Lean Construction – A Tool to Drive Productivity
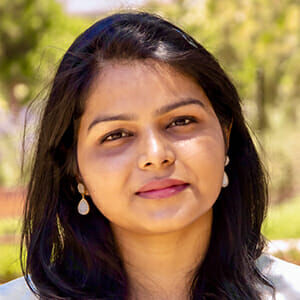
Sneha Kumari, MBA, Six Sigma, is the manufacturing SME at New Gen Architects
As a Lean and Six Sigma Leader, I have highlighted below the importance of using Lean tools and inculcating the culture to address productivity issues facing modular construction.
According to a McKinsey report1, the construction sector overall accounts for a significant 13% of the global GDP. However, despite its substantial contribution, the sector’s annual productivity growth has only witnessed a meager 1% increase over the past two decades. This starkly contrasts with the 2.8% growth observed in the world economy and the 3.6% growth seen in the manufacturing sector. Additionally, modular construction2 could claim $130B of the U.S./Europe market by 2030, saving $22B annually and bridging a $1.6T productivity gap. Based on these findings, it becomes crucial for modular industries to prioritize operational efficiency to deliver maximum value to their customers.
While there are undoubtedly a multitude of causes contributing to this lag in productivity—both internal and external factors—there are specific internal factors that can be addressed to drive incremental improvements in efficiency and ultimately enhance productivity levels. In the face of labor shortages in the industry, enhancing productivity and efficiency with existing systems and processes becomes crucial. Lean methodologies offer valuable tools to achieve these goals.
Implementing a lean culture brings transformative impact by addressing operational challenges, reducing waste, and fostering continuous improvement. It emphasizes respect for people and delivers exceptional customer value. Lean breaks down silos, optimizes operations, and creates a proactive work environment.
Eliminating waste is a primary focus of lean methodology in construction, targeting defects, overproduction, waiting, non-utilized skills, transportation, inventory, motion, and over-processing. A range of tools can be utilized to tackle different types of waste in processes, effectively minimizing or eliminating their impact. This article highlights a few of these tools and the benefits of using them.3 But before we get into the tools that can be leveraged, it is important to note that you cannot improve what you cannot visualize. Exactly why it is important to map your current value stream.
Value Stream Mapping (VSM) is a team-based methodology that involves mapping out each step of the working process and identifying waste aka areas for improvement. VSM focuses on adding value and eliminating waste to achieve optimal outcomes. By visualizing the entire process and addressing non-value-added steps, teams can enhance efficiency and create a more streamlined workflow. This can be accomplished using simple colored sticky notes or any digital tool. However, for optimal engagement, it is highly recommended to conduct the exercise using sticky notes, ensuring active participation from the team during the initial mapping process. These mapping exercises can be eye-opening, revealing the significant amount of back-and-forth that teams go through before achieving a desired outcome. For example, traveling to different stations to get material and tools to finishing building the steel trusses because the materials are not close to the point of use.
Once you know the current state and the wastes highlighted in the process, you can start with one of the foundational tools of Lean which is 5S (Figure 1). The 5S methodology promotes workplace organization and efficiency by focusing on five key steps.
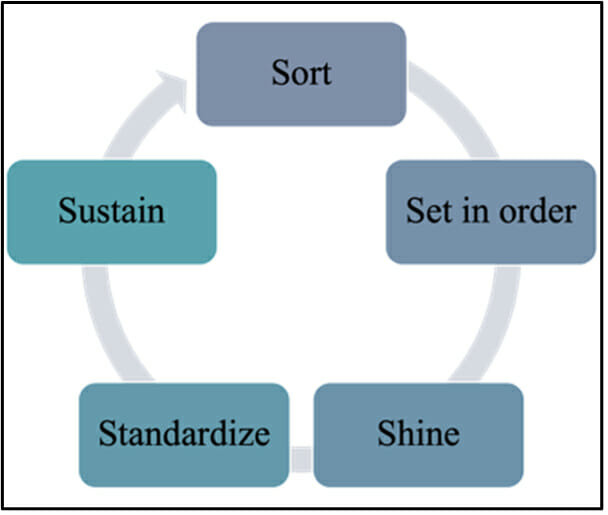
Figure 1. 5S Model.
- First, “Sort” involves determining what is necessary and removing anything that is not, reducing clutter and improving safety.
- Next, “Set in Order” establishes designated places for everything, streamlining workflow and reducing time wasted searching for materials.
- The third step, “Shine,” emphasizes consistently keeping the workspace clean and operational, preventing messes and equipment issues.
