Did the Pandemic Bolster Modular Construction's Long-Term Outlook?
A new report from Anirban Basu, chairman & CEO of Sage Policy Group and Chief Economist of the Modular Building Institute
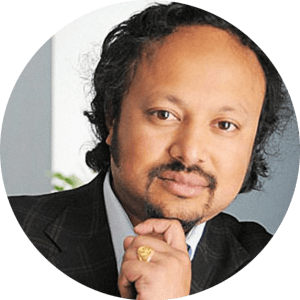
Anirban Basu is chairman & CEO of Sage Policy Group and Chief Economist of the Modular Building Institute
The Answer Appears to be “Yes, it did”
The pandemic of 2020 and beyond not only ended the lengthiest economic expansion in American history, it has also fundamentally altered behavior. In some instances, this has compromised the long-term outlook for certain key construction segments, including the office market (remote work), hotels (remote meetings), and shopping centers (remote shopping). But in many other instances, has rendered modular construction even more competitive, thereby improving its long-term outlook in terms of construction market share and overall activity.
Workforce Considerations
The natural place to begin such a discussion is with the construction workforce. To state the situation as succinctly as possible, it’s too small and under-trained. In this regard, the pandemic didn’t help. It caused many Baby Boomers to retire earlier than anticipated, in part to avoid Covid infection during the pre-vaccination period. But the pandemic also helped launch a surge in asset prices, whether in the form of rising home values or bloated stock portfolios. Many Boomers determined that they had become wealthy enough to retire, and so they did.
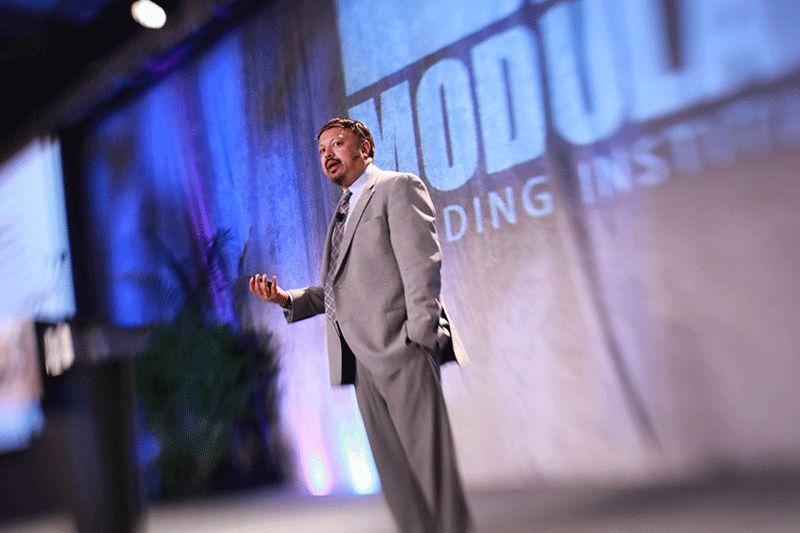
Anirban Basu speaks at the 2022 World of Modular conference and tradeshow.
The problem is that many of North America’s most talented construction workers are Baby Boomers, people who nurtured their skills as craftspeople for decades. Their departure from the workforce has not been neatly offset by the entry of younger skilled workers, helping to produce skills and worker shortages in the process. Much of the construction industry has responded by ramping up hiring of unskilled laborers, with the hope that they could help get products across the proverbial finish line and eventually be trained to become more productive.
There’s more. Construction has traditionally depended heavily upon the efforts and talents of immigrants. Recent presidents have tended not to favor stepped up legal immigration. Partially as a consequence, the size of the working age immigrant population is much smaller than it would have been had pre-2017 trends remained in place.
Worker preferences have also shifted during the pandemic, with more seeking to work remotely and/or enjoy greater flexibility. Such preferences do not suit construction well, given that virtually all construction work must be performed at a jobsite and that a significant volume of construction services is delivered by teams. Construction, therefore, cannot offer the types of flexibility that might be available to white collar workers or to those in the gig economy who do things like drive for Lyft or Uber.
Even in the context of Baby Boomer engagement, during their prime working years, construction productivity lagged. According to data compiled by the Bureau of Labor Statistics and analyzed by Steven G. Allen in 1985, “productivity in the construction industry reached a peak in 1968 and, except for a brief and small upturn between 1974 and 1976, has been falling ever since.”
Recent data indicate much the same thing. Data show that between 2007 and 2020, overall construction productivity was flat, though as pointed out by three economists at the Bureau of Labor Statistics, productivity has actually been rising in especially capital-intensive segments like industrial construction and high, street and bridge construction.
Nonetheless, given the industry’s propensity to deliver projects beyond budget and deadline, greater productivity would be most welcome, especially as America seeks to dramatically improve its roads, bridges, airports, seaports, electrical grids, and water systems. That craving for better outcomes favors modular construction. A 2019 McKinsey report regarding modular construction stated that the productivity boost of the off-site production sometimes shortens timelines by 20 to 50 percent.
