Modular Building is (Almost) as Old as the Hills
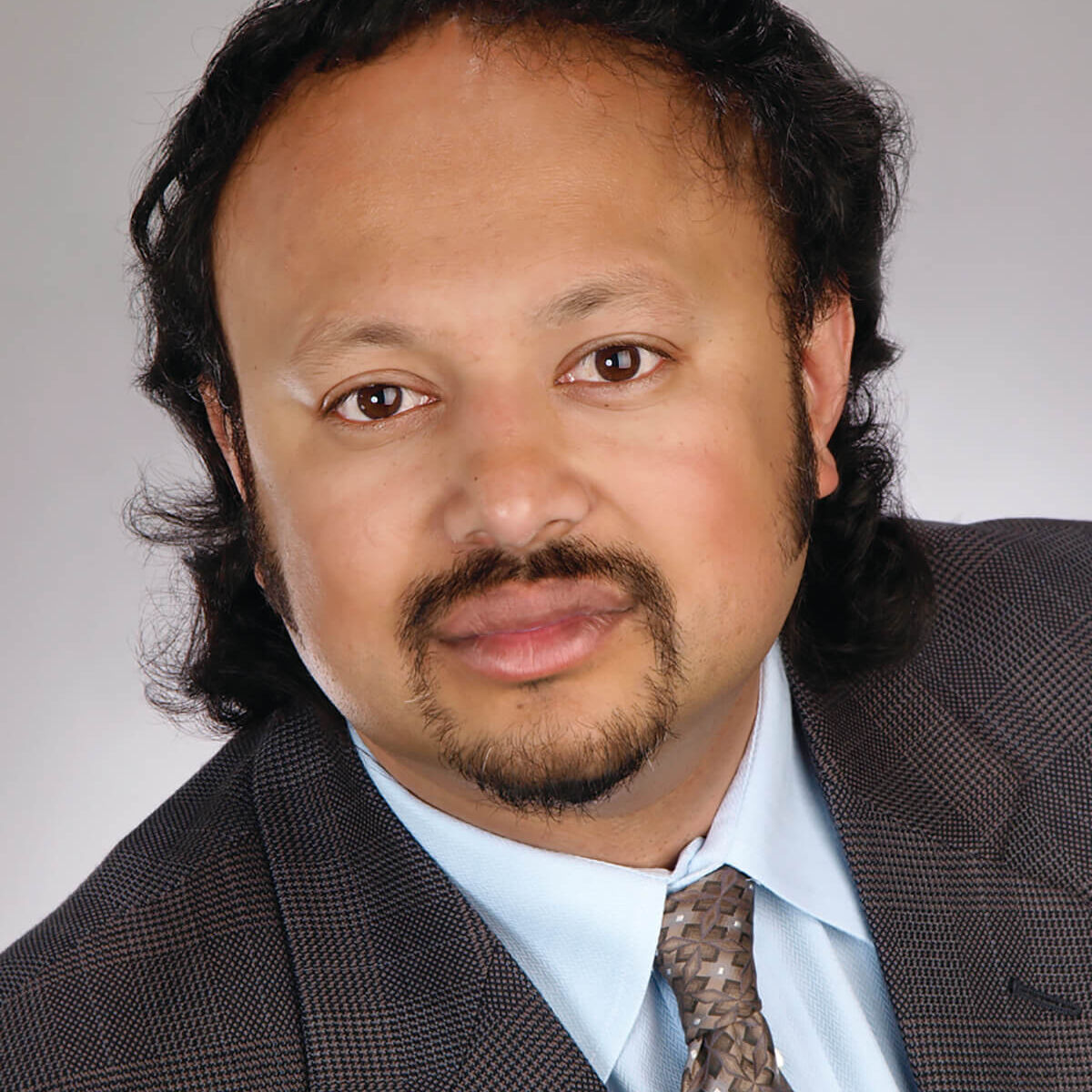
About the Author: Anirban Basu is the chairman & CEO of Sage Policy Group and chief economist of the Modular Building Institute.
