What is an Air Balance? The Comfort Zone
An "air balance" is a useful process for measuring the performance of a simple or complex hvac system, and for providing the occupants with a comfortably conditioned space. To understand how this process works, let's first look at the different types of air balance by defining the two extremes: Comfort Balance and AABC Certified Air Balance.
A "comfort balance" is simply checking to see whether the room feels comfortably conditioned. It may be as easy as walking from room to room, holding a hand up to the ceiling to see if sufficient air is coming out of the registers, and asking the occupants if they are comfortable. If they are not, your journey starts to discover how to resolve the HVAC problems associated with the situation. It may involve adjusting/moving registers, installing restrictors/dampers after the fact, or just insuring the air doesn't blow directly on an occupant. Many occupant complaints are associated with air circulation: too much and too little.
At the other end of the spectrum is the AABC Certified Air Balance. The purpose of this type is to insure all components of the hvac (heating, ventilating, air conditioning) system are working in harmony, at their optimum performance, providing total occupant comfort. While the journey toward a certified air balance starts before the testing stage, let's begin ours with the mechanical engineer.
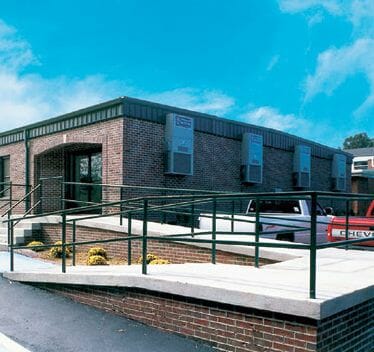
A mechanical engineer develops specifications and a set of mechanical drawings from a mix of occupant desires, local codes, ASHRAE standards, and many years of training. The correct ducting, airflow, registers, and unit performance are brought together with consideration for ventilation requirements and building exhaust needs.
The most important part of the mechanical plans used by the certified balance company is the list of "cfm" requirements next to each supply, return, intake, exhaust and ventilation opening. Without this important information a certified balance is not possible.
To conduct an AABC Certified Air Balance, the building must first be totally sealed/enclosed. Therefore this process would fall under the modular dealer's scope of work. If your project is complex, or your customer includes a certified air balance in the bid specs, be sure to include the following cost allowances on the front end:
- A mechanical engineer
- A system with products capable of a certified balance
- The cost for a balancing company
- An HVAC contractor on site during balance.
The HVAC contractor is advisable because, according to their association, a true AABC certified balance contractor must not be affiliated with any mechanical contractors, design engineers, or equipment manufacturers. So if the HVAC unit needs service during the air balance process, and an HVAC contractor is not on site, the balance will most likely stop.
A total air balance requires an opposed blade damper (OBD) behind the face of each intake and exhaust opening in each room and of the building. Other balancing dampers are required at all branch locations of the duct system.
At the building site prior to occupation, the certified balance technician will change all of the filters in the system, and insure that all dampers are fully open. Readings are taken at every opening inside, on the roof, etc. Slowly the dampers are closed in an effort to meet the cfm requirements set by the mechanical engineer. Adjusting one damper changes the cfm at all other openings. The air balance technician returns to every opening, making new adjustments and readings based on the changes from the previous one. Registers, grills, exhaust fans, and fresh air must all "balance" to meet the system performance requirements.
After the technician believes the system is all in tune, he locks down all of the dampers and other devices, so that the settings will not change. While this should keep the system "balanced," the system can be thrown out of balance by such things as dirty filters, the occupants changing the register setting, office remodeling, and reconfiguring registers and ducting.
The cost to do an AABC Certified Air Balance ranges from $75-150 per opening. You're paying for time, labor, expertise, equipment, and a Certified Balance Report. A building with five supply openings, five return openings, one exhaust fan, and one OSA intake has 12 openings to verify. Depending on the complexity and location of the openings, you can expect to pay $900-$2,000 for an AABC Certified Balance.
Is it worth it on large projects? Definitely. Remember, to avoid wasting money on your balance, be sure to install registers that the occupants cannot adjust.
Hiring a good air balance company with skillful technicians is also important. Visit www.aabchq.com for more information on the Associated Air Balance Council and a member list. The website also lists the requirements for membership, the types of certified technicians, their code of ethics, and their performance guarantee.
We have looked at the simple and the perfect air balance types, just hitting the high spots toward explaining certified air balance requirements and results. This understanding may help you avoid the temptation to put only $50 in your bid when you see your customer specifications requiring an AABC Certified Air Balance. The $50 only covers the cost of the "waving the hand" comfort balance.
More from Modular Advantage
Behind the Design of Bethany Senior Terraces, NYC’s First Modular Passive House Senior Housing Project
As more developers seek to meet new regulations for energy efficiency, the team at Murray Engineering has set a new record. With the Bethany Senior Terraces project, Murray Engineering has helped to develop NYC’s first modular structure that fully encompasses passive house principles — introducing a new era of energy efficiency in the energy-conscious city that never sleeps.
How LAMOD is Using Modular to Address Inefficiency, Sustainability, and the Future of Construction
As developers, designers, and contractors seek to understand the evolving needs of the modular industry, no one is as well-versed in the benefits of going modular as Mārcis Kreičmanis. As the co-founder and CBDO of LAMOD in Riga, Latvia, Mārcis has made it his ultimate goal to address the inefficiencies of traditional construction.
From Furniture Builder to ‘Activist Architect’: Stuart Emmons’ Unique Journey
Stuart Emmons was fascinated by buildings at a young age. He remembers building sand cities with his brother during trips to the Jersey shore. His father gave him his first drawing table at the age of ten. Today, he is an experienced architect who received his FAIA in June 2025. The road he took is unique, to say the least.
Forge Craft Architecture + Design: Codes, Contracts, and Intellectual Property
Founding Principal and Director of Modular Practice for Forge Craft Architecture + Design, Rommel Sulit, discusses the implications of codes, contracts, and intellectual property on
modular construction.
Eisa Lee, the “Bilingual” Architect
Now as the founder of XL
Architecture and Modular Design in Ontario, Canada, she applies not just her education as a traditional architect but an entire holistic view on modular design. It’s this expansive view that guides her work on being a true partner that bridges the gap between architects and modular factories as they collaborate on the design process.
Tamarack Grove Engineering: Designing for the Modular Sector
The role of a structural engineer is crucial to the success of a modular project, from initial analysis to construction administration. Tamarack Grove offers structural engineering services — project analysis, plan creation, design creation, and construction administration — for commercial, manufacturing, facilities, public services, and modular. Modular is only one market sector the company serves but it is an increasingly popular one.
Engineer Masters the Art of Listening to His Customers
Since founding Modular Structural Consultants, LLC. in 2014, Yurianto has established a steady following of modular and container-based construction clients, primarily manufacturers. His services often include providing engineering calculations, reviewing drawings, and engineering certification
Inside College Road: Engineering the Modules of One of the World’s Tallest Modular Buildings
College Road is a groundbreaking modular residential development in East Croydon, South London by offsite developer and contractor, Tide, its modular company Vision Volumetric (VV), and engineered by MJH Structural Engineers.
Design for Flow: The Overlooked Power of DfMA in Modular Construction
Unlocking higher throughput, lower costs, and fewer redesigns by aligning Lean production flow with design for manufacturing and assembly.
Choosing the Right Ramp
Modular construction offers a compelling alternative to traditional methods for designing and building ADA and IBC-compliant entrances. By addressing the challenges of traditional construction, such as time-consuming processes, unavailable specialized labor, and variable field conditions, modular solutions provide a more efficient, cost-effective, and reliable approach.