Enhancing Building Performance with Wraptite
The Wraptite external air barrier system from the A. Proctor Group has enhanced the performance of a considerate inner-city development of retirement living apartments working in partnership with the market-leading Hadley Group.
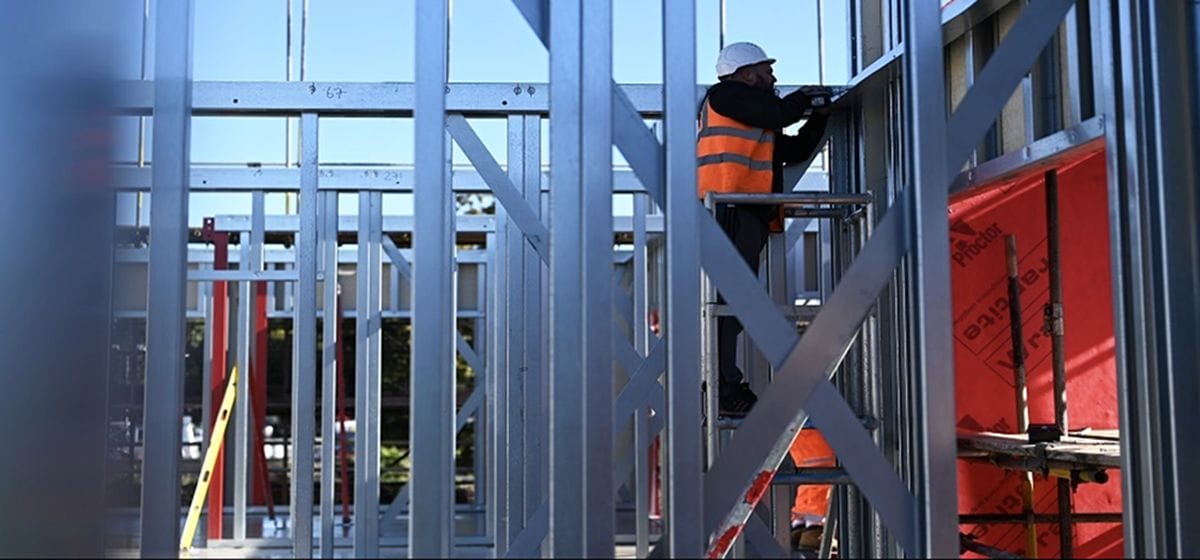
The Lichfield’s Bonds retirement living development for Pegasus Life consists of three apartment blocks in the heart of the cathedral city. Constructing on a compact site and nestled against local residents and businesses required a sensitive building approach and a considerate program design. An essential requirement for the client was ensuring that traffic was not disrupted and that the project positively contributed to the city.
The Wraptite external air barrier system from A. Proctor Group was installed in combination with the innovative, unique pre-panelized and fully load-bearing Hadley Frame offsite system, which is ideal for developments of low to medium rise structures.
The Hadley Frame system is designed to be installed off a structural concrete slab or transfer structure and provides a high strength-to-weight ratio and relative weight saving. In some cases, savings of 20-25% in weight can be achieved compared to traditional methods of construction.
Adam Salt, Business Development Manager of the A. Proctor Group explained, “one of the key benefits of installing the Wraptite air barrier system in the factory for the Hadley Group was minimal on-site disruption. Minimizing disruption on site provides significant benefits to local residents, particularly in the case of compact inner-city sites like the one at Lichfield.”
“The Wraptite air barrier system offers a safer and simplified membrane system. It provides a fully self-adhered vapor permeable air barrier certified by the BBA and combines the critical properties of vapor permeability and airtightness in one self-adhering membrane. The self-adhesive membrane is easily applied in the factory, bonded externally to the substrate, positioning the airtightness line away from the internal service penetrations ensuring a superior performance on the project.”
Joseph Sargeantson, Technical Director of the Hadley Group, explained. “The efficiency of the Hadley Frame system is significantly enhanced by the use of the Wraptite membrane from the A. Proctor Group. Combining Wraptite with Hadley Frame has enabled us to improve the air tightness and building performance and to achieve test results of 1.24m3/hr/m2.
