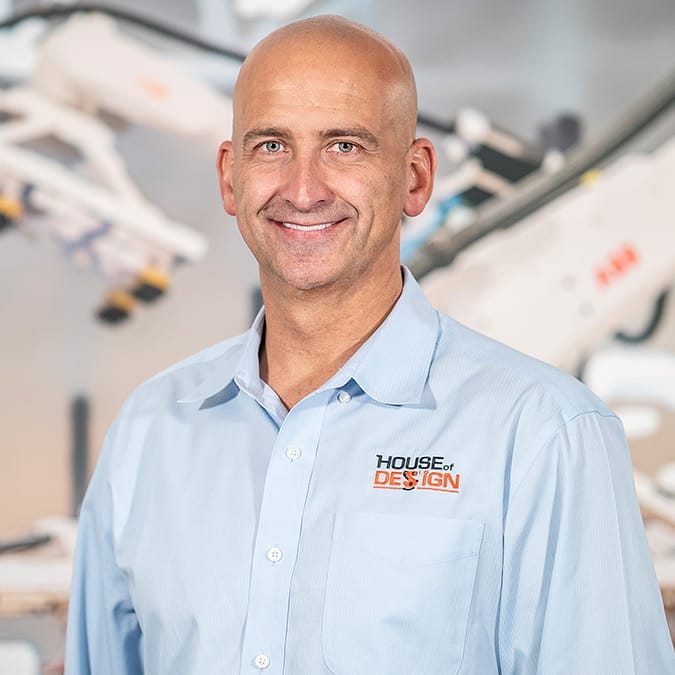
Shane Dittrich, CEO at House of Design.
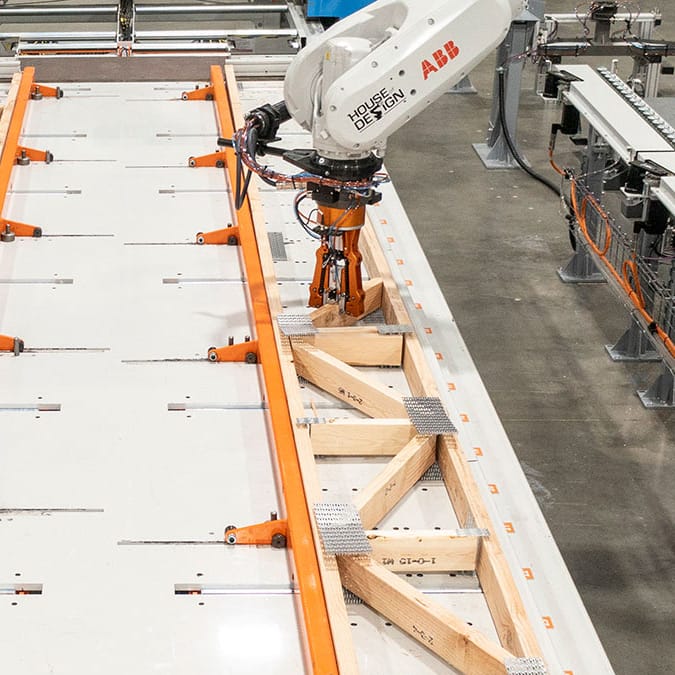
A House of Design-programmed robot assembles a truss for a modular building.
