A Construction Journey from Conventional to Modular
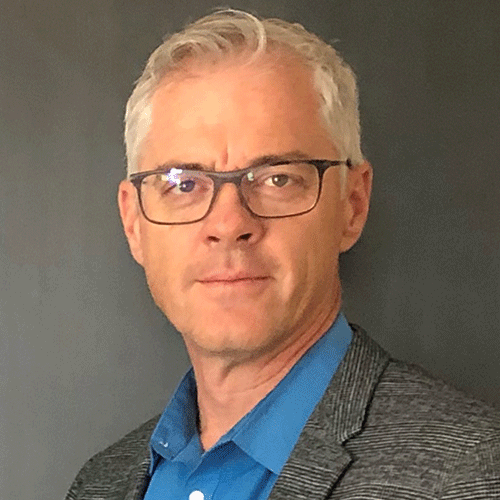
Scott Bridger is the co-founder and Vice President of Proset.
Started by Scott Bridger and Matt Mitchell in 2014, ProSet has grown from a single crew to multiple crews and about 50 installation workers across the country. Though they didn’t know each other previously, both Bridger and Mitchell were from Telluride, Colorado, and were working in the Bakken area of North Dakota and it made sense to commute from Colorado together. An opportunity for a modular construction project came to Mitchell, which he described to Bridger as a “set” project. “I really didn’t know much about modular at the time,” Bridger said, “but he (Mitchell) said the industry is growing as far as commercial modular, meaning multifamily modular and modular hospitality. And there was a sense of interest or maybe a need for a company to just simply do the modular installation scope on these commercial projects. And it was a new enough industry that there really weren’t very many companies out there who really understood how to do this kind of work, but Matt did. He had a lot of experience with it because, as a general contractor building modular apartment buildings, he was self-performing the installation work with his own crew so he knew it very well,” Bridger added.
