Vertical Engineering: Inside the World’s Tallest Modular Building with MJH Structural Engineers’ Michael Hough
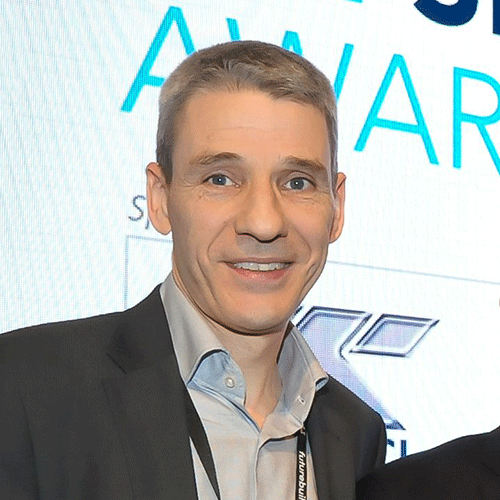
Michael Hough is the founder of MJH Structural Engineers
Michael Hough’s engineering career started in the offsite industry with a Dublin-based precast concrete manufacturer in the late 1980’s.
“I commenced my engineering career with a precast manufacturing business and gained insights and interests in the offsite nature of the construction,” says Hough. “Even though I moved into consulting engineering, when I look back I can see that I always had an interest in the detailing, understanding how elements went together, and creating bespoke solutions for connections and assemblies. This interest has encouraged me into the area of offsite construction that encompasses modular construction.”
After a number of years, Michael joined Barrett Mahony Consulting Engineers in Dublin and progressed to become one of the managing partners. Then, having been introduced to modular construction in 2003, Michael struck out on his own and founded MJH Structural Engineers in 2015 to concentrate on providing solutions for the modular construction industry.
Finding the Perfect Modular Partner
Since the founding of MJH, modular construction has experienced a coming of age both locally in the UK and on the global stage, in part due to the structural engineering services provided by MJH. Since 2015, MJH has provided the structural engineering design for Vision Modular Systems (VMS), the manufacturer behind several high-rise modular projects that have pushed the boundaries for modular construction in terms of construction height, project completion time, and structural engineering complexity.
“We have worked very closely with VMS, and in particular with John Fleming, to develop the system from the early days to the high-rise solutions that VMS now employs,” says Hough. “John has always had a lot of drive and continuously pushed the limits of our previous achievements, continuously funding R&D to investigate new possibilities has been a large part of this process. Together with VMS we create solutions for elements of the structural system or the connections and then analyze, engineer, and test these solutions until we were satisfied with the strength and simplicity for construction.
“There were many challenges along the way,” adds Hough, “developing engineering solutions that consider all aspects of the construction, creating connections that work with the offsite nature of the build and ensuring they provide the necessary structural resistance, and developing much higher levels of details than might be required from a traditional consulting engineering practice.”
Hough’s collaborations with VMS have included projects such as Apex House (28 stories of modules), Mapleton Crescent (25 stories of modules), 101 George Street (43 stories of modules), Lewisham Exchange (33 stories of modules), have all been brought from concept to completion and occupation since 2017, with 101 George Street currently the tallest modular building in the world at 136 meters tall. This will shortly be surpassed by a project MJH is working on with VMS at College Road (44 stories of modules), which will be approximately 150 meters tall. And several other similarly tall projects are in the pipeline, including Marsh Wall, Walthamstow, and Castle Pub ranging from 33 to 50 stories tall.
MJH continues to work with VMS to create and advance the modular structural system to improve efficiency, simplify the connectivity and site work, and minimize material usage and waste. The modular system of construction lends itself to manufacturing with repeated details and systems. This allows efficiencies of scale through the design, detailing, and construction phases.
Mastering Modular Design
MJH developed its engineering knowledge over several years, starting with a variety of low-rise modular projects. Medium-rise and then high-rise construction were added as MJH’s knowledge and experience grew.
