Enthusiasm for Modular Construction Grows in Ukraine as Rebuilding Efforts Take Shape
The future of Ukraine may be uncertain, but one thing isn’t: rebuilding will be a monumental task.
Bruce Talley, Chief Operating Officer at MBI member company OFC Incorporated, is trying ensure that Ukraine’s eventual rebuilding efforts are based in a technology known for its speed and adaptability: modular construction.
During his most recent visit to Ukraine, Talley was invited to share his knowledge of the industry at several building conferences. His first stop: KyivBuilds.
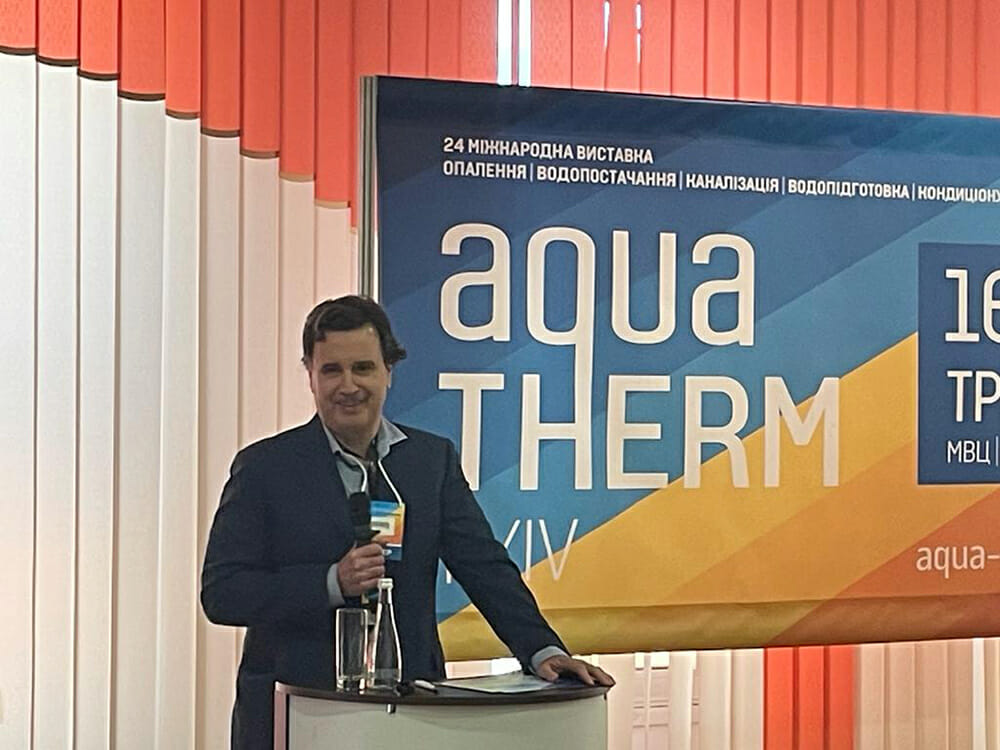
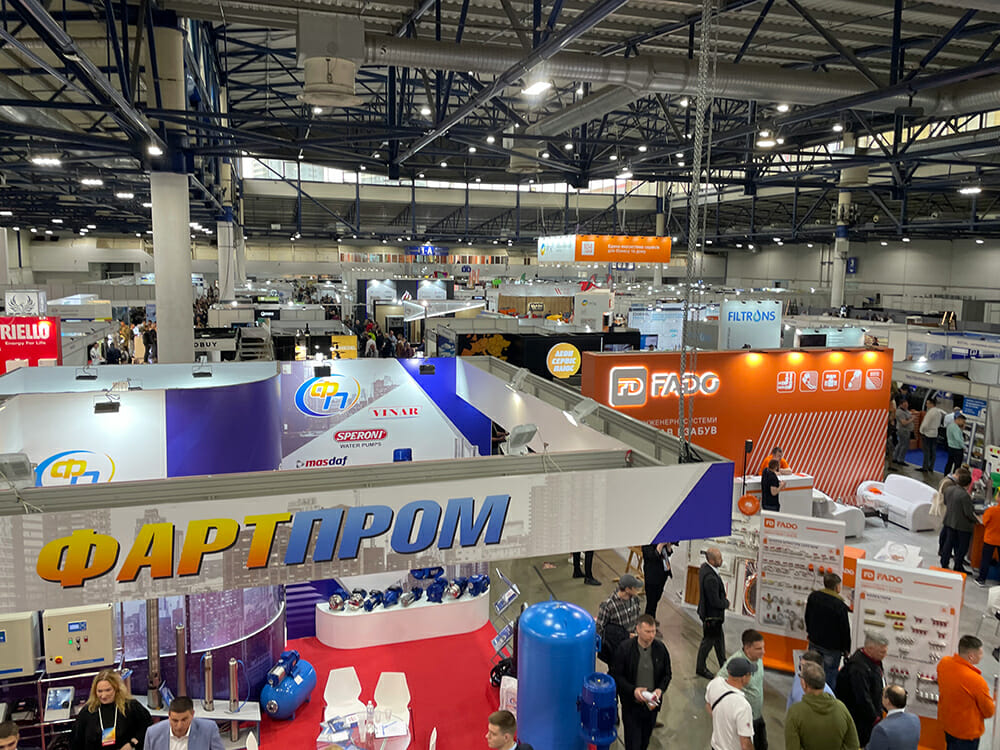
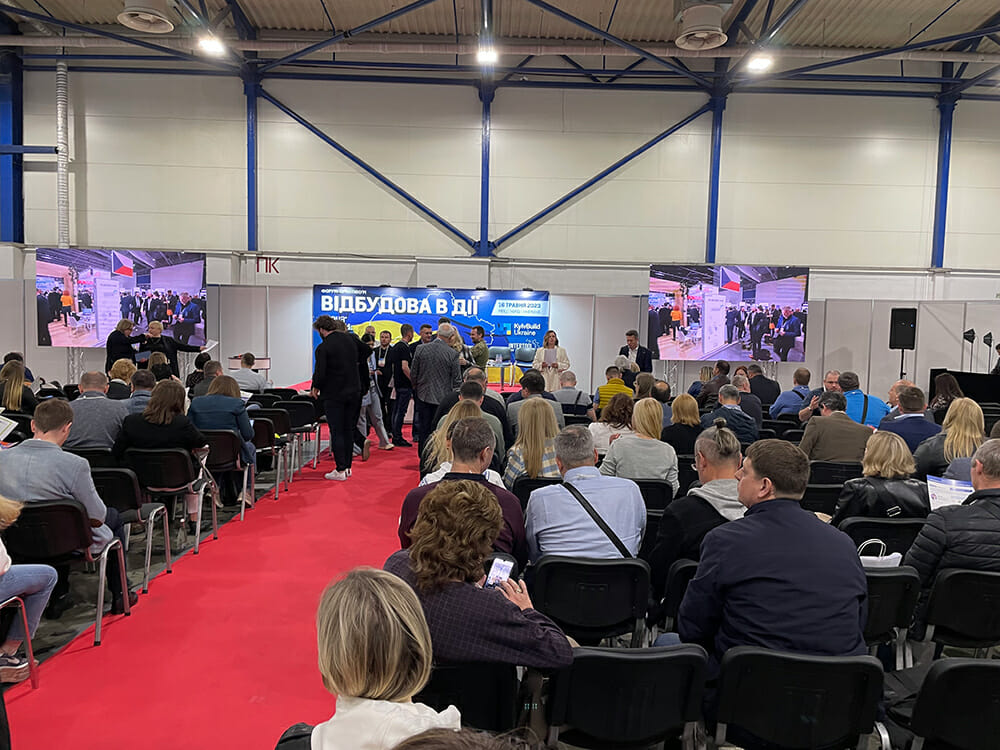
Bruce Talley, chief financial officer at OFC Inc., speaks at KyivBuilds in May, 2023.
Hosted in Ukraine’s capitol May 16-17, the KyivBuilds conference was attended by over 7,300 people with 161 companies exhibiting. There Talley spoke to a group of Ukrainian mayors, developers, and architects about modular housing. Talley then traveled to Irpin and Zhytomyr to talk about modular building applications in those cities.
“The quality of modular building and the uses are much greater than I realized. Modular building will be in great demand in Ukraine to solve housing,” said Oleksandr Markushin, Mayor of Irpin.
“I learned a lot from Bruce's presentation. I think modular building will be very important for Ukraine's rebuilding,” said Artem Shira, director of Nerex, a water treatment and purification company.