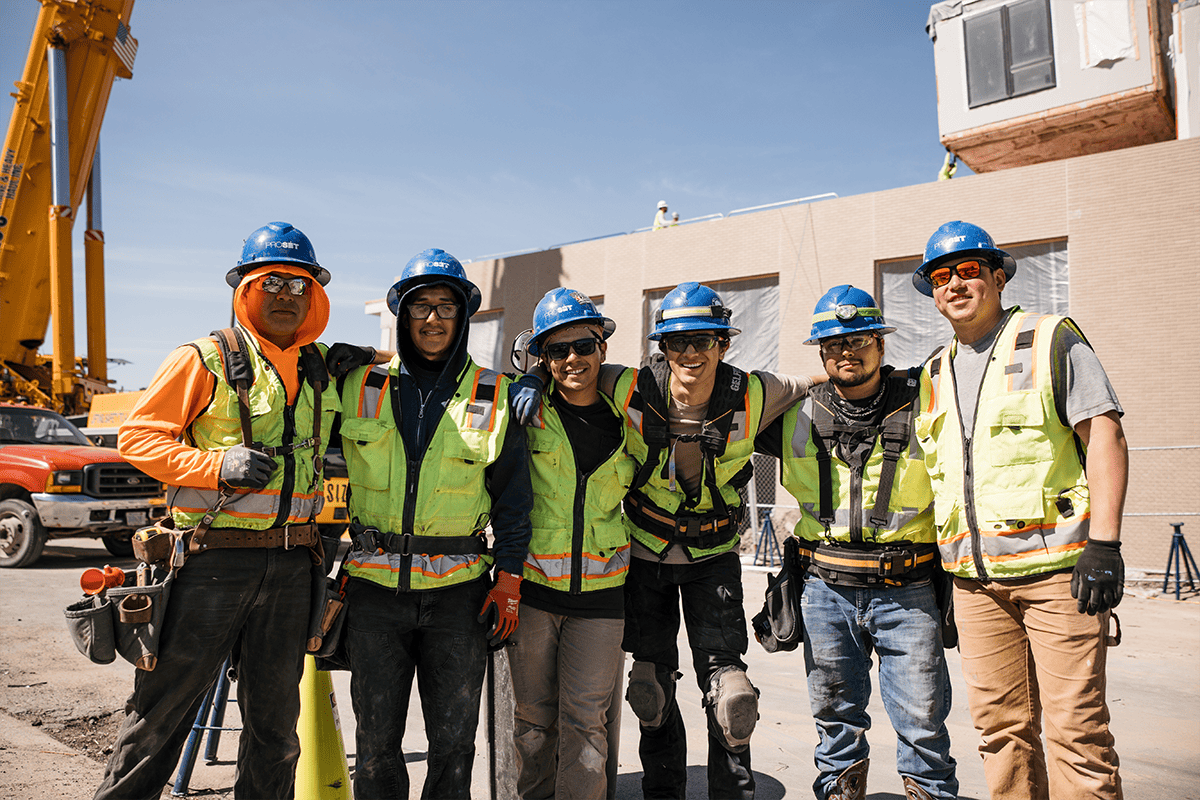
Photo by RISE Modular and Russell Heeter Photography
At that time, though, Mitchell didn’t have the crews in North Dakota to handle the project and proposed combining crews with Bridger. The idea was to create a specialty modular installation or set crew, which they did for that North Dakota Project. When that job wrapped up, the modular builder, Guerdon Enterprises, then hired Bridger’s and Mitchell’s company, which by then was officially ProSet, Inc., to work on their first Marriott Corporation project in Folsom, California, which was a Fairfield Inn. That project appears to have been a turning point for the industry. “In a lot of ways the industry took off at that point,” Bridger said. Until then, Bridger said, the consistent demand wasn’t quite there for the company’s services. It’s a specific niche of multifamily, hospitality, and assisted living. “At the time when we started this company, there was very little activity. There were very few projects anywhere in the country that were in that modular multifamily or hospitality space. There just weren’t very many manufacturers building that product yet,” he said
