Stacking Up: How Vision Modular is Helping Take Modular Construction to New Heights
An interview with Vision Modular System’s John Fleming
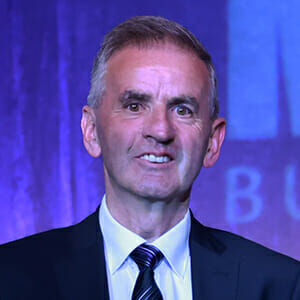
John Fleming is the president and inventor of Tide Construction and Vision Modular Systems
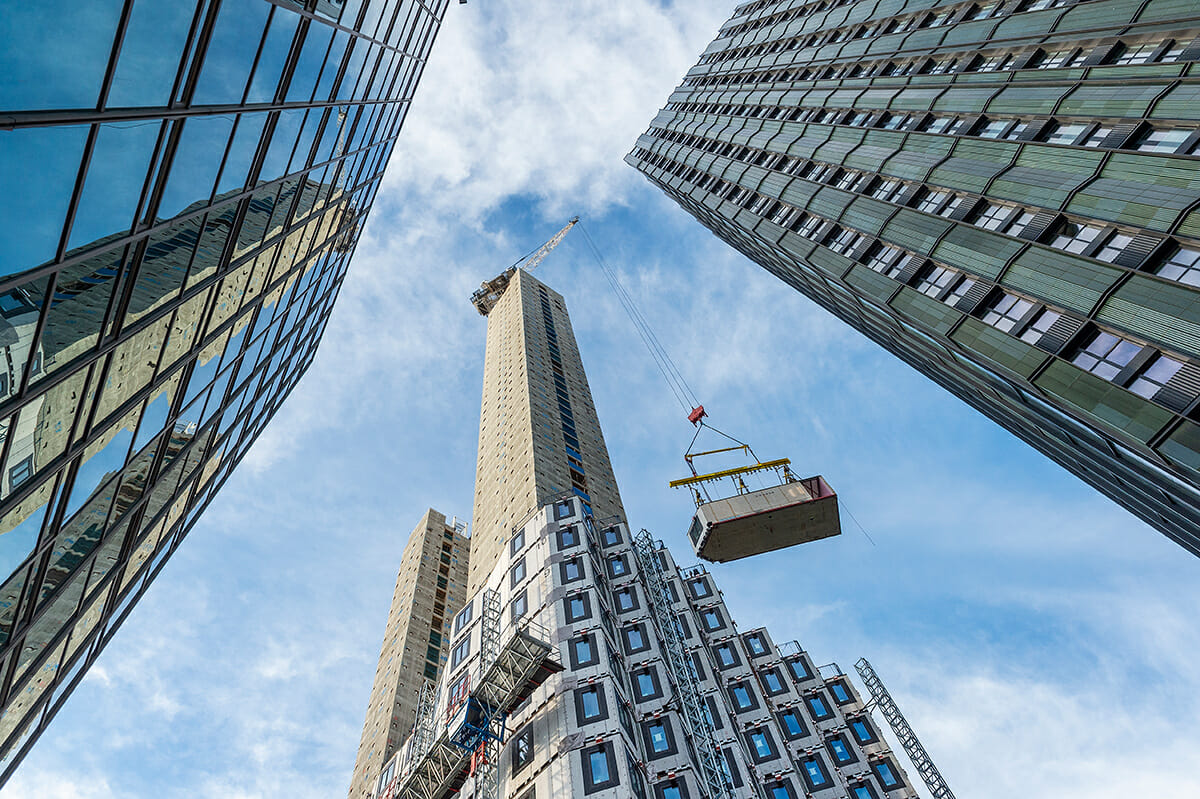
The installation of modules from Vision Modular Systems around the concrete cores of its College Road project in London.
As the manufacturer of some of the United Kingdom’s—and indeed the world’s—tallest modular buildings, Vision Modular has learned a thing or two about building upwards. Launched little over a decade ago as the modular building division of developer/contractor Tide Construction, Vision has steadily moved from one celebrated project to another. It’s 101 George Street and College Road projects are currently among of the tallest modular buildings in the world, and it just announced plans for a 48-story student housing building in the Canary Wharf district of London.
Curious about their success and aspirations, I corresponded with John Fleming, Vision Modular’s and Tide Construction’s president and inventor. My questions and his replies are summarized below.
John McMullen: Tell me about Vision Modular. When was it started and what was its goal in the beginning? What is its goal now?
