Proposed Davis-Bacon Updates: A Deliberate Attack on the Modular Construction Industry
An examination of the Davis-Bacon Act and how its expansion could profoundly impact the modular construction industry
On May 11, 2022, the US Department of Labor (DOL) quietly issued a news release announcing a proposed update to the Davis-Bacon Act1. For the last 20+ years, most modular and off-site construction did not fall under the Davis-Bacon and Related Acts (DBRA) jurisdiction because the work does not occur on-site (primary location).
According to the press release1, the main reason for the update is to improve the Department's ability to administer and enforce prevailing wage standards more efficiently and effectively. In addition, the proposed changes include the following "key points".
- Creating several efficiencies in the prevailing wage update system and ensuring prevailing wage rates keep up with actual wages would mean higher wages for workers over time.
- Returning to the definition of “prevailing wage” used from 1935 to 1983 to ensure prevailing wages reflect actual wages paid to workers in the local community.
- Periodically updating prevailing wage rates to address out-of-date wage determinations.
- Providing broader authority to adopt state or local wage determinations when specific criteria are met.
- Issuing supplemental rates for key job classifications when no survey data exists.
- Updating the regulatory language to reflect modern construction practices better.
- Strengthening worker protections and enforcement, including debarment and anti-retaliation.
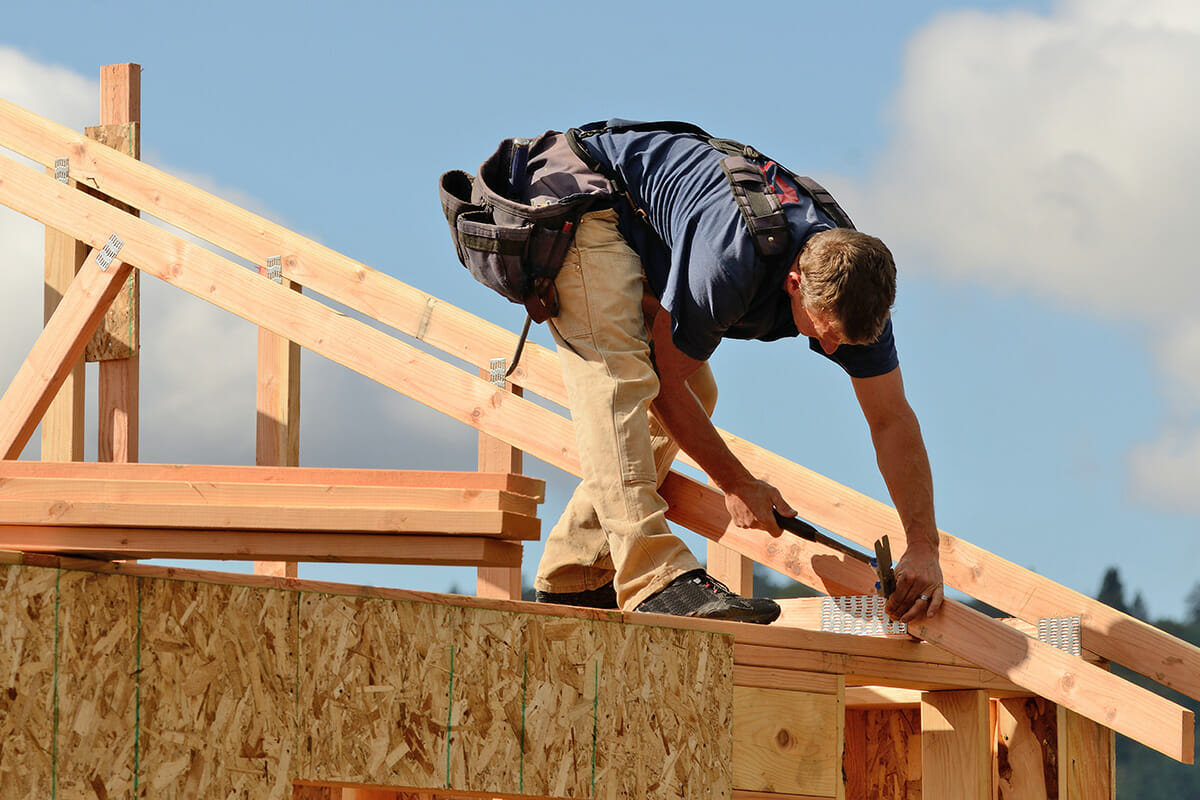
The Davis-Bacon Act (DBA) was written for—and has long only been applied to—onsite construction of federally-funded projects. The expansion of the DBA would mean prevailing wages would apply for both onsite and offsite workers.