“So we were just maintaining one single crew going from one job to another, and to be honest, sometimes having some fairly big gaps in between our projects because there, again, weren’t that many projects out there,” he noted.
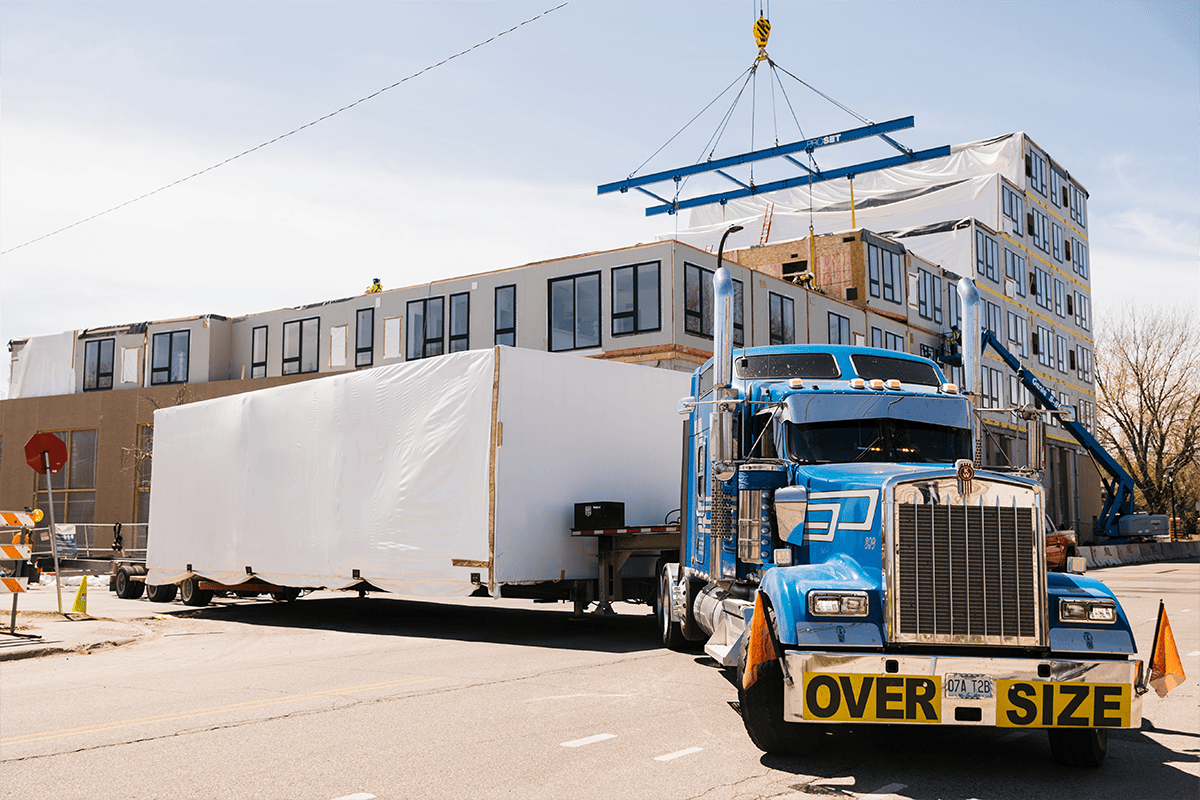
Photo by RISE Modular and Russell Heeter Photography
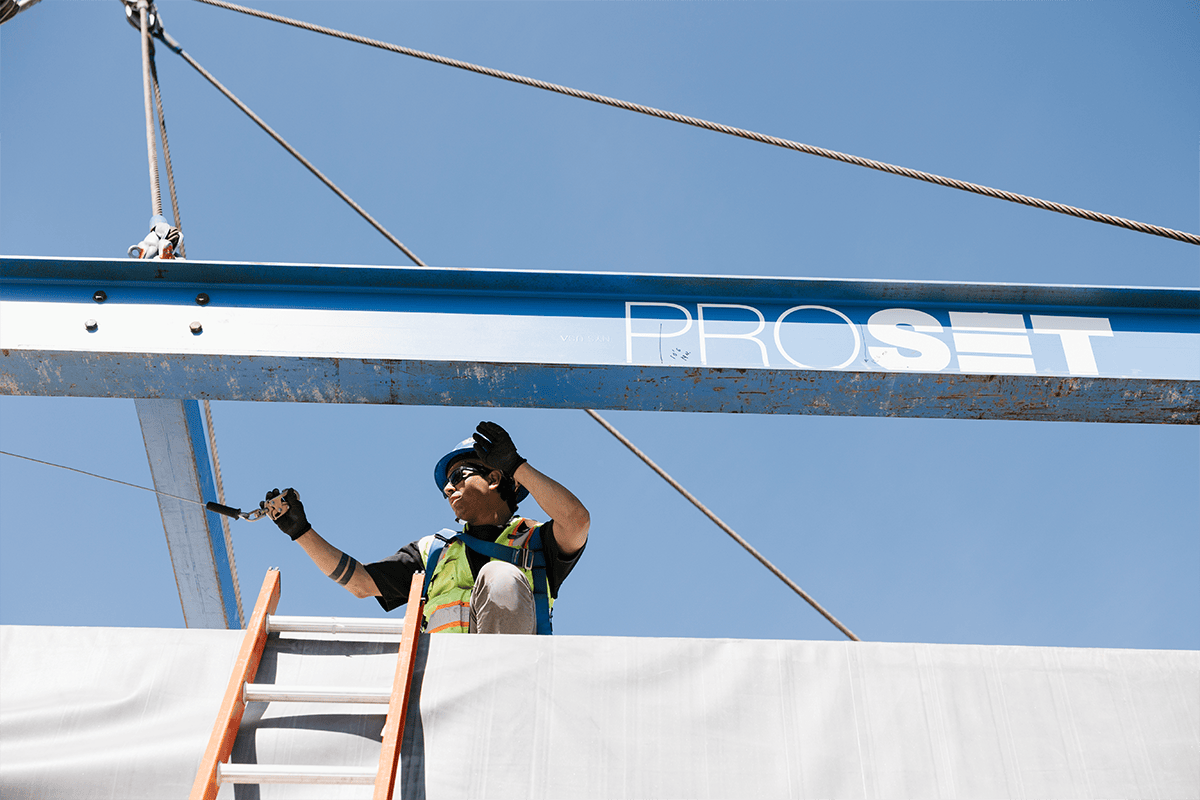
Photo by RISE Modular and Russell Heeter Photography
A Turning Point for Modular
The Fairfield Inn project for Marriott was the start of a new phase for the company, and for the commercial modular industry. “When a company like Marriott, the largest hospitality company in the world, says modular is a great way to build…it really delivered a lot of credibility to modular technology,” Bridger said. Since then, both the industry as a whole and ProSet have grown substantially, he said, and the company now has four full-time crews. “Today we’re setting for many more factories. In fact, in 2023 alone we’ll set for about 20 factories. So that just demonstrates where the growth is coming from and we see that continuing,” he noted. As an example, ProSet will install roughly 500 modular units this year for Rise Modular, a newer modular manufacturer in Minneapolis, Minnesota.