Quite a History
Many view modular building as the emergent wave in construction. Controlled environments, precision manufacturing, and a highly trained workforce represent the cornerstones of the view that modular methods will continue to garner additional market share as time passes.
But despite its status as an upstart, modular building has been around for centuries. In ancient Rome, armies constructed forts in prefabricated sections.1 They brought those sections with them on their campaigns in order to facilitate easy setup in order to quickly secure newly conquered territory. The Romans are associated with many things, including philosophers, emperors, aqueducts, and stadia. Modular construction forms part of the list.
Fast forward to the 1600s. In Europe, settlers prebuilt homes and fishing houses to be transported as they moved to America. This practice was not unique to America, however. There are reports of structures being shipped from Britain to Australia.
While contemporary modular structures are far more capable than those used by Americans before there was a United States, the basic premise remains the same. By eliminating variables such as temperature and moisture, construction conducted in a controlled setting eliminates many risks, including premature deterioration of construction materials and delays in building as weather systems wreak havoc on conditions.
What is perhaps most remarkable is that, despite these advantages and the realization over the course of centuries that they exist, modular construction continues to be in its infancy from the perspective of construction market share. The industry has been striving for years to attain 5 percent market share in many categories, whether in office or healthcare construction.
In the U.S., Sears, Roebuck, and Co. brought the idea into the 20th century (literally) by offering pre-built homes in its catalog starting in 1908. The idea didn’t take off immediately, but following the Second World War, millions of veterans returned home ready to start a family. Pre-built homes emerged as a major contributor to the rapid spread of household formation and homeownership across the countryside.
Enter the history of Levittown. Starting in 1947, Abraham Levitt commenced work on one of four planned communities, the first of which was situated in Nassau County, Long Island. His son, Alfred, had returned from serving in the war.2 He urged his father to take advantage of a utilitarian approach to construction that had become popular in the U.S. Navy. Serving as chief architect for his father, he designed a simple one-floor home supplemented with an unfinished expansion attic. By the following year, they were producing about 30 houses per day, using materials from their own factories located around the country. The homes were popular. Residents quickly inhabited them. Eventually, the town was used as an archetype of the American Dream, bolstering the popularity of America’s suburbs in the process.
Over the last roughly four decades during which the Modular Building Institute has been in existence (founded 1983), prefabricated construction and modular building have expanded beyond one-floor homes in the suburbs. Today, virtually all major developers are incorporating some element of pre-built units or modules into their projects across both residential and nonresidential segments.
By the 1970s, office buildings, schools, and healthcare facilities were taking advantage of off-site construction to reduce costs and speed up delivery. Prefabrication/modular building has become increasingly popular in other parts of the world as well, including in Australia where such techniques are often used in school construction. The government there has forecasted that the number of students will expand by nearly 59 percent, or by 4 million students by 2051. To match demand to capacity, the government is predictably taking advantage of the development of modular classrooms. Much like modular homes, the classrooms are built off-site, which allows contractors to work around the year without being impacted by weather.
Labor Market Logic
It is well known that the principal challenge faced by many contractors relates to a scarcity of skilled construction workers. With Baby Boomers retiring in larger numbers and many members of the labor force, including younger ones, embracing remote work or gig jobs like driving for Lyft or Uber, shortfalls of skilled workers will plague construction for the foreseeable future.
What’s more, at-the-jobsite construction often requires the participation of local labor forces. But in booming communities like Austin, Nashville, Phoenix, Charlotte, Tampa, and elsewhere, the local labor forces are seldom able to keep up with demand. The competition between project owners to secure the efforts of general and subcontractors drives up costs of construction, which may be good for many contractors, but limits housing and other forms of affordability.
Modular building is fundamentally different. In this instance, construction activity can be divorced from where units will ultimately be delivered. This means that construction can take advantage of the national labor force as opposed to local ones. Moreover, manufacturing facilities serving construction can benefit from enormous economies of scale, reducing costs further as modular techniques continue to acquire construction market share. In short, modular building will likely help solve America’s construction worker shortfall, reducing costs and speeding construction delivery in the process.
