Modernizing the Construction Sector
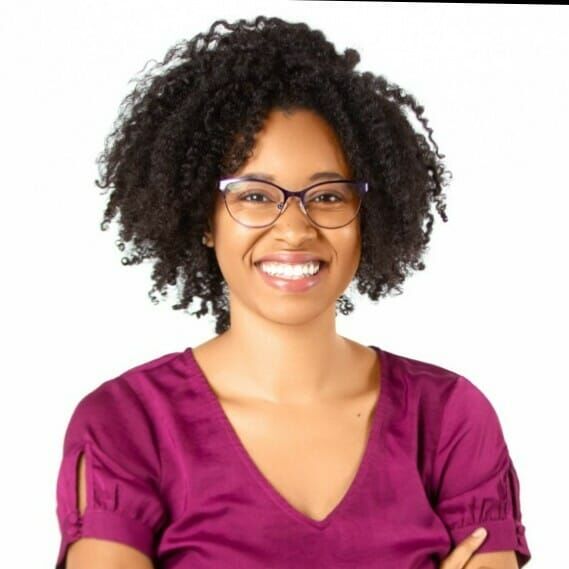
Dyci Manns Sfregola, CSCP, MS, is the founder and Managing Director of New Gen Architects.
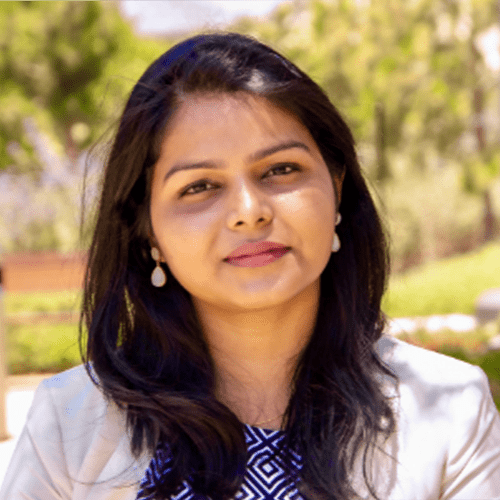
Sneha Kumari, MBA, Six Sigma, is the Manufacturing Principal at New Gen Architects.
Just as the retail and manufacturing sectors transformed themselves with digitization and automation to greatly improve lagging productivity, the construction sector must do the same. Here’s an argument that supports the case for modular construction in pursuing greater productivity:
Parts of the industry could move toward a manufacturing-inspired mass-production system, in which the bulk of a construction project is built from prefabricated standardized components off-site in a factory. Adoption of this approach has been limited thus far, although it’s increasing. Examples of firms that are moving in this direction suggest that a productivity boost of five to ten times is possible.
Source: Reinventing Construction Through A Productivity Revolution
Navigating the path to a modernized construction sector has been a challenge for most firms. But thanks to supply-chain experts like New Gen Architects and Dyci Sfregola, CEO, and Sneha Kumari, Principal Consultant, leading modular construction firms are currently improving supply chain management and seeing productivity growth.
Prior to starting New Gen in 2020, Sfregola worked for other firms and smaller companies would regularly approach her about accessing consulting services. However, the firms she worked for did not service small and medium businesses. This led her to found New Gen Architects in 2020 with the goal of providing value-added quality digital consulting and advisory services to SMBs.
“I spent a lot of time on sales calls where we essentially told companies that they were too small to work with us,” she noted. “You can’t work with everyone. But what I then saw is that there wasn’t someone with a lot of experience and really driving a lot of the best practices at that mid-market and small business level.”
At that point, Sfregola had the idea for a new firm that serves smaller companies. “I really wanted to create New Gen to provide the same service and the same quality of service for the mid-market and small businesses.”
As NGA developed into a supply chain consulting firm heavily focused on tech, Sfregola talked with Kumari about “an intelligent shop floor and project management tool she was working on for prefab and modular companies,” Sfregola said. With her supply chain experience and expertise, Kumari was a natural fit for NGA, enabling the company to “provide value to the industry from both a technical and business process perspective.”
By that point, Kumari had been working as a supply chain manager for roughly a decade for large corporations like Honeywell and Schneider Electric. In performing ERP (enterprise resource planning) implementations for those companies, she was exposed to home automation products, in addition to manufacturing and retail e-commerce concepts. She also has a background with lean processes, Six Sigma, and Kaizen, the Japanese business concept of continuous improvement for all employees and company processes.
Those clients introduced her to the construction sector and its need for more technology tools. “I was working together with the customers and understanding how the processes work,” Kumari said. “What are the gaps? Then I saw the gap and also an understanding of how to work in a project-based business, and how to be able to use the tech tools for your processes to see that productivity come through and improve your bottom line while also focusing on sales.”
