Offsight’s Value Add to Your Factory
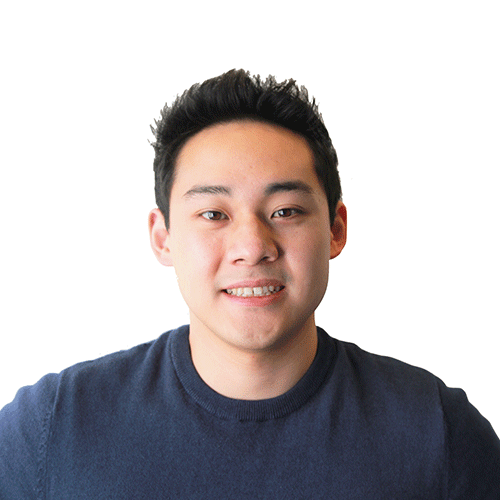
About the Author: Andrew Xue is the chief operating officer at Offsight, a developer of factory project management software for the offsite construction and building components industry.
The offsite and modular construction industry is booming. Over the coming 5 years analysts predict a fundamental shift in the construction industry, resulting in a new $256B annual profit pool up for grabs. This new demand has incentivized the founding of many new factories and the expansion of many currently operating modular businesses. These factories, which are at various stages of production maturity, face an important choice. When is the best time to implement technology and is technology needed to improve and manage quality reporting and operational processes?
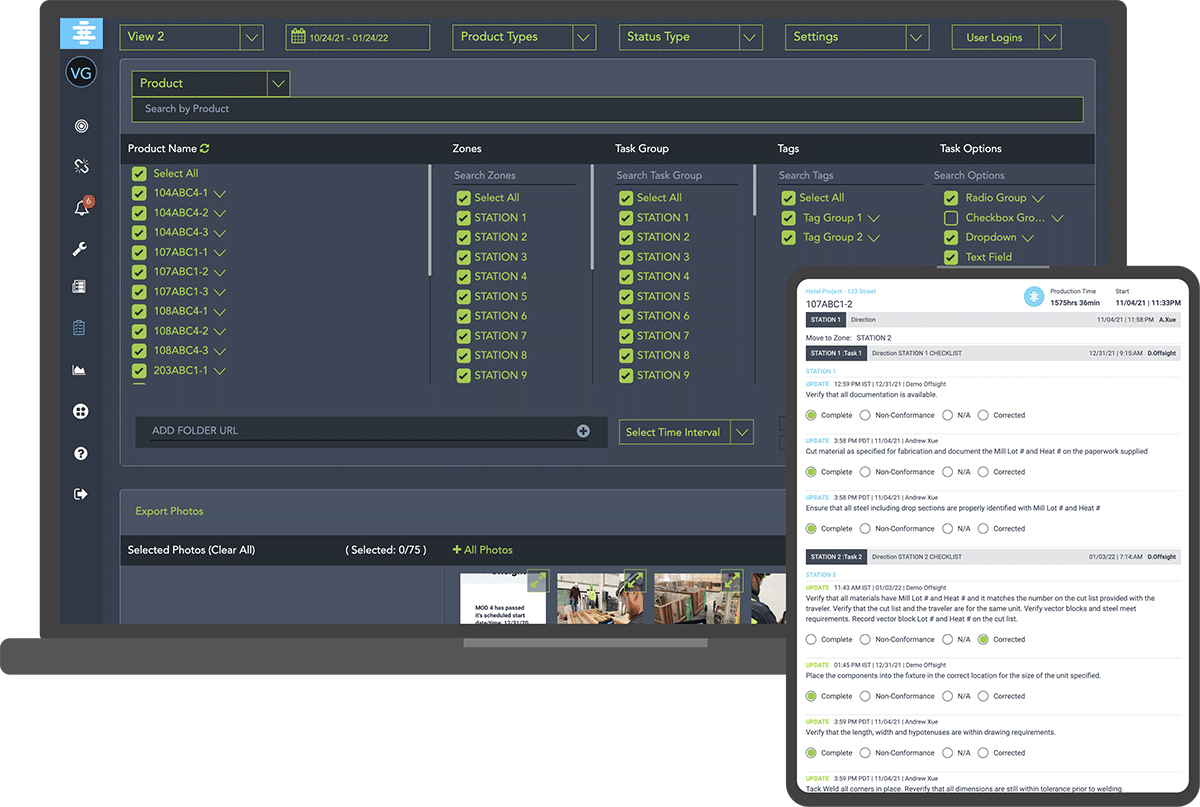
In this article, we outline the value of Offsight’s factory project management software across several clients that participated in case studies after implementing Offsight:
- Volumetric Building Companies (VBC) is a vertically integrated manufacturing and construction company that uses Offsight’s project management software to provide module-level visibility to all critical stakeholders and ensure every offsite project is successful. Offsight provides a multitude of customizable checklists to track production and quality of each module. After module delivery, Offsight digitally stores the entire history of the module and all relevant activity in the History tab. This includes all production interactions such as images taken on the factory floor, checklists completed and production data, which can be leveraged for future offsite projects.
