Is the World Deglobalizing?
A new report from Anirban Basu, chairman & CEO of Sage Policy Group and Chief Economist of the Modular Building Institute
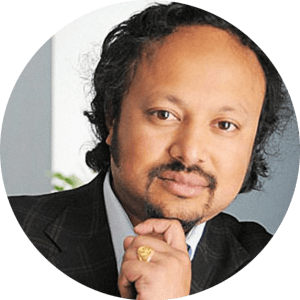
Anirban Basu is chairman & CEO of Sage Policy Group and Chief Economist of the Modular Building Institute
International Trade Matters as Much as Ever
There is a popular narrative indicating that the world is now splintering after a period of coming together. For decades, the world seemed destined to become a unified production unit. Dozens of free trade agreements, the expansion of World Trade Organization (WTO) membership, and import/export data suggested that national boundaries were falling, at least with respect to the movement of goods, including productive construction inputs.
According to the World Trade Organization’s Regional Trade Agreements Database, there are nearly 600 trade agreements in force around the world. The most common are free trade agreements between nations, but many also go so far as to support economic integration. The U.S. is party to 14 such agreements, including bilateral agreements with the Republic of Korea, Israel, and Chile. But the most important of these agreements is the US-Mexico-Canada agreement or USMCA.
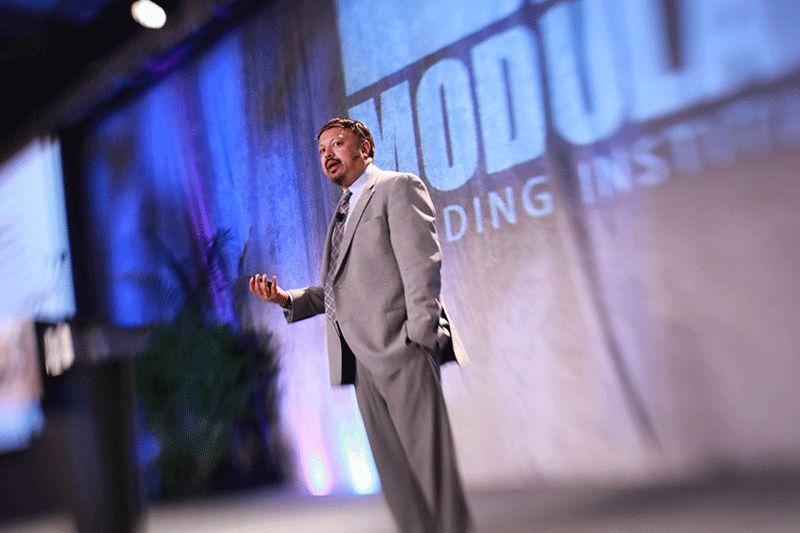
Anirban Basu speaks at MBI's annual World of Modular conference and tradeshow.
Despite trade wars and other forms of conflict, the value of global merchandise trade expanded 12 percent last year to US$ 25.3 trillion, inflated in part by elevated global commodity prices. WTO economists have estimated that merchandise trade volume growth will approach 2 percent this year and then rebound to 3.2 percent in 2024. In short, global trade remains a massive and global force. For MBI members, this means that global supply chains and their degree of functioning will continue to matter even as America seeks to restore various supply chains, including those related to computer chip and battery production.
The Current State of Global Supply Chains
As of this writing, the conflict in Ukraine enters its 17th month. With fighting spilling into Russia, the U.S. and its allies pledging additional military and financial aid to Ukraine, the impacts of the war can be felt everywhere and are spreading, but most particularly in Europe.
An interesting implication has been the further elevation of the importance of natural gas. Economic sanctions placed on Russia by the U.S. among others have forced the balance of Europe to turn to alternative energy sources. Enter liquefied natural gas (LNG). According to Glenn Rickson of S&P Global Commodity Insights, “[Natural gas] is like oil in that it’s now a global commodity via LNG and has a much higher geopolitical significance because of the events of the past year”. He added, “It is also now arguably a higher value product than oil.”
With Covid disrupting supply chains and a war in Eastern Europe following hot on its heals, it comes as no surprise that global supply chains were massively disrupted. As vaccines became widely available in the U.S. and the economy reopened in fits and starts, consumer demand surged. As indicated by the Council on Foreign Relations, “at the same time, companies in critical sectors such as warehousing struggled to attract and retail workers.
These factors, combined with years of underinvestment in U.S. infrastructure, saw goods-laden containers piling up at major ports and ships waiting for weeks to dock.”
It appears that late-2021 represented the worst for such issues. Since then, supply chains have been in recovery mode, helping to drive down many costs, including energy and other construction input costs. The New York Fed’s Global Supply Chain Pressure Index (GSCPI) indicates that in May global supply chains experienced the least pressure of any month since the start of the data series in 1997 (though the GSCPI did increase slightly in June).
Freight rate data coincide with this finding. International container rates have declined 88 percent since their peak in late 2021 according to the Freightos Baltic Index. North American truck freight rates are down more than 10 percent over the past year according to the Cass Freight Index. All things being equal, such dynamics support construction industry profitability, including within its modular building segment.
International Manufacturing
Supply chain functioning is set to improve over the next several quarters, but this has little if anything to do with supply. Weakening demand for goods in the U.S. and elsewhere will generate less pressure on manufacturers and distributors, helping to speed up delivery times.