ProSet’s internal team is a major factor in the company’s continued success. Led by industry veteran and minority shareholder Chris Rimes, the company depends on traveling crews. Finding and retaining team leaders has been crucial and a building block for attracting complementary team members, he said. “Those of us who work in this industry today are going to look back years from now and say that we were part of a very significant change in how buildings get built in the United States,” Bridger said. “And so I think just by the nature of our being part of a young, dynamic industry, we are able to attract some really good talent, some forwardthinking people who are interested in being part of something exciting,” he noted.
A large part of the industry’s growth curve is due to the industry maturing and improving the product, so that a company like Marriott would become a client. And another key factor, Bridger said, is how well the key players work together in getting the projects built. The manufacturer, architect, engineer, general contractor, and developer all play crucial roles in a successful project, and it’s helpful for those professionals to have modular experience. It’s also productive when ProSet gets involved early in the project, he said.
Getting in Early Is Key
“It really helps to have experienced modular architect and engineering firms, particularly the structural engineer. And if the general contractor doesn’t have modular experience, it’s important that they have studied the process and have the right attitude about performing on a modular project,” Bridger noted. “If those stakeholders and those key players are brought together early and have a good depth of experience, that is likely going to result in a good project,” he said.
ProSet, Bridger noted, works on a variety of project types and of varying complexity, so coming in early in the process is always a benefit. single-family home with one or two modules doesn’t require much planning compared to a multi-family project. “Let’s look at a large-scale modular project where let’s say you have 100 modular units, which is kind of average for our projects. So instead of one modular box or two modular units in a single-family modular home, you’ve got maybe 100. And there’s a very specific order that those need to be installed. And so there’s going to be some pretty serious logistics planning with that process,” he said.
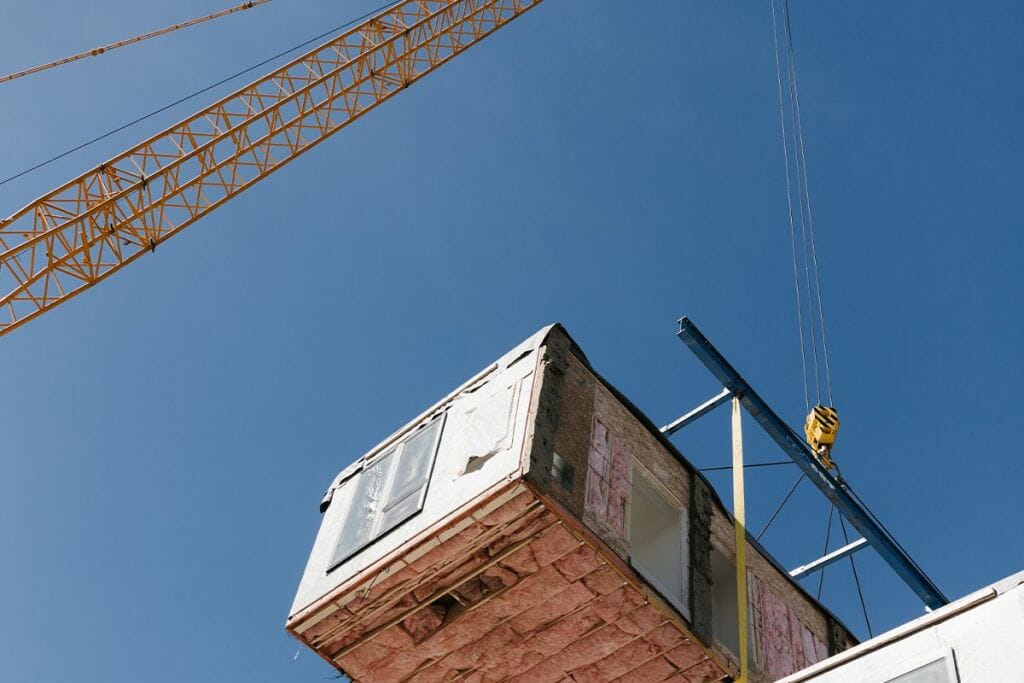
Photo by RISE Modular and Russell Heeter Photography
A big part of the planning involves determining the order of installation on the foundation at the job site, which means directing the order of manufacturing the modules at the factory, and also the order of transporting the modules to the job site or storage yard for the modules so that the erection process goes as efficiently as possible. For that reason, Bridger said, ProSet can have more impact when they’re brought in early on a project. “There’s a symphony that can be coordinated very well if we’re involved early,” he said. “We have less impact the farther into the project or later into the project we get engaged."
