Building Better Buildings with Resilient Modular Construction
Whether you are looking to expand your business and need a larger commercial facility, or you are looking to invest in multifamily housing development, you may find that building and designing a new facility would suit your needs better than buying an existing building. However, with labor shortages and construction costs on the rise, a traditional built on-site facility may not be a realistic option for many businesses.
This has led to a rise in the popularity of modular commercial facilities that are constructed in segments in a factory and are later assembled at the building's site, as this tends to be a much more expedient option than constructing a traditional building. However, just because modular buildings are faster to build than traditional buildings, this does not mean that they are of lesser quality.
Not only are modular buildings built to the same stringent building codes as traditional facilities, but many would also argue that, due to their industrialized construction process, modular buildings are stronger and more resilient than buildings built on-site. Here are just a few of the reasons why modular construction can lead to stronger, more resilient buildings.
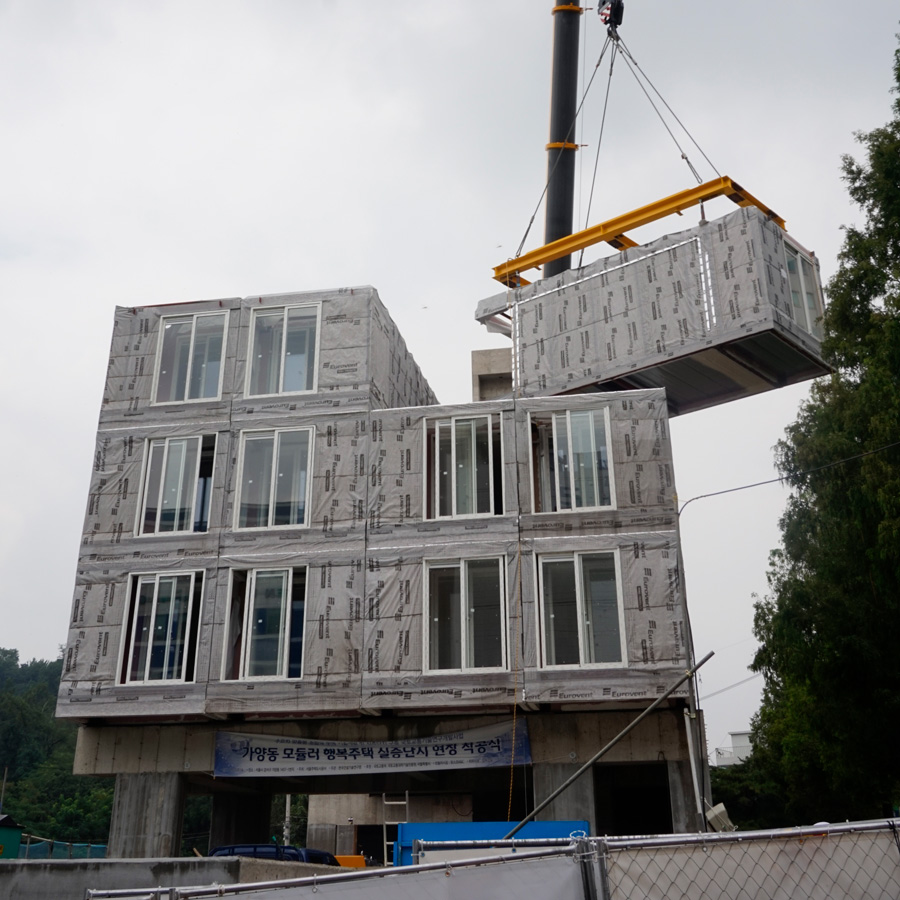
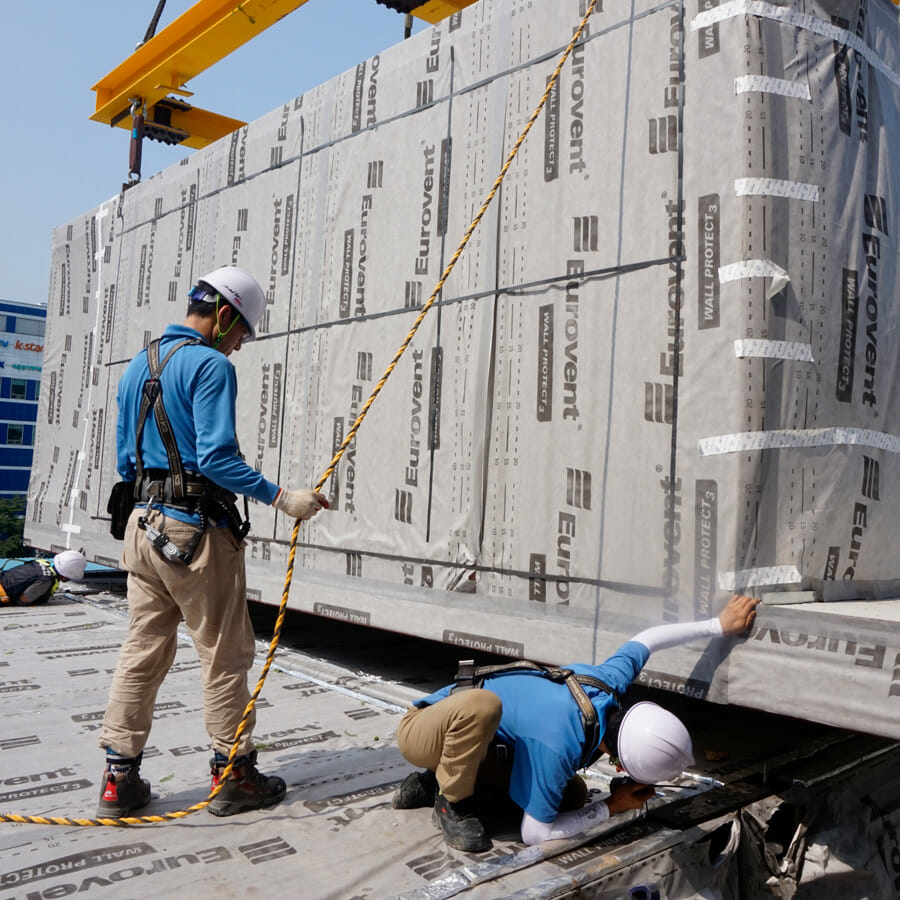
Quality Control
The main reason why modular buildings are often of higher quality than traditional structures is that, being built in a factory setting, there is more quality control in their construction. While contractors at onsite building projects may not always be under close supervision, facilities where modular buildings are constructed adhere to strict procedures.
The build process with modular buildings uses effective oversight as well as innovative automation techniques to ensure that each build is of the highest quality, and building sections are inspected at various points during construction in order to ensure quality. This reduces the chances of a mistake being made during the building process, and it often results in higher-quality buildings.
Built in a Controlled Environment
Another benefit of modular construction is that building inside of a factory, rather than on-site, allows for a controlled environment. When building a traditional building, builders have no control over the weather.
Unexpected storms can not only cause costly delays, but they can also cause damage to materials and exposed structures, which could lead to structural problems that may not be discovered until years later. Alternatively, the factory setting of modular construction allows builders to ensure that modular buildings are constructed in a temperature-and moisture-controlled environment, ensuring a structurally sound finished product.
They're Built for Transport
Another reason why modular buildings are often considered to be stronger than traditional buildings is that they are simply built to handle more abuse. While a site-built building is never meant to be moved, builders of modular buildings are aware that the modular sections will need to be transported to the construction site in order for the building to be assembled.
These building sections are then built with this transportation in mind, and they build these sections to be able to withstand traveling on rough roads and being exposed to debris and high wind speeds on highways. This results in a stronger building, as each section can be independently as strong as a traditional building, and this strength is compounded when the sections are joined together.