According to S&P Global data and the Institute for Supply Management (ISM), America’s manufacturing sector is contracting in the context of rising inventory levels. A CNN report from June noted that the U.S. manufacturing sector contracted in May according to S&P Global data. ISM data indicate that the industry has been contracting for seven months. Durable goods orders have been rising in recent months, however, in large measure because of the volatile transportation sector.
In Europe, recent economic numbers point to recession for the continent’s largest economies. Reuters reported in late-July that both French and German economies are contracting. High interest rates promulgated by the European Central Bank have waylaid consumers and diminished economy activity. A Purchasing Managers’ Index covering the euro zone indicates that manufacturing activity contracted in July at its fastest pace since Covid.
And then there’s China. Global factory activity continues to slump according to many private surveys, with economists increasingly concluding that slowing growth and broadening economic weakness in China are taking a toll on the global economy. As reported by Reuters, S&P Global’s gauge of worldwide manufacturing activity stood at 48.7 in July, matching its lowest level since June 2020 when Covid was still undoing international commerce. The subindices of factory output and new orders both slipped to six month lows.
Looking Ahead
After enjoying a period of robust demand for their output, many manufacturers around the world are struggling to generate orders. Not only will that place downward pressure on prices, it will induce faster delivery times, including for input-purchasing modular builders.
At the same time, America is rebuilding critical supply chains, eventually expanding domestic production and simplifying logistics. Many of the headlines focus on the reshoring of electronics and inputs to alternative energy. Nonetheless, the trend toward reshoring is more general in nature, and should help modular builders more easily source key inputs, including sustainable timber.
At the same time, certain construction segments that tend to utilize modular building services frequently enjoy solid prospects, including single-family homebuilding, education, and healthcare. While certain key commercial real estate segments may exhibit profound weakness and risk of recession remains elevated, at this point, based on supply and demand fundamentals, the outlook for modular building appears solid.
More from Modular Advantage
DORÇE Navigates Mountainous Terrain, Extreme Weather to Help Rebuild Türkiye
The February 6 earthquakes in 2023 were enormous. In response, DORÇE moved quickly, obtaining a government bid to help create housing and multipurpose structures—both temporary and permanent—for earthquake victims and laborers hired for reconstruction efforts.
Modern Desert Oasis: Building Reset Hotel the Modular Way
While the off-site construction part of the Reset Hotel project has been carefully controlled and with every necessity close at hand at BECC Modular’s factory in Ontario, Canada, the remote location of the project site has created additional challenges for the on site portion of the build.
Revisiting Yellowstone Canyon Village—a Groundbreaking Modular Construction Feat—Ten Years On
With such a short building period due to impending cold, it made the most sense for park developer Xanterra to pursue modular. Yellowstone’s high visitor traffic also required some odd transportation scheduling, as traffic from the West Yellowstone entrance determined the times when trucks could unload modules. Guerdon was up to the challenge.
Built for Brutal Cold, This Modular Office Building Shines
Houlton, the county seat of Aroostook County, Maine, is a small town with a population of about 6,000 residents. Situated along the border between the U.S. and Canada, what the town is most known for is bitterly cold winters. When the U.S. Border Patrol needed new office space, a modular building approach from Modular Genius offered the perfect solution.
Panel Replacement Adds Years of Life to Navy Vessel
Panel Built, Inc., recently replaced all the wall and roof panels on a two-story US Navy barge deck house that the company had originally installed 30 years ago, giving the vessel new life. Now, the commanding officer of the unit that uses the barge said the difference between the condition and appearance from when the barge left their facility to when the project was complete was beyond his expectations of what was possible.
True Modular Building Seeks to Revolutionize Housing. It’s Next Stop: MBI’s World of Modular Europe
True Modular Building (TMB) specializes in crafting attainable, eco-friendly, and comfortable build-to-rent (BTR) housing with modern designs and customizable features, ensuring that residents feel at home both today and tomorrow.
From Toronto to Suriname: A Global Modular Building Story
When I AM Gold – a Canadian gold mining operation based in Toronto, Ontario – wanted to expand its mining operations in Suriname, it knew it would also need to expand its infrastructure. More specifically, they needed to build a mechanical services compound that would allow their local crews to maintain and equipment critical to their mining operations. They also knew that it would be a challenge.
There Were a “Sea of Challenges” for this Modular, Island Development
Question: Can modular construction be used to build a series of affordable, unique housing buildings, all styled to look like they were built in 1845, on an
island that caters to the wealthy? The answer is, of course, yes, but how the
team at Signature Building Systems and KOH Architecture got there is quite a story.
America’s Construction Economy: A Race Against Time
If the economy has been able to handle higher interest rates thus far, undoubtedly it will be able to manage the lower interest rates to come. But many economists are pointing out that the Federal Reserve may already be too late to the game. While they gradually reduce interest rates, the U.S. economy could quickly decelerate, at least based on theoretical grounds if not on the most recent data releases, culminating in that long-predicted recession. Only time will tell.
Top Five Benefits of Modular Office Space
Modular office spaces are transforming how businesses think about their work environments. These innovative structures offer a mix of flexibility, efficiency, and sustainability, making them a smart choice for companies looking to gain an advantage.