“Wraptite is applied in the factory under controlled conditions for higher quality control and enables us to reduce on-site activity. This was particularly important on the compact site at Lichfield, where a key requirement was to minimize disruption in the local area.
“In addition to the enhanced air tightness performance, the self-adhesive design of Wraptite is ideally suited to offsite manufacture, easy and quick to apply, and provides valuable weatherproofing allowing follow-on trades to start to work much sooner.”
The superior airtightness performance of the Wraptite membrane from the A. Proctor Group delivers significant benefits to projects combining in-factory manufacture and on-site construction. The self-adhesive design ensures that the membrane is held firmly in place, even during transportation, maintaining the system’s quality from installation to build and completion.
More from Modular Advantage
Behind the Design of Bethany Senior Terraces, NYC’s First Modular Passive House Senior Housing Project
As more developers seek to meet new regulations for energy efficiency, the team at Murray Engineering has set a new record. With the Bethany Senior Terraces project, Murray Engineering has helped to develop NYC’s first modular structure that fully encompasses passive house principles — introducing a new era of energy efficiency in the energy-conscious city that never sleeps.
How LAMOD is Using Modular to Address Inefficiency, Sustainability, and the Future of Construction
As developers, designers, and contractors seek to understand the evolving needs of the modular industry, no one is as well-versed in the benefits of going modular as Mārcis Kreičmanis. As the co-founder and CBDO of LAMOD in Riga, Latvia, Mārcis has made it his ultimate goal to address the inefficiencies of traditional construction.
From Furniture Builder to ‘Activist Architect’: Stuart Emmons’ Unique Journey
Stuart Emmons was fascinated by buildings at a young age. He remembers building sand cities with his brother during trips to the Jersey shore. His father gave him his first drawing table at the age of ten. Today, he is an experienced architect who received his FAIA in June 2025. The road he took is unique, to say the least.
Forge Craft Architecture + Design: Codes, Contracts, and Intellectual Property
Founding Principal and Director of Modular Practice for Forge Craft Architecture + Design, Rommel Sulit, discusses the implications of codes, contracts, and intellectual property on
modular construction.
Eisa Lee, the “Bilingual” Architect
Now as the founder of XL
Architecture and Modular Design in Ontario, Canada, she applies not just her education as a traditional architect but an entire holistic view on modular design. It’s this expansive view that guides her work on being a true partner that bridges the gap between architects and modular factories as they collaborate on the design process.
Tamarack Grove Engineering: Designing for the Modular Sector
The role of a structural engineer is crucial to the success of a modular project, from initial analysis to construction administration. Tamarack Grove offers structural engineering services — project analysis, plan creation, design creation, and construction administration — for commercial, manufacturing, facilities, public services, and modular. Modular is only one market sector the company serves but it is an increasingly popular one.
Engineer Masters the Art of Listening to His Customers
Since founding Modular Structural Consultants, LLC. in 2014, Yurianto has established a steady following of modular and container-based construction clients, primarily manufacturers. His services often include providing engineering calculations, reviewing drawings, and engineering certification
Inside College Road: Engineering the Modules of One of the World’s Tallest Modular Buildings
College Road is a groundbreaking modular residential development in East Croydon, South London by offsite developer and contractor, Tide, its modular company Vision Volumetric (VV), and engineered by MJH Structural Engineers.
Design for Flow: The Overlooked Power of DfMA in Modular Construction
Unlocking higher throughput, lower costs, and fewer redesigns by aligning Lean production flow with design for manufacturing and assembly.
Choosing the Right Ramp
Modular construction offers a compelling alternative to traditional methods for designing and building ADA and IBC-compliant entrances. By addressing the challenges of traditional construction, such as time-consuming processes, unavailable specialized labor, and variable field conditions, modular solutions provide a more efficient, cost-effective, and reliable approach.