The Acting Wage and Hour Division Administrator, Jessica Looman stated, "Given recent unprecedented investments in our nation's infrastructure, this comprehensive review is necessary to ensure employers on federally funded or assisted construction projects pay fair wages to the workers who build our roads, bridges, federal buildings and energy infrastructure.”
Based on the language used for the press release, it appears that the primary purpose of the DBRA is to streamline the enforcement process and address some outdated wage determinations.
On March 18, 2022, the Federal Register published the Proposed DBRA Updates2 and opened a sixty-day commenting period for contractors and stakeholders to express their viewpoint on the proposed changes.
On Prevailing Wages
Davis-Bacon requires that on-site workers be paid the local prevailing wage for their craft/occupation on federally funded or assisted projects, based on the prevailing wage determinations provided by the U.S. Wage and Hour Division (WHD).
Usually, the wage determinations match the current local union pay scale (hourly rate plus benefits) for the same work classification. The contractor must pay the prevailing wage to on-site workers and submit weekly payroll reports, certifying the company’s compliance under penalty of perjury.
Recent data from the Bureau of Labor Statistics3 indicates that the median pay for a carpenter in the State of California is $31.57, while in New York State the average rate is $31.94 per hour.
Labor costs for a public works project can nearly double compared to a non-DBRA project. And this does not include the mandatory hourly fringe benefits for DBRA projects, which can add another $8-10/hour. While many might erroneously argue that the higher DBRA wages somehow deliver a superior final product, there is no research to suggest this correlation and every contractor's work must pass the local building requirements and inspections.
Luckily, the modular and off-site construction industries have never had to concern themselves with these issues – until now.
Deep down within the proposed DBRA updates (2) is a singular paragraph that could stop the industry dead in its tracks.
(G) Site of the Work and Related Provisions
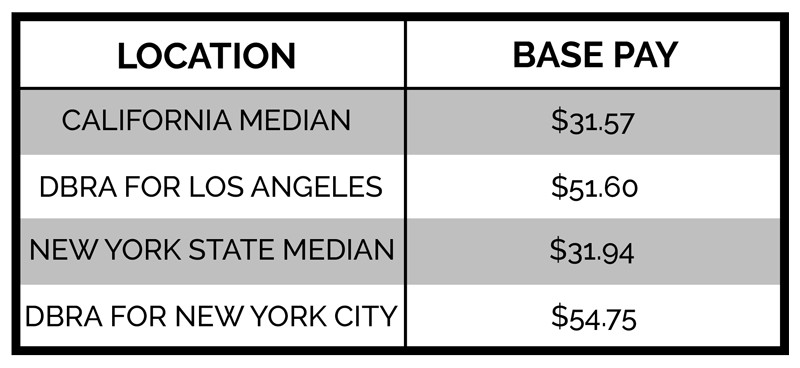
This chart compares the state median wage to the DBRA wage determinations for two
major metro areas.
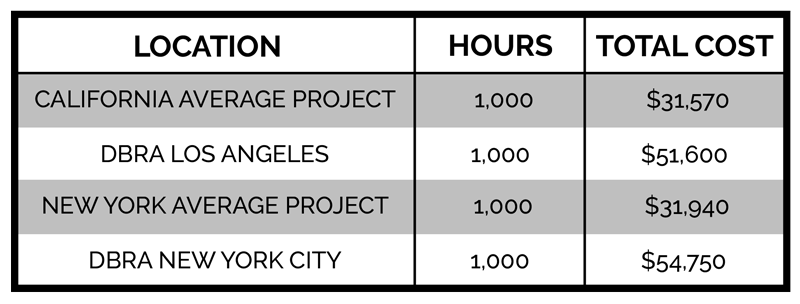
For a project requiring 1,000 labor hours, here are the aggregate cost comparatives.
What is the Site of Work?
The Department proposes the following revisions related to the DBRA’s ‘‘site of the work’’ requirement: (1) Revising the definition of ‘‘site of the work’’ to further encompass certain construction of significant portions of a building or work at secondary worksites, (2) clarifying the application of the ‘‘site of the work’’ principle to flaggers, (3) revising the regulations to better delineate and clarify the ‘‘material supplier’’ exemption, and (4) revising the regulations to set clear standards for DBA coverage of truck drivers.
