CertainTeed's ONE PRECISION ASSEMBLIES™ Panelized Solution
Using the latest advances in building science and prefabrication, CertainTeed developed these wall, floor, ceiling, and roof panel assemblies to meet the needs of builders and developers wanting to build higher-performing homes, faster. Prefabricated using best-in-class structural systems, insulation, windows, doors, weatherproofing, and finishes all designed to work together, these fully-constructed building panels are precision-built in a controlled environment for precise quality assurance, adherence to design, and minimal waste. The higher quality combined with the latest advances in energy and moisture simulation translates to better performing, more durable homes, while significantly increasing jobsite speed and safety. Find CertainTeed in MBI’s member directory to discuss modular building projects in your area.
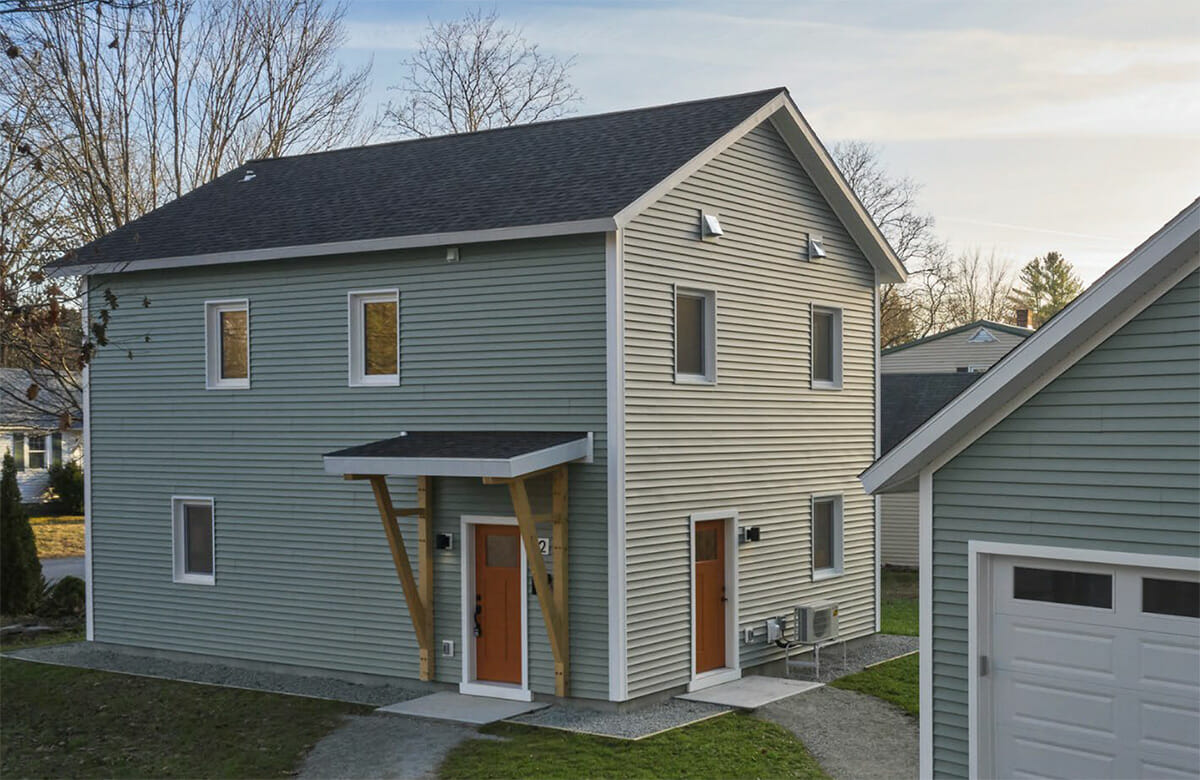
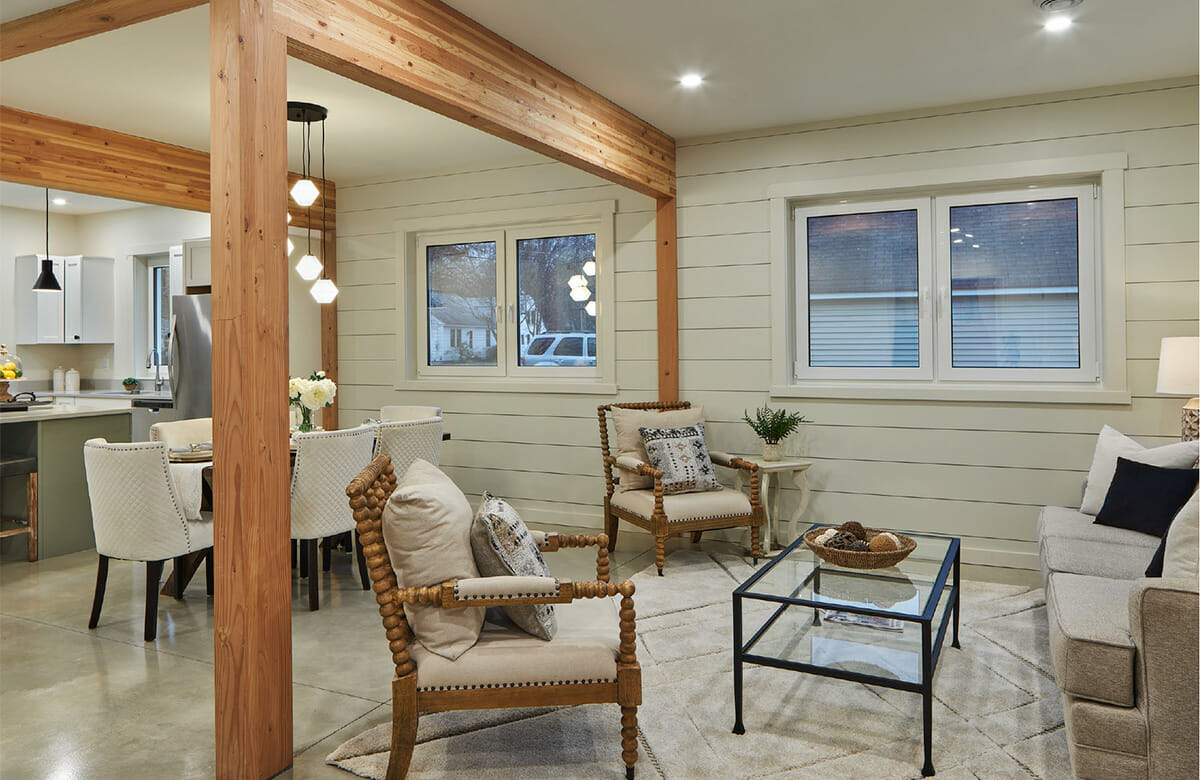
© CertainTeed, Photographs by Mark Bealer | Studio 66
“With our wide portfolio of building solutions and deep building science expertise, CertainTeed is uniquely positioned to bring exceptional value,
performance, and simplicity to the construction industry,” said Dennis Michaud, Director CertainTeed Platforms and Managing Director of CertainTeed Offsite Solutions. “We’ve seen a real need for a product like this, and now we’re nearly eliminating the challenges related to diverse, evolving codes and customer expectations around speed, sustainability, and safety.”
This launch marks a pivotal expansion of CertainTeed’s comprehensive suite of building solutions and is a prime example of how the company is making good on its promise to “make the world a better home.” With all panels customized to the builder’s design and typically exceeding local building codes, it is easier and more cost effective than ever to achieve industry-leading quality, productivity, and sustainability.
“We are confident that ONE PRECISION ASSEMBLIES will play a major role in construction as it offers a way to address current sustainability needs
and provides a solution to the ongoing housing and labor shortage,” adds Michaud. “With CertainTeed’s solution-minded strategy, market-leading
portfolio, deep building expertise, and phenomenal partners and customers, we have all of the ingredients to bring a significant, positive change to the construction industry.”
ONE PRECISION ASSEMBLIES are engineered to meet local building codes and the requirements of various energy and sustainability certifications, typically consuming less than half the energy of other new homes. While lead times vary, in-factory production is usually less than a week, with on-site installation of the wall panels in less than three days. The result is a watertight, high-performance home ready for final builder customization to the desires of their local market and customers.