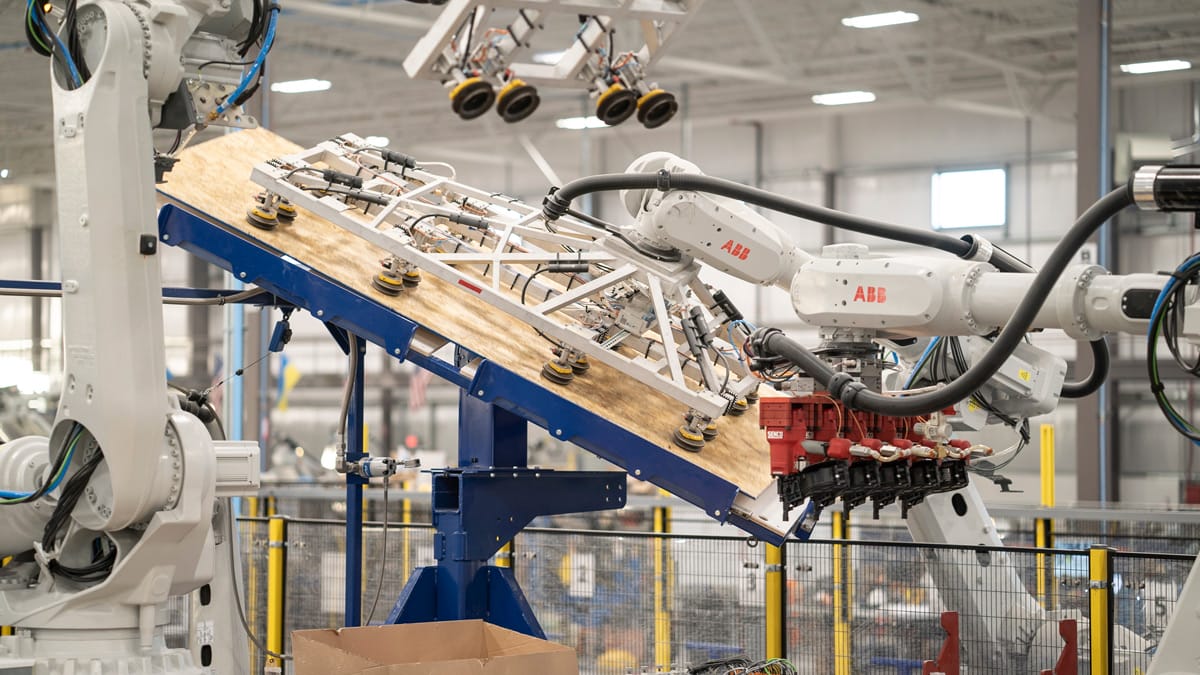
Starting Small
House of Design was founded in 2012 and was focused on custom robotic automation. As Dittrich put it, “We would do anything and everything for anybody.” The company quickly grew from two to almost 100 people right now.
In 2018 they landed work with both Katerra and Autovol. Dittrich has a lot of respect for how Katerra pushed the industry forward, and the contract with Autovol is ongoing and has led to the construction of almost 30 miles of wall assembly.
After getting the contracts with Katerra and Autovol the company pivoted to focus almost exclusively on construction and modular building. Their mission now is to use their robotic automation solutions to help solve the affordable housing crisis.
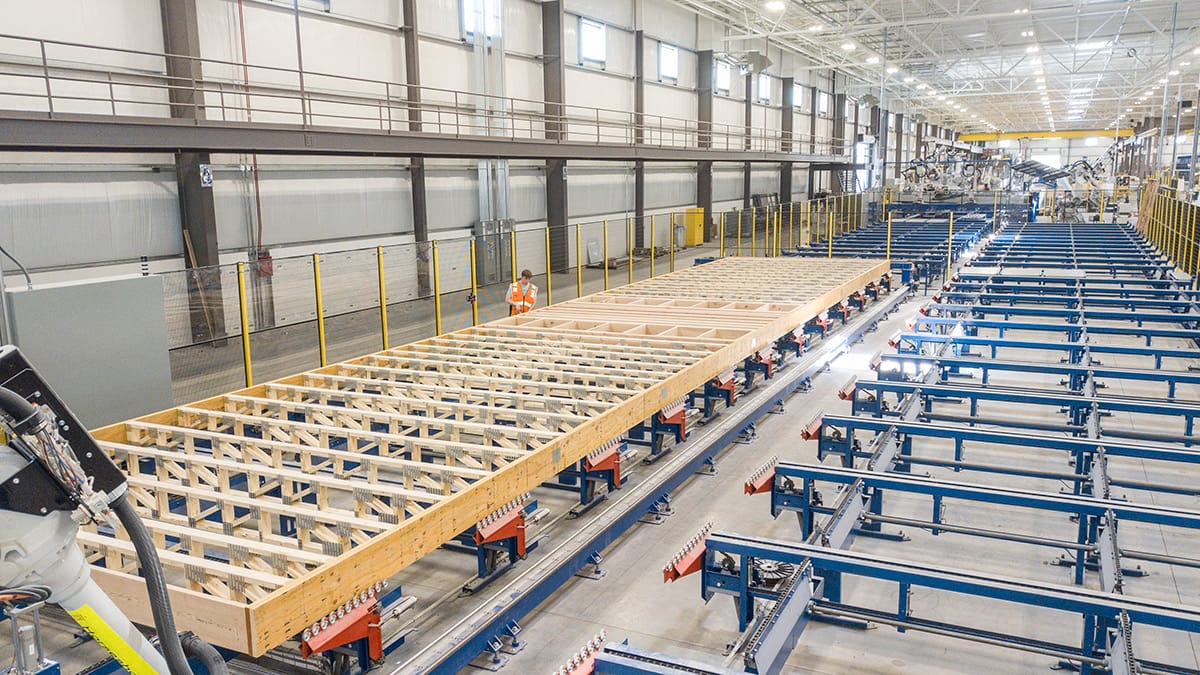
Benefits of Automation
Dittrich sees several benefits to the increased use of robots and automation in the construction industry. One of the most important is that technology opens the door to more diversity in the workforce. It has the ability to appeal to a wider audience, such as women, those of smaller stature, older workers, and those with technological knowledge and aptitudes. “Nowadays younger workers don’t want to be lifting 4 feet by 8 feet sheets of gypsum board all day long. It’s a hard job, and nobody should have to do it. But they love operating a robotic system. It’s almost like gaming to them. Automation opens up the available labor pool for factories.”
