Make Allies and Win Together
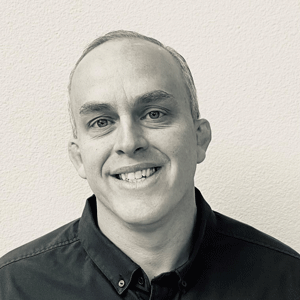
Landon Boucher is the director of business design and innovations at MiTek Inc.
Off-Site Construction is a term that has become a bit of a buzzword (that’s putting it mildly). Everyone these days, seems to tout the same exasperated (albeit valid) talking points about being built in a factory-controlled environment, improved processes, sustainability, reduced on-site build cycle, labor etc.
What many fail to mention, unfortunately, is that none of this matters if we have the wrong people managing it all. It is not just about process or product. It’s about people. All three are needed to make building successful.
Too often, those of us in the off-site construction sector dismiss the incredible accomplishments of our on-site construction counterparts and the tradesmen and women that are the workforce behind this industry. It’s inaccurate to claim that not much has changed in the last 100 years in the way we build homes. The list of what has changed in the last 20 years alone is too long for this post. What has always amazed me about construction is the people. The people who build our homes, our communities, our world. It is the people who have developed improved processes and products and it is the people who must be relied upon to utilize them efficiently. Like all things with people, sometimes we do it well and sometimes we don’t. This reality exists just as much in off-site construction. I have seen many projects delayed, factories failed, and processes not followed. Every single time, I can point to the people as the key factor in derailing otherwise well thought out plans.
I do believe off-site construction can be the better solution. All things being equal (i.e., good process, product, and people), I believe off-site teams will outperform on-site teams every time. But we need to be honest with ourselves and our industry by acknowledging that many times things are not equal. I think we do a disservice to the advancement of off-site construction when we fail to recognize (and furthermore, proclaim) this truth.
In lieu of making claims about how “traditional construction” is outdated, slow, and prone to problems, how about we work together, create allies, and foster a relationship of collaboration? I see a lot of posts on social media and in industry presentations that contain side-by-side comparisons of off-site and on-site construction. One photo is a messy and disorganized project and the other is a clean, well-managed depiction of just-in-time delivery methods utilizing mods or panels. I don’t ever see anyone share the failures of their own respective side of this equation. As a consultant for many years to contractors, engineers, and manufacturers, I’ve seen the failures and successes of both. I’ve seen them up close. Some I’ve even been responsible for, at least on some level.
It is my hope that we will see further progress in continuous improvement of construction by letting down our guards and engaging in collaborative efforts where we can share best practices and lessons learned based on our own direct experiences. A rising tide will raise all ships.
Let’s be authentic in our communications and win together.
More from Modular Advantage
DORÇE Navigates Mountainous Terrain, Extreme Weather to Help Rebuild Türkiye
The February 6 earthquakes in 2023 were enormous. In response, DORÇE moved quickly, obtaining a government bid to help create housing and multipurpose structures—both temporary and permanent—for earthquake victims and laborers hired for reconstruction efforts.
Modern Desert Oasis: Building Reset Hotel the Modular Way
While the off-site construction part of the Reset Hotel project has been carefully controlled and with every necessity close at hand at BECC Modular’s factory in Ontario, Canada, the remote location of the project site has created additional challenges for the on site portion of the build.
Revisiting Yellowstone Canyon Village—a Groundbreaking Modular Construction Feat—Ten Years On
With such a short building period due to impending cold, it made the most sense for park developer Xanterra to pursue modular. Yellowstone’s high visitor traffic also required some odd transportation scheduling, as traffic from the West Yellowstone entrance determined the times when trucks could unload modules. Guerdon was up to the challenge.
Built for Brutal Cold, This Modular Office Building Shines
Houlton, the county seat of Aroostook County, Maine, is a small town with a population of about 6,000 residents. Situated along the border between the U.S. and Canada, what the town is most known for is bitterly cold winters. When the U.S. Border Patrol needed new office space, a modular building approach from Modular Genius offered the perfect solution.
Panel Replacement Adds Years of Life to Navy Vessel
Panel Built, Inc., recently replaced all the wall and roof panels on a two-story US Navy barge deck house that the company had originally installed 30 years ago, giving the vessel new life. Now, the commanding officer of the unit that uses the barge said the difference between the condition and appearance from when the barge left their facility to when the project was complete was beyond his expectations of what was possible.
True Modular Building Seeks to Revolutionize Housing. It’s Next Stop: MBI’s World of Modular Europe
True Modular Building (TMB) specializes in crafting attainable, eco-friendly, and comfortable build-to-rent (BTR) housing with modern designs and customizable features, ensuring that residents feel at home both today and tomorrow.
From Toronto to Suriname: A Global Modular Building Story
When I AM Gold – a Canadian gold mining operation based in Toronto, Ontario – wanted to expand its mining operations in Suriname, it knew it would also need to expand its infrastructure. More specifically, they needed to build a mechanical services compound that would allow their local crews to maintain and equipment critical to their mining operations. They also knew that it would be a challenge.
There Were a “Sea of Challenges” for this Modular, Island Development
Question: Can modular construction be used to build a series of affordable, unique housing buildings, all styled to look like they were built in 1845, on an
island that caters to the wealthy? The answer is, of course, yes, but how the
team at Signature Building Systems and KOH Architecture got there is quite a story.
America’s Construction Economy: A Race Against Time
If the economy has been able to handle higher interest rates thus far, undoubtedly it will be able to manage the lower interest rates to come. But many economists are pointing out that the Federal Reserve may already be too late to the game. While they gradually reduce interest rates, the U.S. economy could quickly decelerate, at least based on theoretical grounds if not on the most recent data releases, culminating in that long-predicted recession. Only time will tell.
Top Five Benefits of Modular Office Space
Modular office spaces are transforming how businesses think about their work environments. These innovative structures offer a mix of flexibility, efficiency, and sustainability, making them a smart choice for companies looking to gain an advantage.