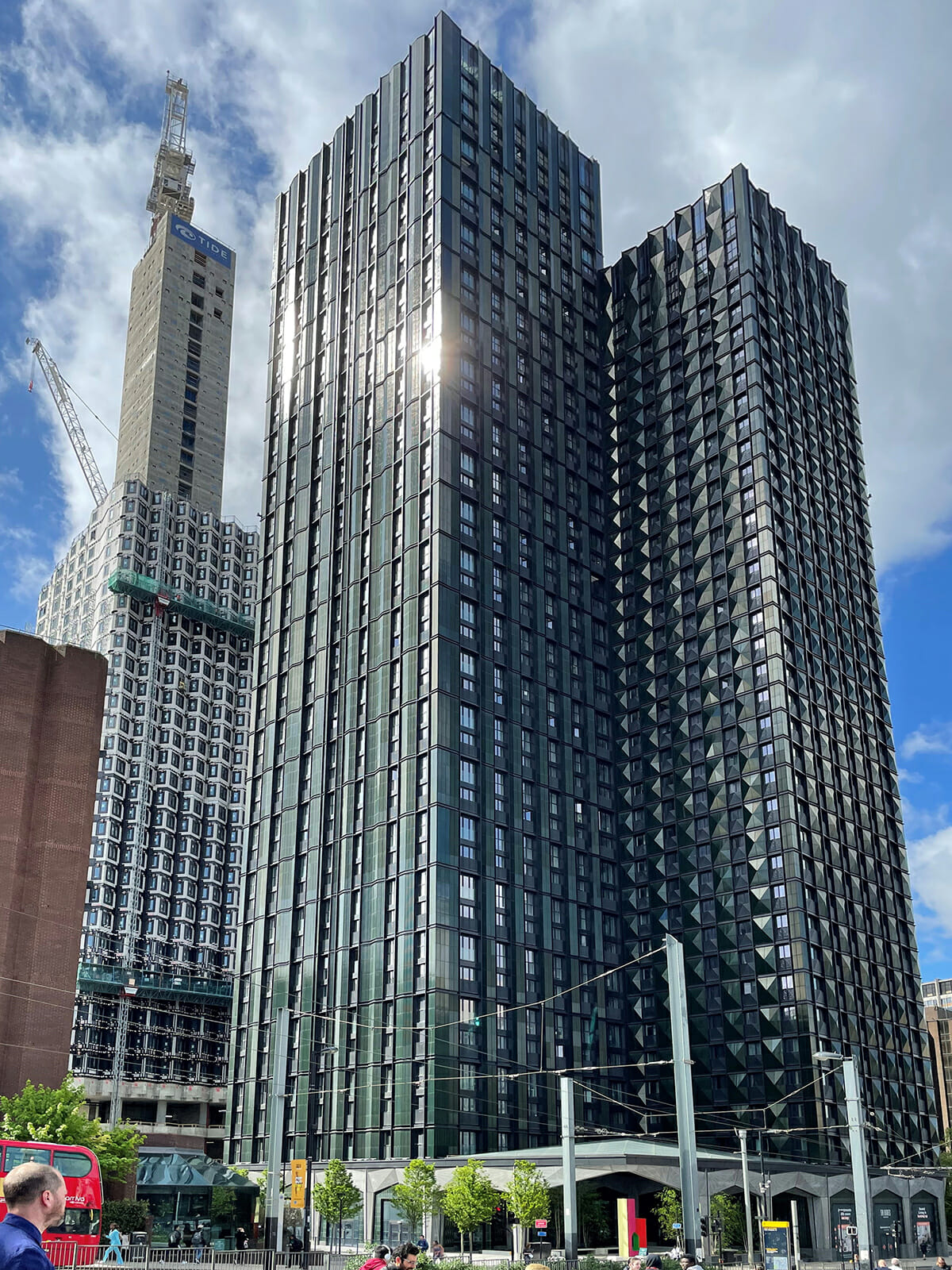
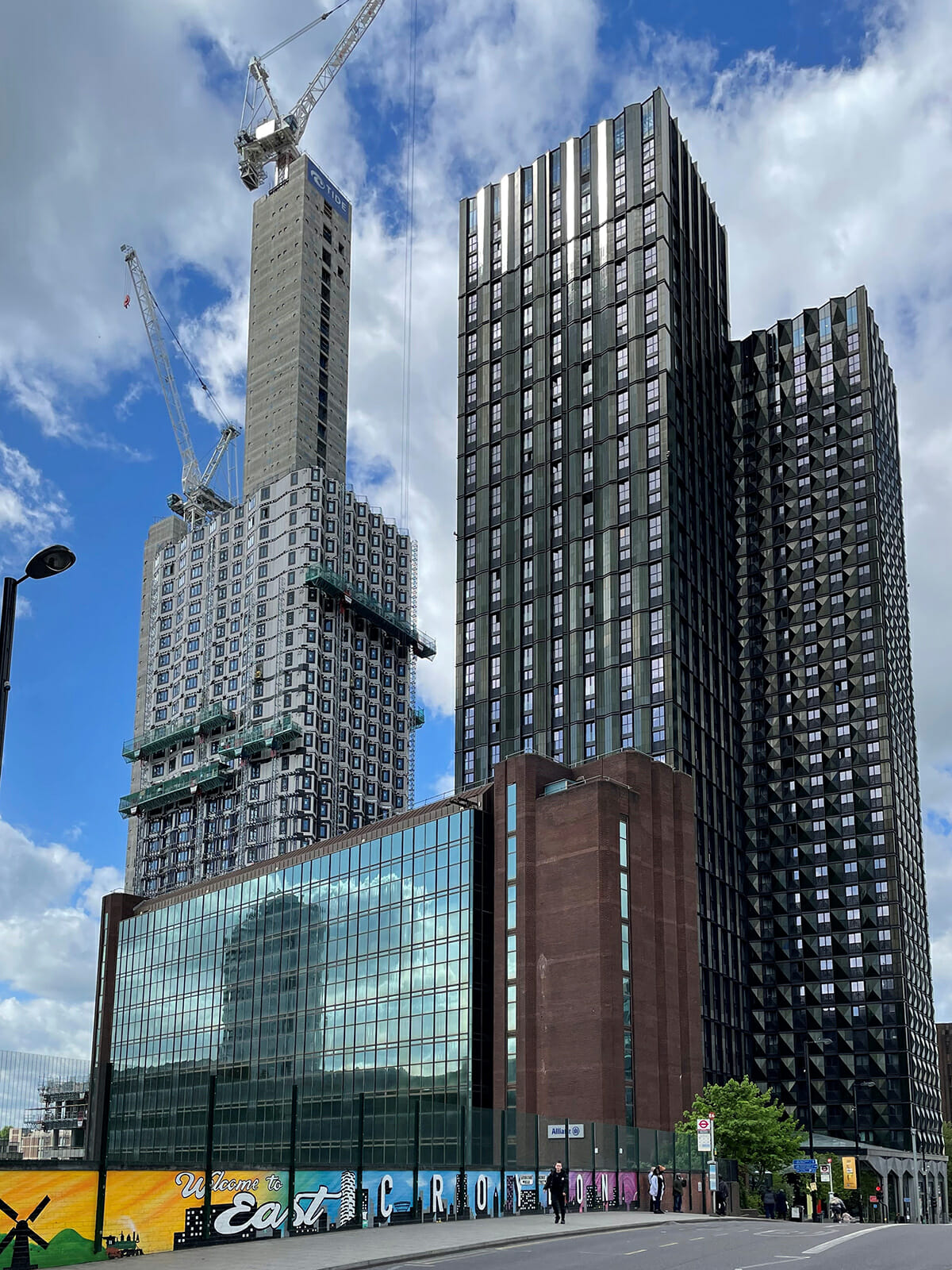
101 George Street stands tall in London and is currently the world's tallest volumetric modular building. College Road, another modular building, is under construction just behind.
High-Rise Modular Building Design 101
Connecting the Blocks
High-rise modular construction utilizes a key element borrowed from many traditional skyscrapers: the centralized core shaft. The building core is constructed with reinforced concrete and is home to the elevator shafts, emergency stairwells and major utility service runs. The modular units that abut the core shaft are structurally connected to the core before installing adjoining units. The modules are all interconnected and all the horizontal loads on the building are transferred through the modules and supported by the concrete core.
Some of the key items to consider in the structural design of modules are the assembly of the modules and the design of the connections between the modules. In addition to their capability to build high-rise modular buildings, well-placed connections provide flexibility of layout to the architects. This philosophy of providing flexibility results in projects which, when complete, do not resemble the traditional perception of modular buildings.
The importance and complexity of the connections used in the modular system increases as the building gets taller, both in line with the traditional rules for execution classes and with the increased difficulties associated with building taller buildings in general. A major consideration when designing connections for modular buildings, in addition to their structural capacity, is the location of the connections within the modules. Having access to these connections during installation allows for minimal disruption to the finishes within the modules.
The Importance of BIM
For high-rise buildings, computational design is employed alongside BIM modelling to create a full building model that is used for the fabrication of the modules. Each module is individually referenced and forms part of an assembly with shared information. Prior to manufacture, all services are fully coordinated by wall, module, and assembly of modules. Adequate space for connections, access, avoidance of clashes, and simplicity of site work is prioritised and coordinated.
The process commences with detailed drawings for the structure and intensifies with information from other disciplines and coordination right through to site install. At each stage of design, manufacture, and construction the relevant information is presented in the most appropriate manner using the most appropriate technology. This methodology allows for direct linking with CNC machines to improve manufacture as well as the ability of the manufacturer to determine the most efficient service routes through the modules.
Since the start of their partnership in 2015, MJH has worked closely with VMS to develop structural systems and connections with sufficient accuracy and flexibility to permit high-rise construction. Unlike traditional construction, the delivered modules are rigid units with internal finishes which limit the ability to line and level. This requirement must be engineered into the system.