(1) Current Statutory and Regulatory Provisions Related to Site of the Work
a. Site of the Work
The DBA and Related Acts generally apply to ‘‘mechanics and laborers employed directly on the site of the work’’ by ‘‘contractor[s]’’ and ‘‘subcontractor[s]’’ on contracts for ‘‘construction, alteration, or repair, including painting and decorating, of [covered] public buildings and public works.’’ 40 U.S.C. 3142(a), (c)(1).
The Department’s current regulations define ‘‘site of the work’’ as including ‘‘the physical place or places where the building or work called for in the contract will remain’’ and ‘‘any other site where a significant portion of the building or work is constructed, provided that such site is established specifically for the performance of the contract or project.’’ 29 CFR 5.2(l)(1).
They further provide that in general, ‘‘job headquarters, tool yards, batch plants, borrow pits, etc.’’ are part of the ‘‘site of the work’’ if they are ‘‘dedicated exclusively, or nearly so, to performance of the covered contract or project’’ and also are ‘‘adjacent or virtually adjacent to the site of the work’’ itself. 29 CFR 5.2(l)(2).
Perhaps the two most important words of the entire proposed update are “secondary worksite,” at least for anyone working in the modular construction industry. And it doesn’t matter whether you perform prevailing wage project work or not; those two little words could potentially wreak havoc across the entire modular industry.
Secondary Worksites
Another problem with the secondary worksites is the concern that they are the first phase of building a slippery slope regarding future DBRA projects.