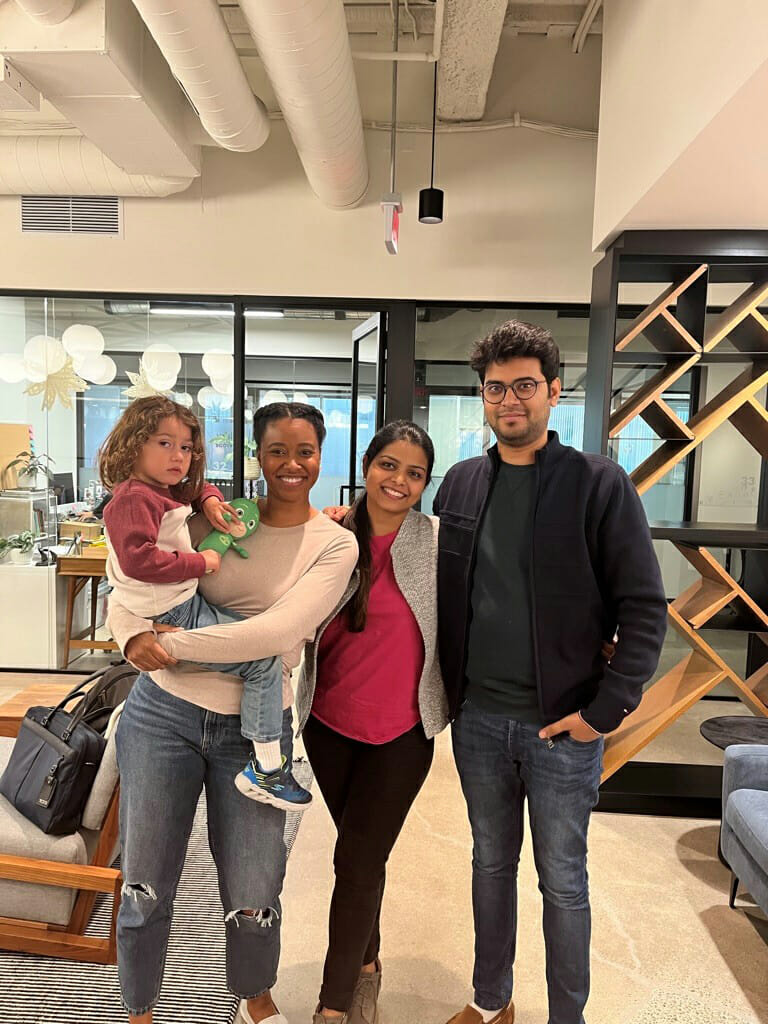
Dyci Sfregola and Sneha Kumari pose in their New Gen Architects office.
Another key factor for New Gen is learning why a company continues to follow “outdated” or under-productive processes. It’s easy to conclude from an outside perspective that they’re doing it wrong, Sfregola noted. “I think that most people are very intelligent. And it was the least bad choice of the bad choices.” Figuring out the why is Kumari’s superpower, Sfregola added. “The analysis and the value-stream mapping and really figuring out ‘What are you doing now and why is that happening?’ And then I can say ‘Okay, now what technologies can we layer on to that to enable whatever process improvement?’ So we play off each other very well.”
Supply Chain Engineering: The Magic of Systems
Supply chain engineering is the overall process that maximizes the performance of a company’s supply chain while minimizing costs. It aims to improve the efficiency and effectiveness of the flow of more than just product, though. It’s effective at improving flow for information and services, too.
“Supply chain engineering is actually you really getting your hands dirty,” Kumari said, “getting into the processes, going at the level of the user, the doer, whoever is part of that process, mapping it out. I think a lot in terms of problem solving.”
In addition, she considers how to use the technology tools at hand to get the desired ROI. She also uses tools like Lean Six Sigma to evaluate the current state of processes, and also considers all these factors in relation to the company’s strategic goals. “Managing this change is supply chain engineering to me, and it’s a holistic view instead of just working in silos,” she said.
Sfregola likens the engineering functions to having “boots on the ground,” and New Gen’s architecture functions to the “30,000 foot view.” “The architecture is thinking about the entire big picture of all of the things that the supply chain also touches outside of the supply chain function,” she said. “Your finance, your marketing, your sales, your customer, thinking about what your customer is going to want, thinking about how employees are now going to interact in order to provide what the customer wants, and architecting that in a way for the engineers to then go and execute. The architecture is the high level and then the engineering is the actual boots on the ground, executing on what the architects have designed.”