This is hardly theoretical. An article published by Construction Dive in 2020 noted that Chick-fil-A, one of the nation’s most popular fast-food establishments, built a restaurant in Roswell, GA in three months using modular techniques. This was significantly faster than the typical 23-week build the chain routinely endures.
The company states that the modular approach “improved efficiency and time savings”, while allowing for “consistency and quality in the fast-food chain’s building across the country.” The article also notes that less waste is produced and that there is less disruption in the surrounding community, which helps to reinforce brand loyalty.
Prefabricated facilities can also limit exposure of harmful chemicals and minimize excess waste. As the world seeks to solve the problem of global warming and to improve public health outcomes, modular techniques represent part of the solution. In the final analysis, modular building has quite a history, but it has an even more spectacular future.
Endnotes
1 Gasc, Marco. “A Brief History on Modular Architecture”. GKV Architects.
2 Jackson, Kenneth T. “The Baby Boom and the Age of the Subdivision”. Ch. 13 from Crabgrass Frontier: The Suburbanization of the United States (New York: Oxford University Press, 1982), 231-245.
More from Modular Advantage
Samantha Taylor: Leading the (Modular) Design of Tomorrow
“With modern technology and the way we’ve all embraced things like BIM, file sharing, and video conferencing since COVID, it’s easy to collaborate with companies in Austria, or Singapore, or anywhere else in the world.”
Greg DeLeon: Military Engineering to Modular Design
Greg DeLeon, a structural engineer at ISE Structural Engineers in Temecula, California, can tell you not only how large a beam needs to be to support a house, but also how much explosives you’ll need to take it down, thanks to his unique combination of professional and military experience.
To Remake North Minneapolis, Devean George Swaps Basketball for Buildings
He’s lived in Los Angeles, Dallas, and San Francisco (to name a few). He’s delivered championships with the Los Angeles Lakers and made career-defining moves with the Dallas Mavericks and the Golden State Warriors. No matter the wins, the championships, or even the seemingly impossible 3-pointers, Devean George has always returned to where it all started for him: Minneapolis.
Chelsi Tryon: Making the World a Better Place
For Chelsi Tryon, Director of Environmental, Social, and Governance (ESG) for WillScot Mobile Mini, nothing is more enjoyable than increasing the
company’s sustainability efforts while simultaneously doing her bit to save the environment.
Joshua Hart: Pushing Boundaries
Joshua Hart, P.E., vice president at Modular
Solutions, can sum up his job responsibilities in one sentence: “I do whatever needs to be done.” Hart thrives on the variety and the opportunity to be involved in every aspect of the company. And it shows! You might say Hart has come full circle.
Jamie Metzger: From Construction to Apparel and Back Again
Growing up in a blue-collar city like Edmonton, Alberta, Canada, it’s no surprise that Jamie Metzger spent some time working labor jobs on construction sites. It’s one of the most common summer jobs in the city. But that’s probably the last predictable thing about this particular story.
Victor Masso: Expanding Modular in Puerto Rico
Victor Masso joined 2 Go Storage, a company started by his grandfather and father, in 2018 to develop a modular building division in the wake of the devastation caused by Hurricane Maria in 2017. Prior to joining the company, he had worked in the industry for about four years focusing on pharmaceutical, commercial, and government projects.
Eliyah Ryals: Finding the Perfect Fit
It’s not common for people to find their perfect career fit straight out of college. It’s even less common to find it in the town you grew up in. But that’s exactly what happened when Eliyah Ryals was told about vacancies at Panel Built and made the decision to apply.
Through It All, It’s Still About the Workers
By February 2024, the number of available, unfilled construction job openings had reached an all-time high. At some point, interest rates will fall, creating another surge in demand for such workers. In short, solving the nation’s skilled worker shortage issue has never been more important.
Navigating Insurance Challenges in the Modular Construction Industry
Utilizing practical written minimum insurance and indemnity requirements, along with monitoring certificates of insurance by someone who has COI training will not yield a perfect risk transfer strategy, but the exposure will be managed much better than it likely is currently.