John Fleming: Vision Modular was established over a decade ago to tackle three of the main challenges the construction industry was facing and continues to face - the housing crisis, the climate crisis and skill shortages. We use traditional construction materials, but with all the benefits of a modular, factory-built format.
The advantages of using volumetric modular construction technology include quality – all our modules are constructed off-site in a quality-controlled factory environment - together with sustainability, safety, scalability and minimal disruption to the communities we build in. A key goal for us is to continue to pave the way for more industry and government leaders to support the use of modular construction.
JM: How have your manufacturing capabilities evolved since you started?
JF: There is a continuing investment program in our technologies, ongoing rigorous research and development, and testing regimes. When the business started, we were building low-rise projects. We’re now delivering schemes of 50 stories, clearly demonstrating the evolution and advancement of the system. We’re designing and delivering flexible schemes that reflect the demands of our clients across a range of asset classes.
JM: How have your manufacturing capabilities evolved since you started?
JF: There is a continuing investment program in our technologies, ongoing rigorous research and development, and testing regimes. When the business started, we were building low-rise projects. We’re now delivering schemes of 50 stories, clearly demonstrating the evolution and advancement of the system. We’re designing and delivering flexible schemes that reflect the demands of our clients across a range of asset classes.
JM: Tell me about how your factory is laid out. How has it changed since you started and why have you made the changes that you’ve made?
JF: Our manufacturing facilities are bespoke to Vision Modular and are purpose-built factories with automated production lines developed for the construction industry. The process can be likened to the modern-day car manufacturer. Modules, each taking around 10 days to complete, are transferred around the manufacturing line and fitted out by skilled labor, rather than the labor going to the modules. It’s hugely efficient and again, the emphasis is on achieving the highest quality and safety possible.
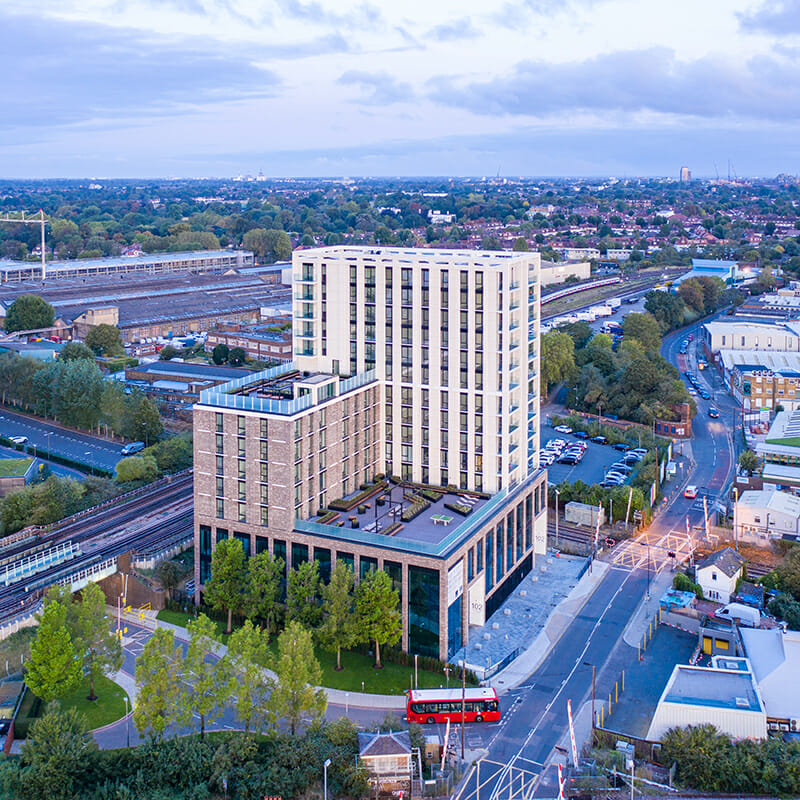
Bollo Lane, Chiswick by Tide Construction and Vision Modular Systems
JM: Is there a difference between manufacturing for 40-storey buildings and manufacturing for much shorter buildings? If so, what are they?
JF: Each project we deliver is highly unique. However, Modules are manufactured and fitted out the same way, whether they are going to be on the first floor of a building or the 50th floor. The design and manufacturing processes however are effectively the same. Naturally, the module installation for a low-rise and high-rise building differs. However, the same rigorous quality and safety controls are applied to every module regardless of its location within our buildings.
JM: Your partnership with MJH Structural Engineers has been going strong for several years now. What do you think is the secret behind your string of successful projects?