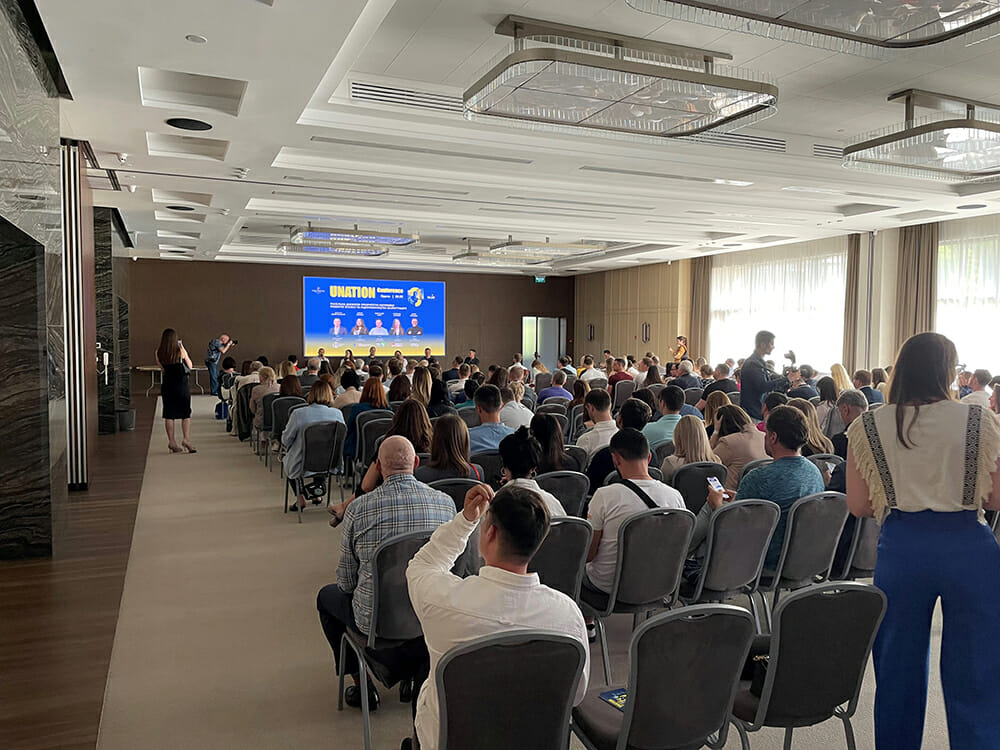
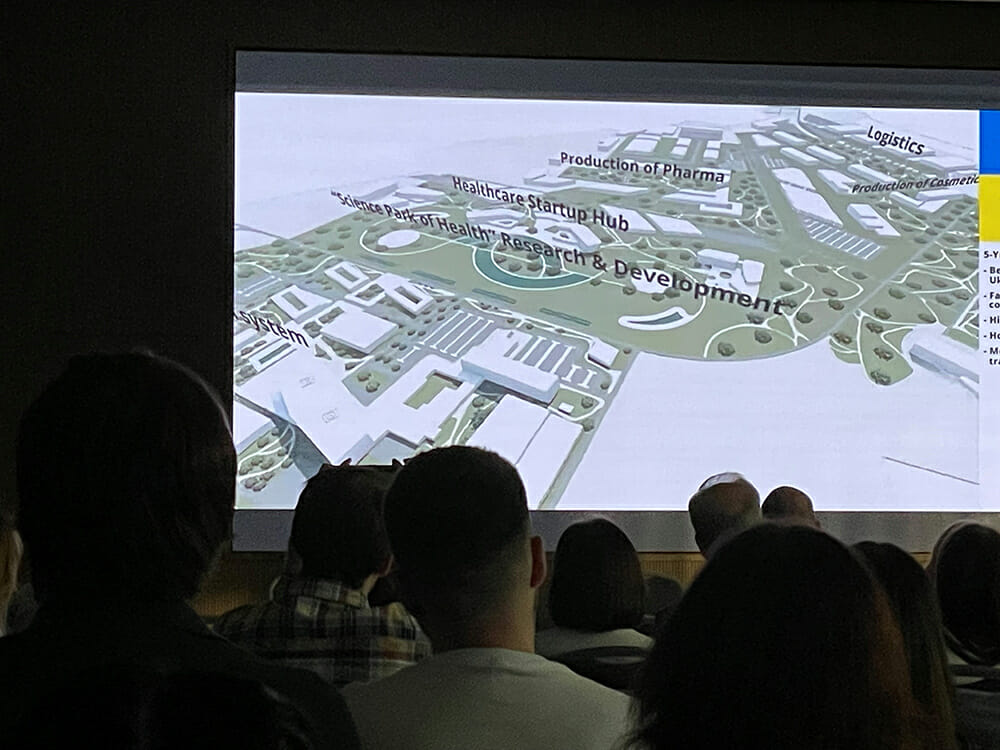
Bruce also presented at the UNation conference in Odesa on May 20, 2023.
Following his talks in Kyiv, Irpin, and Zhytomyr, Talley attended the UNation conference on May 20th in Odesa. Topics included rebuilding, tech incubators, and the reforms that Ukraine needs to instate to attract foreign investment, as well as regional issues affecting Odesa. Also discussed were several large business parks to be developed in Ukraine, with retail, housing, Olympic training, medical, offices, and redevelopment of an airport.