- “Standardize” involves creating standardized processes facilitating continuous improvement.
- Finally, “Sustain” emphasizes the importance of maintaining implemented processes.
Implementing the 5S methodology offers numerous benefits extending beyond the desire for a clean and organized work environment. It enhances safety by reducing hazards and the risk of accidents caused by cluttered workspaces. It improves the quality of outcomes by allowing individuals to focus on their work without distractions. Additionally, 5S enhances productivity as workers can easily locate materials and information, optimizing their time spent on value-adding tasks. Lastly, it contributes to better project scheduling through pull planning and consistent organization, ensuring materials are available when and where they are needed.
By embracing 5S principles, teams can achieve improved safety, quality, productivity, and adherence to project schedules. The investment of time and effort in creating an organized workspace pays off significantly in advancing towards project objectives.
Another valuable tool to visualize the team’s work and provide a quick overview of ongoing and completed tasks is a Kanban board (Figure 2). This is a project management system in Lean design and construction that enhances process efficiency through visualizing the workflow on a Kanban board.
This pull system aligns with Lean principles by starting work precisely where and when needed. By using the Kanban Board, teams can effectively visualize, plan, and set Work in Progress limits for different project stages. This exercise involves visualizing the workflow, setting Work In Progress limits, managing flow, conducting regular meetings, and collaboratively improving processes based on feedback.
The Kanban Board consists of sections like “To Do”, “In Progress”, and “Done”. These boards can exist in physical boards or even on digital tools as preferred by teams. By adhering to these practices, teams can optimize workflow, achieve continuous improvement, and deliver greater value to stakeholders.
While utilizing the Kanban board for work management, encountering complex problems that require in-depth analysis and critical problem-solving calls for another effective tool called A3 thinking. This exercise can be conducted on a simple sheet of paper or digitally, allowing for a deeper dive into the problem and facilitating a structured problem-solving approach.
A3 problem solving is a powerful Lean methodology that empowers teams to tackle problems collaboratively and make informed decisions. The essence of A3 thinking lies in laying the entire problem onto a single sheet of paper, allowing the team members to collaborate, analyze, and rationalize their problem-solving process. This approach not only enhances problem- solving process but also generates detailed written explanations that can be shared with senior management, fostering their confidence in the team’s capabilities. It guides the team through a systematic approach, leveraging the available tools and resources to arrive at the most effective countermeasure.
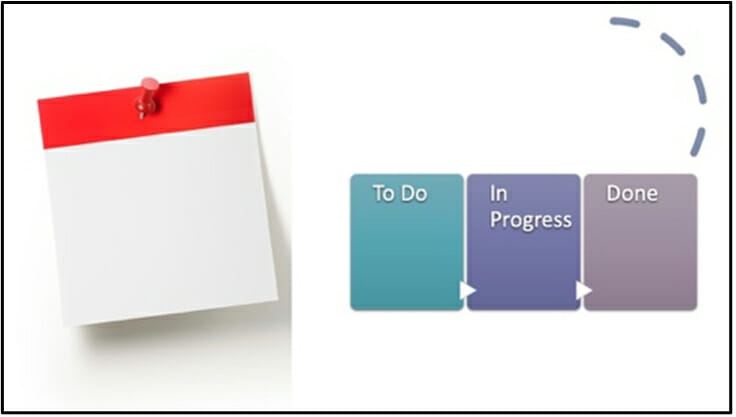
Figure 2. Kanban board
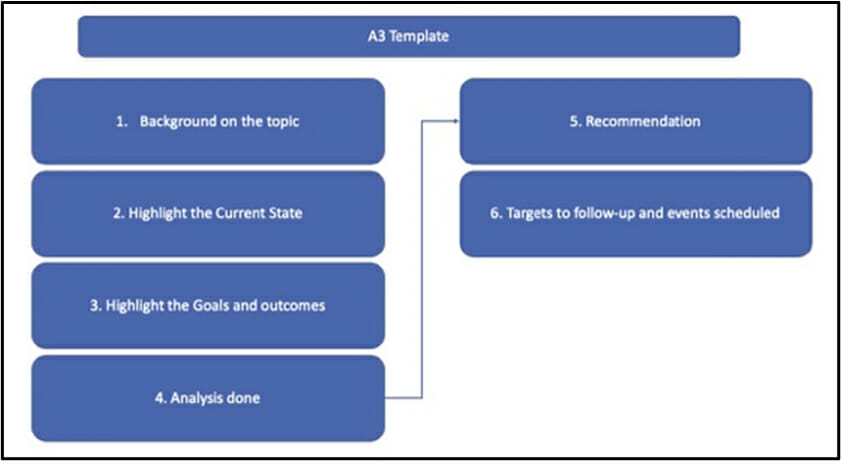
Figure 3. A3 template.