JF: We operate on a vertically integrated procurement model with our company Tide Construction being the main developer and contractor, and Vision Modular being the offsite manufacturer. This integration gives us full autonomy over each moving part of a development. In addition to our strategic business model, we also work with some of the industry’s leading consultants, and partnerships, such as the one we have with MJH Structural Engineers, and these teams have been a crucial part of our success.
JM: Tell me about the plans (as best you can) for the just-approved 48-storey student housing building at 30 Marsh Wall. What was that development process like and what details can you share about the modules you’ll be building?
JF: Located in London’s central business district, Canary Wharf, Marsh Wall will sit among many of the city’s iconic, high-rise buildings. Award-winning practice EPR Architects have designed the building and along with 1,068 student beds’ accommodation, the scheme will provide amenity space and a generously sized roof garden. A light bronze aluminum vertical band on the principal façade highlights the main entrance before extending up the entire 48 stories, while secondary horizontal articulations varying in depth provide solar shading on each level. This scheme demonstrates the flexibility in design that the Vision Modular System makes possible.
An innovatively designed, recreational space will enhance the surrounding public space.
This modular approach on Marsh Wall will cut construction time by up to 50% and result in a more dependable construction program, with efficient construction logistics minimizing disruption in the local area.
Having just received planning, we are due to start onsite imminently.
JM: Are there any specific design elements for this building that make its modules different than the others you’ve built? For example, are there any net-zero elements or structural complexities that have to be accounted for?
JF: As mentioned above, all buildings are designed individually and take into consideration elements such as the local architecture and site constraints. Marsh Wall follows the principles of previous schemes we’ve delivered in terms of carbon emissions. Research by academics from the University of Cambridge and Edinburgh Napier University found that construction using volumetric modular systems produced significantly less CO2 emissions compared to traditional methods. In Marsh Wall’s case, using off-site construction could reduce construction waste by up to 80%, according to the local authority, with 97% of the waste being recycled. Furthermore, our schemes result in lower operating costs.
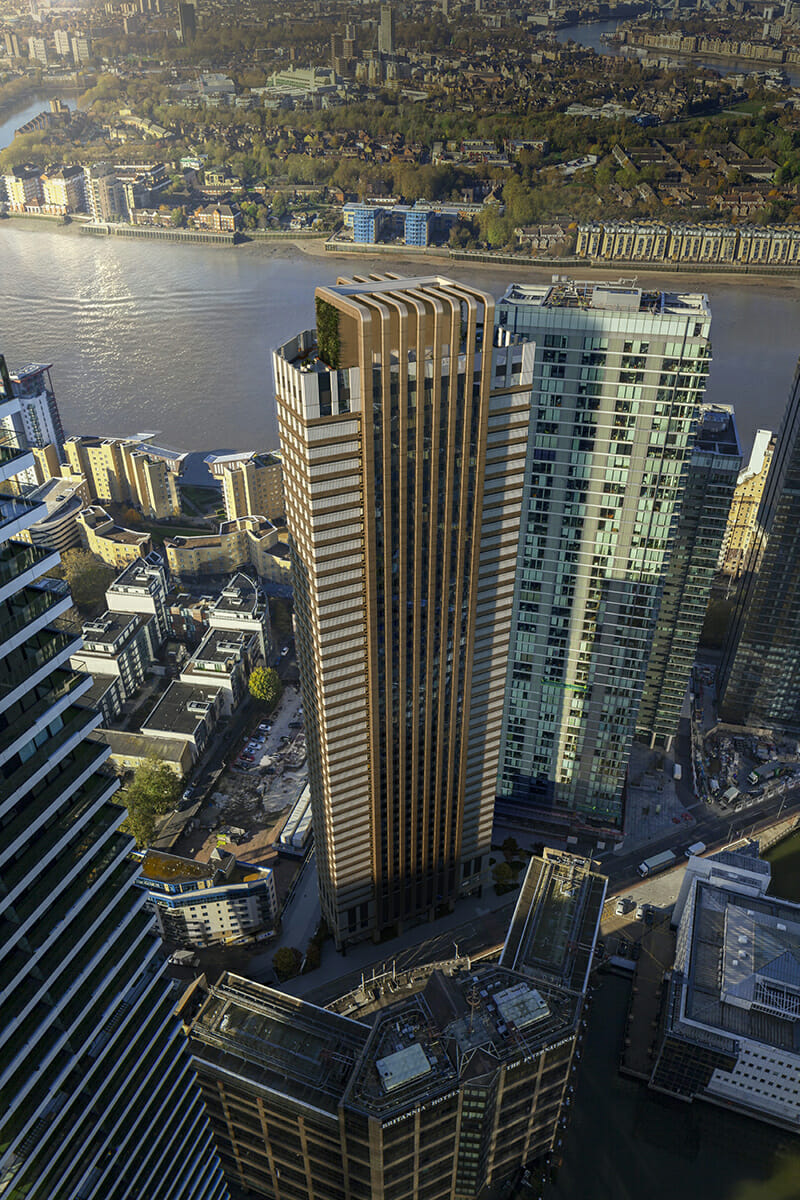
A rendering of Marsh Wall, Canary Wharf by Tide Construction and Vision Modular Systems
JM: What’s the projected timeline for this project?
