Ingenious System Assembles Buildings with Concrete Superstructure in Weeks
New technology being implemented by Andrew Neill Construction (ANC), a construction company in Canada, allows multi-story housing developments to be completed in weeks instead of months. Imagine housing developments being completed with only two weeks of on-site construction. With ANC’s Void Form System, it’s possible.
The ingenious system uses stackable modules to provide the forms for the concrete superstructure. The concrete is poured into the voids between the modules, and another layer of modules can be immediately stacked on top, without waiting for the concrete to cure.
The fully finished modules are built off-site while the overall project is being reviewed and approved for permits. In Canada, modular units of this type do not fall under standard building codes. Therefore, they can be constructed while the plans for the building are being reviewed.
Once permits are issued, the modular units are ready to be shipped and stacked. Here’s where the magic happens: After the units have been stacked, concrete is poured into the voids, creating a strong structural frame for the building. Additional module layers can be stacked on top of existing units before the concrete cures because of the structural steel elements in each unit.
This patent-pending system provides an opportunity for quick construction of concrete formed midrises and highrises. Andrew Neill, the President and CEO of ANC, thinks the design could be useful for hurricane ravaged areas, earthquake-prone regions, as well as areas rocked by war, such as the Ukraine.
Neill developed the idea for the system when another contractor approached him about finding a better way to construct hospital rooms using modular construction. The contractor was looking to find cost savings through speed, quality, and efficiency. He thought modular construction was the answer, but the project called for a concrete superstructure. The contractor’s idea was to form and pour the structure, then slide the finished modules in from the side. Neill thought that wouldn’t be cost effective.
Neill’s next idea was to set the units first, then pour the concrete. After many sleepless nights and meetings with structural engineers, he developed a system that could work. The process has taken about a year to develop.
How It Works
The modules are completely finished and assembled off-site. They come complete with insulation, electrical, plumbing, HVAC, drywall, millwork, flooring, lighting, and plumbing fixtures. The steel frame that surrounds each module is engineered to act as a structure of its own, as well as act as a concrete form that will provide additional structural strength once concrete is poured into it.
The modules stack on top of each other without any additional shoring or support and are bolted together. The structural steel frames are clad with corrugated steel and are ready to receive concrete in the vertical wall section, and also on top of the modules horizontally.
The next level of modules can be added almost immediately after the concrete is poured; no curing is required. When reinforcing steel bars are added and the concrete has cured, the weight of the building transfers to the concrete, changing the fire and structural ratings. This allows the system to be used for highrise applications, even in areas with strict structural codes, like California and Miami.
There are no special concrete mixes required and the concrete is pumped to each module using tower cranes and concrete pumps.
The system allows projects to meet the requirements for a concrete superstructure without having to use conventional forming methods, saving 98% of the costs related to forming, pouring, and stripping concrete.
The system’s only drawback may be that there’s more steel than necessary. But Neill says the time and cost savings far outweigh the cost of the redundant steel.
The Future
Andrew Neill started ANC in 2017 in Brantford, Ontario, near Toronto. He has 18 years of experience as a residential carpenter and superintendent on projects in Canada and the Caribbean.
The timing couldn’t have been better, as the Canadian federal government started a funding program for affordable housing called the Rapid Housing Initiative (RHI). ANC was granted several contracts for affordable housing projects for municipalities and indigenous communities in the area.
Although no projects have yet been completed using the system, Neill hopes to change that soon. The flexibility of the system allows it to be tailored to almost any project.
There’s seemingly no limit to how high the modules can be stacked. “All the fire rating and structural capacity is being placed on the concrete structure after it has cured, making the modules only a cosmetic fit-out at the end. They are used temporarily to eliminate the need for most of the concrete forming, and also eliminate the need for a conventional structural ‘core.’ You could, in theory, pour the walls and slabs, and stack fully finished modules concurrently, literally without stopping, until you reach the top, which could be over 100 stories.”