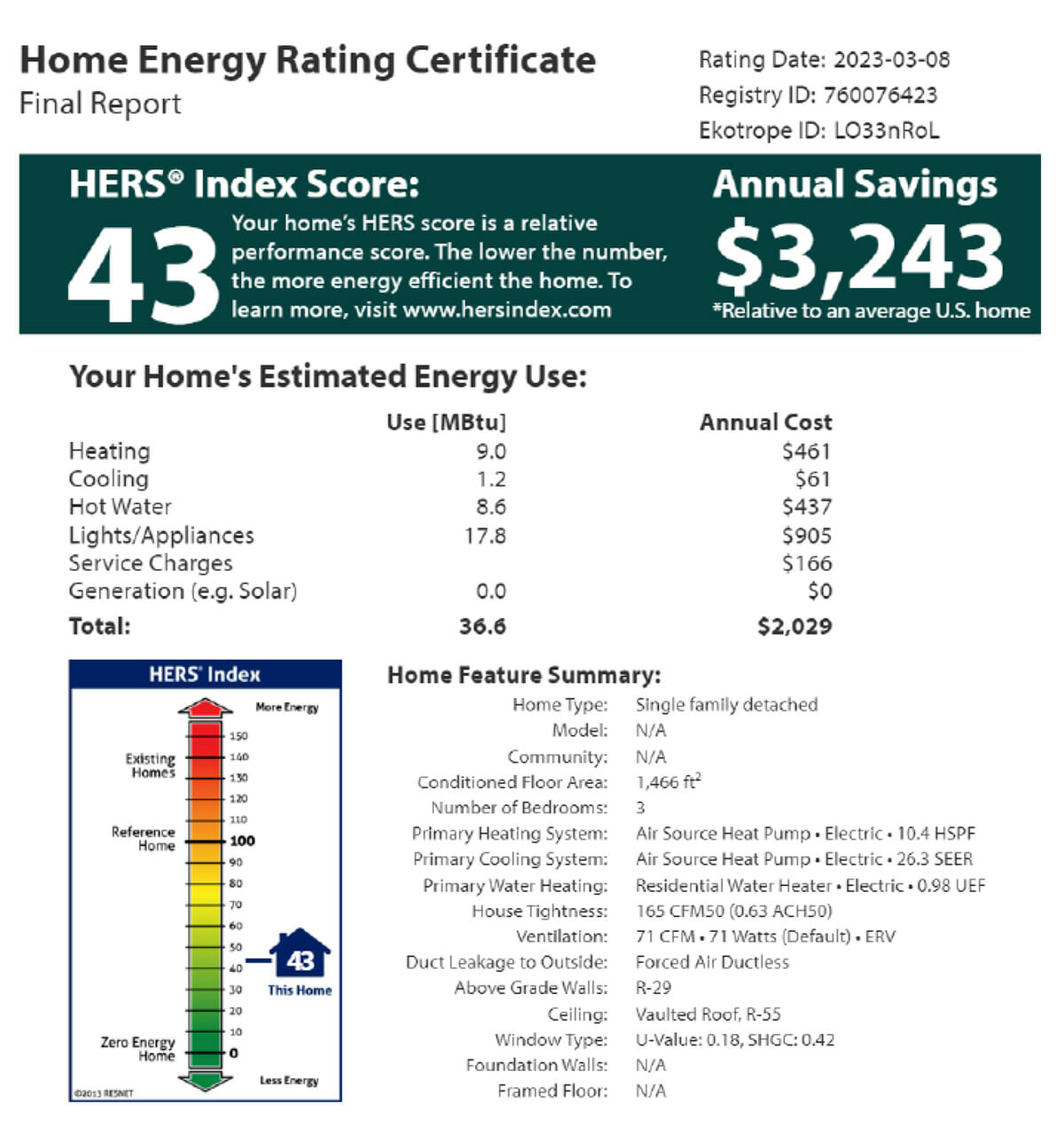
“We have listened to the needs of builders and developers asking for solutions bringing simplicity and speed,” said Mark Rayfield, CEO of CertainTeed and Saint-Gobain North America. “And following our group core values, the launch of ONE PRECISION ASSEMBLIES also addresses broader needs around labor scarcity, the need to build more homes faster, and in particular the desire for buildings that require less energy and maintenance while being healthier for building occupants and the environment.”