To ensure a thorough and well-rounded analysis, an A3 report (Figure 3) is typically filled out by a designated champion who gathers input and insights from team members. This collective knowledge and expertise contribute to a more holistic understanding of the problem and increase the likelihood of a satisfying outcome.
Before diving into the A3 process, it is crucial to accurately identify and define the problem at hand. In the context of design and construction, challenges such as unexpected lead times or communication breakdowns are common. By addressing key questions and clarifying the problem’s nature, teams can set the stage for successful A3 problem solving and navigate the path towards resolution.
It is important to note that Lean is a mindset and a culture that will need to be fostered over time and instilled with leadership leading it for others to follow. It is extremely important to manage and tread this change carefully. Organizations should identify and empower ambassadors or change agents who can champion this transformation. Respecting all employees and valuing their contributions is essential in creating a supportive culture. Investing in upskilling initiatives and providing opportunities for continuous learning demonstrates the recognition that people are the most valuable asset of a company.
By establishing mutual trust between management and employees, organizations can cultivate a collaborative atmosphere
that encourages innovation and growth.
More from Modular Advantage
Behind the Design of Bethany Senior Terraces, NYC’s First Modular Passive House Senior Housing Project
As more developers seek to meet new regulations for energy efficiency, the team at Murray Engineering has set a new record. With the Bethany Senior Terraces project, Murray Engineering has helped to develop NYC’s first modular structure that fully encompasses passive house principles — introducing a new era of energy efficiency in the energy-conscious city that never sleeps.
How LAMOD is Using Modular to Address Inefficiency, Sustainability, and the Future of Construction
As developers, designers, and contractors seek to understand the evolving needs of the modular industry, no one is as well-versed in the benefits of going modular as Mārcis Kreičmanis. As the co-founder and CBDO of LAMOD in Riga, Latvia, Mārcis has made it his ultimate goal to address the inefficiencies of traditional construction.
From Furniture Builder to ‘Activist Architect’: Stuart Emmons’ Unique Journey
Stuart Emmons was fascinated by buildings at a young age. He remembers building sand cities with his brother during trips to the Jersey shore. His father gave him his first drawing table at the age of ten. Today, he is an experienced architect who received his FAIA in June 2025. The road he took is unique, to say the least.
Forge Craft Architecture + Design: Codes, Contracts, and Intellectual Property
Founding Principal and Director of Modular Practice for Forge Craft Architecture + Design, Rommel Sulit, discusses the implications of codes, contracts, and intellectual property on
modular construction.
Eisa Lee, the “Bilingual” Architect
Now as the founder of XL
Architecture and Modular Design in Ontario, Canada, she applies not just her education as a traditional architect but an entire holistic view on modular design. It’s this expansive view that guides her work on being a true partner that bridges the gap between architects and modular factories as they collaborate on the design process.
Tamarack Grove Engineering: Designing for the Modular Sector
The role of a structural engineer is crucial to the success of a modular project, from initial analysis to construction administration. Tamarack Grove offers structural engineering services — project analysis, plan creation, design creation, and construction administration — for commercial, manufacturing, facilities, public services, and modular. Modular is only one market sector the company serves but it is an increasingly popular one.
Engineer Masters the Art of Listening to His Customers
Since founding Modular Structural Consultants, LLC. in 2014, Yurianto has established a steady following of modular and container-based construction clients, primarily manufacturers. His services often include providing engineering calculations, reviewing drawings, and engineering certification
Inside College Road: Engineering the Modules of One of the World’s Tallest Modular Buildings
College Road is a groundbreaking modular residential development in East Croydon, South London by offsite developer and contractor, Tide, its modular company Vision Volumetric (VV), and engineered by MJH Structural Engineers.
Design for Flow: The Overlooked Power of DfMA in Modular Construction
Unlocking higher throughput, lower costs, and fewer redesigns by aligning Lean production flow with design for manufacturing and assembly.
Choosing the Right Ramp
Modular construction offers a compelling alternative to traditional methods for designing and building ADA and IBC-compliant entrances. By addressing the challenges of traditional construction, such as time-consuming processes, unavailable specialized labor, and variable field conditions, modular solutions provide a more efficient, cost-effective, and reliable approach.