Based on the proposed DBRA changes, what happens to the project architect for a relocatable classroom project?
Most of the design and drawing work will likely occur at the architect's office (secondary worksite?). With the specifically-built-facility clause removed, the architect should collect or be paid the prevailing wage rate for architects.
Unfortunately, there is no current wage determination for architects, so how does the architect maintain DBRA compliance?
And what about the sheet metal shop that manufactures HVAC ducting? Or the factory assembling the heating and AC units? The State of California has already determined that offsite sheet metal fabrication does NOT fall under prevailing wage requirements in the Russ Will Mechanical case. But will that case matter to the feds if the proposed update takes effect?
Thanks to the secondary worksite language, and the fact that their work will become part of a DBRA project, will factory workers everywhere become eligible for prevailing wages while performing their off-site factory work?
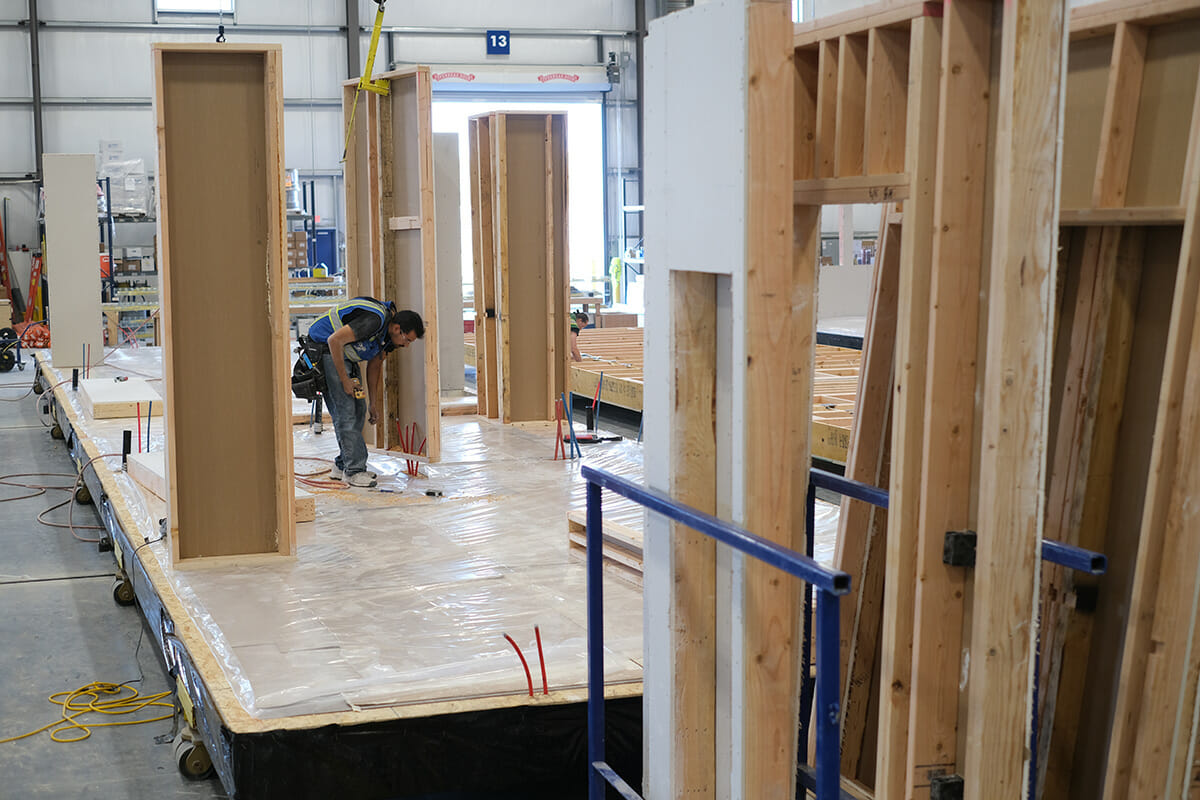
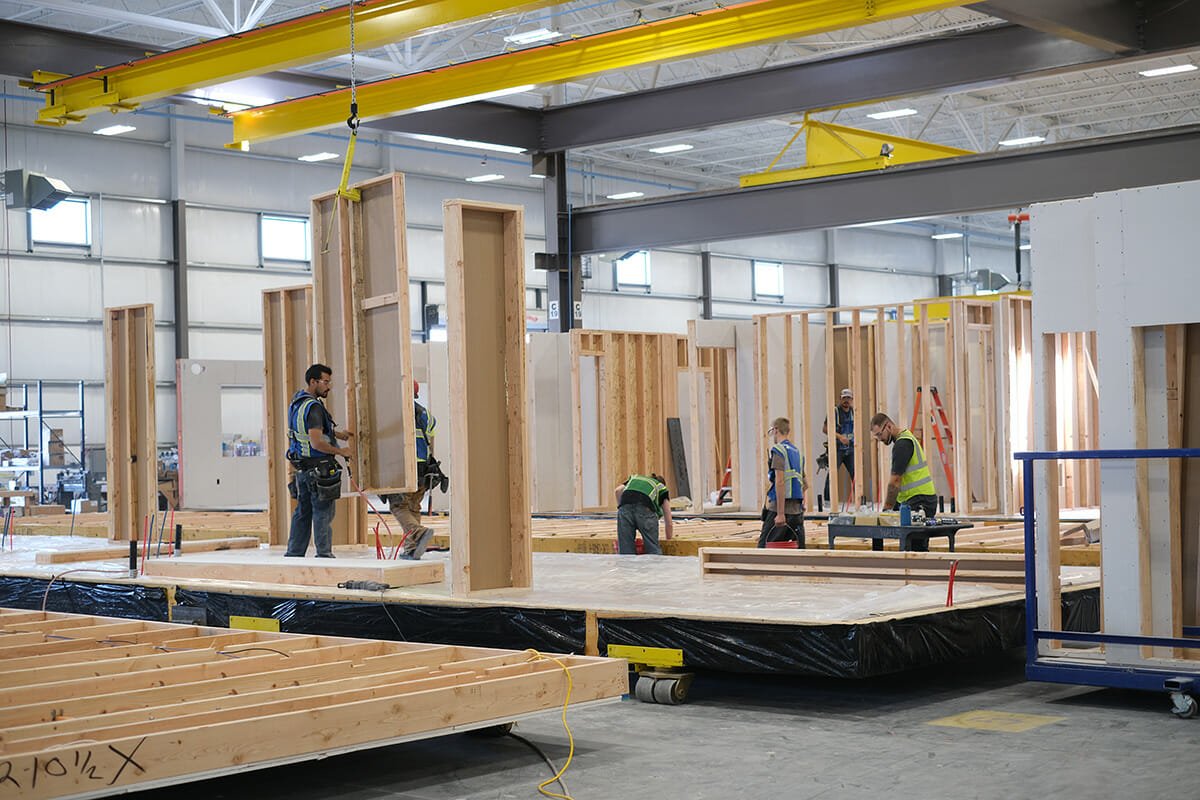

Offsite construction and assembly is often done by cross-trained workers. How would prevailing wages be set for workers who act as builders, plumbers, and electricians? Image credit: Autovol
One possible outcome is that any manufacturer that provides building materials or products for a DBRA project could find themselves unwittingly drawn into a compliance nightmare if the proposed update goes into effect.