JF: We are about to start construction onsite with the building due to be completed for the commencement of the 2025 academic year. This is a significant program savings particularly given the scheme’s scale, intricacies, and the site’s complex nature. It illustrates the speed at which our modular system can deliver such projects. The Tide and Vision modular framework offers significant program savings and certainty due to its ability to manage certain external risks.
JM: Tell me about the logistics for this project (and similar projects). How much advance work needs to be done to coordinate the storage and transportation of all the modules you’ll be building?
JF: As a high-level overview, the first process is to divide the building floor plate into appropriate module sizes suitable for transport – we call this modularization. We then identify an appropriate offloading point and carry out a detailed route analysis from our manufacturing facility to the site to identify any logistical restrictions. As with all our schemes, we will implement a highly effective logistics scheduling program to ensure modules are delivered when needed and craned into position. The process is mapped out meticulously in collaboration with the relevant local transport authorities, and progress is continually monitored to ensure we are on target to deliver on time.
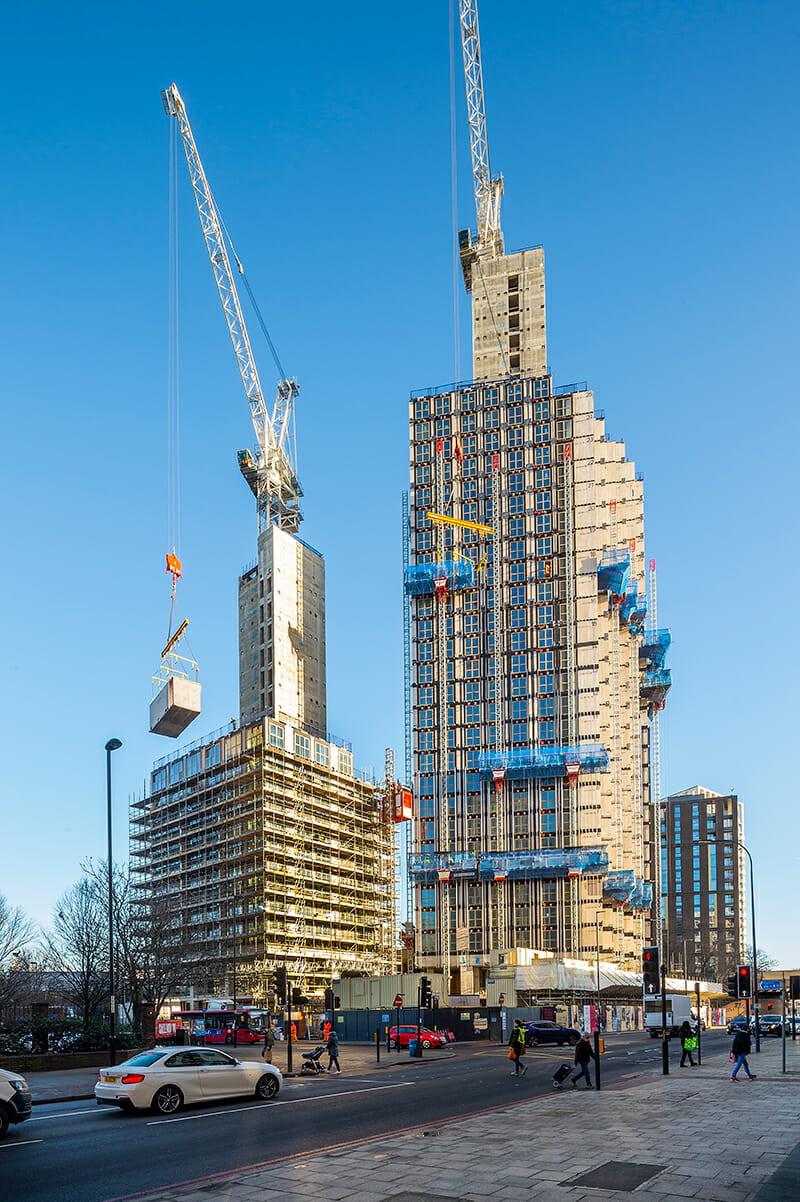
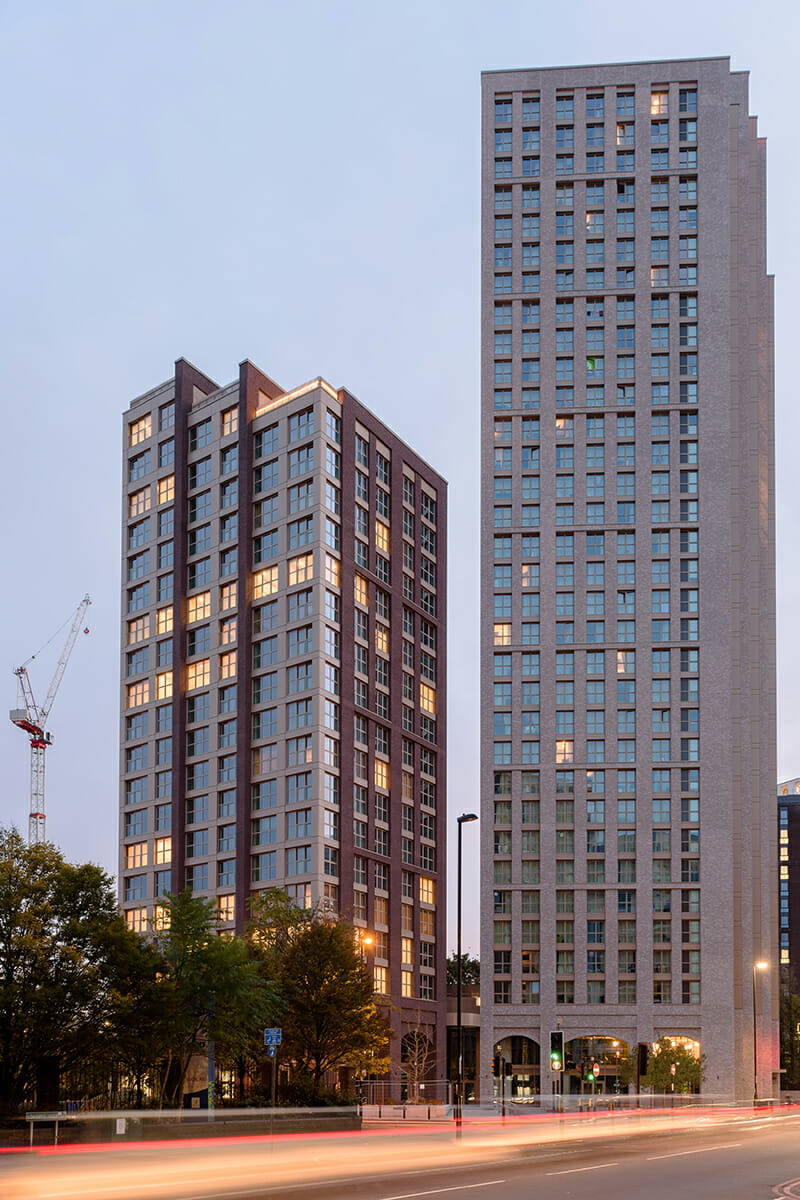
VMS' Lewisham Exchange project in London, under construction (left) and completed (right)
JM: Are you in charge of craning and setting the modules as well, or just building them? What can you tell me about craning modules for very tall structures? Are there procedures or processes that aren’t used with smaller modular buildings? If so, what are they?
JF: Vision Modular executes the safe arrival, lifting, and installation of all our modules. In conjunction with the logistics strategy, this is known as the cranage strategy, each requiring the same detailed consideration. Factors that need to be considered include the size and weight of the modules, the location of the loading bay and the footprint of the building. The crane location will then be determined by a variety of factors and engineered to suit. The process is similar regardless of the height of the building, and the same stringent quality controls and strategy apply. For taller buildings, an additional tower crane mast restraint may be required.
JM: In taller buildings, generally speaking, are the modules nearer to the foundation built differently than the modules nearer to the top? If so, how?