Related Listening:
Rebuilding Ukraine: What Modular Manufacturers, Dealers, and Developers Need to Know w/ OFC, Inc
Bruce Talley, chief operating officer of OFC Inc., discusses the current conditions inside Ukraine, including the state of its infrastructure and housing, and recounts his personal experience and observations from recent visits. Bruce also shares important information for modular companies looking to help in the relief and rebuilding efforts.
The opportunities for modular construction in Ukraine, it seems, are boundless. But for the industry to make an impact, inroads will need to be made.
“In general,” said Talley, “I’m in Ukraine to meet with people, look at potential production sites (especially in western Ukraine, but not limited to there), and discuss modular housing and container conversion applications for apartments, homes, retail, offices, schools, and hospitals. Everyone is interested in solutions that will save time and money and control costs and outcome. Clearly, employment is driving a lot of thought. However, at each event I have attended that has been a lot of discussion around Smart Cities and sustainable development. So much has been damaged in some areas, that instead of rebuilding like it was, cities will look and work differently with new infrastructure.”
It's early yet to make predictions on when rebuilding efforts can be made in earnest, but Talley sees an opportunity for the global industry to get involved when the time is right. That said, it won’t be a cake walk.
“When we're talking about getting involved in Ukraine, there is a steep learning curve," says Talley. "There are cultural and legal barriers that will be new to many, especially to North American companies. So, it's possible. But if a manufacturer or builder wants to acquire our abilities, our knowledge, our culture, cultural understanding and language skills, and ability to bridge that gap, I think we can do that very well.”
About the Author: John McMullen, PCM, is the marketing director for the Modular Building Institute. You can reach him directly at mcmullen@modular.org or on LinkedIn.
More from Modular Advantage
Samantha Taylor: Leading the (Modular) Design of Tomorrow
“With modern technology and the way we’ve all embraced things like BIM, file sharing, and video conferencing since COVID, it’s easy to collaborate with companies in Austria, or Singapore, or anywhere else in the world.”
Greg DeLeon: Military Engineering to Modular Design
Greg DeLeon, a structural engineer at ISE Structural Engineers in Temecula, California, can tell you not only how large a beam needs to be to support a house, but also how much explosives you’ll need to take it down, thanks to his unique combination of professional and military experience.
To Remake North Minneapolis, Devean George Swaps Basketball for Buildings
He’s lived in Los Angeles, Dallas, and San Francisco (to name a few). He’s delivered championships with the Los Angeles Lakers and made career-defining moves with the Dallas Mavericks and the Golden State Warriors. No matter the wins, the championships, or even the seemingly impossible 3-pointers, Devean George has always returned to where it all started for him: Minneapolis.
Chelsi Tryon: Making the World a Better Place
For Chelsi Tryon, Director of Environmental, Social, and Governance (ESG) for WillScot Mobile Mini, nothing is more enjoyable than increasing the
company’s sustainability efforts while simultaneously doing her bit to save the environment.
Joshua Hart: Pushing Boundaries
Joshua Hart, P.E., vice president at Modular
Solutions, can sum up his job responsibilities in one sentence: “I do whatever needs to be done.” Hart thrives on the variety and the opportunity to be involved in every aspect of the company. And it shows! You might say Hart has come full circle.
Jamie Metzger: From Construction to Apparel and Back Again
Growing up in a blue-collar city like Edmonton, Alberta, Canada, it’s no surprise that Jamie Metzger spent some time working labor jobs on construction sites. It’s one of the most common summer jobs in the city. But that’s probably the last predictable thing about this particular story.
Victor Masso: Expanding Modular in Puerto Rico
Victor Masso joined 2 Go Storage, a company started by his grandfather and father, in 2018 to develop a modular building division in the wake of the devastation caused by Hurricane Maria in 2017. Prior to joining the company, he had worked in the industry for about four years focusing on pharmaceutical, commercial, and government projects.
Eliyah Ryals: Finding the Perfect Fit
It’s not common for people to find their perfect career fit straight out of college. It’s even less common to find it in the town you grew up in. But that’s exactly what happened when Eliyah Ryals was told about vacancies at Panel Built and made the decision to apply.
Through It All, It’s Still About the Workers
By February 2024, the number of available, unfilled construction job openings had reached an all-time high. At some point, interest rates will fall, creating another surge in demand for such workers. In short, solving the nation’s skilled worker shortage issue has never been more important.
Navigating Insurance Challenges in the Modular Construction Industry
Utilizing practical written minimum insurance and indemnity requirements, along with monitoring certificates of insurance by someone who has COI training will not yield a perfect risk transfer strategy, but the exposure will be managed much better than it likely is currently.