Does the WHD Have the Power to Change the Law?
Many across the construction industry, not just modular and off-site contractors, are questioning the timing of this proposed update and whether the WHD has the power to change the laws it enforces.
On May 16, 2022, President Biden announced New Actions to Ease the Burden of Housing Costs (4) and specifically referenced modular and off-site construction to lower construction costs while rapidly increasing the supply of available homes nationwide. The President also discussed changing lending laws to make financing a modular home easier through existing federal loan programs.
However, Biden’s Housing Plan makes no mention of expanding DBRA requirements to include off-site/modular construction, a move that will certainly INCREASE the cost of housing.
If Onsite Construction is an Apple, Offsite is an Orange
Another point of contention involves the tools and processes used for on- and off-site construction. Again, sticking with the carpenter example from above, the DBRA suggests that a carpenter builds walls and that the work is the same whether the location is on or off-site. Unfortunately, while the result is the same (a framed wall), the processes and tools are not.
The on-site worker will need to climb ladders or scaffolding to complete the work; the off-site worker predominantly uses tables and jigs.
The on-site worker uses portable/handheld devices for cutting, and the off-site worker utilizes a permanent saw station.
The on-site worker deals with a constantly changing work area while the off-site worker area seldom changes.
The on-site worker normally carries his tools and materials using a truck or van; the off-site worker doesn't deal with this issue.
The on-site worker deals with inclement weather, and the off-site worker predominantly works inside the facility regardless of the weather.
The Modular Industry's Response
Obviously, what the DBRA labeled as an update could dramatically impact the entire modular/off-site construction industry.
Here is a small sampling of the different perspectives posted by MBI members, and others in the modular and off-site construction industry2.
ID: WHD-2022-0001-27916
Please consider these comments as a strong opposition to the expansion of the Davis Bacon rates to offsite construction.