"Supply chain engineering is actually you really getting your hands dirty, getting into the processes, going at the level of the user, the doer, whoever is part of that process, mapping it out. I think a lot in terms of problem solving.”
— Sneha Kumari, Manufacturing Principal, New Gen Architects
How Modular Constructors Can Optimize Using Supply Chain Engineering
Modular construction is sort of a hybrid, Sfregola said, with elements of both manufacturing and construction. “It’s a unique cross of two industries and honestly not like any other industry I’ve worked with in the past,” she added. It’s also a relatively young part of the construction sector, with great opportunities to learn from more mature industries that have already optimized with automation and digitization, to name just two examples.
Common mistakes Sfregola sees from modular constructors include continuing with manual execution and planning, which hinders the growth of scale and creates the inability to meet demand. “That’s the biggest mistake I see,” she noted, “not investing as much, if not more time, energy, and resources in supply chain and ops.”
A positive step for growth and operational excellence she typically recommends is embracing documentation for current processes and their network. “It never ceases to amaze me how many people just don’t know what’s happening and the visibility into what everyone is doing,” she said. Getting into the gritty details of everything is the way to optimize and grow.
“Just documenting, not even doing the exercise of identifying the ideal state, just only documenting the current state,” Sfregola said. Crucial questions include: How long does it take you to get paid? How long does it take you to pay people and what are the steps involved?
“It provides a lot of insights into unnecessary and redundant spin. And then when you’re ready to automate…then you already have all of this documented to be able to give to a [software] vendor and they can give you a realistic estimate on how long it’s going to take them to now automate, customize, and develop.” Without documentation, she emphasized, you’ll get a vendor bid for technology tools that is simply inaccurate and of little value.
Working With New Gen Architects
NGA will step in to consult at pre-implementation, during implementation, or post-implementation, Sfregola said. Ideally, a company contracts NGA early on to help them realize the successful adoption of the technology tools according to plan.
That path is unusual, though. “What happens more often than not is that they call us during the implementation” because they’ve hit some snags, such as not having their documentation in place, and/or not having qualified people in place to implement.
“So at that point, it’s minimizing the level of dumpster fire that is going to happen at go live because it’s gonna be a dumpster fire. You can see all signs lead to dumpster fire at this point,” she said.
Due to the choices that people make, such as forgoing documentation, their technology implementations do poorly. “The vast majority of technology implementations fail,” she added, “in that they don’t meet the ROI that they are expected to provide for companies. It’s like 70% or 76%...a very, very large number. So, when I was doing technology implementations, I was able to see why that was the case. And a lot of these are preventable. Things that we can fix from the very beginning to not cause these issues.”
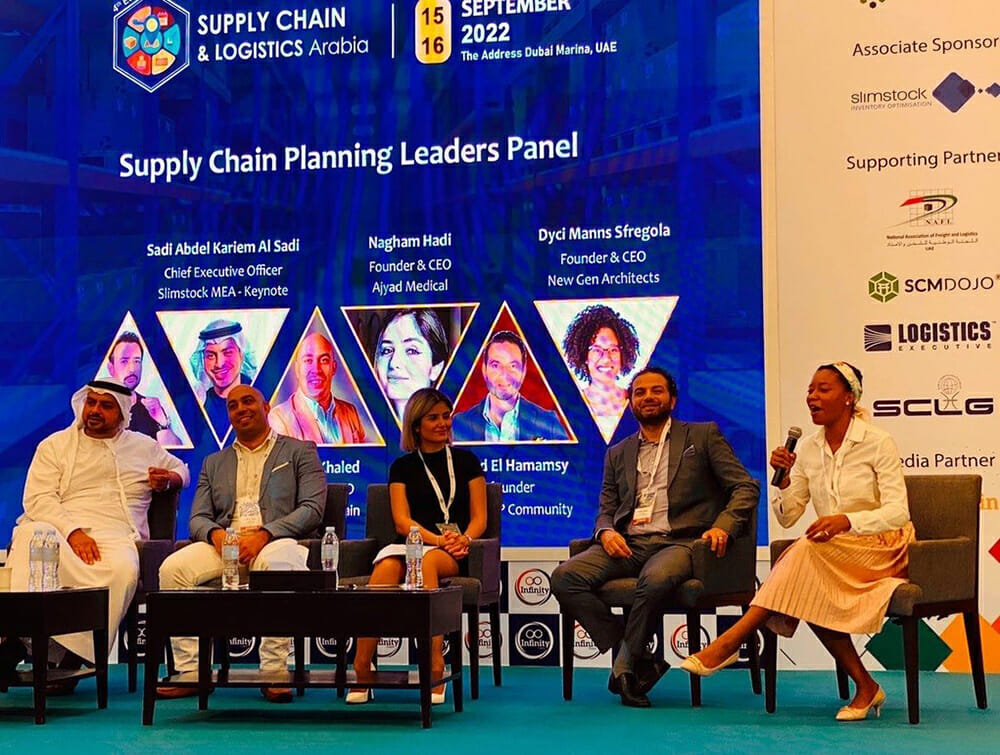
Dyci Sfregola speaks during the Supply Chain Planning Leaders panel at the 2022 Supply Chain & Logistics Arabia conference in Riyadh, Saudi Arabia.