JF: Our modular buildings also use traditional construction methods for the substructure. Larger, robust columns are used on the lower floors of our taller buildings to support the substantial vertical loads for these higher rise buildings.
JM: What’s the most challenging part of the fabricating very tall modular buildings?
JF: We look at this another way. We believe the modular system removes many challenges modern developers face. The manufacturing and fit out process takes place on a factory floor which is a safe, clean and temperature-controlled environment. We’re removing those high-risk activities for the onsite workforce, for example, we can install module windows for the 40th story within the safety of the factory.
JM: What’s next for Vision Modular? What other projects do you have in the pipeline?
JF: We currently have 3,000 homes under construction in the UK with a further significant pipeline, and there is strong interest in our technologies from other jurisdictions. We believe we can continue with our track record of delivering homes and play a significant part in revolutionizing how modular projects are delivered.
We are demonstrating the potential of volumetric modular construction to become a mainstream method for delivery in the construction industry, while ensuring architectural design intent and aesthetics remain at the heart of each project.
Years of significant growth, in terms of our pipeline and financial strength, is demonstrated through our long-standing partnerships with some of the world’s biggest institutional purchasers and has established modular as a mainstream method of delivery.
JM: Thank you, John!
About the Author: John McMullen is the marketing director for Modular Building Institute
More from Modular Advantage
Behind the Design of Bethany Senior Terraces, NYC’s First Modular Passive House Senior Housing Project
As more developers seek to meet new regulations for energy efficiency, the team at Murray Engineering has set a new record. With the Bethany Senior Terraces project, Murray Engineering has helped to develop NYC’s first modular structure that fully encompasses passive house principles — introducing a new era of energy efficiency in the energy-conscious city that never sleeps.
How LAMOD is Using Modular to Address Inefficiency, Sustainability, and the Future of Construction
As developers, designers, and contractors seek to understand the evolving needs of the modular industry, no one is as well-versed in the benefits of going modular as Mārcis Kreičmanis. As the co-founder and CBDO of LAMOD in Riga, Latvia, Mārcis has made it his ultimate goal to address the inefficiencies of traditional construction.
From Furniture Builder to ‘Activist Architect’: Stuart Emmons’ Unique Journey
Stuart Emmons was fascinated by buildings at a young age. He remembers building sand cities with his brother during trips to the Jersey shore. His father gave him his first drawing table at the age of ten. Today, he is an experienced architect who received his FAIA in June 2025. The road he took is unique, to say the least.
Forge Craft Architecture + Design: Codes, Contracts, and Intellectual Property
Founding Principal and Director of Modular Practice for Forge Craft Architecture + Design, Rommel Sulit, discusses the implications of codes, contracts, and intellectual property on
modular construction.
Eisa Lee, the “Bilingual” Architect
Now as the founder of XL
Architecture and Modular Design in Ontario, Canada, she applies not just her education as a traditional architect but an entire holistic view on modular design. It’s this expansive view that guides her work on being a true partner that bridges the gap between architects and modular factories as they collaborate on the design process.
Tamarack Grove Engineering: Designing for the Modular Sector
The role of a structural engineer is crucial to the success of a modular project, from initial analysis to construction administration. Tamarack Grove offers structural engineering services — project analysis, plan creation, design creation, and construction administration — for commercial, manufacturing, facilities, public services, and modular. Modular is only one market sector the company serves but it is an increasingly popular one.
Engineer Masters the Art of Listening to His Customers
Since founding Modular Structural Consultants, LLC. in 2014, Yurianto has established a steady following of modular and container-based construction clients, primarily manufacturers. His services often include providing engineering calculations, reviewing drawings, and engineering certification
Inside College Road: Engineering the Modules of One of the World’s Tallest Modular Buildings
College Road is a groundbreaking modular residential development in East Croydon, South London by offsite developer and contractor, Tide, its modular company Vision Volumetric (VV), and engineered by MJH Structural Engineers.
Design for Flow: The Overlooked Power of DfMA in Modular Construction
Unlocking higher throughput, lower costs, and fewer redesigns by aligning Lean production flow with design for manufacturing and assembly.
Choosing the Right Ramp
Modular construction offers a compelling alternative to traditional methods for designing and building ADA and IBC-compliant entrances. By addressing the challenges of traditional construction, such as time-consuming processes, unavailable specialized labor, and variable field conditions, modular solutions provide a more efficient, cost-effective, and reliable approach.