As a modular manufacturer we depend on work from many sectors including federal contracts, state agencies, local school districts, and the private sector. However, this expansion will likely eliminate multiple potential sectors by forcing us to meet these requirements for all work done in our factory or simply stop pursuing projects where this would apply. It is safe to say the result will be lost revenue and lost jobs at our factory at a minimum.
ID: WHD-2022-0001-26695
I strongly oppose the legislation to expand the Davis Bacon regulations to offsite manufacturing of buildings because, quite simply, offsite manufacturing is clearly manufacturing and not construction. It would no sooner apply to the fabrication of buildings offsite as it would the fabrication of any other building components. It's inappropriate to compare offsite manufacturing with construction because the nature of the jobs and working environment are so different. Please don't put manufacturing jobs in the US at risk by not understanding this crucial distinction.
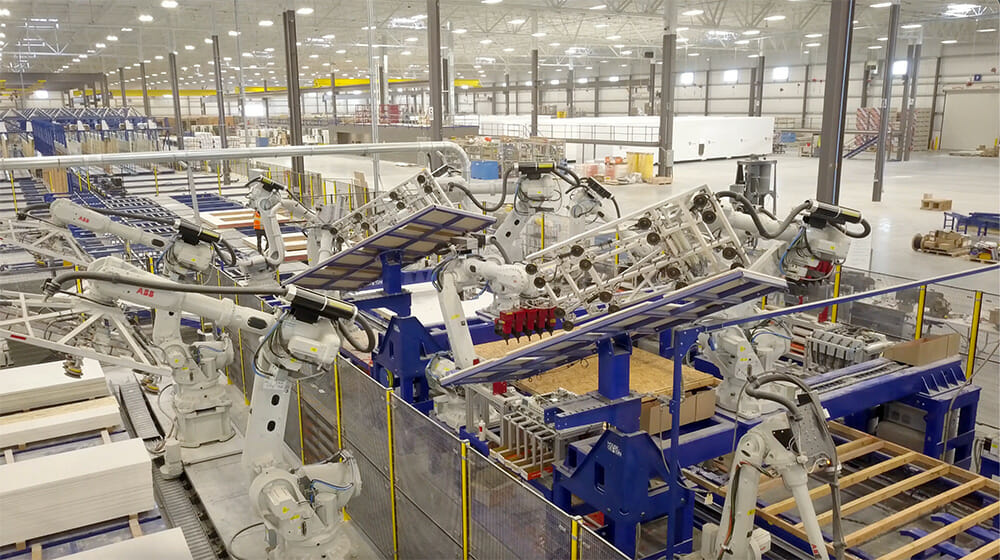
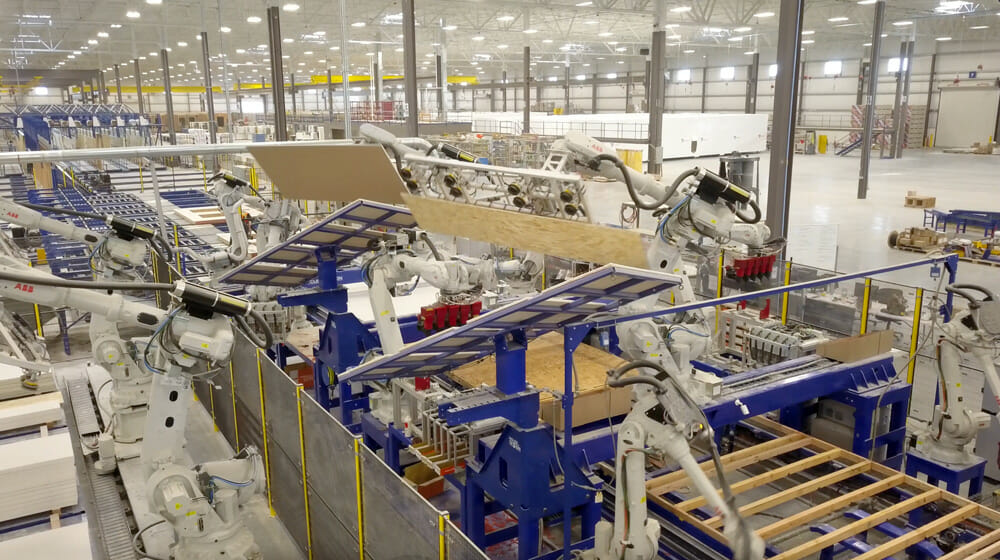
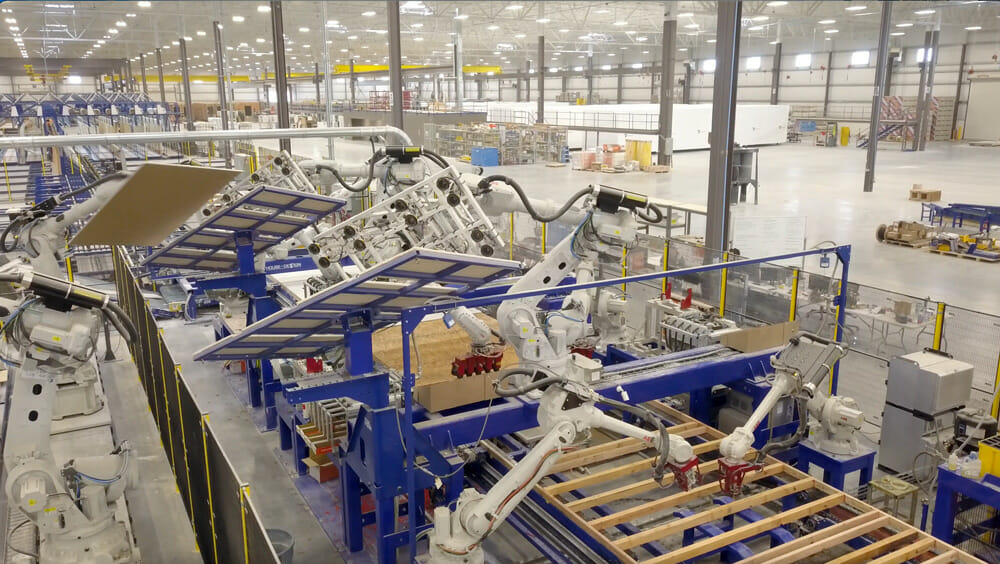
Many modular manufacturers are turning to automation to improve speed, safety, and efficiency, all of which are critically needed to address the growing need for federal- and state-funded affordable housing and infrastructure. In MBI’s view, the DBA expansion is a significant disincentive for such manufacturers to bid on these projects and threatens our industry’s ability to participate in and solve these immediate problems. Image credit: Autovol
ID: WHD-2022-0001-29352
As a small business owner, the expansion of Davis Bacon rates to offsite construction will create an administrative hardship leading to one of two outcomes – higher cost for construction or my company declining to bid on future federal work. We always have multiple projects being constructed at any given time with manpower bouncing back and forth between project as needed. The logistics of paying different labor rates for different projects and the employee relations aspects of employees only wanting to work on higher paying projects which are side-by-side in the factory are management nightmares. Please do not expand the Davis Bacon rates to offsite construction.