Neill sees this product best being used for midrise and high-rise buildings in coastal areas and those prone to earthquakes or other natural disasters. It would provide a way for a quick response to rebuild in an area after a disaster. He looks to get the product approved in the US soon, as well as expand its use to hospitals and healthcare buildings.
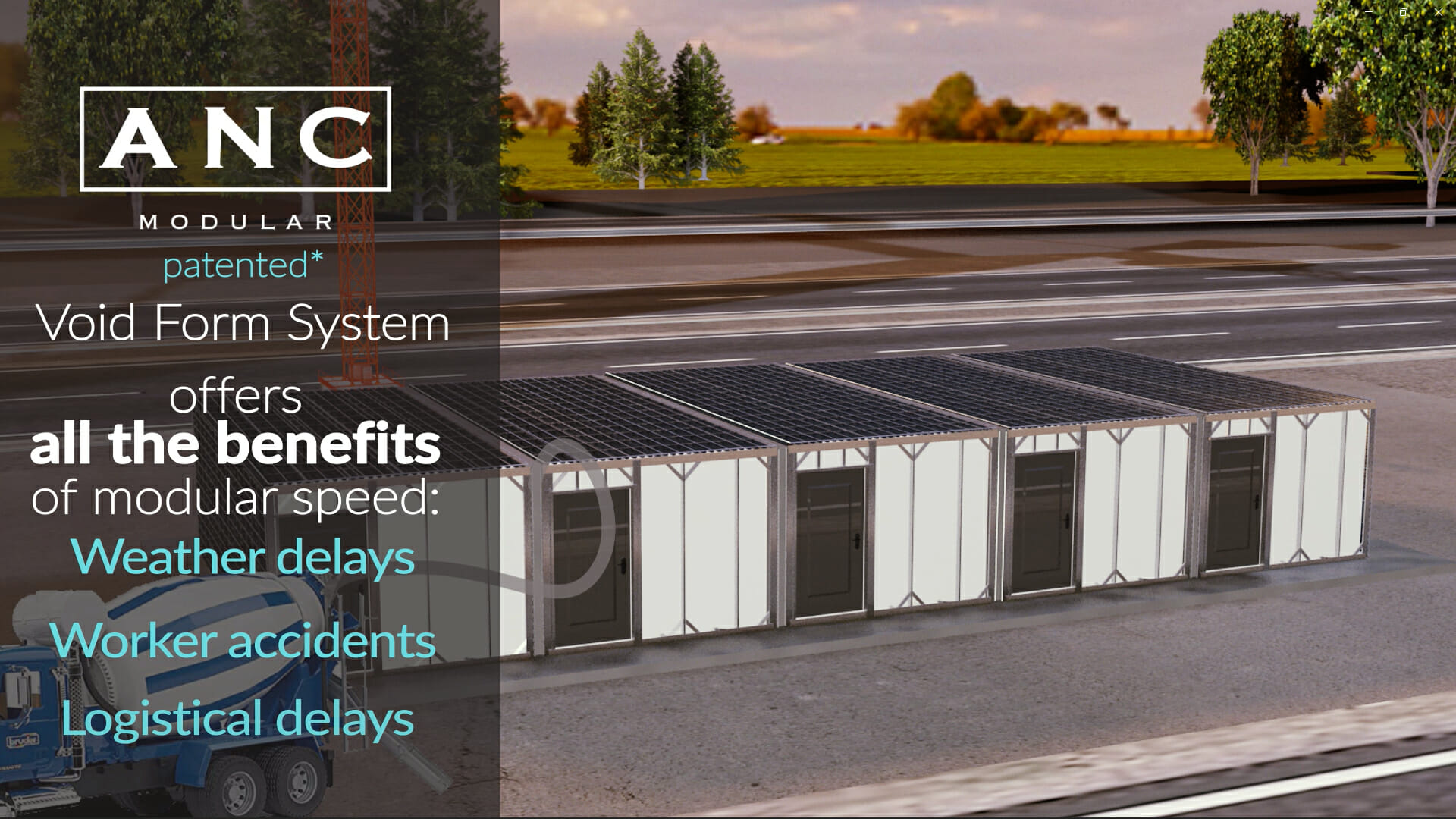
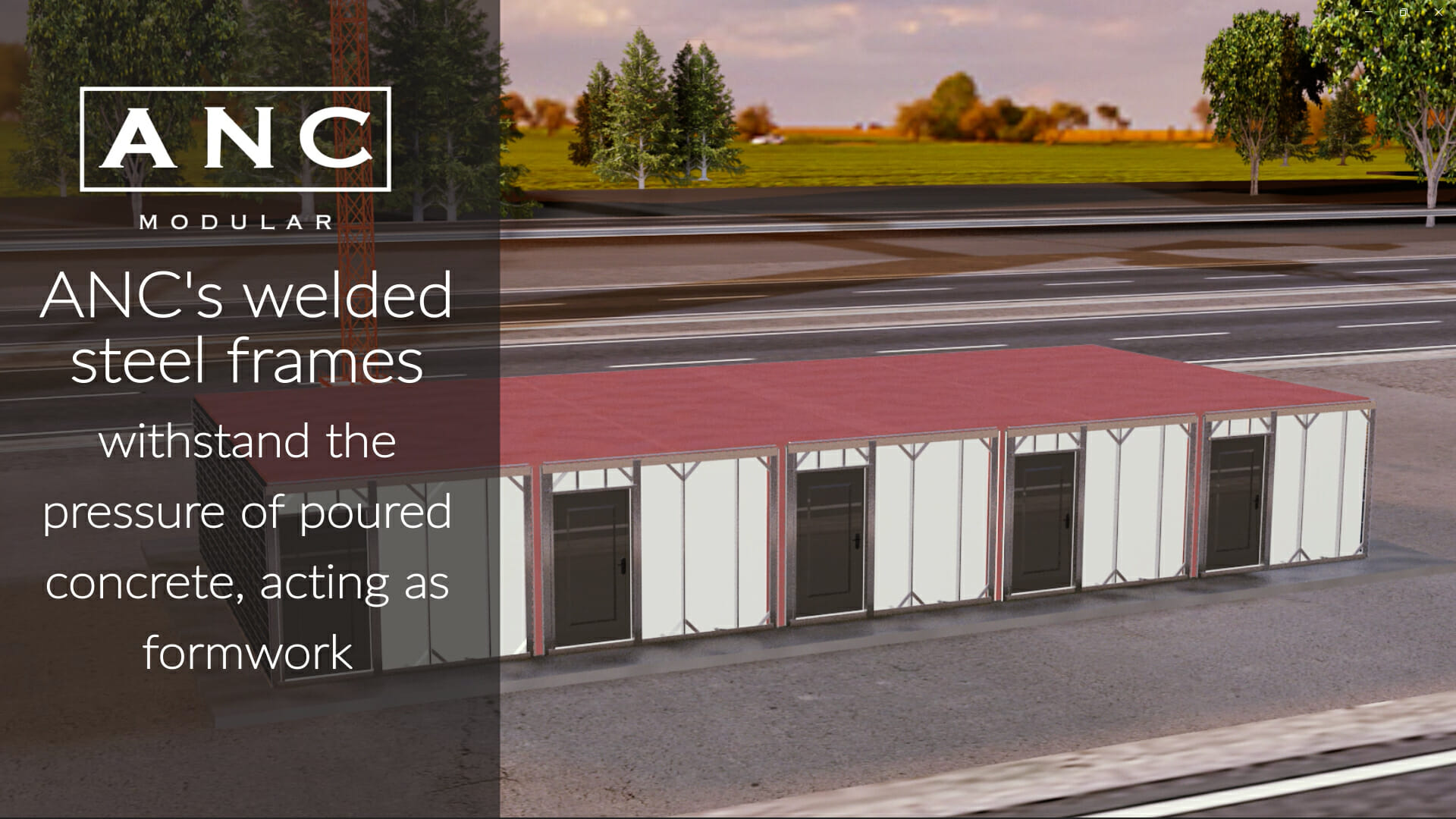