Another benefit is improved safety. “We want to get the nail guns out of worker’s hands, because I can guarantee you’re going to have an accident. At Autovol, we’ve built 28 miles of wall assemblies without someone getting hurt with a nail gun. At a manual manufacturing facility, it’s almost guaranteed that someone has driven a nail into their hand.”
Consistent quality is another advantage. “We’re going to pump out the exact same thing every single time.” People can have bad days and bring those bad days to work, greatly affecting the product that comes out of a factory. Automation helps bring consistency to the process.
Labor savings is another benefit that is discussed in the industry, but Dittrich sees it more as labor redistribution. “I don’t know of any company where we’ve gone in, installed automation, and they actually removed or fired people. Usually, they move them to a process that isn’t automated to increase production.”
The Future of Automation
Unfortunately, the cost of automation is increasing, as the price of the steel and electronics used to build robots has gone through the roof in recent years. Dittrich said the industry needs to rethink its mindset when it comes to the role of automation in the workforce. If contractors don’t have enough workers to produce according to project schedules, they’ll need to seek out alternatives, such as automation, to help them keep up with building demand. At that point, cost isn’t going to be as important.
Although automation, even dynamic automation, may not solve all of the construction industry’s woes, it can make significant improvements in specific areas and on specific tasks. “It’s a solution to the specific task that you’re automating, and if it pencils out, then great. If not, that task is not for automation.”
Dittrich sees more on-site manufacturing as the future of automation in the construction industry. Although moving production out of the controlled environment of a warehouse or factory does present risks. Efficiency and safety may be compromised. When asked if we’ll see buildings built exclusively by robots in the near future, Dittrich says he can see that if we address the differences in local building codes and standardize materials dimensions and quality. “You improve those two things, and we will be right there with you to automate those processes.”
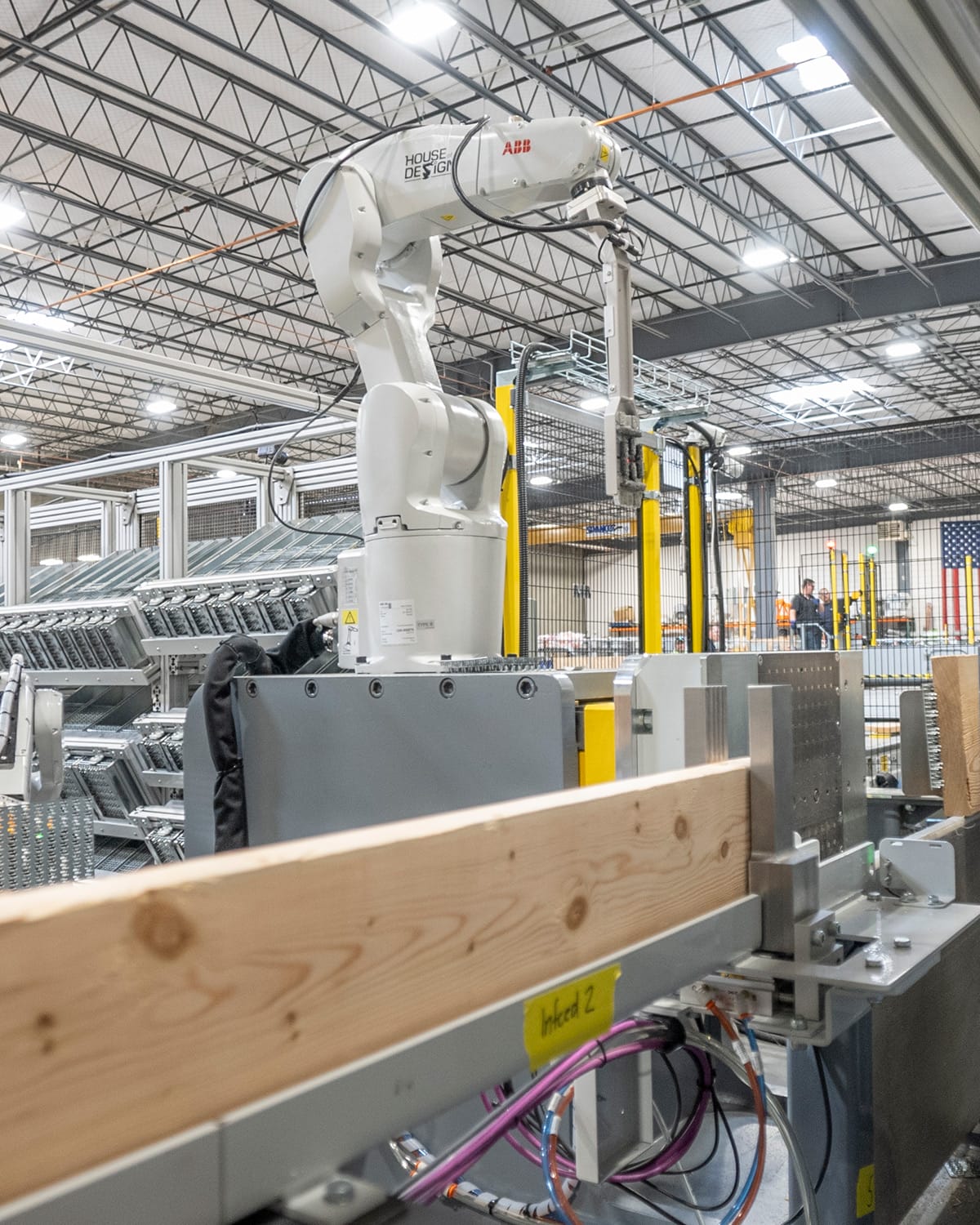
About the Author: Dawn Killough is a freelance construction writer with over 25 years of experience working with construction companies, subcontractors and general contractors. Her published work can be found at dkilloughwriter.com.
More from Modular Advantage
Samantha Taylor: Leading the (Modular) Design of Tomorrow
“With modern technology and the way we’ve all embraced things like BIM, file sharing, and video conferencing since COVID, it’s easy to collaborate with companies in Austria, or Singapore, or anywhere else in the world.”
Greg DeLeon: Military Engineering to Modular Design