ID: WHD-2022-0001-27649
I lead a large regional modular building solutions provider and I have grave concerns about the proposed expansion of the Davis Bacon act. The proposed expansion will have a number of unfavorable outcomes for taxpayers, the government, school districts. A modular approach to construction is being adopted because it represents a sustainable, higher productivity approach. Projects can be completed more quickly at or slightly below the costs of conventional construction. Adding significant labor costs to a project will result in fewer modular projects, which will result in more waste, higher administrative costs and longer project timelines. Firms may choose to use modular providers outside of the US, who will have a cost advantage as they don't have to abide by the same rules.
This expansion also severely impacts our ability to use small businesses and other diversified suppliers. They don't have the capabilities or processes to track labor hours at the level of detail needed and will no longer able to participate or be competitive. The administrative costs of tracking multiple rates of pay based on the type of project across lots of different trades are astronomical. We cannot manage this and would likely have to seek fewer government projects.
Implementing measures to increase construction costs when supply chains and inflation are already challenged, seems very short-sighted. I hope you will reconsider this unnecessary expansion of the Davis Bacon rules.
Lastly, here is a summary of a phone interview conducted with Jennifer A. Harper, Global Employment Law and Policy Head, L&E Government Contracts Industry Group, Squire Patton Boggs. Jennifer and her firm were hired by MBI to spearhead the modular industry’s response to the DBRA expansion.
“If I could summarize what should happen, it must be a complete withdrawal of the ‘secondary’ worksite provision expanding the Davis Bacon Act (DBA) to offsite modular businesses. The expansion of DBA to offsite construction ignored the express language of the Act unambiguously limiting prevailing wages to laborers and mechanics employed ‘directly on site’ and creates an untenable financial impact on contractors within the industry (particularly for small to medium businesses). This will reduce participation and competition for federal construction projects and have a halting effect on federally funded public projects like affordable housing, school classroom construction, and potentially even military and federal infrastructure projects.”
What Happens Next?
Unfortunately, the commenting period closed on May 17, and the next step is to wait and see what the WHD decides what to do with the proposed update.
- They could opt to do nothing and leave the current DBRA requirements alone.
- They could attempt to implement the proposed updates with changes made to address the feedback concerns.
- They could attempt to implement the proposed update and then battle any future legal challenges.
- They could put the update on hold and reopen the update process to include roundtable discussions with industry leaders and representatives from around the nation to create changes that don't threaten our businesses and economic well-being.
Hopefully, the WHD will choose options 1, 2, or 4.
“We’re hoping the WHD chooses to do nothing, but that’s not looking likely,” says Tom Hardiman, executive director of the Modular Building Institute. “If they do proceed, then they should at least take a close look at the feedback our industry has provided and reconsider their next steps.”
MBI’s expectation, however, is that the WHD will default to option 3 and let the courts figure it out.
The SBA, the AGC, the MBI, and the NAHB have already expressed their opposition to the proposed update. Only time will tell if the update does go into effect and if any legal challenges get filed.
Get Involved
Unfortunately, while the proposed update goes through the courts, the proposed update and revisions would go into effect until changed or modified by the court’s final ruling. Luckily, there is something that we can do as the waiting game plays out.
Step 1. Find out who your congressional representatives (both the House and Senate) are via congress.gov. Simply enter your physical mailing address into the search box and receive their contact information.
Step 2. Send them a letter or email urging them not to support the proposed update for the reasons that resonate most with you. Or you can use this handy template.
Use This Template
Dear Senator or Representative <insert their last name>,
I am writing you today regarding the WHD’s Proposed DBRA updates.
Although labeled as an update to the current DBRA requirements to streamline the agency’s enforcement and wage determinations, it’s a significant change to the existing DBRA laws passed by Congress.
In short, the protections from DBRA compliance for off-site and modular construction are stripped away with changes to the definition of "site of work" and the addition of new language, specifically "secondary worksite.”