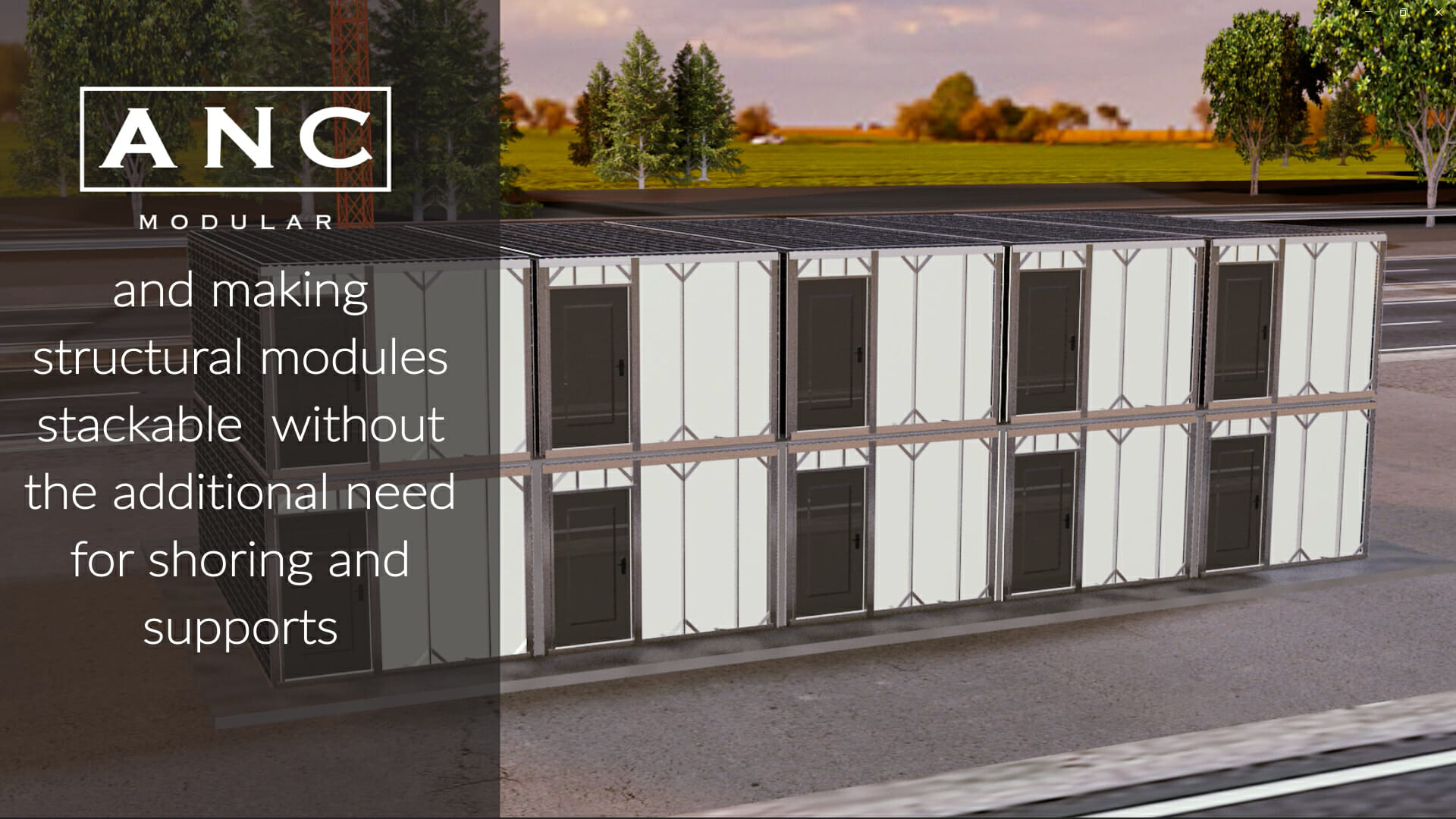
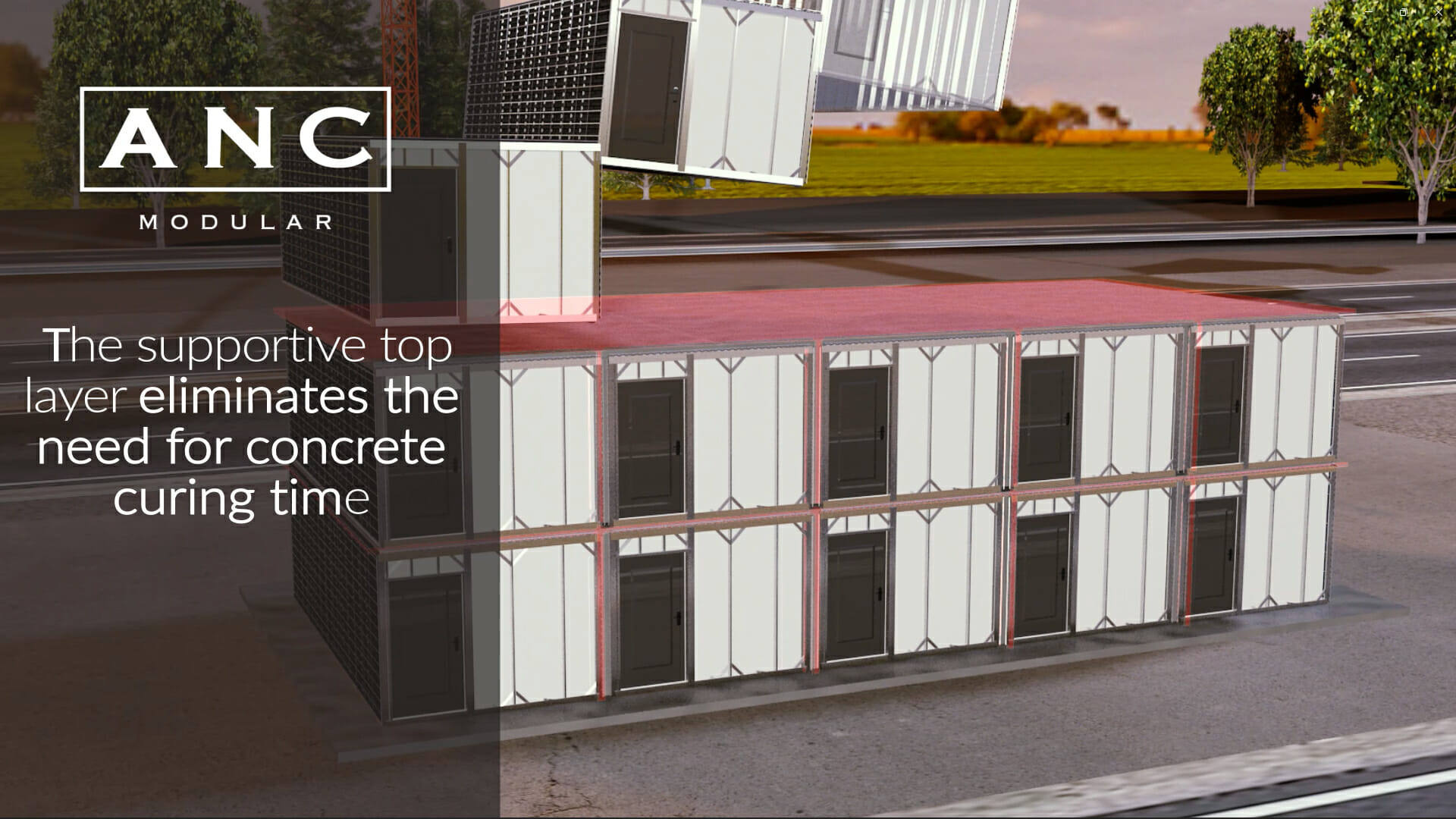
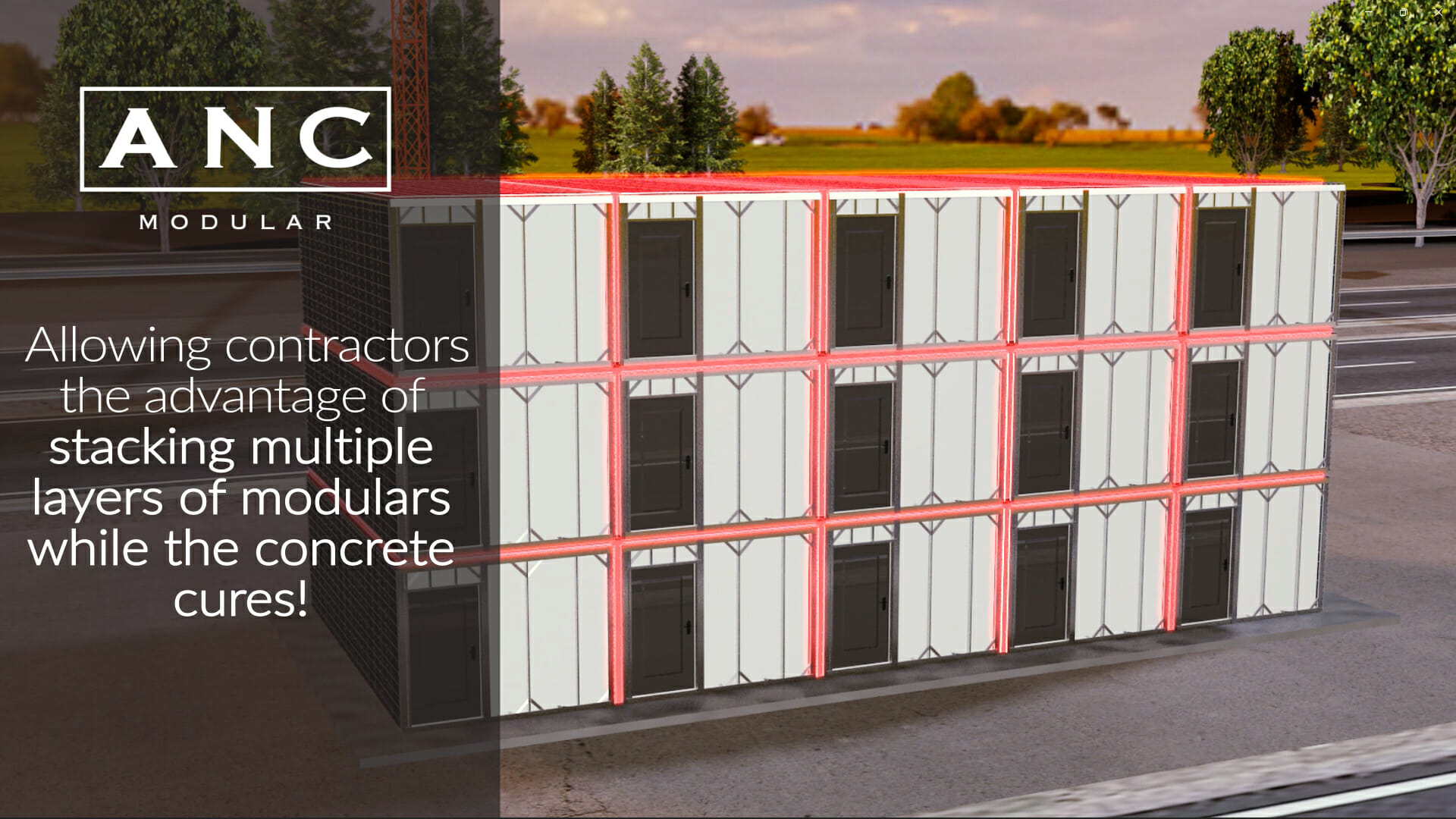