Greg DeLeon, a structural engineer at ISE Structural Engineers in Temecula, California, can tell you not only how large a beam needs to be to support a house, but also how much explosives you’ll need to take it down, thanks to his unique combination of professional and military experience.
To Remake North Minneapolis, Devean George Swaps Basketball for Buildings
He’s lived in Los Angeles, Dallas, and San Francisco (to name a few). He’s delivered championships with the Los Angeles Lakers and made career-defining moves with the Dallas Mavericks and the Golden State Warriors. No matter the wins, the championships, or even the seemingly impossible 3-pointers, Devean George has always returned to where it all started for him: Minneapolis.
Chelsi Tryon: Making the World a Better Place
For Chelsi Tryon, Director of Environmental, Social, and Governance (ESG) for WillScot Mobile Mini, nothing is more enjoyable than increasing the
company’s sustainability efforts while simultaneously doing her bit to save the environment.
Joshua Hart: Pushing Boundaries
Joshua Hart, P.E., vice president at Modular
Solutions, can sum up his job responsibilities in one sentence: “I do whatever needs to be done.” Hart thrives on the variety and the opportunity to be involved in every aspect of the company. And it shows! You might say Hart has come full circle.
Jamie Metzger: From Construction to Apparel and Back Again
Growing up in a blue-collar city like Edmonton, Alberta, Canada, it’s no surprise that Jamie Metzger spent some time working labor jobs on construction sites. It’s one of the most common summer jobs in the city. But that’s probably the last predictable thing about this particular story.
Victor Masso: Expanding Modular in Puerto Rico
Victor Masso joined 2 Go Storage, a company started by his grandfather and father, in 2018 to develop a modular building division in the wake of the devastation caused by Hurricane Maria in 2017. Prior to joining the company, he had worked in the industry for about four years focusing on pharmaceutical, commercial, and government projects.
Eliyah Ryals: Finding the Perfect Fit
It’s not common for people to find their perfect career fit straight out of college. It’s even less common to find it in the town you grew up in. But that’s exactly what happened when Eliyah Ryals was told about vacancies at Panel Built and made the decision to apply.
Through It All, It’s Still About the Workers
By February 2024, the number of available, unfilled construction job openings had reached an all-time high. At some point, interest rates will fall, creating another surge in demand for such workers. In short, solving the nation’s skilled worker shortage issue has never been more important.
Navigating Insurance Challenges in the Modular Construction Industry
Utilizing practical written minimum insurance and indemnity requirements, along with monitoring certificates of insurance by someone who has COI training will not yield a perfect risk transfer strategy, but the exposure will be managed much better than it likely is currently.