A Bright Future for Modular Construction
The challenges facing conventional building and the housing market are well known. A shortage of construction labor seems to be intractable, as is housing affordability in many markets across the country. Modular construction offers an alternative approach that addresses the well-known, decades-old problems of conventional construction. “Modular can really provide a lot of predictability on schedule and cost, but also can, in most cases, reduce construction durations considerably,” Bridger said. “And depending on where that particular project is, it can probably also save some money on construction costs,” he added.
Those attributes can be a major benefit in creating attainable housing all across the country, Bridger said. “Modular is not a silver bullet, but it certainly provides the opportunity to move the needle where conventional construction is just not able to keep up and certainly not able to catch up in terms of the number of modular housing units that we need across the country,” he noted. “So long story short, the industry has, I think, a very, very bright future and much as it’s grown in the last few years, I think we’ll see a considerably faster pace of growth in the modular commercial industry in years to come,” he added.
About the Author: Steve Hansen is a Colorado-based writer with a focus on the built environment—architecture, construction, renewable energy, and transportation. He can be reached on LinkedIn.
More from Modular Advantage
Samantha Taylor: Leading the (Modular) Design of Tomorrow
“With modern technology and the way we’ve all embraced things like BIM, file sharing, and video conferencing since COVID, it’s easy to collaborate with companies in Austria, or Singapore, or anywhere else in the world.”
Greg DeLeon: Military Engineering to Modular Design
Greg DeLeon, a structural engineer at ISE Structural Engineers in Temecula, California, can tell you not only how large a beam needs to be to support a house, but also how much explosives you’ll need to take it down, thanks to his unique combination of professional and military experience.
To Remake North Minneapolis, Devean George Swaps Basketball for Buildings
He’s lived in Los Angeles, Dallas, and San Francisco (to name a few). He’s delivered championships with the Los Angeles Lakers and made career-defining moves with the Dallas Mavericks and the Golden State Warriors. No matter the wins, the championships, or even the seemingly impossible 3-pointers, Devean George has always returned to where it all started for him: Minneapolis.
Chelsi Tryon: Making the World a Better Place
For Chelsi Tryon, Director of Environmental, Social, and Governance (ESG) for WillScot Mobile Mini, nothing is more enjoyable than increasing the
company’s sustainability efforts while simultaneously doing her bit to save the environment.
Joshua Hart: Pushing Boundaries
Joshua Hart, P.E., vice president at Modular
Solutions, can sum up his job responsibilities in one sentence: “I do whatever needs to be done.” Hart thrives on the variety and the opportunity to be involved in every aspect of the company. And it shows! You might say Hart has come full circle.
Jamie Metzger: From Construction to Apparel and Back Again
Growing up in a blue-collar city like Edmonton, Alberta, Canada, it’s no surprise that Jamie Metzger spent some time working labor jobs on construction sites. It’s one of the most common summer jobs in the city. But that’s probably the last predictable thing about this particular story.
Victor Masso: Expanding Modular in Puerto Rico
Victor Masso joined 2 Go Storage, a company started by his grandfather and father, in 2018 to develop a modular building division in the wake of the devastation caused by Hurricane Maria in 2017. Prior to joining the company, he had worked in the industry for about four years focusing on pharmaceutical, commercial, and government projects.
Eliyah Ryals: Finding the Perfect Fit
It’s not common for people to find their perfect career fit straight out of college. It’s even less common to find it in the town you grew up in. But that’s exactly what happened when Eliyah Ryals was told about vacancies at Panel Built and made the decision to apply.
Through It All, It’s Still About the Workers
By February 2024, the number of available, unfilled construction job openings had reached an all-time high. At some point, interest rates will fall, creating another surge in demand for such workers. In short, solving the nation’s skilled worker shortage issue has never been more important.
Navigating Insurance Challenges in the Modular Construction Industry
Utilizing practical written minimum insurance and indemnity requirements, along with monitoring certificates of insurance by someone who has COI training will not yield a perfect risk transfer strategy, but the exposure will be managed much better than it likely is currently.