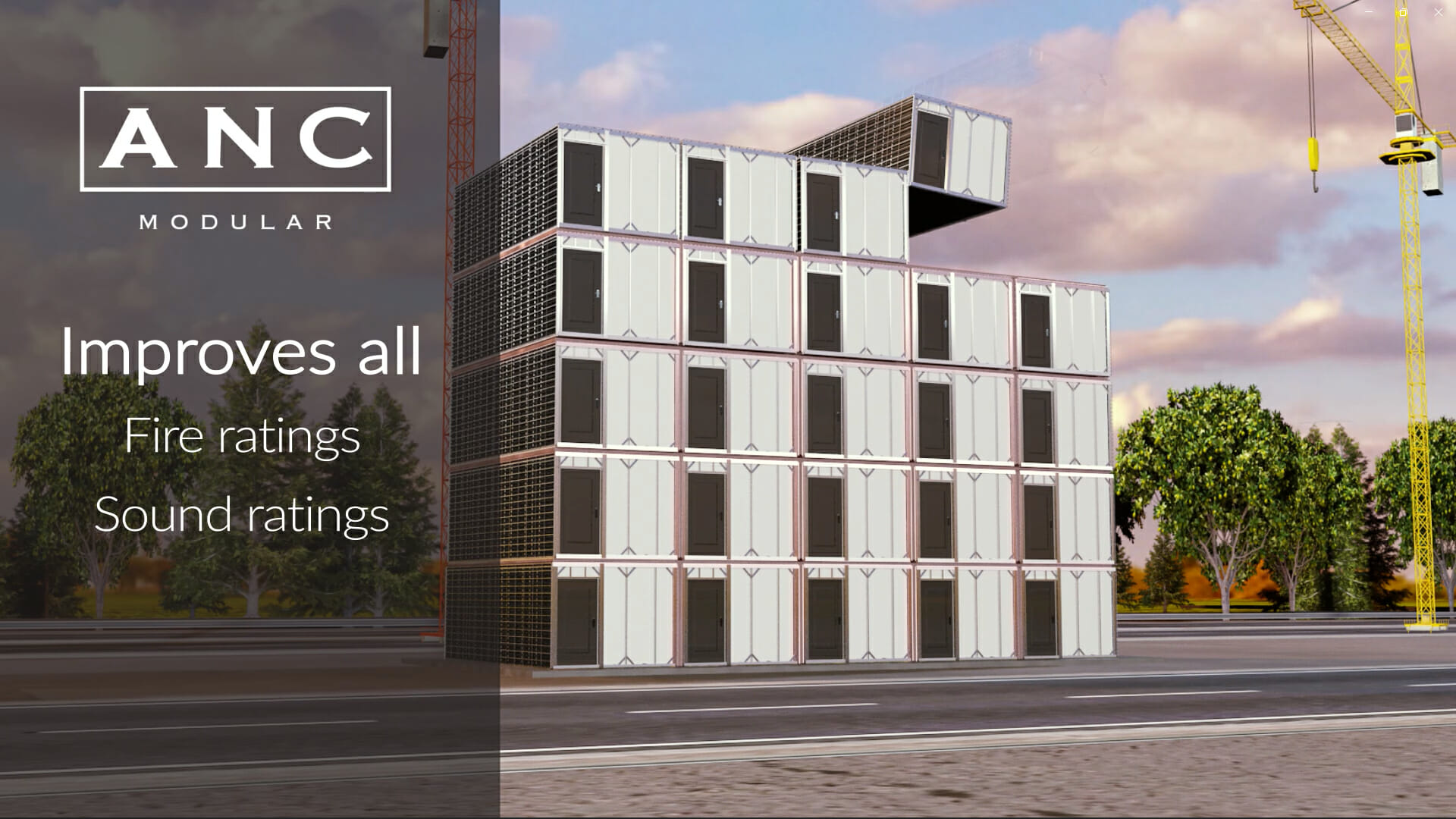
About the Author: Dawn Killough is a freelance construction writer with over 25 years of experience working with construction companies, subcontractors and general contractors. Her published work can be found at dkilloughwriter.com.