Modular Buildings Have Proven Their Resilience
Since modular buildings are built to withstand extreme conditions on the road, they also often fare better than traditional buildings during extreme weather conditions, such as during hurricanes. Many modular buildings are made to withstand the types of high winds and heavy impacts from debris that one would see during a hurricane, making modular buildings truly resilient.
While on-site building construction has been the norm for generations, modular building is gaining popularity for the construction of hotels and commercial facilities due to the fact that modular buildings allow for a quicker ROI and are faster to build than traditional buildings, and they are also stronger and more resilient as well.
More from Modular Advantage
DORÇE Navigates Mountainous Terrain, Extreme Weather to Help Rebuild Türkiye
The February 6 earthquakes in 2023 were enormous. In response, DORÇE moved quickly, obtaining a government bid to help create housing and multipurpose structures—both temporary and permanent—for earthquake victims and laborers hired for reconstruction efforts.
Modern Desert Oasis: Building Reset Hotel the Modular Way
While the off-site construction part of the Reset Hotel project has been carefully controlled and with every necessity close at hand at BECC Modular’s factory in Ontario, Canada, the remote location of the project site has created additional challenges for the on site portion of the build.
Revisiting Yellowstone Canyon Village—a Groundbreaking Modular Construction Feat—Ten Years On
With such a short building period due to impending cold, it made the most sense for park developer Xanterra to pursue modular. Yellowstone’s high visitor traffic also required some odd transportation scheduling, as traffic from the West Yellowstone entrance determined the times when trucks could unload modules. Guerdon was up to the challenge.
Built for Brutal Cold, This Modular Office Building Shines
Houlton, the county seat of Aroostook County, Maine, is a small town with a population of about 6,000 residents. Situated along the border between the U.S. and Canada, what the town is most known for is bitterly cold winters. When the U.S. Border Patrol needed new office space, a modular building approach from Modular Genius offered the perfect solution.
Panel Replacement Adds Years of Life to Navy Vessel
Panel Built, Inc., recently replaced all the wall and roof panels on a two-story US Navy barge deck house that the company had originally installed 30 years ago, giving the vessel new life. Now, the commanding officer of the unit that uses the barge said the difference between the condition and appearance from when the barge left their facility to when the project was complete was beyond his expectations of what was possible.
True Modular Building Seeks to Revolutionize Housing. It’s Next Stop: MBI’s World of Modular Europe
True Modular Building (TMB) specializes in crafting attainable, eco-friendly, and comfortable build-to-rent (BTR) housing with modern designs and customizable features, ensuring that residents feel at home both today and tomorrow.
From Toronto to Suriname: A Global Modular Building Story
When I AM Gold – a Canadian gold mining operation based in Toronto, Ontario – wanted to expand its mining operations in Suriname, it knew it would also need to expand its infrastructure. More specifically, they needed to build a mechanical services compound that would allow their local crews to maintain and equipment critical to their mining operations. They also knew that it would be a challenge.
There Were a “Sea of Challenges” for this Modular, Island Development
Question: Can modular construction be used to build a series of affordable, unique housing buildings, all styled to look like they were built in 1845, on an
island that caters to the wealthy? The answer is, of course, yes, but how the
team at Signature Building Systems and KOH Architecture got there is quite a story.
America’s Construction Economy: A Race Against Time
If the economy has been able to handle higher interest rates thus far, undoubtedly it will be able to manage the lower interest rates to come. But many economists are pointing out that the Federal Reserve may already be too late to the game. While they gradually reduce interest rates, the U.S. economy could quickly decelerate, at least based on theoretical grounds if not on the most recent data releases, culminating in that long-predicted recession. Only time will tell.
Top Five Benefits of Modular Office Space
Modular office spaces are transforming how businesses think about their work environments. These innovative structures offer a mix of flexibility, efficiency, and sustainability, making them a smart choice for companies looking to gain an advantage.