Modular construction is also far more likely to meet the tastes and preferences of younger workers. By operating in controlled settings, modular construction employers are able to keep employees more comfortable, remove variables such as wind and rain, and perhaps even offer more flexible working arrangements since workers are more likely to be interchangeable to the extent that they engage in repetitive tasks uncompromised by the vagaries of the outside world.
Environmental Concerns
There is also a growing demand for rapid improvements in environmental outcomes, something reinforced by the pandemic and a desire for more climate and biological stability. The construction industry is rarely considered especially friendly to the environment. A study from the Global Alliance for Building and Construction states that the global construction industry is “responsible for almost 40 percent of energy- and process-related emissions”. Other reports estimate that the amount of waste generated by construction totals around 56 million tons of debris.
Modular construction mitigates these environmental impairments in multiple ways. First, by operating in controlled, indoor settings, modular construction can contain the release of chemicals, dust, and other byproducts. Air filters can add to environmental protections. Byproducts are more easily captured and recycled. Moreover, many of today’s modular structures come with integrated solar panels, favor dimmable LED lighting, sensors that detect when people are present, and triple-paned windows. Fiction Factory, a construction studio based in Amsterdam, produces the Wikkelhouse, a completely modular home that is fully biodegradable. Nonetheless, they are built to last for decades.
Autovol, a modular construction company based in Idaho, is increasingly taking advantage of robotics, another technical feature likely to be easier to introduce in modular settings. In a Construction Dive piece, CEO Rick Murdock indicates that a bit less than a third of its production process is conducted robotically and that he expects that number to rise to 45 percent in the future. The company is also employing women at a significantly higher rate than non-modular construction segments. Whereas women comprise approximately 5 percent of total construction workers, they hold nearly one in three jobs at Autovol.
Looking Ahead
With interest rates rising and risk of recession elevated, the near-term could prove challenging for many modular and non-modular construction firms alike. But societal shifts wrought by the pandemic have rendered modular construction’s narrative all the more compelling, which should set the stage for larger market share gains going forward.
More from Modular Advantage
Samantha Taylor: Leading the (Modular) Design of Tomorrow
“With modern technology and the way we’ve all embraced things like BIM, file sharing, and video conferencing since COVID, it’s easy to collaborate with companies in Austria, or Singapore, or anywhere else in the world.”
Greg DeLeon: Military Engineering to Modular Design
Greg DeLeon, a structural engineer at ISE Structural Engineers in Temecula, California, can tell you not only how large a beam needs to be to support a house, but also how much explosives you’ll need to take it down, thanks to his unique combination of professional and military experience.
To Remake North Minneapolis, Devean George Swaps Basketball for Buildings
He’s lived in Los Angeles, Dallas, and San Francisco (to name a few). He’s delivered championships with the Los Angeles Lakers and made career-defining moves with the Dallas Mavericks and the Golden State Warriors. No matter the wins, the championships, or even the seemingly impossible 3-pointers, Devean George has always returned to where it all started for him: Minneapolis.
Chelsi Tryon: Making the World a Better Place
For Chelsi Tryon, Director of Environmental, Social, and Governance (ESG) for WillScot Mobile Mini, nothing is more enjoyable than increasing the
company’s sustainability efforts while simultaneously doing her bit to save the environment.
Joshua Hart: Pushing Boundaries
Joshua Hart, P.E., vice president at Modular
Solutions, can sum up his job responsibilities in one sentence: “I do whatever needs to be done.” Hart thrives on the variety and the opportunity to be involved in every aspect of the company. And it shows! You might say Hart has come full circle.
Jamie Metzger: From Construction to Apparel and Back Again
Growing up in a blue-collar city like Edmonton, Alberta, Canada, it’s no surprise that Jamie Metzger spent some time working labor jobs on construction sites. It’s one of the most common summer jobs in the city. But that’s probably the last predictable thing about this particular story.
Victor Masso: Expanding Modular in Puerto Rico
Victor Masso joined 2 Go Storage, a company started by his grandfather and father, in 2018 to develop a modular building division in the wake of the devastation caused by Hurricane Maria in 2017. Prior to joining the company, he had worked in the industry for about four years focusing on pharmaceutical, commercial, and government projects.
Eliyah Ryals: Finding the Perfect Fit
It’s not common for people to find their perfect career fit straight out of college. It’s even less common to find it in the town you grew up in. But that’s exactly what happened when Eliyah Ryals was told about vacancies at Panel Built and made the decision to apply.
Through It All, It’s Still About the Workers
By February 2024, the number of available, unfilled construction job openings had reached an all-time high. At some point, interest rates will fall, creating another surge in demand for such workers. In short, solving the nation’s skilled worker shortage issue has never been more important.
Navigating Insurance Challenges in the Modular Construction Industry
Utilizing practical written minimum insurance and indemnity requirements, along with monitoring certificates of insurance by someone who has COI training will not yield a perfect risk transfer strategy, but the exposure will be managed much better than it likely is currently.