More from Modular Advantage
Behind the Design of Bethany Senior Terraces, NYC’s First Modular Passive House Senior Housing Project
As more developers seek to meet new regulations for energy efficiency, the team at Murray Engineering has set a new record. With the Bethany Senior Terraces project, Murray Engineering has helped to develop NYC’s first modular structure that fully encompasses passive house principles — introducing a new era of energy efficiency in the energy-conscious city that never sleeps.
How LAMOD is Using Modular to Address Inefficiency, Sustainability, and the Future of Construction
As developers, designers, and contractors seek to understand the evolving needs of the modular industry, no one is as well-versed in the benefits of going modular as Mārcis Kreičmanis. As the co-founder and CBDO of LAMOD in Riga, Latvia, Mārcis has made it his ultimate goal to address the inefficiencies of traditional construction.
From Furniture Builder to ‘Activist Architect’: Stuart Emmons’ Unique Journey
Stuart Emmons was fascinated by buildings at a young age. He remembers building sand cities with his brother during trips to the Jersey shore. His father gave him his first drawing table at the age of ten. Today, he is an experienced architect who received his FAIA in June 2025. The road he took is unique, to say the least.
Forge Craft Architecture + Design: Codes, Contracts, and Intellectual Property
Founding Principal and Director of Modular Practice for Forge Craft Architecture + Design, Rommel Sulit, discusses the implications of codes, contracts, and intellectual property on
modular construction.
Eisa Lee, the “Bilingual” Architect
Now as the founder of XL
Architecture and Modular Design in Ontario, Canada, she applies not just her education as a traditional architect but an entire holistic view on modular design. It’s this expansive view that guides her work on being a true partner that bridges the gap between architects and modular factories as they collaborate on the design process.
Tamarack Grove Engineering: Designing for the Modular Sector
The role of a structural engineer is crucial to the success of a modular project, from initial analysis to construction administration. Tamarack Grove offers structural engineering services — project analysis, plan creation, design creation, and construction administration — for commercial, manufacturing, facilities, public services, and modular. Modular is only one market sector the company serves but it is an increasingly popular one.
Engineer Masters the Art of Listening to His Customers
Since founding Modular Structural Consultants, LLC. in 2014, Yurianto has established a steady following of modular and container-based construction clients, primarily manufacturers. His services often include providing engineering calculations, reviewing drawings, and engineering certification
Inside College Road: Engineering the Modules of One of the World’s Tallest Modular Buildings
College Road is a groundbreaking modular residential development in East Croydon, South London by offsite developer and contractor, Tide, its modular company Vision Volumetric (VV), and engineered by MJH Structural Engineers.
Design for Flow: The Overlooked Power of DfMA in Modular Construction
Unlocking higher throughput, lower costs, and fewer redesigns by aligning Lean production flow with design for manufacturing and assembly.
Choosing the Right Ramp
Modular construction offers a compelling alternative to traditional methods for designing and building ADA and IBC-compliant entrances. By addressing the challenges of traditional construction, such as time-consuming processes, unavailable specialized labor, and variable field conditions, modular solutions provide a more efficient, cost-effective, and reliable approach.