Weight was another factor Michael’s team had to account for as they designed taller projects. For example, the modules in the Croydon project weigh over 20 tonnes each.
“Each module has to be constructed in the factory, transported to site, and craned into place,” says Hough. “The ability to work with heavy units allows us to maximize the size of the module and minimize the number of them on a floor plate. This gives rise to efficiencies in the construction in terms of number of manufactured items, items craned on site, connections, finishing and speed of the overall operations.”
Due to the nature of modular construction and its demand for accuracy, the building weights are very predictable. This ability to predict the building weights helps ensure precise engineering design and streamlined onsite assembly.
101 George Street: A Towering Achievement
MJH has strived to establish itself as a leader in the field of structural design for modular construction and, through its relationship with VMS, its journey culminated in 101 George Street receiving recognition from several professional bodies in open categories for traditional construction. 101 George Street was awarded the Best Tall Building Award in 2020 at the UK Tall Building Awards, for which MJH were also awarded the Best Structural Engineer Award for their work on this project. 101 George Street was also a finalist for the 2021 IStructe Awards in the Tall and Slender Building categories and has received an award of excellence in the Best Tall Building 100-199m, Best Tall or Residential Building, Innovation, Construction, and Structural Engineer categories for the upcoming CTBUH awards in November in Chicago.
“101 George Street has moved modular into the realm of skyscrapers and is achieving recognition alongside some of the world’s most amazing new tall buildings,” says Hough. “Winning Best Structural Engineer with a modular building is a big step for the industry and places modular into the mainstream in the UK.”
About the Author: Curtis Dennis is a freelance writer specializing in the construction industry.
More from Modular Advantage
Samantha Taylor: Leading the (Modular) Design of Tomorrow
“With modern technology and the way we’ve all embraced things like BIM, file sharing, and video conferencing since COVID, it’s easy to collaborate with companies in Austria, or Singapore, or anywhere else in the world.”
Greg DeLeon: Military Engineering to Modular Design
Greg DeLeon, a structural engineer at ISE Structural Engineers in Temecula, California, can tell you not only how large a beam needs to be to support a house, but also how much explosives you’ll need to take it down, thanks to his unique combination of professional and military experience.
To Remake North Minneapolis, Devean George Swaps Basketball for Buildings
He’s lived in Los Angeles, Dallas, and San Francisco (to name a few). He’s delivered championships with the Los Angeles Lakers and made career-defining moves with the Dallas Mavericks and the Golden State Warriors. No matter the wins, the championships, or even the seemingly impossible 3-pointers, Devean George has always returned to where it all started for him: Minneapolis.
Chelsi Tryon: Making the World a Better Place
For Chelsi Tryon, Director of Environmental, Social, and Governance (ESG) for WillScot Mobile Mini, nothing is more enjoyable than increasing the
company’s sustainability efforts while simultaneously doing her bit to save the environment.
Joshua Hart: Pushing Boundaries
Joshua Hart, P.E., vice president at Modular
Solutions, can sum up his job responsibilities in one sentence: “I do whatever needs to be done.” Hart thrives on the variety and the opportunity to be involved in every aspect of the company. And it shows! You might say Hart has come full circle.
Jamie Metzger: From Construction to Apparel and Back Again
Growing up in a blue-collar city like Edmonton, Alberta, Canada, it’s no surprise that Jamie Metzger spent some time working labor jobs on construction sites. It’s one of the most common summer jobs in the city. But that’s probably the last predictable thing about this particular story.
Victor Masso: Expanding Modular in Puerto Rico
Victor Masso joined 2 Go Storage, a company started by his grandfather and father, in 2018 to develop a modular building division in the wake of the devastation caused by Hurricane Maria in 2017. Prior to joining the company, he had worked in the industry for about four years focusing on pharmaceutical, commercial, and government projects.
Eliyah Ryals: Finding the Perfect Fit
It’s not common for people to find their perfect career fit straight out of college. It’s even less common to find it in the town you grew up in. But that’s exactly what happened when Eliyah Ryals was told about vacancies at Panel Built and made the decision to apply.
Through It All, It’s Still About the Workers
By February 2024, the number of available, unfilled construction job openings had reached an all-time high. At some point, interest rates will fall, creating another surge in demand for such workers. In short, solving the nation’s skilled worker shortage issue has never been more important.
Navigating Insurance Challenges in the Modular Construction Industry
Utilizing practical written minimum insurance and indemnity requirements, along with monitoring certificates of insurance by someone who has COI training will not yield a perfect risk transfer strategy, but the exposure will be managed much better than it likely is currently.