The goal of this update seems to focus on severely limiting or eliminating our industry's participation in any project that receives federal or state funding.
I urge you to not support this DBRA update.
Thank you,
<Your name, email address, and phone number>
Citations:
- FOR THE FIRST TIME IN 40 YEARS, US DEPARTMENT OF LABOR PROPOSES RULEMAKING FOR DAVIS-BACON ACT TO REFLECT NEEDS OF TODAY’S CONSTRUCTION INDUSTRY. (2022, March 18). US Department of Labor. Retrieved June 25, 2022, from https://www.dol.gov/newsroom/releases/whd/whd20220311
- Updating the Davis-Bacon and Related Acts Regulation. (2022, March 18). Retrieved June 29, 2022, from https://www.federalregister.gov/documents/2022/03/18/2022-05346/updating-the-davis-bacon-and-related-acts-regulations
- Occupational Employment and Wage Statistics. (2022, March 21). Bureau of Labor Statistics. Retrieved June 25, 2022, from https://www.bls.gov/oes/current/oes472031.htm
- President Biden Announces New Actions to Ease the Burden of Housing Costs. (2022, May 16). The White House. Retrieved June 25, 2022, from https://www.whitehouse.gov/briefing-room/statements-releases/2022/05/16/president-biden-announces-new-actions-to-ease-the-burden-of-housing-costs/
About the Author: Curtis Dennis is a freelance writer specializing in the construction industry.
More from Modular Advantage
Samantha Taylor: Leading the (Modular) Design of Tomorrow
“With modern technology and the way we’ve all embraced things like BIM, file sharing, and video conferencing since COVID, it’s easy to collaborate with companies in Austria, or Singapore, or anywhere else in the world.”
Greg DeLeon: Military Engineering to Modular Design
Greg DeLeon, a structural engineer at ISE Structural Engineers in Temecula, California, can tell you not only how large a beam needs to be to support a house, but also how much explosives you’ll need to take it down, thanks to his unique combination of professional and military experience.
To Remake North Minneapolis, Devean George Swaps Basketball for Buildings
He’s lived in Los Angeles, Dallas, and San Francisco (to name a few). He’s delivered championships with the Los Angeles Lakers and made career-defining moves with the Dallas Mavericks and the Golden State Warriors. No matter the wins, the championships, or even the seemingly impossible 3-pointers, Devean George has always returned to where it all started for him: Minneapolis.
Chelsi Tryon: Making the World a Better Place
For Chelsi Tryon, Director of Environmental, Social, and Governance (ESG) for WillScot Mobile Mini, nothing is more enjoyable than increasing the
company’s sustainability efforts while simultaneously doing her bit to save the environment.
Joshua Hart: Pushing Boundaries
Joshua Hart, P.E., vice president at Modular
Solutions, can sum up his job responsibilities in one sentence: “I do whatever needs to be done.” Hart thrives on the variety and the opportunity to be involved in every aspect of the company. And it shows! You might say Hart has come full circle.
Jamie Metzger: From Construction to Apparel and Back Again
Growing up in a blue-collar city like Edmonton, Alberta, Canada, it’s no surprise that Jamie Metzger spent some time working labor jobs on construction sites. It’s one of the most common summer jobs in the city. But that’s probably the last predictable thing about this particular story.
Victor Masso: Expanding Modular in Puerto Rico
Victor Masso joined 2 Go Storage, a company started by his grandfather and father, in 2018 to develop a modular building division in the wake of the devastation caused by Hurricane Maria in 2017. Prior to joining the company, he had worked in the industry for about four years focusing on pharmaceutical, commercial, and government projects.
Eliyah Ryals: Finding the Perfect Fit
It’s not common for people to find their perfect career fit straight out of college. It’s even less common to find it in the town you grew up in. But that’s exactly what happened when Eliyah Ryals was told about vacancies at Panel Built and made the decision to apply.
Through It All, It’s Still About the Workers
By February 2024, the number of available, unfilled construction job openings had reached an all-time high. At some point, interest rates will fall, creating another surge in demand for such workers. In short, solving the nation’s skilled worker shortage issue has never been more important.
Navigating Insurance Challenges in the Modular Construction Industry
Utilizing practical written minimum insurance and indemnity requirements, along with monitoring certificates of insurance by someone who has COI training will not yield a perfect risk transfer strategy, but the exposure will be managed much better than it likely is currently.