New Generation at World of Modular
Both Kumari and Sfregola will speak at World of Modular 2023 in Las Vegas. Kumari will focus on lean concepts, Six Sigma, and continuous improvement tactics that modular constructors can readily implement to optimize their processes and develop best practices. Her presentation will offer examples of tech tools that more mature industries have implemented, as well as specific action items.
Sfregola’s presentation will focus on leveraging supply chain functions to scale a business intentionally and intelligently, developing operations and the supply chain into a competitive advantage. In addition, she’ll address appropriate technology tools for modular constructors.
About the Author: Steve Hansen is a Colorado-based writer with a focus on the built environment—architecture, construction, renewable energy, and transportation. He can be reached on LinkedIn.
More from Modular Advantage
DORÇE Navigates Mountainous Terrain, Extreme Weather to Help Rebuild Türkiye
The February 6 earthquakes in 2023 were enormous. In response, DORÇE moved quickly, obtaining a government bid to help create housing and multipurpose structures—both temporary and permanent—for earthquake victims and laborers hired for reconstruction efforts.
Modern Desert Oasis: Building Reset Hotel the Modular Way
While the off-site construction part of the Reset Hotel project has been carefully controlled and with every necessity close at hand at BECC Modular’s factory in Ontario, Canada, the remote location of the project site has created additional challenges for the on site portion of the build.
Revisiting Yellowstone Canyon Village—a Groundbreaking Modular Construction Feat—Ten Years On
With such a short building period due to impending cold, it made the most sense for park developer Xanterra to pursue modular. Yellowstone’s high visitor traffic also required some odd transportation scheduling, as traffic from the West Yellowstone entrance determined the times when trucks could unload modules. Guerdon was up to the challenge.
Built for Brutal Cold, This Modular Office Building Shines
Houlton, the county seat of Aroostook County, Maine, is a small town with a population of about 6,000 residents. Situated along the border between the U.S. and Canada, what the town is most known for is bitterly cold winters. When the U.S. Border Patrol needed new office space, a modular building approach from Modular Genius offered the perfect solution.
Panel Replacement Adds Years of Life to Navy Vessel
Panel Built, Inc., recently replaced all the wall and roof panels on a two-story US Navy barge deck house that the company had originally installed 30 years ago, giving the vessel new life. Now, the commanding officer of the unit that uses the barge said the difference between the condition and appearance from when the barge left their facility to when the project was complete was beyond his expectations of what was possible.
True Modular Building Seeks to Revolutionize Housing. It’s Next Stop: MBI’s World of Modular Europe
True Modular Building (TMB) specializes in crafting attainable, eco-friendly, and comfortable build-to-rent (BTR) housing with modern designs and customizable features, ensuring that residents feel at home both today and tomorrow.
From Toronto to Suriname: A Global Modular Building Story
When I AM Gold – a Canadian gold mining operation based in Toronto, Ontario – wanted to expand its mining operations in Suriname, it knew it would also need to expand its infrastructure. More specifically, they needed to build a mechanical services compound that would allow their local crews to maintain and equipment critical to their mining operations. They also knew that it would be a challenge.
There Were a “Sea of Challenges” for this Modular, Island Development
Question: Can modular construction be used to build a series of affordable, unique housing buildings, all styled to look like they were built in 1845, on an
island that caters to the wealthy? The answer is, of course, yes, but how the
team at Signature Building Systems and KOH Architecture got there is quite a story.
America’s Construction Economy: A Race Against Time
If the economy has been able to handle higher interest rates thus far, undoubtedly it will be able to manage the lower interest rates to come. But many economists are pointing out that the Federal Reserve may already be too late to the game. While they gradually reduce interest rates, the U.S. economy could quickly decelerate, at least based on theoretical grounds if not on the most recent data releases, culminating in that long-predicted recession. Only time will tell.
Top Five Benefits of Modular Office Space
Modular office spaces are transforming how businesses think about their work environments. These innovative structures offer a mix of flexibility, efficiency, and sustainability, making them a smart choice for companies looking to gain an advantage.