- Z Modular, a subsidiary of industry steel giant Zekelman Industries, has implemented Offsight’s project management software at their Chandler, AZ and Killeen, TX modular manufacturing facilities to streamline product quality and production progress tracking. Offsight’s software helps manufacturers maximize scalability in their process, coordinate with many internal and external project stakeholders and provides a level of flexibility necessary to accommodate a wide variety of commercial modular projects.
See our Online Case Studies
The rapid rise of offsite and modular construction across multifamily, commercial, affordable housing, workforce housing and hospitality projects have shifted work from the traditional construction jobsite to the factory. With this process shift and move to modular, owners and project stakeholders are increasing their expectations around managing production quality and reporting at the factory level. In this case study, we walk through how industry leaders leverage Offsight to track factory quality and manage crucial internal and third-party reporting.
The global modular construction market is booming and expected to exceed $100B by 2025 with steel modular construction expected to be the fastest growing segment over the next 5 years. This bodes well for many steel modular manufacturers, including Offsight’s customer Z Modular.
Check us out at the 2022 World of Modular
Implementing Offsight’s technology, even at the early stages of your factory’s prototyping and design production stage, helps you avoid rising operational costs and position your business as an innovative and thought leading brand for operational and quality excellence from day one. If you’re interested in learning more, we encourage you to visit our booth at the 2022 World of Modular Conference. You can check out our product in action or reach out to our team directly at sales@offsight.com to schedule your private demo.
More from Modular Advantage
DORÇE Navigates Mountainous Terrain, Extreme Weather to Help Rebuild Türkiye
The February 6 earthquakes in 2023 were enormous. In response, DORÇE moved quickly, obtaining a government bid to help create housing and multipurpose structures—both temporary and permanent—for earthquake victims and laborers hired for reconstruction efforts.
Modern Desert Oasis: Building Reset Hotel the Modular Way
While the off-site construction part of the Reset Hotel project has been carefully controlled and with every necessity close at hand at BECC Modular’s factory in Ontario, Canada, the remote location of the project site has created additional challenges for the on site portion of the build.
Revisiting Yellowstone Canyon Village—a Groundbreaking Modular Construction Feat—Ten Years On
With such a short building period due to impending cold, it made the most sense for park developer Xanterra to pursue modular. Yellowstone’s high visitor traffic also required some odd transportation scheduling, as traffic from the West Yellowstone entrance determined the times when trucks could unload modules. Guerdon was up to the challenge.
Built for Brutal Cold, This Modular Office Building Shines
Houlton, the county seat of Aroostook County, Maine, is a small town with a population of about 6,000 residents. Situated along the border between the U.S. and Canada, what the town is most known for is bitterly cold winters. When the U.S. Border Patrol needed new office space, a modular building approach from Modular Genius offered the perfect solution.
Panel Replacement Adds Years of Life to Navy Vessel
Panel Built, Inc., recently replaced all the wall and roof panels on a two-story US Navy barge deck house that the company had originally installed 30 years ago, giving the vessel new life. Now, the commanding officer of the unit that uses the barge said the difference between the condition and appearance from when the barge left their facility to when the project was complete was beyond his expectations of what was possible.
True Modular Building Seeks to Revolutionize Housing. It’s Next Stop: MBI’s World of Modular Europe
True Modular Building (TMB) specializes in crafting attainable, eco-friendly, and comfortable build-to-rent (BTR) housing with modern designs and customizable features, ensuring that residents feel at home both today and tomorrow.
From Toronto to Suriname: A Global Modular Building Story
When I AM Gold – a Canadian gold mining operation based in Toronto, Ontario – wanted to expand its mining operations in Suriname, it knew it would also need to expand its infrastructure. More specifically, they needed to build a mechanical services compound that would allow their local crews to maintain and equipment critical to their mining operations. They also knew that it would be a challenge.
There Were a “Sea of Challenges” for this Modular, Island Development
Question: Can modular construction be used to build a series of affordable, unique housing buildings, all styled to look like they were built in 1845, on an
island that caters to the wealthy? The answer is, of course, yes, but how the
team at Signature Building Systems and KOH Architecture got there is quite a story.
America’s Construction Economy: A Race Against Time
If the economy has been able to handle higher interest rates thus far, undoubtedly it will be able to manage the lower interest rates to come. But many economists are pointing out that the Federal Reserve may already be too late to the game. While they gradually reduce interest rates, the U.S. economy could quickly decelerate, at least based on theoretical grounds if not on the most recent data releases, culminating in that long-predicted recession. Only time will tell.
Top Five Benefits of Modular Office Space
Modular office spaces are transforming how businesses think about their work environments. These innovative structures offer a mix of flexibility, efficiency, and sustainability, making them a smart choice for companies looking to gain an advantage.