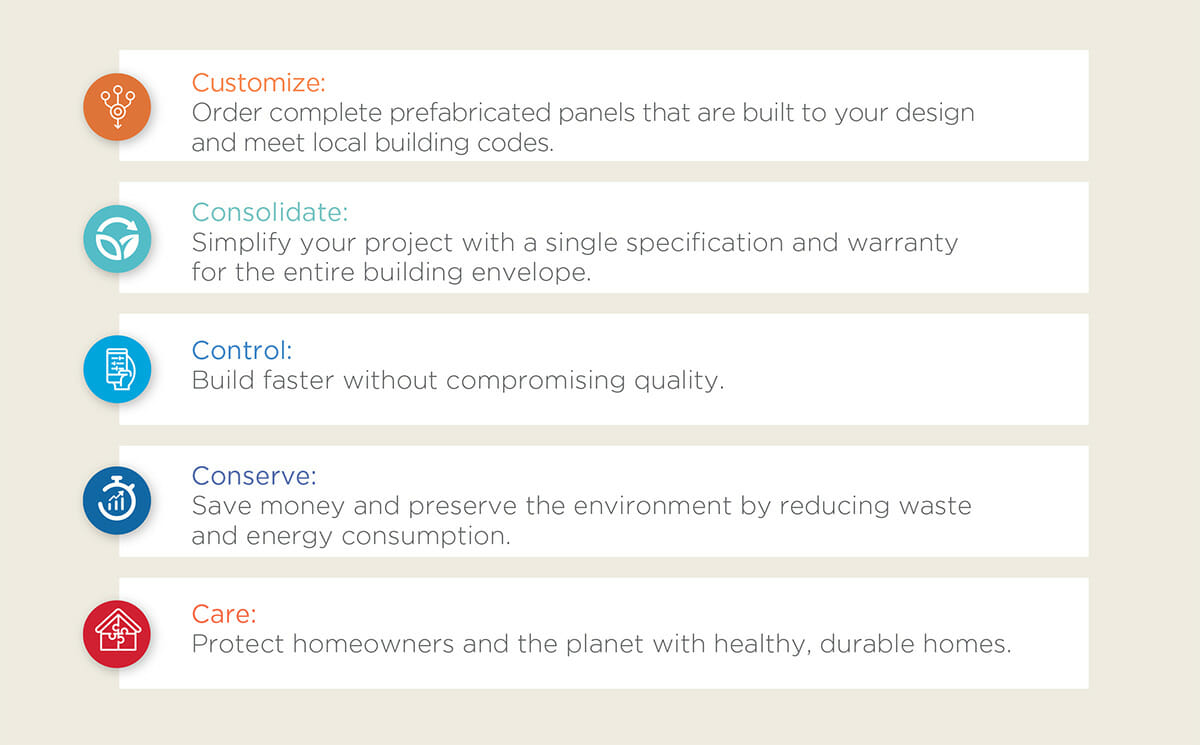
More from Modular Advantage
Samantha Taylor: Leading the (Modular) Design of Tomorrow
“With modern technology and the way we’ve all embraced things like BIM, file sharing, and video conferencing since COVID, it’s easy to collaborate with companies in Austria, or Singapore, or anywhere else in the world.”
Greg DeLeon: Military Engineering to Modular Design
Greg DeLeon, a structural engineer at ISE Structural Engineers in Temecula, California, can tell you not only how large a beam needs to be to support a house, but also how much explosives you’ll need to take it down, thanks to his unique combination of professional and military experience.
To Remake North Minneapolis, Devean George Swaps Basketball for Buildings
He’s lived in Los Angeles, Dallas, and San Francisco (to name a few). He’s delivered championships with the Los Angeles Lakers and made career-defining moves with the Dallas Mavericks and the Golden State Warriors. No matter the wins, the championships, or even the seemingly impossible 3-pointers, Devean George has always returned to where it all started for him: Minneapolis.
Chelsi Tryon: Making the World a Better Place
For Chelsi Tryon, Director of Environmental, Social, and Governance (ESG) for WillScot Mobile Mini, nothing is more enjoyable than increasing the
company’s sustainability efforts while simultaneously doing her bit to save the environment.
Joshua Hart: Pushing Boundaries
Joshua Hart, P.E., vice president at Modular
Solutions, can sum up his job responsibilities in one sentence: “I do whatever needs to be done.” Hart thrives on the variety and the opportunity to be involved in every aspect of the company. And it shows! You might say Hart has come full circle.
Jamie Metzger: From Construction to Apparel and Back Again
Growing up in a blue-collar city like Edmonton, Alberta, Canada, it’s no surprise that Jamie Metzger spent some time working labor jobs on construction sites. It’s one of the most common summer jobs in the city. But that’s probably the last predictable thing about this particular story.
Victor Masso: Expanding Modular in Puerto Rico
Victor Masso joined 2 Go Storage, a company started by his grandfather and father, in 2018 to develop a modular building division in the wake of the devastation caused by Hurricane Maria in 2017. Prior to joining the company, he had worked in the industry for about four years focusing on pharmaceutical, commercial, and government projects.
Eliyah Ryals: Finding the Perfect Fit
It’s not common for people to find their perfect career fit straight out of college. It’s even less common to find it in the town you grew up in. But that’s exactly what happened when Eliyah Ryals was told about vacancies at Panel Built and made the decision to apply.
Through It All, It’s Still About the Workers
By February 2024, the number of available, unfilled construction job openings had reached an all-time high. At some point, interest rates will fall, creating another surge in demand for such workers. In short, solving the nation’s skilled worker shortage issue has never been more important.
Navigating Insurance Challenges in the Modular Construction Industry
Utilizing practical written minimum insurance and indemnity requirements, along with monitoring certificates of insurance by someone who has COI training will not yield a perfect risk transfer strategy, but the exposure will be managed much better than it likely is currently.